Mechanical conveying systems are a very effective and efficient way to transfer large amounts of product from point to point. Because they’re very robust, mechanical conveyors can move a wide variety of product shapes, sizes, or weights.
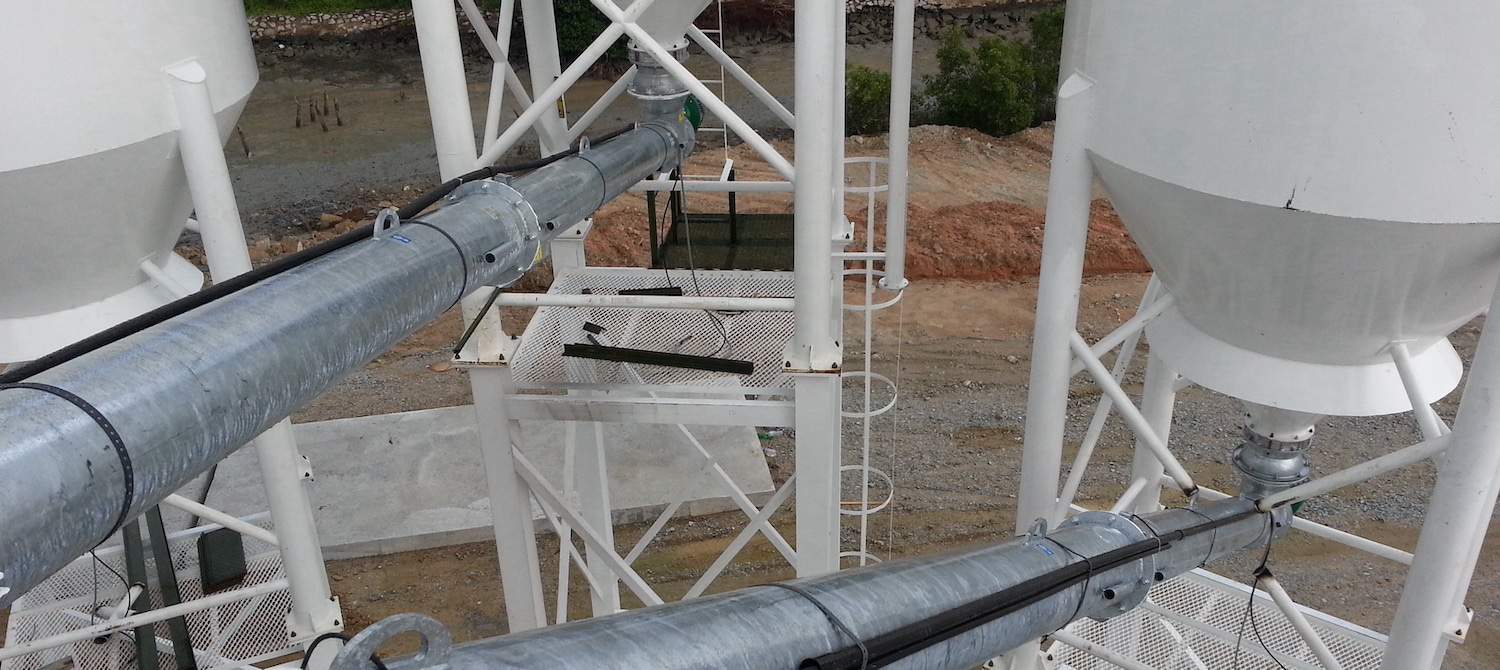
Mechanical conveying systems are a very effective and efficient way to transfer large amounts of product from point to point. Because they’re very robust, mechanical conveyors can move a wide variety of product shapes, sizes, or weights.
Mechanical conveyors are one of the most efficient methods of conveying materials in their dust-free and clean handling properties. These conveyors are designed and custom-built for the product to be conveyed and are ideally suited to meet a variety of applications in many industries.
Mechanical conveyors offer design flexibility since they can be installed almost anywhere. They’re also versatile systems since they can convey material horizontally, at an incline, or even vertically.
Many kinds of mechanical conveying systems are available and are used according to the various needs in dry material processing operations.
There are many ways to convey products mechanically, from screws and chains to buckets and belts, and each has its advantages.
Selecting the best mechanical conveyor for an application is essential to processing success and business profits.
Here are some of the most common types of mechanical conveyors and what they’re used for:
Aeromechanical conveyors – Working on the principle of a fluidized airstream created by discs mounted on a rope, aeromechanical conveyors can efficiently move moderate amounts of material. A wire rope with evenly spaced discs travels at high speed within a steel tube, running in sprockets at each end of the conveyor. As bulk material is fed in, the air stream aerates or fluidizes it and carries it to the outlet, which is discharged by centrifugal force.
Bucket elevators – Bucket elevators are designed for vertically handling various dry, free-flowing bulk materials efficiently and with high capacities. Bucket elevators consist of buckets placed either on a single or double chain.
Belt conveyors – Belt conveyors utilize a wide belt over rollers to move material. It’s perfect for carrying a lot of bulk solids or covering very long distances. It’s surprisingly gentle for as fast as it can move and can be used to convey almost anything, although sticky bulk solids sometimes cause maintenance issues. Belt conveyors are used for transporting, feeding, discharging, and proportioning.
Drag chain conveyors – Drag chain conveyors use a chain and paddle design to move material. Drag chain conveyors come in 2 primary styles: En masse and bulk flow. En masse conveyors utilize a low-profile paddle in a tall box, and bulk flow drag chain conveyors use a taller paddle in a divided box.
Screw conveyors – Screw conveyors, use an auger-type motion to move materials – often horizontally or at a slight incline. Screw conveyors can move the fabric at rates almost up to 40 tons in an hour and cover 65 feet. They are used in dairy production, food, and pharmaceutical applications.
Flexible screw conveyors – Flexible screw conveyors, also known as auger conveyors, convey dry bulk solids in any direction into mixers, packaging machines, or storage bins. Flexible screw conveyors require low investment, good reliability, and are not complicated to operate.
Spiral conveyors – Spiral conveyors are used wherever bulk solids must be conveyed vertically, both upwards and downwards. Spiral conveyors are suitable for conveying a host of bulk solids from various production processes, and they often combine conveying with cooling, drying, heating, or humidification processes.
Tubular Cable Conveyors – Tubular cable conveyors are designed for gentle handling and installations. They can transfer fragile bulk solids from single or multiple in-feed points to single or multiple discharge points over long distances with little or no damage.
Vibratory conveyors – They have a single trough design that vibrates to move the material both upwards and forward. Cross-sectional areas along with the slope of the trough determine the capacity of the vibratory conveyor. Because vibratory conveyors use vibrating trays to advance materials, they’re well suited for products that tend to clump or stick together. They’re also suitable for sticky products and need to cool, as well as coating applications. The vibration keeps them from clumping as they move from coater to cooler.
Getting a bulk product from point A to point B isn’t the only consideration that has to be made when deciding about a mechanical conveying system.
When choosing from these types of mechanical bulk material conveyors, buyers will want to consider the relative advantages and disadvantages of their operation and application.
Making the right choice will result in improved operations, reduced costs, and ensure a good match with other equipment and systems.
Mechanical conveyor systems are often the lifeline to a company’s ability to move its bulk product in a timely fashion effectively.
This Technology Zone offers an insight into the latest innovations in mechanical conveying solutions for dry material processing industries.
Get the extensive coverage for dry material handling professionals who buy, maintain, manage or operate equipment, delivered to your inbox (it’s free!).
By signing up for our list, you agree to our Terms & Conditions.
Get the extensive coverage for dry material handling professionals who buy, maintain, manage or operate equipment, delivered to your inbox (it’s free!).
By signing up for our list, you agree to our Terms & Conditions. We deliver two E-Newsletters every week, the Weekly E-Update (delivered every Tuesday) with general updates from the industry, and one Market Focus / E-Product Newsletter (delivered every Thursday) that is focused on a particular market or technology.
Since 2010, we have been providing industrial professionals with the latest innovations, case studies, and the most comprehensive equipment guide in solids handling, in a variety of markets.
A
website
© BulkInside 2025
By signing up for our list, you agree to our Terms & Conditions. We deliver two E-Newsletters every week, the Weekly E-Update (delivered every Tuesday) with general updates from the industry, and one Market Focus / E-Product Newsletter (delivered every Thursday) that is focused on a particular market or technology..