
Fortunately, advancements like the Vortex Automated Loading System (VALS) and its integrated components are redefining how industries tackle these issues.
This article dives into the complexities of dust collection and air pollution control, discusses the challenges of dry bulk solid handling, and highlights innovative solutions like VALS to enhance efficiency and safety.
Challenges in Handling Dry Bulk Solids
Labor and Safety Complexities
Loading dry bulk solids into trucks, storage tanks, or silos often involves labor-intensive steps. Miscommunication between operators and truck drivers, the manual alignment of loading spouts, and constant supervision of the process are just a few examples of obstacles. Not only is this method time-consuming, but it also increases the chance of human error and safety risks, such as material spillage or accidents during operation.
Additionally, the health risks posed by airborne dust cannot be ignored. Prolonged exposure to particulate matter can lead to severe respiratory issues for workers. Industries must prioritize dust control measures to maintain workplace safety and comply with environmental regulations.
Vortex Automated Loading System (VALS)
One of the most advanced solutions addressing these challenges is the Vortex Automated Loading System (VALS). VALS integrates cutting-edge technology to provide an efficient, precise, and safe approach to loading dry bulk materials.
Components and Functionality
VALS’s seamless integration of key components ensures superior performance:
- Loading Spouts: Designed for various dry bulk materials, these spouts prevent material loss and reduce dust emissions with cone-in-cone stacking technology.
- Dual-Axis Positioner: Automatically aligns the loading spout to the truck or vessel hatch with precise X and Y-axis movements.
- Camera and PLC System: Uses cameras and programmable logic controllers (PLC) to locate hatches and maintain consistent, predictable load times.
- Inline Filtration System: Effectively controls dust during the loading process by filtering and returning particulate matter back into the load.
Together, these components streamline operations and set new standards for safety and efficiency.
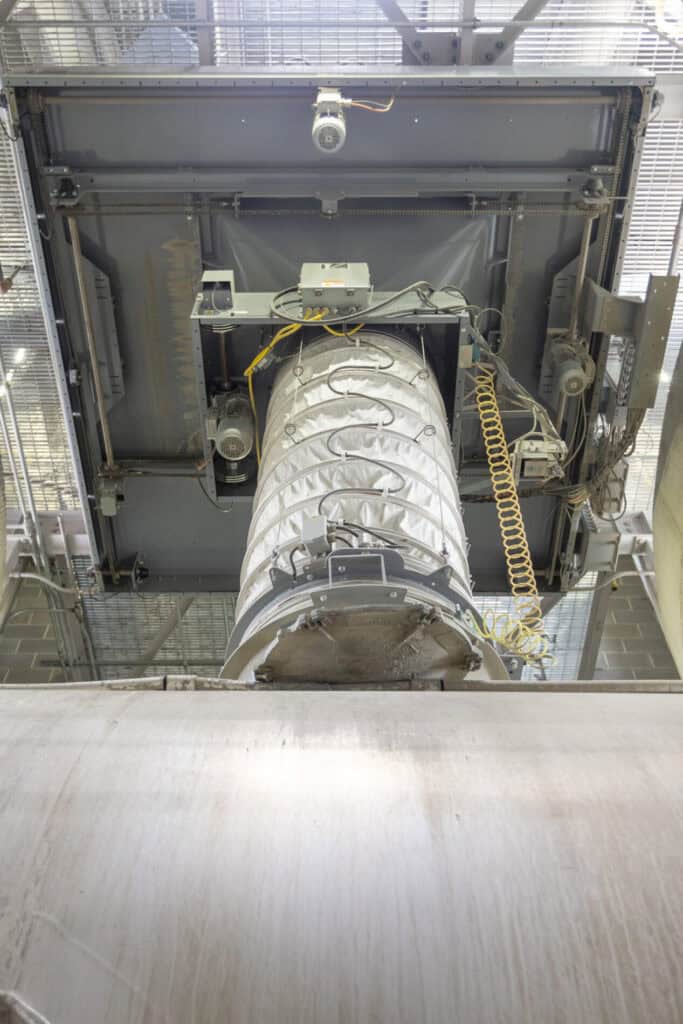
Benefits of Using VALS
Adopting VALS offers several key advantages:
- Improved Safety: Minimizes human involvement, helping eliminate safety-related incidents. Operators and drivers remain safely out of harm’s way during the process.
- Enhanced Efficiency: Automates the alignment and loading process, reducing the time needed to load each truck or container. Operations become faster, smoother, and more reliable.
- Dust Control and Compliance: Integrated filtration systems reduce fugitive dust emissions, protecting both workers and the surrounding environment.
- Reduced Labor Costs: By automating manual processes, VALS reduces reliance on skilled labor, addressing concerns about labor shortages and costs.
The Role of Inline Filtration Systems
An essential feature of VALS is its Inline Filtration System, which plays a critical role in dust collection and pollutant management.
Design and Functionality
Inline Filtration Systems are compact, efficient units designed to:
- Displace dust-laden air.
- Separate particulate matter from the air stream.
- Reintroduce filtered dust back into the material flow.
Unlike central dust collection systems, these units are located directly at the loading site, offering better performance and energy efficiency. With vertically mounted filter cartridges, the design minimizes wear and tear, while automatic reverse pulse jets ensure consistent self-cleaning for uninterrupted operation.
Advantages of the Inline Filtration System
- Energy Savings: Operates only during loading, significantly reducing energy consumption.
- Improved Work Environment: Protects employees from harmful exposure to airborne dust during loading operations.
- Compact Design: Fits into limited space installations, making it ideal for facilities of all sizes.
- Reduced Maintenance Costs: With its durable components and self-cleaning mechanisms, the system requires less frequent upkeep compared to centralized alternatives.
Case Study: Cement Manufacturer in Kansas
A cement producer in Kansas partnered with Vortex to implement an automated loading system for their newly established terminal. Their goal? To improve logistics, enhance safety, and optimize load times.
The Solution
Vortex supplied a complete automated system, including:
- Aero-Slides
- Inline Filtration Systems
- Dual-Axis Positioners
- Enclosed Loading Spouts
With VALS, the facility achieved average truck load times of under 7 minutes while drastically reducing material spillage and labor requirements.
Enhancing Efficiency and Safety with Vortex Systems
From reducing dust emissions to streamlining operational processes, Vortex Automated Loading Systems and Inline Filtration Systems represent game-changing solutions for industries handling dry bulk solids. By addressing critical challenges like safety risks, labor costs, and environmental concerns, these innovations pave the way for cleaner, safer, and more efficient operations.
Interested in optimizing your facility’s efficiency and safety? Explore Vortex’s full range of solutions and start transforming your approach to dust collection and air pollution control today.