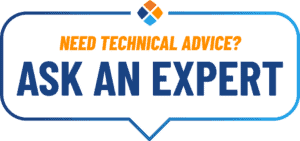
Because both questions and answers will be posted, please make sure to only include information that you are willing to have appeared on the site or advise us about which details should not appear.
Please also let us know if there are any other technical areas for which you’d like to see us line up authorities — or if you want to become an expert of BulkInside yourself.
Experts are available in the listed categories.
BulkInside reserves the right to omit questions. If your question is chosen, it will appear with the Expert answer on the site. Please check back frequently to see the answer to your question and others submitted by people in your industry.
Submit a Question
Please send us your question; we will forward it to the appropriate expert and post the answer as soon as possible.
"*" indicates required fields