Among the most compelling answers to this issue is the DUSTFIX® Dust Conditioner by MAP®, a division of WAMGROUP®, global leader in bulk material handling and processing technologies.
The DUSTFIX® unit isn’t just another piece of auxiliary equipment—it’s a purpose-designed solution that reflects over four decades of MAP®’s innovation in the field. Built to address the evacuation, conditioning, and disposal of industrial dusts, it brings together efficiency, economy, and environmental care in a compact, intelligent design.
A Legacy of Mixing Innovation
Founded in 1983 with the vision of manufacturing modular single-shaft mixers, MAP® has evolved into a major player in industrial mixing solutions. From batch to continuous processes, from laboratory-scale blenders to heavy-duty twin-shaft mixers, the company’s product range covers virtually every mixing application.
Yet the DUSTFIX® stands out for one key reason: it’s more than a mixer. It’s a targeted tool for dust conditioning—a process that transforms dry, airborne dust particles into manageable, moist agglomerates ready for disposal. For industries in sectors such as cement, lime, steel, food processing, or chemical manufacturing, this kind of control over fugitive dusts can make a significant difference in both compliance and cleanliness.
The Technical Core
At the heart of the DUSTFIX® system is a carefully engineered configuration designed for continuous duty and minimum maintenance. The main features include:
- Carbon steel tubular casing with a SINT® engineering polymer liner for durability and non-stick performance
- A combined feeder screw/mixing shaft to ensure thorough, uniform conditioning
- A liquid injection system, optimized via strategically placed nozzles that drastically reduce mixing time
- A self-cleaning conditioning chamber that resists material build-up thanks to its flexible, pulsating polymer jacket
- Replaceable internal components including the conditioning chamber and rotor tools
- Capacity range from 2 to 80 m³/h to fit small to large-scale operations
These components are integrated into a system driven by a high-efficiency electric motor with an adjustable shaft sealing unit—another sign of the machine’s thoughtful design. Importantly, MAP® achieves all this without compromising on price, thanks to the use of standardised components across its product family.
The Power of SINT® Engineering Polymers
One of the major innovations embedded in DUSTFIX® is the application of SINT® engineering polymers, a proprietary material that offers exceptional wear resistance and elasticity. The chamber lining made from SINT® not only prevents product adhesion but also plays a crucial role in self-cleaning during operation.
The flexible chamber jacket expands and contracts with the machine’s operation, gently dislodging any material attempting to stick. This prevents hardening materials from building up, ensures consistent product flow, and extends the lifespan of internal parts.
Mixing Beyond Just Dust Control
Though primarily designed for industrial dust, the DUSTFIX® Dust Conditioner’s versatility expands into a variety of mixing functions. Depending on process needs, the unit is capable of:
- Mixing powder with powder (e.g., homogenization of dry blends)
- Mixing powder with liquid (e.g., conditioning, granulation, or coating)
- Humidification and agglomeration (ideal for reducing airborne dust and improving handling characteristics)
This makes the DUSTFIX® not just a terminal disposal tool but an integral part of upstream process improvement—be it for environmental controls or preparing materials for further processing.
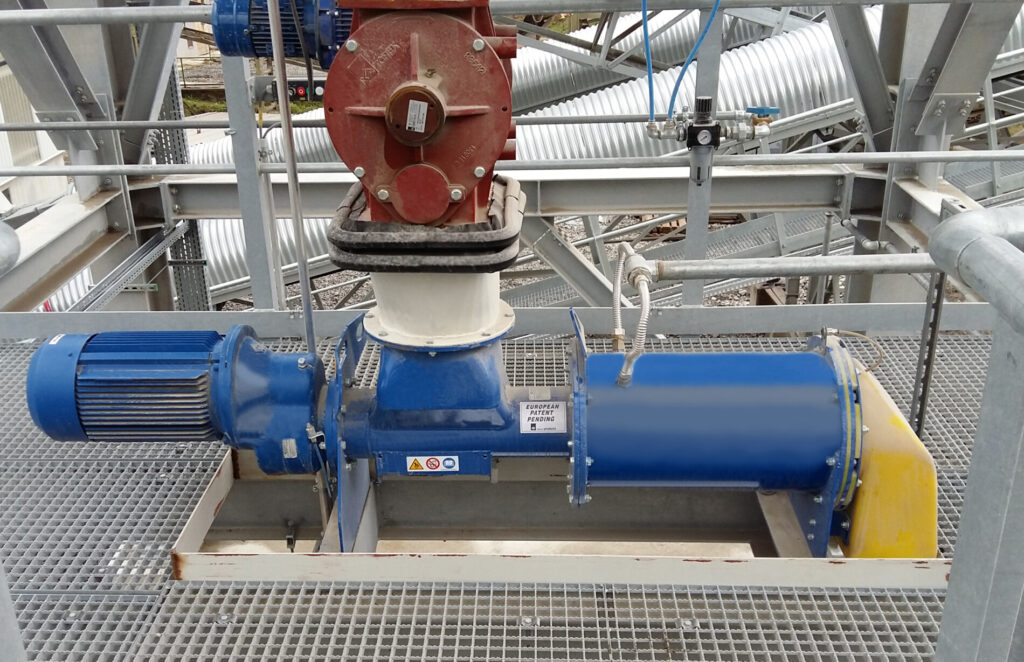
Designed for the Real World
One of the standout characteristics of the DUSTFIX® is its ease of installation and operation. It can be retrofitted into existing dust collection systems or designed into new production lines with minimum disruption. Operators will appreciate the machine’s low maintenance profile, quick access for cleaning, and rotor system that is completely removable and replaceable.
Additionally, the DUSTFIX®’s modular construction reflects MAP®’s core philosophy: standardised components engineered for flexibility. This allows for a degree of customisation while keeping overall system costs in check—critical for plants under constant pressure to do more with less.
Meeting Industry and Environmental Expectations
Dust disposal is an environmental obligation. Increasingly strict regulations on particulate
emissions are prompting manufacturers to find better ways to handle airborne pollutants. DUSTFIX® offers a practical solution that helps companies comply with environmental legislation while improving workplace safety and hygiene.
Moreover, the energy efficiency of the system, coupled with the long-lasting performance of SINT® components, supports broader sustainability goals. Reduced wear means less downtime, fewer spare parts, and lower energy consumption—all key factors in making a plant eco-friendlier.
Why It Matters
In a market saturated with generic mixing equipment, the DUSTFIX® Dust Conditioner represents a refreshing shift toward specialised, purpose-built machinery. It brings to bear MAP®’s deep knowledge of material behavior, process engineering, and operational constraints. The result is a product that does not simply perform a function—it solves a problem.
From bulk solids handling and waste reduction to operator safety and environmental compliance, the DUSTFIX® checks all the boxes. For engineers, plant managers, and procurement officers looking to modernise their dust disposal systems, it offers an intelligent and economical path forward.
The DUSTFIX® Dust Conditioner by MAP® is more than a tool—it’s a strategic upgrade for any production environment where dust poses a challenge. Backed by decades of experience, engineered for performance and simplicity, and built with an eye on sustainability, it’s a product that sets a new benchmark in mixing-based dust conditioning.
Whether you’re aiming to streamline your waste handling or seeking a cleaner, safer, more compliant plant, DUSTFIX® proves that effective solutions don’t have to be complex—or expensive.
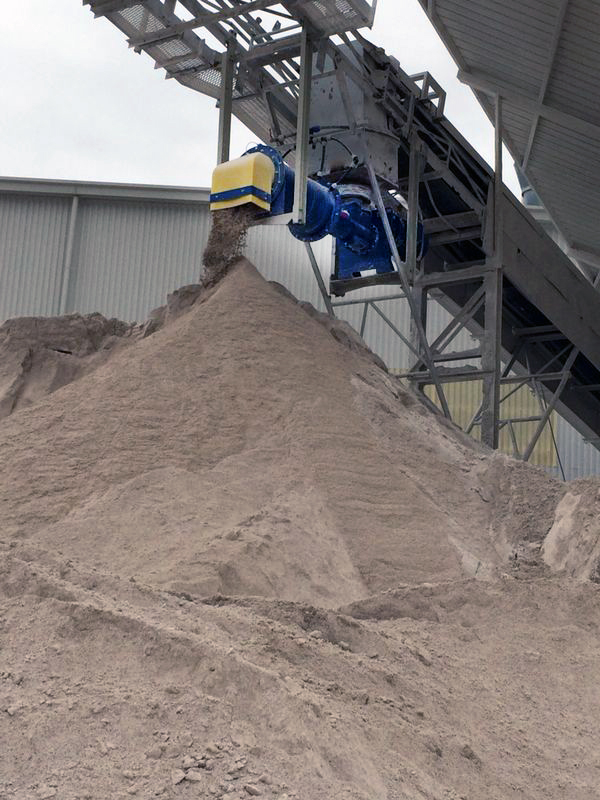