As its product line has grown, Systemic Formulas has streamlined production to meet demand, replacing its Paddle Mixer with a Rotary Batch Mixer that cuts mixing and cleaning time by 80 percent.
Blending 15 to 60 ingredients per batch
Products are batched according to recipes that may contain between 15 to 60 raw materials, including vitamins, minerals, enzymes, RNA/DNA tissue factors, amino acids, and botanicals. With so many products, from adrenal health to macular degeneration and weight management supplements, Systemic Formulas’ production process must provide both flexibility and accuracy.
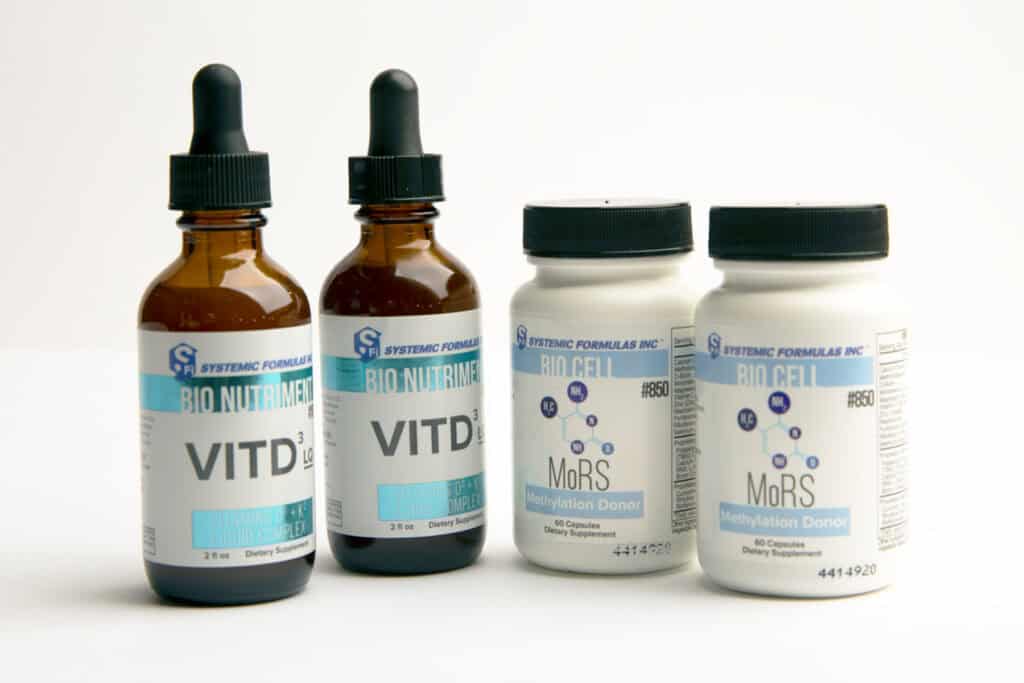
The company operates one shift per day, 5 to 7 days per week, depending upon demand. “We create one or two batches in an 8-hour shift,” he explains, “with a stringent cleaning protocol required between batches.”
Materials are reduced to the desired particle size in a hammer mill, transported in 44 gal (194 l) lined food-handling containers, and then gravity fed into the Rotary Batch Mixer, a 40 cu ft (1132 l) model 700-TS-40-SS from Munson Machinery.
Batches run as small as 100 lb (45 kg) and as large as 1147 lb (521 kg), with the average batch weighing 880 lb (400 kg) to yield 800,000 half-gram capsules which are packaged into bottles.
Incorporating liquid additions without clumping
The batch is blended in 4 to 6 minutes, versus 20 minutes for the paddle mixer. “No matter the particle size, it does not under- or over-mix, providing the uniform consistency we need,” says Hansen.
The mixer’s internal mixing flights impart a, four-way mixing action that tumbles, folds, cuts and turns the material gently, without the shear of agitated machines.
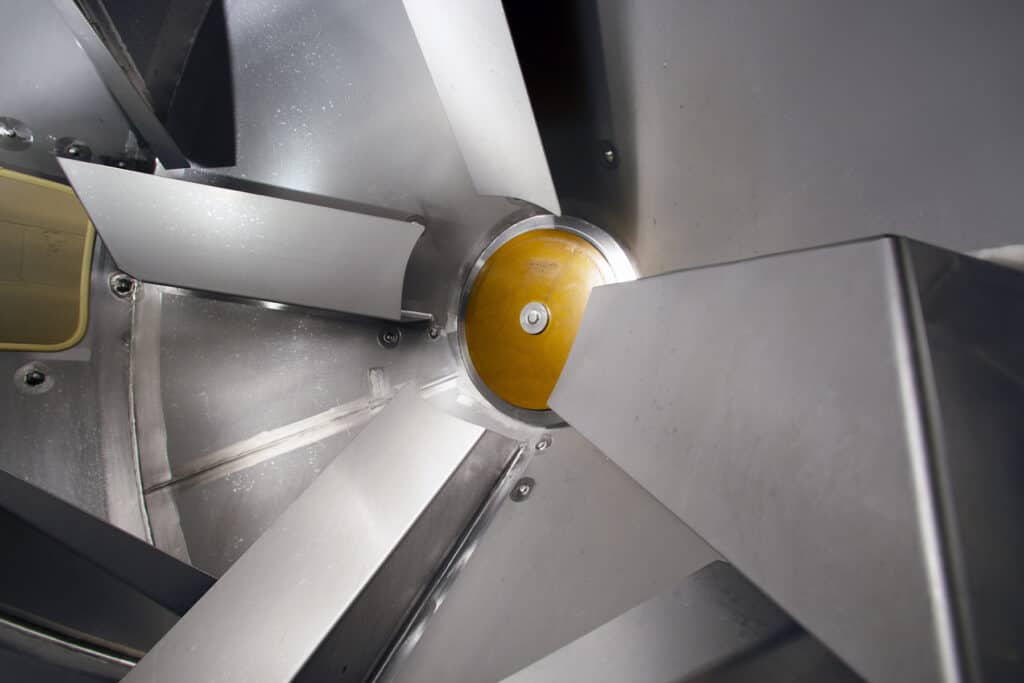
To add liquids, an optional pressure pot with an internal atomizer sprays a mist of hemp, wintergreen, grapeseed and other oils onto a moving bed of material for rapid and uniform distribution.
“The aerating system allows us to add oils without wet spots or clumping,” comments Hansen. “Air gaps constantly move the surface area so no snowball-sized clumps occur. The result is a uniform yield that we could not achieve with our paddle mixer.”
At the conclusion of a blending cycle, the drum continues to rotate, causing the mixing internal flights to elevate the material toward and through a plug gate valve, eliminating stratification associated with discharging of static batches. “The mixer completely discharges,” says Hansen, eliminating material waste and reducing cleaning time.
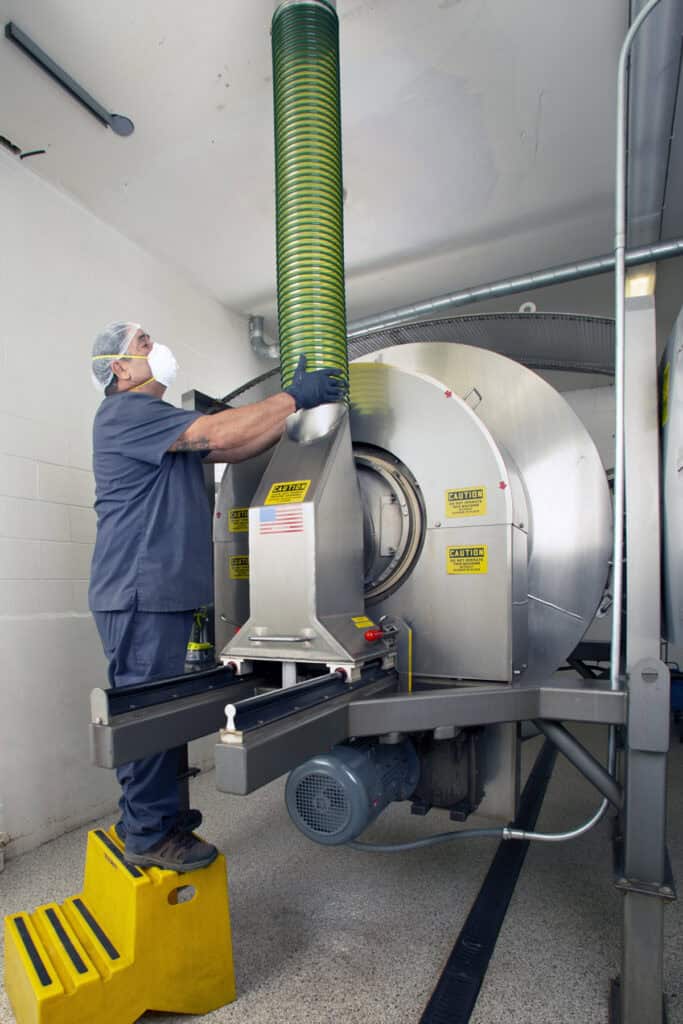
Sanitizing five-times faster
“Between each batch, we treat the mixer like a big washing machine,” says Hansen. It is prewashed, soaped down and rinsed. A second soap cycle is run with agitation balls and dried with clean rags or towels. The unit is then rescrubbed, rinsed, sanitized and air dried, after which it is wiped down with alcohol, ready for the next batch.
“Cleaning took 2.5 to 3 hours with our old mixer, which operated like a cement truck with paddles.” notes Hansen. “With the Rotary Batch Mixer, we pared cleaning cycle time down to 30 minutes. The large discharge gate and multiple doors give us easy access for final wipe-down cleaning.”
Maintaining rigid quality control
Regulated by the FDA, Systemic Formulas must trace the lot number of the finished product back to the origin of the raw materials. “Having our own in-house lab gives us control over raw material vendors,” says Hansen. “Our CEO is a PhD biochemist, so our sourcing agents must find the best vendors of specialty materials. Our purchasers even understand harvest cycles to obtain the purest herbs for our product.”
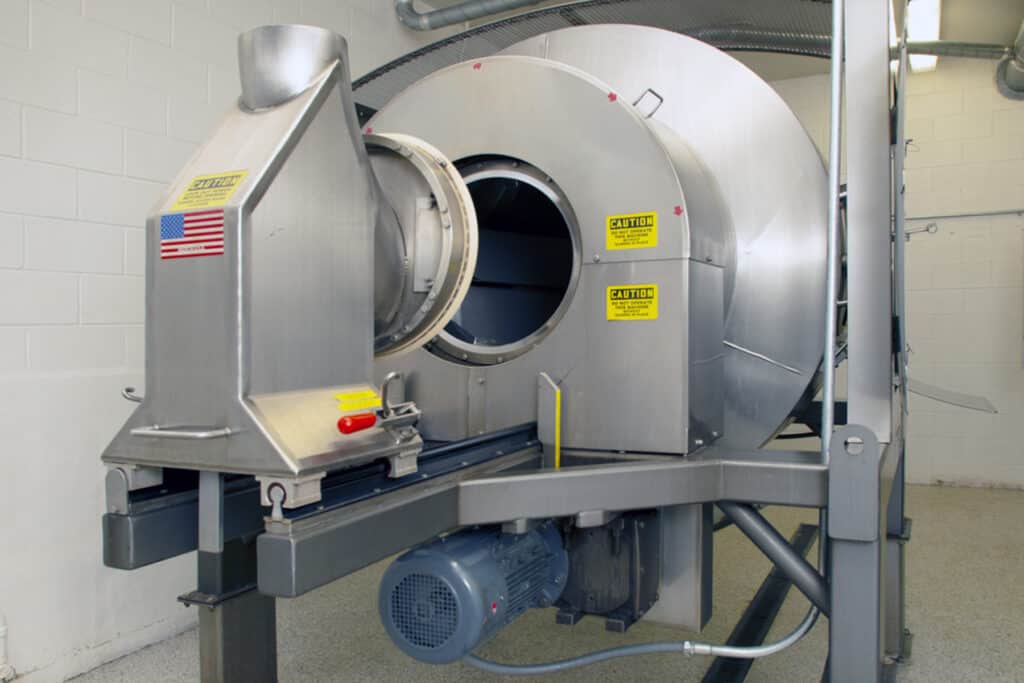
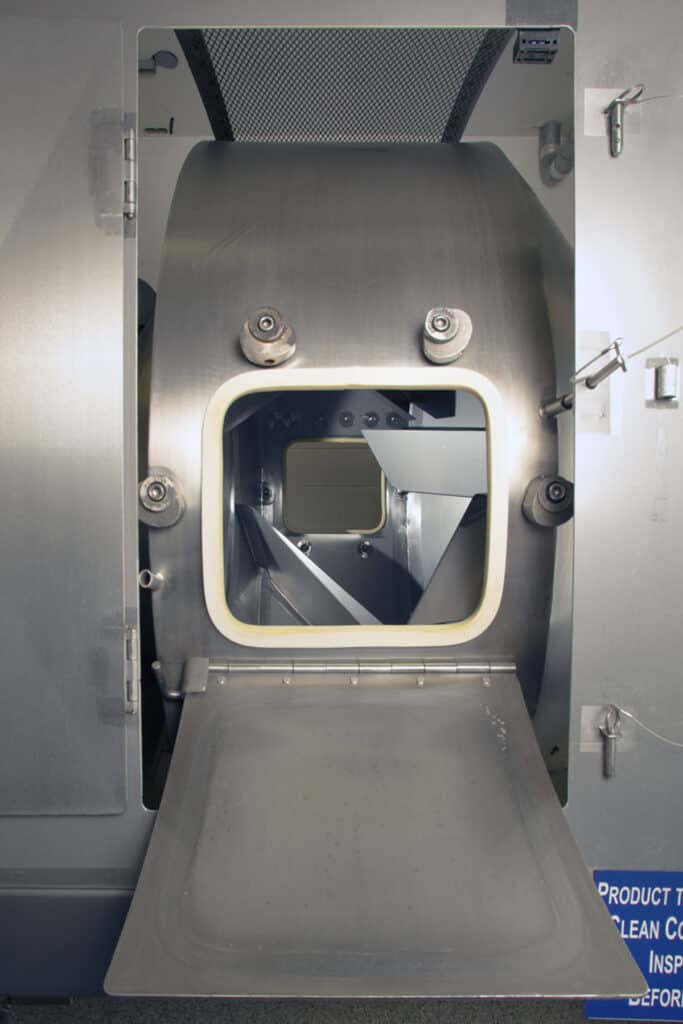
“These delicate ingredients are thoroughly blended without damage,” observes Hansen.
“We’re a niche player in the herbal and vitamin/mineral supplement industry,” he says. “Systemic Formulas is distinct because our products are unique and of the highest quality. It follows that our operators and equipment need to be the best.”