While manufacturers may think they are taking all the necessary precautions, there is one often underrated risk factor in a processing line that involves bulk dry products: the flexible connectors used to transfer product between pieces of equipment.
It can be surprising to learn that old-style clamped flexible connections not only jeopardise product integrity and quality, but they also pose significant risks to the health and safety of factory workers.
From combustible dust explosions to physical injuries, the potential hazards posed by these connectors can be serious.
The Risks Associated with Traditional Flexible Connections
1. Dust Leakage and Explosion Risks
One of the most critical safety threats is combustible dust buildup. When processing powders, any dust leakage into the surrounding factory environment becomes a ticking time bomb. Traditional hose-clamped flexible connectors are notorious for allowing small amounts of product to escape, especially under pressure. Over time, this dust accumulates on surfaces.
With just a small spark—potentially from static build-up—an airborne dust cloud can ignite, leading to catastrophic explosions.
Transition points between equipment are particularly high-risk areas. Not only is product movement more turbulent here, but many flexible connectors are also made of non-conductive materials, such as rubber or silicone. These materials allow static charges to build unchecked, creating a perfect ignition source.
Furthermore, most traditional connectors are not explosion-resistant, meaning that if an explosion occurs inside the processing line for any reason, the connector is likely to rupture, suddenly releasing flames and gases into the workplace.
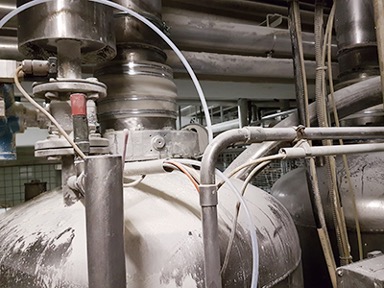
2. Hand Safety Risks During Maintenance
Frequent maintenance and cleaning are essential for hygienic operation, but traditional flexible connectors often require time-consuming disassembly involving tools and clamps.
For plants that process multiple products on the same line, this can involve frequent changeovers and CIP cycles.
Workers must manipulate hose clamps or struggle with awkward connectors, putting their hands at risk of pinching, cuts, or using sharp tools like screwdrivers in sometimes difficult-to-reach locations.
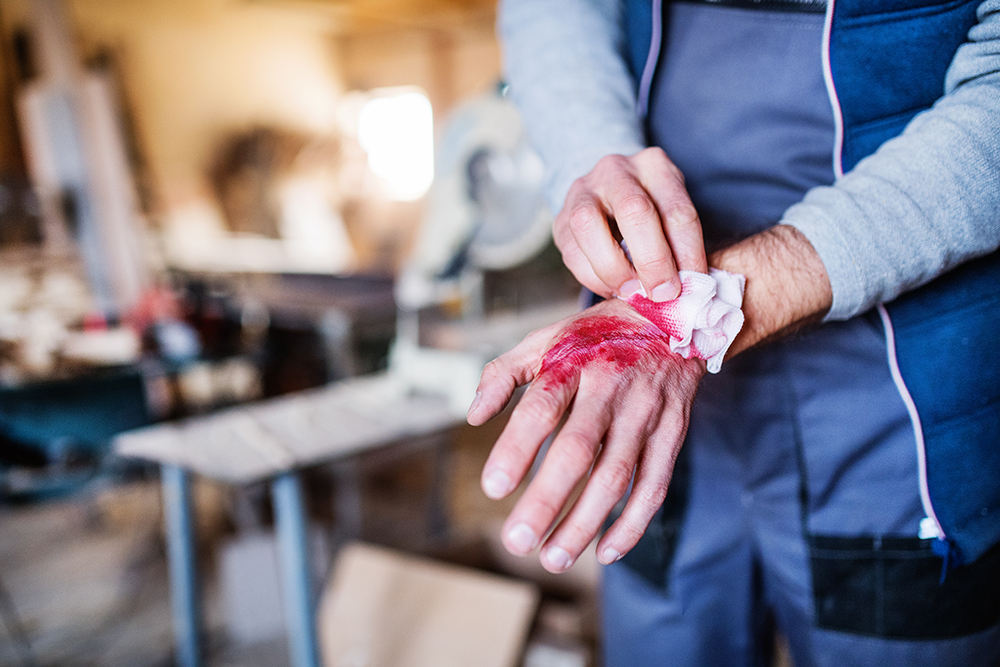
3. Access to Dangerous Locations
The fact that flexible connectors allow easy access to the product flow can pose additional risks when they are located near hazardous equipment, such as above rotary valves or rotating knives.
The use of standard clamped connectors in these areas means that any member of staff could effectively gain access by removing the clamps, presenting a significant risk of injury.
4. Bulk Bag Loading Hazards
Bulk bag loading systems are another significant point of risk. In conventional setups, the lack of a fully sealed connection between the bag and the loading spout can result in dust emissions when the bag is filled.
Airborne dust during bulk loading contributes to combustible dust hazards and poses inhalation risks to workers directly involved in the operation.
The other major concern for many bulk bag loading heads is the potential pinch points for staff’s hands while attempting to secure the neck of the bulk bag.
Fortunately, there is a safer flexible connector solution: the BFM® fitting system.
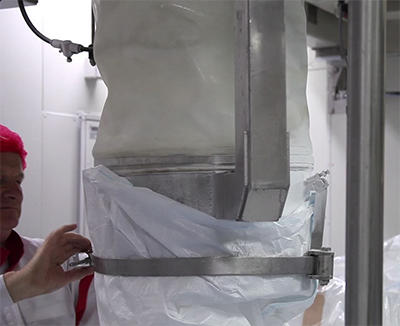
7 Reasons Why the BFM® fitting System Is the Safer Choice
The BFM® fitting system directly addresses each of these major safety concerns, offering a game-changing alternative to outdated flexible connection methods.
1. A True 100% Seal That Prevents Dust Leakage & Contains Explosions
Unlike hose-clamped connectors, the BFM® fitting system features a patented snap-fit design that creates a 100% sealed connection.
Made with high-quality, durable materials like the ether-based polyurethane Seeflex 040E, these connectors maintain their seal even under constant pressures of up to 5 PSI (34.5 kPa).
This seal prevents dust from escaping at product transition points, significantly reducing the likelihood of combustible dust accumulation within the factory environment.
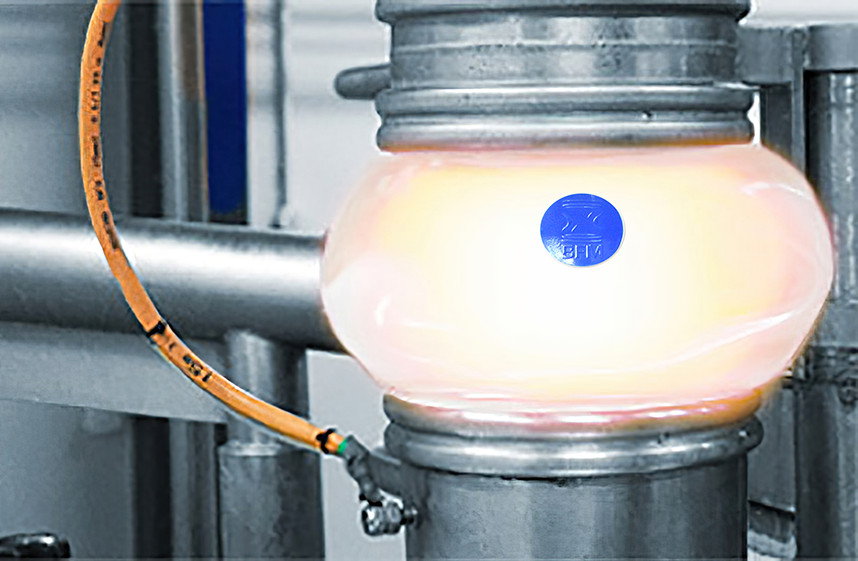
By virtually eliminating dust emissions from connection points, the BFM® fitting system directly reduces the risk of secondary explosions caused by airborne dust.
If there is an explosion inside the process equipment for any reason, the BFM® fitting’s design makes it highly explosion resistant, containing the dangerous gases and flames inside, rather than giving way like clamped connectors.
2. Anti-Static Materials Minimize Ignition Sources
BFM® fitting offers static-dissipative materials such as Seeflex 040AS and Teflex NP Black, ensuring that any electrostatic charges generated during product flow are safely dissipated through grounded pipework.
These materials have been rigorously tested and certified for use in ATEX and IECEx hazardous zones, providing processors with confidence that they are minimising the risk of spark generation at connection points.
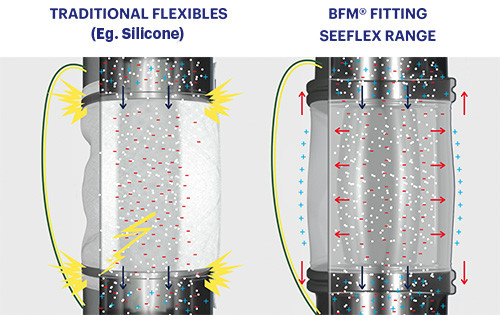
3. No Tools, No Hands Near Clamps – Safer Maintenance
One of the most worker-friendly aspects of the BFM® system is its simple installation and removal of connectors. The snap-fit mechanism enables connectors to be removed and replaced quickly by hand, without the need for tools. This drastically reduces the risk of hand injuries, cuts, or burns during routine maintenance.
In fact, because the system is so quick and easy to use, maintenance teams are less likely to delay connector inspections or cleaning, enhancing overall plant hygiene and safety.
4. Additional Hand-Safe Options for More Dangerous Locations
Above rotary valves, rotating knives, and other hazardous positions, several layers of safety can be added using the TR (Tool Release) product range.
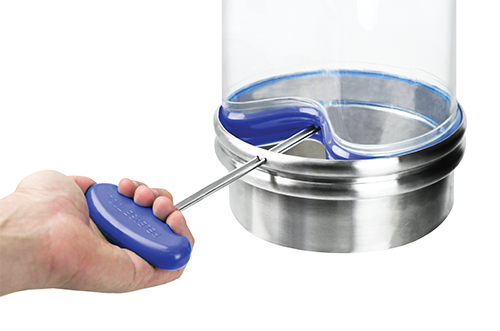
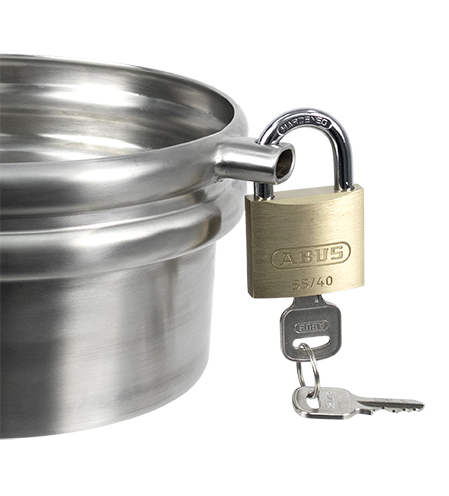
The BFM® TR connectors have a much firmer snap band, making them virtually impossible to remove by hand. A specially shaped tool is inserted through a hole in the top of the spigot to release the connector from the spigot. Only a designated holder of the special TR tool can remove the connector as a safety control.
A TR ‘Lock-Out’ system (shown left)can also be added to prevent any improvisation of a tool to try and access the release hole.
5. Monitoring System Option to Know When your Connectors are Removed
For the ultimate peace of mind, you can monitor when a BFM® fitting is removed in potentially dangerous areas with the Pneumatic Monitoring System.
This system works by pumping pressurised air between the cuff of the BFM® connector and the spigot. Air-line sensors immediately detect if this outward pressure is released as the connector cuff gets pushed inwards anywhere around the connector when it is being removed, setting off an alarm and/or shutting off any moving parts below.
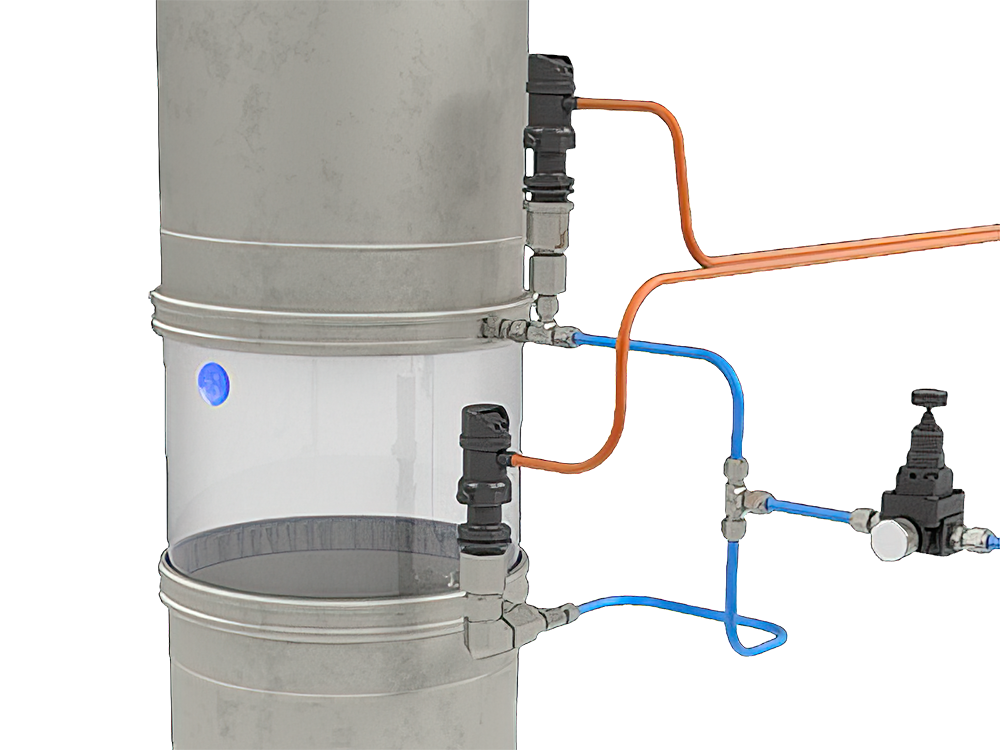
6. Cleaner, Safer Bulk Bag Loading
BFM® also provides specially designed bulk bag loading connectors that create a fully sealed interface between the loading spout and the bag.
This virtually eliminates dust emissions during filling, protecting operators from inhalation risks and contributing to a safer, cleaner environment.
Additionally, by eliminating the need for clamps, bars or cages, the BFM® Bulk Bag Loader prioritizes workplace safety by removing pinch points that pose a risk to operators’ hands.
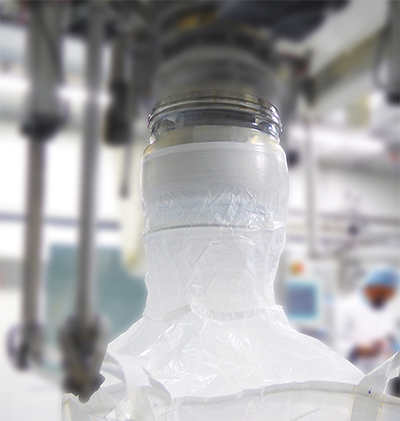
7. Added Protection with Dual Layer Options
For plants operating in highly explosive environments or with particularly dangerous products, BFM® fittings can be installed in a ‘dual layer’ configuration.
In the unlikely event that the inner connector fails for any reason, the outer connector acts as an immediate containment, preventing dust from reaching the factory floor.
This innovative approach can also allow companies to designate lower-risk ATEX zones around their equipment, saving on costly explosion-proofing requirements.
In an industry where worker safety and regulatory compliance are non-negotiable, the flexible connectors you choose matter more than you might think. Traditional hose-clamped connectors introduce unnecessary risks—dust leakage, static build-up, hand injuries, and bulk loading hazards—that can have devastating consequences.
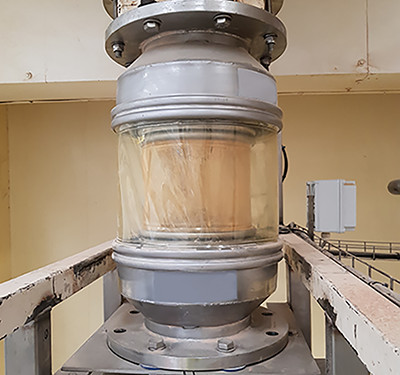
The BFM® fitting flexible connector system offers a proven, globally recognised solution that not only eliminates these risks but also improves operational efficiency and plant hygiene. By investing in safer connections, processors protect their people, their product, and their reputation.