In extractive metallurgy, mineral processing (also known as mineral dressing, ore dressing, mineral engineering, mineral beneficiation, and mineral extraction) is defined as extracting valuable minerals from their ores.
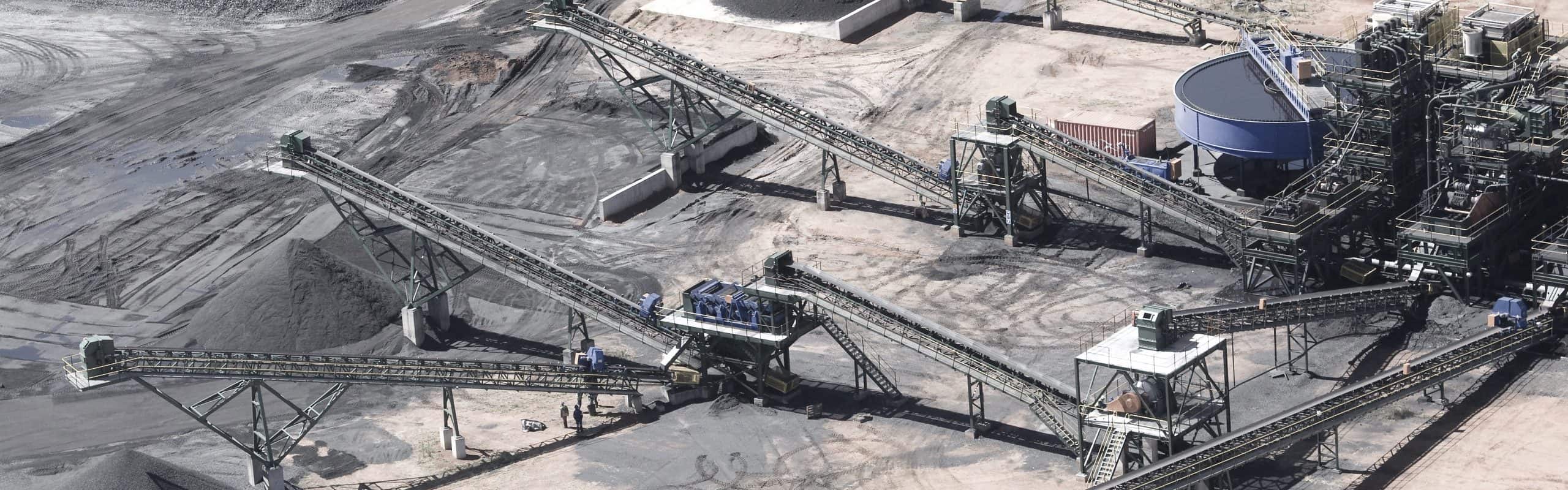
In extractive metallurgy, mineral processing (also known as mineral dressing, ore dressing, mineral engineering, mineral beneficiation, and mineral extraction) is defined as extracting valuable minerals from their ores.
In minerals processing, unit operations must prepare and classify ores before separating the valuable materials. These processes form valuable minerals.
Necessary unit operations include:
To achieve the goal of recovering valuable materials, the raw ore must be reduced to a reasonable size before separation. This process is called ‘comminution’ or ‘size reduction.’
Comminution may be carried out on either dry materials or slurries. Most mineral processing operations are conducted with water as the medium; this is called wet processing against dry processing.
Crushing, grinding, milling, and vibration (feeding) are examples of comminution processes.
Sizing is the general term for separating minerals according to their size.
The separation methods are based on the variations among the physical properties of different minerals, such as shape, susceptibility to size reduction, specific gravity, surface chemical property, and electromagnetic exposure.
The most straightforward mineral sizing process is screening or passing the particles to be sized through a screen or multiple screens.
Classification of particles by size comprises an essential operation in mineral processing, and it can be accomplished either by screening through sieves or applying forces by the medium, gas, or water.
Mineral processing concentration means the increase of the percentage of the valuable mineral in the concentrate. Concentration includes processes that involve the separation of minerals without a change in their structure, chemical composition, or state of aggregation. The results of mineral concentration are two main products: concentrate and tailings.
For economic reasons, dewatering/drying is essential in mineral processing. Removal of the moisture content enables easy and cost-effective handling and transportation of minerals. The water removed during dewatering can be recycled through a mineral processing plant. The main processes used in dewatering/drying include dewatering screens, filtering, sedimentation, and thermal drying.
In all of these operations, the most important considerations are the processes’ economics, which is dictated by the grade and recovery of the final product. To achieve the goal of extracting minerals from ores in their purest form for mineral processing engineers, only the best mineral processing technology suffice. An essential first step in both comminution and sizing operations in mineral processing is particle size analysis.
In the particle size reduction (comminution) process, crushers (jaw crushers, gyratory crushers, cone crushers) and grinders (rod mills, ball mills, impact mills, attrition mills) are primarily used systems.
In the sizing (separation) process, necessary equipment includes:
In the mineral concentration process, designed to produce a concentrate consisting predominantly of valuable minerals, the following mineral processing equipment is primarily used:
It is challenging to find a source covering all aspects of mineral processing. From plant supervisors to project engineers, they all need to keep up-to-date with the latest mineral processing news.
Access to the latest mineral processing news, innovations, and mineral processing events is crucial for any mineral industry professional.
Get the extensive coverage for dry material handling professionals who buy, maintain, manage or operate equipment, delivered to your inbox (it’s free!).
By signing up for our list, you agree to our Terms & Conditions.
Get the extensive coverage for dry material handling professionals who buy, maintain, manage or operate equipment, delivered to your inbox (it’s free!).
By signing up for our list, you agree to our Terms & Conditions. We deliver two E-Newsletters every week, the Weekly E-Update (delivered every Tuesday) with general updates from the industry, and one Market Focus / E-Product Newsletter (delivered every Thursday) that is focused on a particular market or technology.
Since 2010, we have been providing industrial professionals with the latest innovations, case studies, and the most comprehensive equipment guide in solids handling, in a variety of markets.
A
website
© BulkInside 2025
By signing up for our list, you agree to our Terms & Conditions. We deliver two E-Newsletters every week, the Weekly E-Update (delivered every Tuesday) with general updates from the industry, and one Market Focus / E-Product Newsletter (delivered every Thursday) that is focused on a particular market or technology..