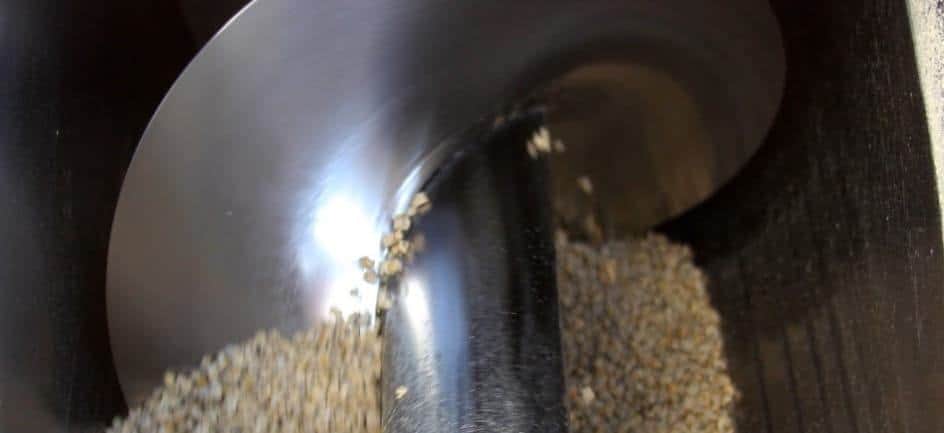
Animal feed processing is the cornerstone of modern agriculture, powering the health, growth, and productivity of livestock across the globe. It’s a complex and indispensable industry that transforms raw ingredients into nutritious and balanced feed for a diverse range of animals, from poultry and cattle to aquaculture species. The impact of this process extends beyond the barnyard, playing a pivotal role in global food security and sustainability.