Challenge
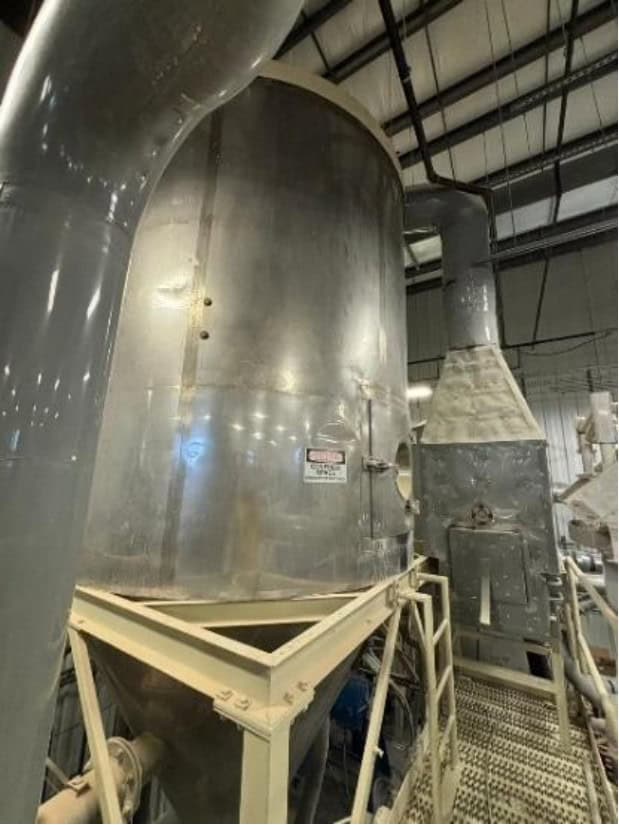
At Piezo Kinetics, Inc., producing top-quality piezoelectric ceramic powders involves spray drying including a binder system that is used to keep the solids in suspension. While effective in molding ceramic bodies, this process posed a recurring challenge: powder caking on the inner walls of the spray dryer.
These deposits required frequent cleaning, achieved through heavy, noise- inducing mechanical knockers that left operators with inefficiency and material loss. The results were not just stress for the spray dryer (Fig. 1) and its operators; the operation produced unusable fine dust and large clumps, wasting valuable powder. Maintenance interruptions and downtime became a costly inevitability.
Approach
Piezo Kinetics sought a smarter solution, one that produced less noise and increased productivity. Artech outfitted the spray dryer with three custom flowsonic® waveguides, seamlessly welded to its steel outer walls. Coupled with ultrasonic converters (Fig. 2) and generators (Fig. 3), the system delivered continuous micro vibrations, keeping the inner walls seamless without interrupting production. The ultrasonic worked like an invisible cleaning crew, preventing material build-up and ensuring optimal performance – all while operating quietly and autonomously.

Result
With the flowsonic® system fully integrated, the transformation was remarkable:
1. Prevention of Powder Build-ups: The ultrasonic excitation effectively prevented powder deposits throughout each run, eliminating the need for noisy, mechanical intervention. The spray dryer’s interior remained homogenous and clean of undesired product agglomerates (Fig. 4).
2. Increased Production Yield: Freed from excessive caking, the recovered powder was now largely reusable. Finer particles seamlessly flowed through production processes, while coarse residues were easily screened out, ensuring maximum material utilization.
3. Minimal Maintenance Downtime: Operators no longer had to frequently access the confined spray dryer for maintenance. This not only enhanced worker safety but also significantly reduced operational interruptions.
4. Quieter, Streamlined Operations: The ultrasonic system ensured a more quiet, efficient process, fostering a more pleasant work environment.
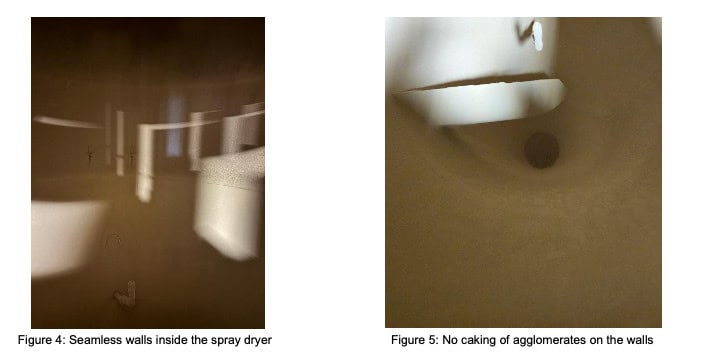
Through this innovative approach with Artech Ultrasonic Systems, Piezo Kinetics turned a persistent production challenge into a streamlined, efficient workflow. The adoption of the flowsonic® ultrasonic system exemplifies how cutting-edge technology can unlock unparalleled benefits, from reduced waste to enhanced productivity.