Size reduction of bulk solids is a very common and important unit operation found across the process industries. It is necessary for processing products, enhancing and improving the material’s performance properties, or meeting particular processing requirements.
Size enlargement is a process in which small particles are combined into larger masses but the individual particles can still be distinguished.
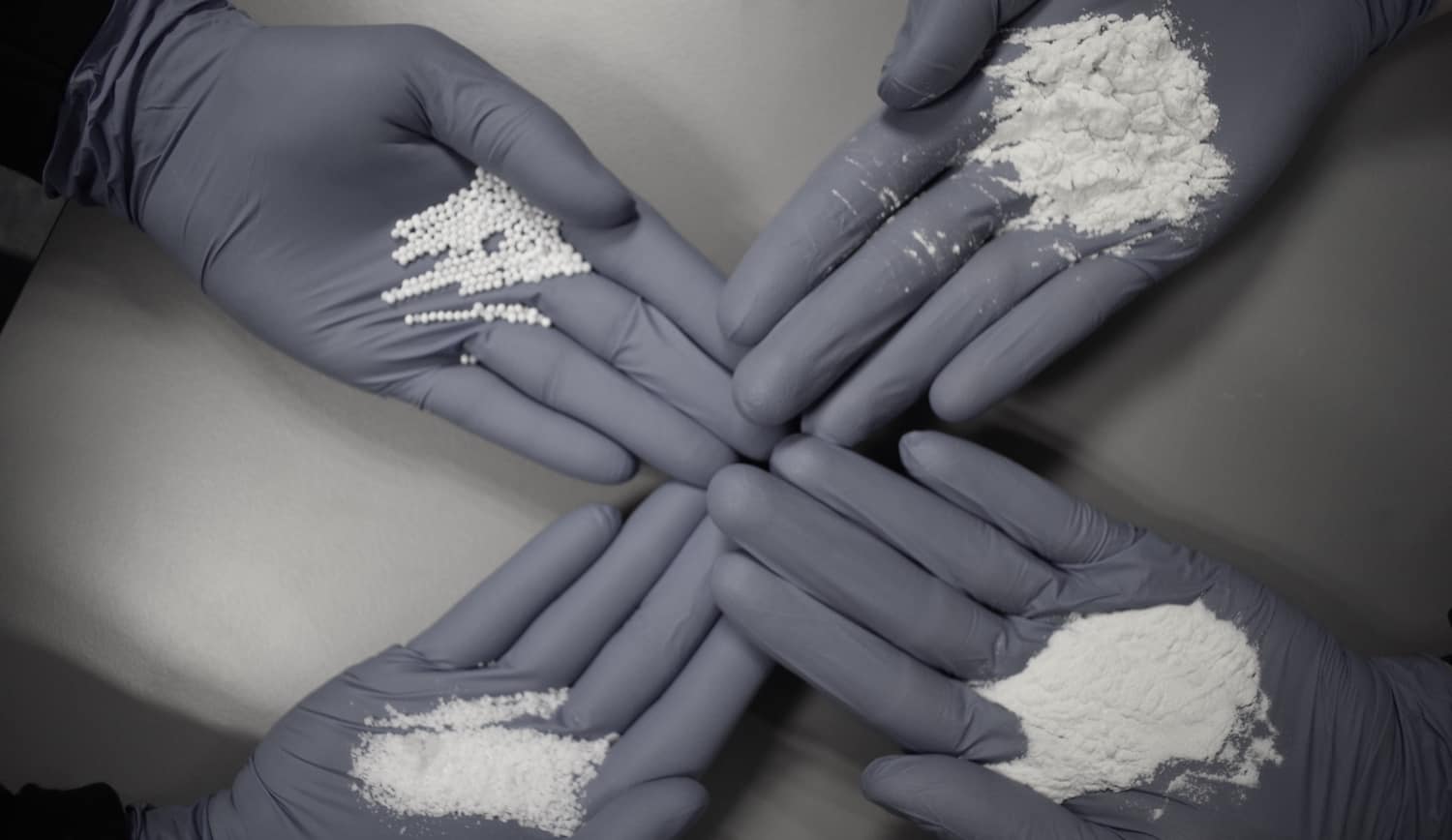