The AZO Cyclone Screener Type DA Vario Containment redefines how processors can achieve both with smarter design, safer maintenance, and no compromise on process performance.
The Industry Status Quo: Bunny Suits and Clean Rooms
When handling active pharmaceutical ingredients (APIs) or other high-risk powders, many processors default to a combination of full-body protective gear (often referred to as “bunny suits”) and dedicated clean rooms to manage safety and hygiene. But these solutions are costly, cumbersome, and inefficient. For example:
- Operators in full PPE face physical strain and longer work times.
- Clean rooms require extensive investment in HVAC, gowning procedures, and space segregation.
- Maintenance becomes a major disruption — often requiring system shutdowns and full decontamination just to inspect or replace a screen.
The DA Vario Containment screener was developed to break free from that model.
Safer Screening, No Clean Room Required
With its innovative flexible liner containment system, AZO’s screener enables complete material handling from screening to maintenance without exposing the operator or the surrounding environment. Here’s how it works:
- Inspection ports with integrated gloves and lighting allow operators to view and manipulate the screen internally without opening the machine to the outside world.
- Component replacement, including the screen basket and dosing screw, is performed entirely within sealed liners. No PPE-intensive procedures, no airborne dust, and no product escape.
- Used components and liners are sealed and crimped off for safe disposal, reducing cross-contamination risk and clean-up effort.
This approach removes the need for additional infrastructure like a clean room, and eliminates operator contact with the product entirely even during maintenance.
Proven Technology with Smart Upgrades
The DA Vario Containment screener is based on AZO’s longstanding and trusted DA cyclone screener platform, which is already known for its reliable, self-dosing operation and compact footprint. The containment version enhances it with:
- Quick-release fasteners for fast tool-free access
- Exchangeable dosing modules to accommodate different performance demands
- Split-valve integration for secure, dust-tight waste or product transfer
Whether you’re processing a high-potency pharmaceutical or a finely milled battery powder, the DA Vario Containment screener brings the same performance you’d expect from a traditional screener, but with vastly superior safety and hygiene.
Reduced Downtime, Improved Ergonomics
One of the biggest hidden costs in hazardous material handling is labor. From donning PPE to adhering to strict clean room protocols, time and human effort are major drains on productivity. This system solves that by:
- Eliminating full-body PPE requirements for basic operations and maintenance
- Allowing routine inspection and part exchange to occur safely inline
- Improving operator comfort and speed, especially during changeovers
These operational advantages are felt every day and add up to measurable ROI over time.
Applications That Benefit Most
While the DA Vario Containment screener is ideal for pharmaceutical manufacturers working with APIs, its advantages apply across multiple sectors, including:
- Chemical production involving toxic or irritant powders
- Food processing environments handling allergenic ingredients
- Additive manufacturing or battery material operations where airborne particles must be tightly controlled
Any facility looking to reduce clean room reliance, lower PPE costs, and enhance containment without sacrificing throughput will find strong value in this solution.
A Modern Approach to Safe Screening
The AZO Cyclone Screener Type DA Vario Containment system brings together the best of two worlds: precision screening and proactive protection. It replaces outdated assumptions about what’s required to handle high-risk materials, delivering a safer, more streamlined, and ultimately smarter alternative to bunny suits and clean rooms.
When the cost of error is high and operator well-being matters just as much as process output, this is the screener that sets a new standard.
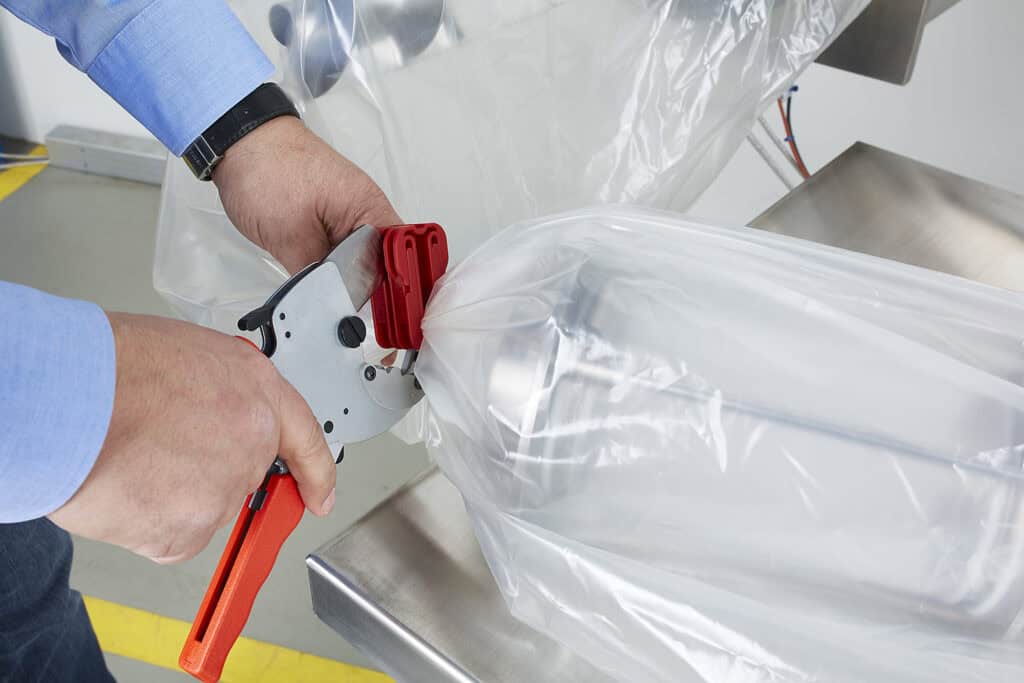
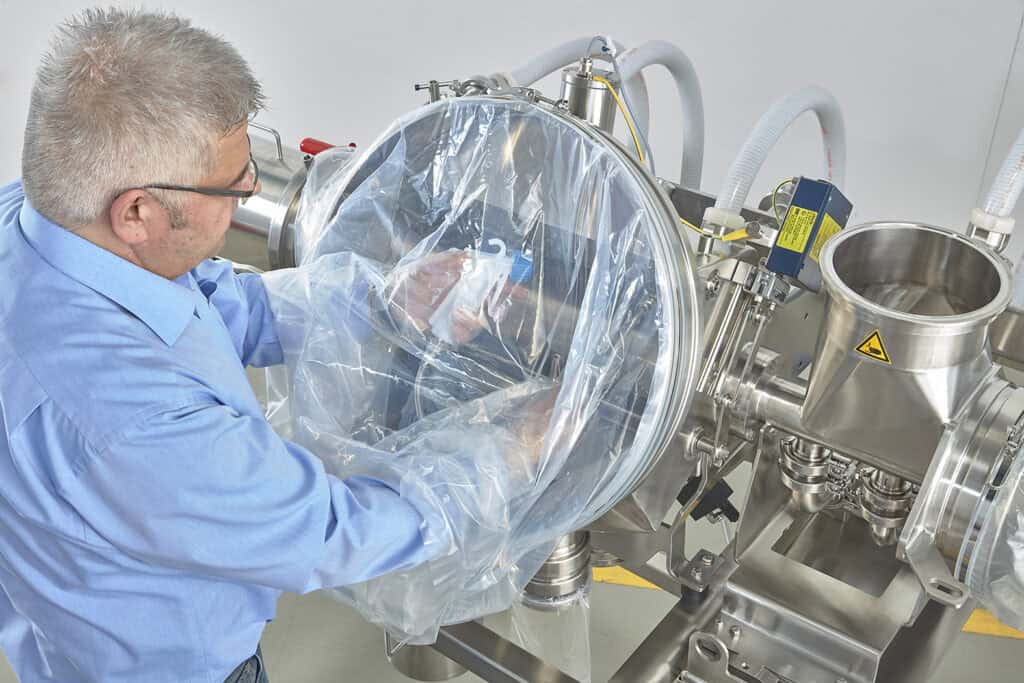