Mixing and blending of dry bulk materials
Mixing and blending dry bulk materials is an important processing step in many industries. When processing dry materials, the mixing quality plays a central role.
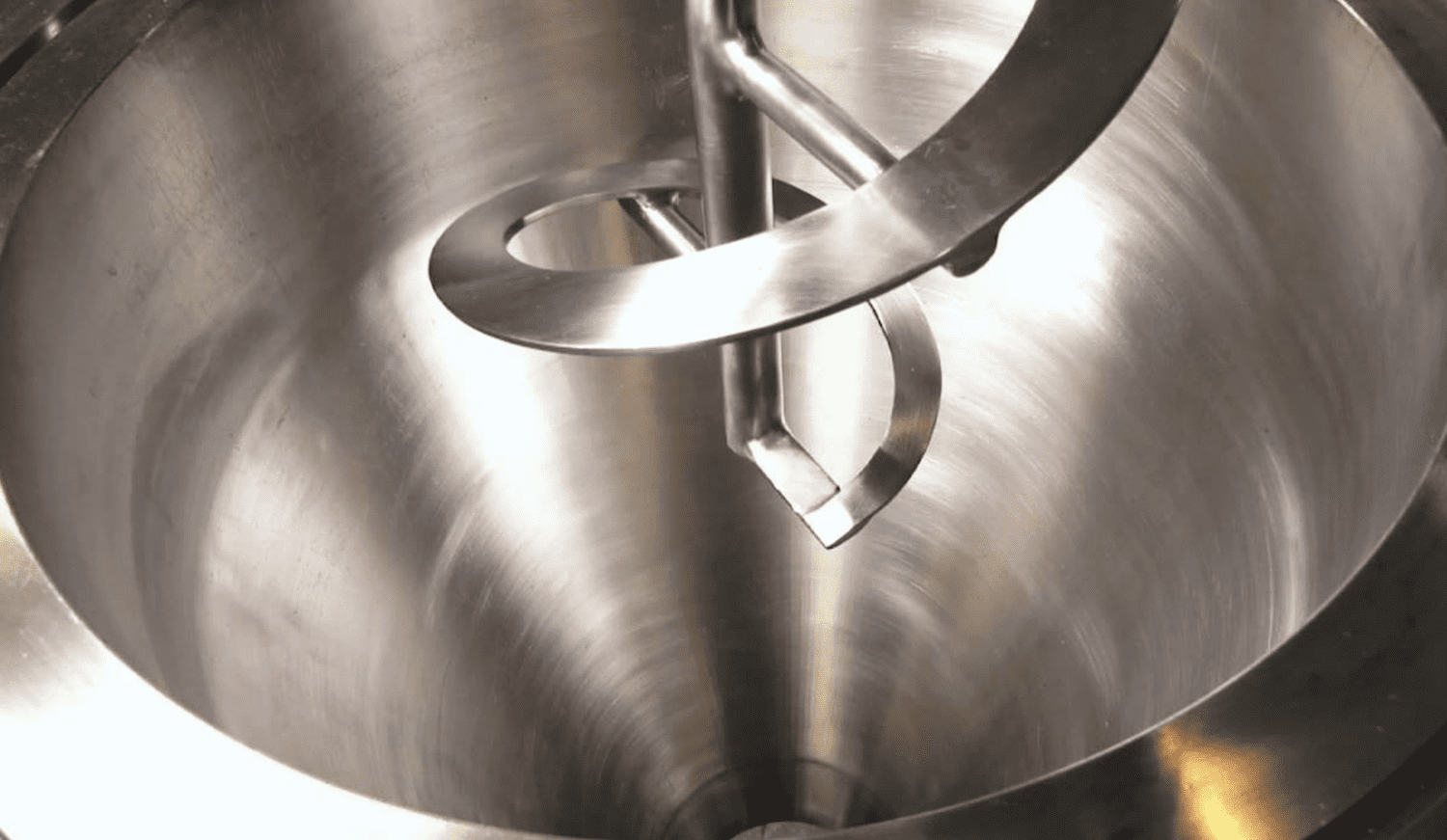
Mixing and blending dry bulk materials is an important processing step in many industries. When processing dry materials, the mixing quality plays a central role.
The mixing of solids is the oldest and most frequently performed chemical operation. With the increasing automation of engineering processes in all material transformation sectors, applying scientific principles to such operations is of increasing importance. Solid mixing refers to blending at least one solid component with another, whereby the particulate components differ in at least one of their characteristics.
The mixing process can be seen in diagrammatic form as an overlap of dispersion and convection. These are the two main mechanisms of solids mixing, and the movement of the particulate solids is a requirement of both mechanisms.
Dispersion means the utterly unexpected change of the individual particles in the mix. The frequency of the changing movement of both particles is related to the number of particles of the other ingredients. On the other hand, the convection mechanism causes a movement of large groups of particles relative to each other, also known as macromixing.
Powder mixing is critical for the quality and performance of a wide range of products in many processes in the paper, rubber, food, plastics, and pharmaceutical industries. The product produced through powder mixing is considered finished with three essential features: homogeneity, flow, and sampling.
Most powders are cohesive; many pair up spontaneously when exposed to a moist or damp atmosphere. Agitation of the powder often results in the migration of particles of a smaller size downwards and larger ones upwards. There are standard and non-standard mixing devices; the standard ones include drum tumblers and Turbula mixers, while the non-standard devices are often called static mixers. Static mixers disable segregation, save energy, and affect particle migration.
In pharmaceutical manufacturing of solid dosage formulations (capsules or tablets), small amounts of a powdered active drug are gently blended with excipients, such as cellulose, lactose, starch, sugar, and lubricants.
With food products, many powder-form consumer products result from custom mixed batches; consider cake mix, ice tea, and dry seasonings. Many chemical process industries (CPI) processes involve mixing or blending specialty chemicals, fertilizers, explosives, glass or ceramics, detergents, and resin compounds.
There are three primary mechanisms of mixing: convection, shear, and diffusion.
As continued research and development races to meet the growing demand for sustainable adhesives, manufacturers must also push the mixing processing industry innovations.
Planetary Mixing
Multi-shaft mixers are most commonly used for dispersing solid raw materials into a liquid vehicle. They offer a combination of both shear agitation that can be fine-tuned throughout the batching process.
High-Speed Powder Injection
One area of improvement in the preparation of lower forceful formulations is the method of raw material addition. This may be accomplished by new-generation high-shear mixers equipped with a built-in powder injection mechanism.
Continuous Improvement
These are just a few examples of recent innovations in the mixing and blending industry. Many more innovations will surface in the future to create more solventless, bio-based, renewable, recyclable, and non-toxic adhesives. While pain points persist, like cost, raw material availability, the performance difference between petrochemical-based manufacturers and their mixing counterparts can boost their will to improve sustainability by periodically reviewing their current mixing equipment and procedures.
Get the extensive coverage for dry material handling professionals who buy, maintain, manage or operate equipment, delivered to your inbox (it’s free!).
By signing up for our list, you agree to our Terms & Conditions.
Get the extensive coverage for dry material handling professionals who buy, maintain, manage or operate equipment, delivered to your inbox (it’s free!).
By signing up for our list, you agree to our Terms & Conditions. We deliver two E-Newsletters every week, the Weekly E-Update (delivered every Tuesday) with general updates from the industry, and one Market Focus / E-Product Newsletter (delivered every Thursday) that is focused on a particular market or technology.
Since 2010, we have been providing industrial professionals with the latest innovations, case studies, and the most comprehensive equipment guide in solids handling, in a variety of markets.
A
website
© BulkInside 2025
By signing up for our list, you agree to our Terms & Conditions. We deliver two E-Newsletters every week, the Weekly E-Update (delivered every Tuesday) with general updates from the industry, and one Market Focus / E-Product Newsletter (delivered every Thursday) that is focused on a particular market or technology..