As industry expectations rise and product quality standards become more stringent, moisture measurement is no longer a step reserved for lab testing. Instead, it has become an integral part of the production line, helping manufacturers safeguard product quality, boost efficiency, and meet compliance targets.
Why Moisture Monitoring Matters
Moisture plays a key role in determining a product’s texture, weight, stability, shelf life, and even chemical composition. Left unchecked, moisture can compromise product quality, consumer safety, and, as a result, brand reputation. In industries where moisture levels can trigger microbial growth or accelerate spoilage, the stakes are particularly high.
Traditional moisture management methods, such as batch sampling and off-line lab testing, introduce critical delays to the production process. These approaches provide only intermittent, retrospective data that may not accurately reflect the full scope of process variability. As a result, deviations in moisture content may go undetected until well after affected products have progressed through multiple stages of production, leading to costly rework, scrap, or even recalls. On the other hand, to avoid this outcome, manufacturers can tend to overcompensate when moisture levels are detected in the lab, scrapping product that may not have been impacted by the moisture variability.
In contrast, continuous moisture monitoring offers immediate, real-time data that empowers operators to make precise, on-the-fly adjustments. By identifying and correcting moisture variations as they occur, manufacturers can isolate and address only the impacted portion of a production run. This targeted response dramatically reduces material waste and ensures that overall quality standards are consistently met.
Additionally, real-time monitoring minimizes energy consumption by helping to optimize drying times and temperatures. Instead of running dryers longer “just in case,” facilities can fine-tune their processes with confidence, conserving both energy and resources. By eliminating unnecessary production steps and reducing time-to-market, continuous moisture monitoring shifts moisture management from a reactive quality assurance measure to a proactive, strategic tool that drives efficiency across the board.
The Hidden Costs of Poor Moisture Management
When moisture management is reactive instead of proactive, the consequences ripple across operations. High energy usage during drying, rework due to off-spec batches, supply chain bottlenecks caused by spoilage or delays, and lost product from moisture-induced defects all contribute to ballooning operational costs.
In some cases, seemingly minor moisture fluctuations can have outsized effects. For example, a 1% increase in moisture content in a pelletized product can raise the amperage load on equipment, reducing throughput or causing a complete equipment shutdown. In high-volume production environments, these deviations compound quickly, impacting both the bottom line and customer satisfaction.
Industry Focus: Food Manufacturing
In food manufacturing, moisture levels directly affect texture, taste, safety, and shelf life. Too much moisture promotes microbial growth, mold formation, and premature spoilage. Too little, and products become dry, brittle, or nutritionally compromised. Additionally, moisture inconsistencies can lead to product clumping, affect batch uniformity, and interfere with critical processes like drying and curing. These issues not only harm product quality but can also trigger compliance failures in regulated markets.
Continuous moisture monitoring allows food processors to stabilize conditions in real time, maintaining tight control over product quality and reducing recall risk. By managing moisture proactively, companies also reduce energy costs associated with drying and extend shelf life, ensuring products reach consumers in optimal condition.
Industry Focus: Pharmaceuticals
Pharmaceutical manufacturing demands a level of consistency and traceability that leaves no room for guesswork. Here, moisture isn’t just a quality issue—it’s a regulatory one. Variations in moisture content can alter the chemical stability of active ingredients, compromise the efficacy of medications, or affect tablet disintegration and dissolution times.
Regulatory agencies like the FDA require strict documentation and verification of moisture levels, especially in oral solid dose manufacturing. Real-time monitoring helps pharmaceutical producers meet these standards while minimizing material waste, rework, and downtime. Beyond this, integrated data-logging and automated controls reduce human error and ensure that each batch, regardless of production site, adheres to the same moisture specifications—helping manufacturers meet Good Manufacturing Practices (GMP) and pass audits with confidence.
Common Misconceptions Around Moisture Monitoring
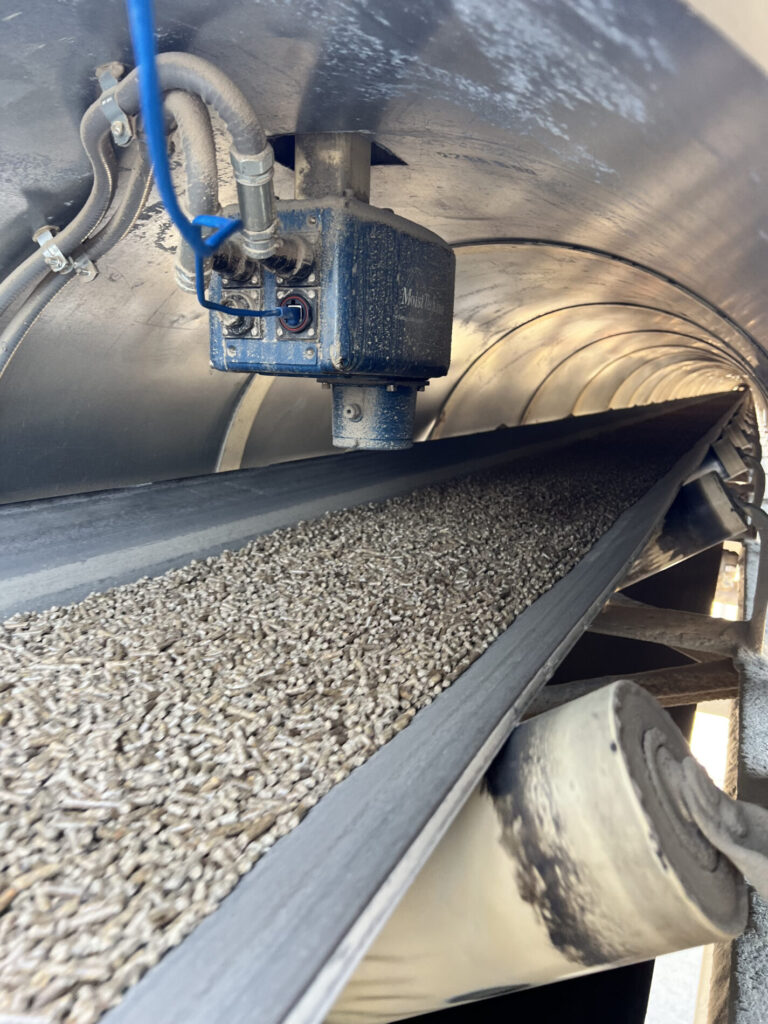
A major misconception in the manufacturing world is the belief that all moisture sensors are created equal. While many companies have adopted near-infrared (NIR) technology to track moisture levels, they often overlook the significant performance differences between sensor models, particularly when it comes to long-term accuracy. Older or less sophisticated sensors tend to suffer from calibration drift over time. Much like an analog clock that gradually loses precision, these sensors slowly deviate from their original baseline, delivering increasingly unreliable data as time goes on.
To address this, manufacturers must schedule regular recalibration visits from service technicians, an added layer of maintenance that can interrupt production, increasing labor costs. Even brief periods of inaccurate moisture readings can lead to substandard product quality, inefficient drying processes, or equipment wear. That’s why advanced continuous moisture monitoring systems that resist calibration drift offer such a distinct operational advantage. These systems are engineered for stability and reliability, maintaining accurate performance over years of operation without the need for consistent recalibration. This not only reduces the burden on maintenance teams but also ensures that real-time data can be trusted when making critical process decisions.
Real-Time Consistency, Site to Site
For companies operating multiple facilities, maintaining product consistency across production sites is a constant challenge. Moisture variability between raw material batches, environmental conditions, or processing parameters can easily introduce inconsistencies that undermine brand integrity. With continuous in-line moisture monitoring, manufacturers can standardize moisture levels across sites. By automating adjustments based on real-time data, operators can ensure uniform product quality, reduce waste, and shorten drying cycles regardless of location.
One provider that has helped manufacturers across industries take control of their moisture management is MoistTech. Their NIR-based sensors are known for providing accurate, non-contact moisture readings in real time, without the calibration drift that plagues many other systems. MoistTech sensors are designed to operate continuously for years without recalibration, making them a reliable option for manufacturers seeking long-term process control with minimal maintenance. With a wide array of industry applications, from food and pharmaceuticals to biomass, paper, and bulk solids, their technology has become a trusted solution for organizations looking to boost product quality and reduce costs.
Making Moisture Detection Work for You
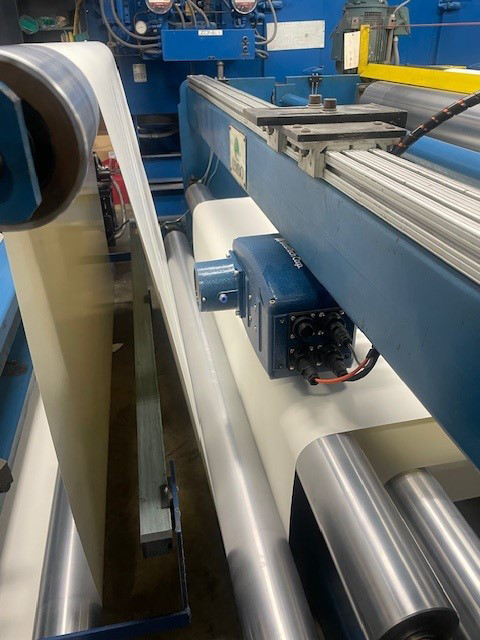
In an era where manufacturing efficiency and quality assurance are inseparable, continuous moisture monitoring offers one of the most actionable, cost-effective upgrades for your production line. Whether you’re trying to extend shelf life in a food product, ensure regulatory compliance in pharmaceuticals, or simply reduce drying costs, managing moisture in real time gives your operation the agility it needs to stay competitive.
The path forward is clear: move from batch testing to continuous monitoring. Equip your facilities with the tools to detect small changes before they become big problems. When moisture is monitored consistently, quality becomes predictable—and that predictability builds trust, performance, and profitability.
Upgrade Your Production Line with Continuous Moisture Monitoring
In an era where manufacturing efficiency and product quality are tightly linked, continuous moisture monitoring stands out as one of the most effective, cost-saving upgrades available. Whether looking to reduce drying time, increase shelf life, ensure regulatory compliance, or maintain product consistency, real-time moisture control offers a clear competitive edge.
Moisture management doesn’t have to be reactive. With MoistTech’s inline moisture sensors, manufacturers gain the ability to detect changes as they happen, act immediately, and maintain control over critical variables. When moisture is managed proactively, quality becomes consistent, and that consistency builds customer trust, operational efficiency, and long-term profitability.