Pneumatic conveying provides a cost-effective way to handle and transfer powdered and bulk granular materials easily with very little loss. It is suitable for a range of process industries such as; Food and Beverage, Pet Food, Chemicals and Detergents, Renewables and Specialist Materials.
What are the categories of pneumatic conveying?
Pneumatic conveying can be separated into two categories, lean phase and dense phase.
Lean phase: Lean phase conveying is the most common conveying method for powders or granules and can generally be split into two further categories:
- Dilute phase: where conveying gas velocities are typically in excess of 17-18 m/s and conveying pressure or vacuum is low; usually below 0.1 barg. The material particles remain wholly suspended in the conveying gas stream and the concentration or solids loading ratio (mass of solids/mass of gas) is relatively very low. Dilute phase conveying is ideal for materials with low bulk density and that is non-abrasive. Typical air movement devices for this type of conveying would be a Fan or Side Channel Blower/Exhauster.
- Negative Pressure Lean Phase
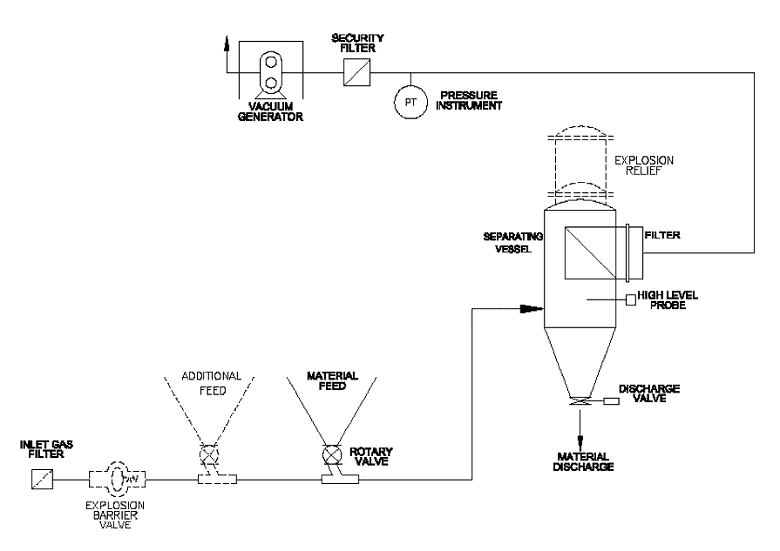
- Positive Pressure Lean Phase
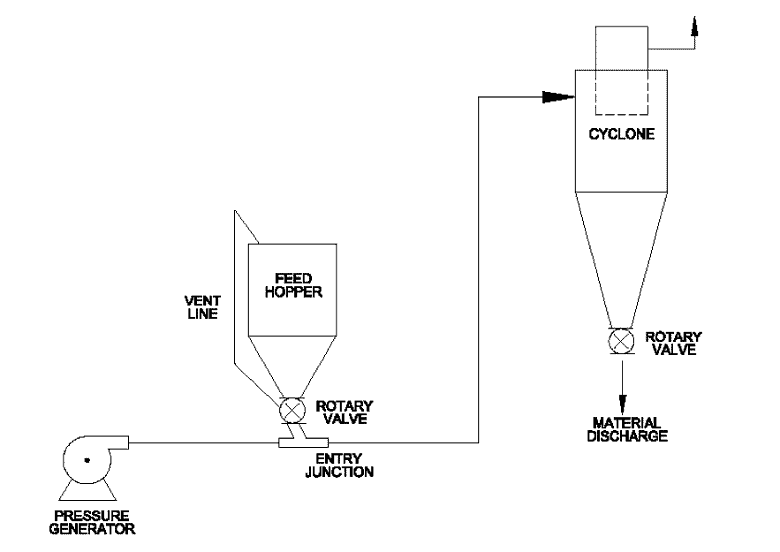
- Medium Phase: Medium phase, where conveying gas velocities are typically in excess of 17-18 m/s and conveying pressure or vacuum is typically up to 0.35 barg. The material particles remain substantially suspended in the conveying gas stream and the concentration or solids loading ratio is relatively low. Typical air movement device for this type of conveying would be a Roots Blower/Exhauster.
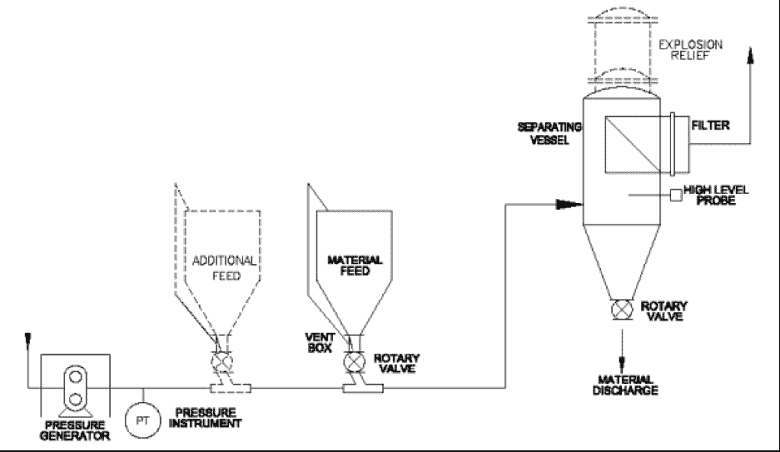
Dense Phase: Dense phase, where conveying gas velocities are typically in the range 6-18 m/s and conveying pressures are above 1 barg. At higher conveying velocities, the material particles can still be substantially in suspension, however, at the lower velocities, the material will be predominantly in contact with the conveying pipe and will move in waves or plugs. This type of conveying is more commonly used to convey materials over longer distances and at higher throughputs, where the limitations of air movement devices such as Fans and Roots Blowers become prohibitive. This method is also commonly used to convey fragile or abrasive materials at low velocities in order to minimise either material damage or system damage. Typical air movement devices for this type of conveying would be a compressor of liquid ring pump.
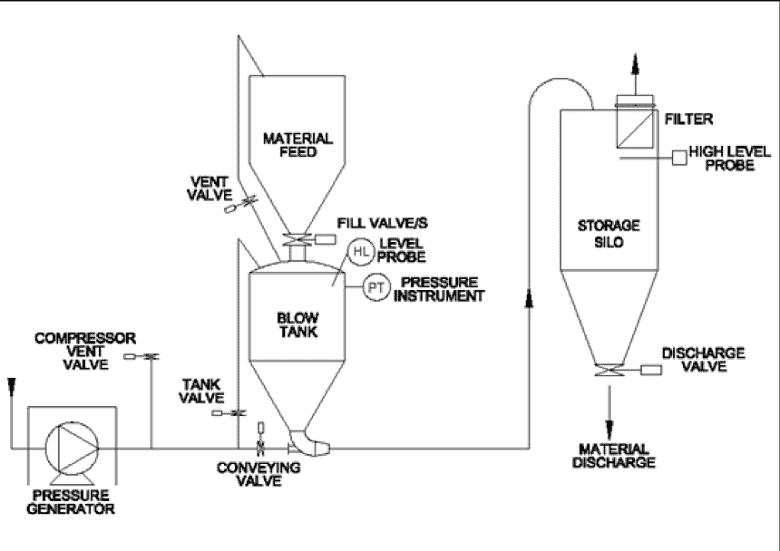
- Continuous Dense Phase
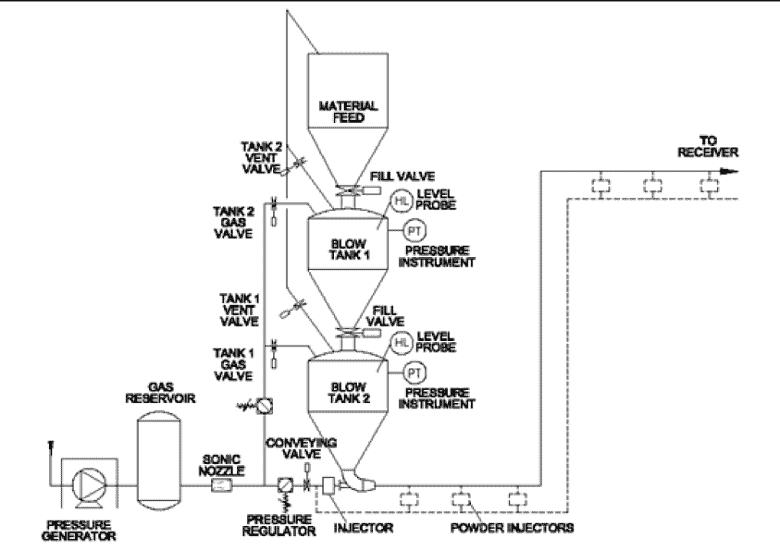
What does a pneumatic conveying system include?
Material introduction point, piping, a receiving point, and a gas flow movement device.
Advantages of pneumatic conveying.
- Due to the compact nature of the conveying pipe transfer line, a pneumatic conveying system can be routed around existing equipment, giving more flexibility than a mechanical conveying system.
- Can run vertically or horizontally over a long distance.
- As the system is enclosed, there is protection against dust emissions to the atmosphere and also protection of the conveyed material from external contaminants.
- Pneumatic conveying systems can be easier and more cost effective to maintain than a mechanical conveying system – fewer moving parts.
- The ability to maintain a controlled atmosphere around the material.
- Minimise system wear from abrasive materials and damage to fragile materials.
- Take up less floor space so are easier to locate.
- Can have multiple pick up and discharge points.
Disadvantages of pneumatic conveying.
- Pneumatic conveying systems need to change air pressure to produce the conveying power and as a result, are less efficient than a mechanical conveyor.
- Typically used to transfer smaller volume throughputs of materials, although they can be used to transfer higher volume throughputs, this may present greater challenges.
- As the dust needs to be extracted from a pneumatic conveyor at the end of the system, a larger dust collection system may be required.
- Materials with high bulk densities, larger particles, and sticky or wet materials may not be suitable for pneumatic conveying.
Things to consider when looking at your application.
- Particle size distribution and shape
- Air Humidity
- Moisture content
- Angles of flow, slip, and repose
- Density
- Fluidisation
- Hardness / Friability
- Temperature
- Concentration
- System throughput
- System distance
What next?
We have explained a few of the variables that make scoping, designing and installing a pneumatic conveying system so complex. Mistakes can be incredibly costly both at the outset and further down the line. To avoid this, call WBL Engineering Ltd to discuss how we can design a system that works not only for your process but also for your budget.
If you would like more information on pneumatic conveying systems, please do not hesitate to contact WBL.