Solids feeders are of great importance in bulk material handling systems since feeders control the solid flow rate.
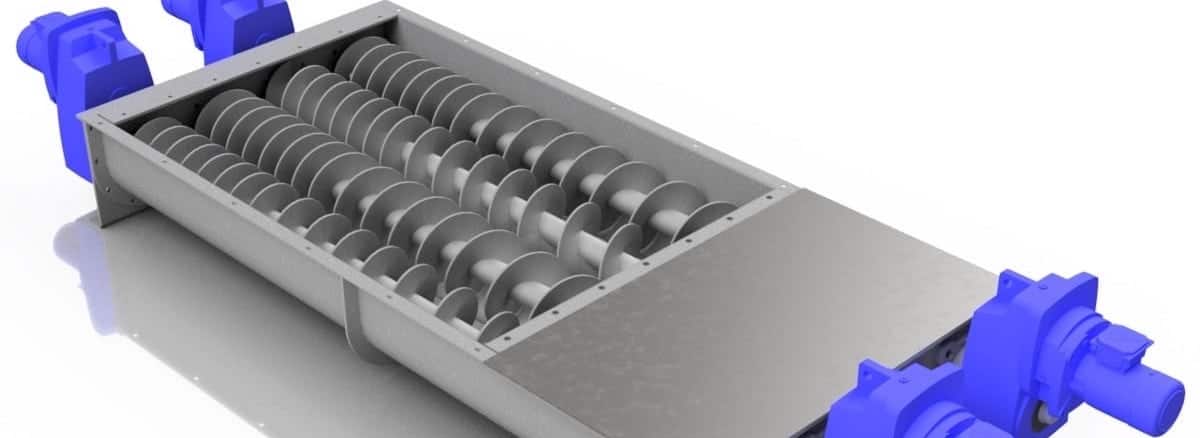
Solids feeders are of great importance in bulk material handling systems since feeders control the solid flow rate.
Solids feeders deliver powder, granular, and other bulk solid materials along a process line, or to and from process units, storage bins, conveyors, and product packaging. Additionally, feeders may serve to break down clumps or arches to allow for more uniform distribution. There are two basic types of bulk feeders: volumetric feeders and gravimetric feeders.
The difference between a feeder and a conveyor is that a conveyor is only capable of transporting material, not controlling the flow rate. When feeders stop working, the solids flow rate will come to an end.
There are many types of bulk feeders available today. The most broadly used include vibratory tubes, vibratory trays, vibratory belts, screw feeders, and rotary feeders (also known as rotary airlocks or rotary valves).
Below are some common types of dry material feeders and the types of applications in which they are used:
Vibratory tube feeders: Vibratory tube feeders can utilize electromagnetic or brute force (offset weight vibrators) and feed dry materials in an enclosed tube to downstream equipment.
Vibratory tray feeders: Vibratory tray feeders can utilize electromagnetic or brute force (offset weight vibrators) to feed dry materials along a pan (or tray) into downstream equipment. These are particularly good with friable, sticky, or easily smeared materials.
Both vibratory tray feeders and vibratory tube feeders are a good option for materials that are friable. Also, when properly applied, these devices will empty completely.
Vibratory belt feeders: Vibratory belt feeders can be a good option when you have limited headroom. Even with its low profile, it can be capable of high rates. Vibratory belt feeders are best suited for materials that are not dusty and are well suited for friable types of materials.
Volumetric Screw Feeders: Volumetric screw feeders allow consistent feeding of dry materials into downstream processes. These can be tuned to feed rates ranging from just a few grams or ounces per minute to well over 100 pounds per minute by utilizing different screw diameters and pitches, as well as variable frequency drives and gearbox combinations.
Loss-In-Weight Screw Feeders: By mounting a feeder (screw, tube, tray, belt, etc.) to a scale platform, you can gravimetrically (Loss-in-Weight) feed material into a downstream process. This can be done as a “batch” or continuous process.
Rotary feeders (also known as rotary airlocks or rotary valves): Rotary feeders consist of a paddle wheel-shaped rotor that rotates at low rpm to dispense material into a hopper or process unit (mixer, crusher, screener). If the blades form a tight seal against the valve wall, then the valves can be applied in airlock applications.
While more commonly used as a refill device, rotary valves can be a desirable option as a feeder.
The type of feeder to be selected for a particular application is dependent upon several factors.
First, it is essential to clearly define the application parameters.
These include the feed rate range, accuracy requirements, temperature and/or pressure considerations, possible dimensional restraints, the type of system used to get the material to the feeder, and to what downstream equipment the feeder will discharge.
Then, it is essential to define the characteristics of the material to be fed. Establishing these parameters will reduce the available feeder types that are applicable to your specific application.
Once you have established all essential parameters and decided on the device (or devices) you believe will best suit your needs, it is always a good idea to have a potential manufacturer test your bulk product.
This Technology Zone offers an insight into the latest innovations in bulk solids feeders for material processing industries.
Get the extensive coverage for dry material handling professionals who buy, maintain, manage or operate equipment, delivered to your inbox (it’s free!).
By signing up for our list, you agree to our Terms & Conditions.
Get the extensive coverage for dry material handling professionals who buy, maintain, manage or operate equipment, delivered to your inbox (it’s free!).
By signing up for our list, you agree to our Terms & Conditions. We deliver two E-Newsletters every week, the Weekly E-Update (delivered every Tuesday) with general updates from the industry, and one Market Focus / E-Product Newsletter (delivered every Thursday) that is focused on a particular market or technology.
Since 2010, we have been providing industrial professionals with the latest innovations, case studies, and the most comprehensive equipment guide in solids handling, in a variety of markets.
A
website
© BulkInside 2025
By signing up for our list, you agree to our Terms & Conditions. We deliver two E-Newsletters every week, the Weekly E-Update (delivered every Tuesday) with general updates from the industry, and one Market Focus / E-Product Newsletter (delivered every Thursday) that is focused on a particular market or technology..