A critical operation is fluidized bed granulation (FBG), where granule moisture and particle size distribution (PSD) are key quality attributes (CQAs) impacting product performance. Precise control over these attributes is not just operational; it’s a regulatory imperative for consistent product quality.
Historically, monitoring these attributes in real-time during FBG has presented significant hurdles. Traditional methods often involve manual sampling and offline analysis, leading to delays, potential for human error, and a reactive approach to process adjustments. While Near-Infrared (NIR) spectroscopy offers in-line real-time data, its standalone predictive power can is limited by disparate systems. This study enhanced prediction by synergistically combining PAT data with real-time FBG process control. This required a robust, intelligent process automation platform for seamless data acquisition, precise control, and comprehensive integration – a role fulfilled by InnoGlobal’s Smart manufacturing platform called SmartX.
The Intricacies of Granulation Control: A “Black Box” Challenge
FBG is complex, involving particle suspension and binder spraying, with air flow, spray rate, and temperature influencing granule properties. Without precise, real-time insights from intelligent sensors, FBG often operates as a “black box.” Traditional methods suffered from information lag, sampling bias, and limited data correlation, leading to reactive adjustments and scalability issues. These challenges highlight the need for advanced PAT solutions providing continuous, reliable, integrated data streams for proactive, predictive control, especially for real-time process monitoring in bulk handling.
SmartX: The Foundation for Intelligent Process Development
InnoGlobal’s SmartX platform addresses these complex challenges in advanced manufacturing. In study with the Pharmaceutical Manufacturing Technology Centre (PMTC) at the University of Limerick, titled “Merging Real-Time NIR and Process Parameter Measurements in a Fluidized Bed Granulation Process to Predict Particle Size” (Link: https://www.mdpi.com/1999-4923/17/6/720) aided in enhancing the prediction performance of endpoint particle sizes via a merged-PLS model to enhance the process understanding and control of a Fluidized Bed Granulation Process. The comprehensive process automation platform offered capabilities in connectivity, data acquisition, real-time control, and intuitive interaction.
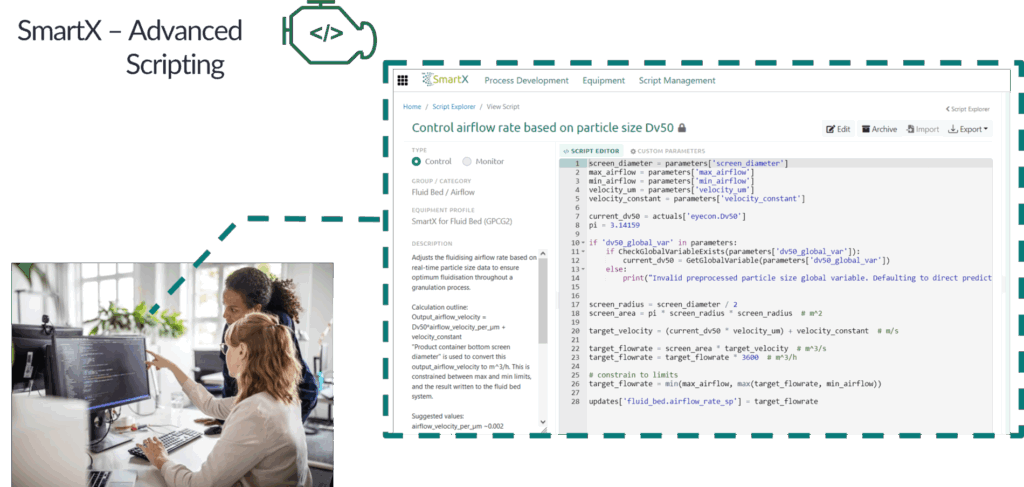
Key features instrumental in this research include:
- Universal Connectivity & Intelligent Sensors: SmartX boasts multiprotocol device connectivity, effortlessly integrating a vast array of intelligent sensors and manufacturing equipment (e.g., Wurster fluid bed, in-line NIR spectrometer, temperature, humidity, airflow, pressure, spray rate sensors). Via Communication methods such as OPC UA, MQTT, TCP/IP, Profinet, RS485 unified connectivity eliminates data silos, making all process information accessible in a synchronized environment.
- High-Fidelity Data Acquisition: Robust capabilities allowed high-frequency, synchronized collection of spectroscopic data (from NIR) and discrete process parameters. This precision was paramount for developing multivariate models based on exact correlation, ensuring data integrity for analysis.
- Real-time Process Control & R&D Automation: SmartX provided advanced control functionalities for precise FBG parameter manipulation. This enabled automated, systematic variation of conditions during experimental runs, generating comprehensive datasets on process variability and granule properties. This automation in an R&D environment ensured reproducibility and validity of experimental batches, accelerating discovery.
- Intuitive User Interface (UI): A touchscreen UI designed by the operator allowed monitoring of real-time data, adjusting parameters, and overseeing runs with ease. This human-centric approach facilitated immediate insights and informed decision-making during experiments.
- Scalability and Flexibility: The SmartX architecture is inherently scalable, allowing insights and control strategies developed in R&D to transfer to pilot or production scale.
- Data Integrity and Traceability: Robust data management ensured all collected data was secure, unalterable, and fully traceable, meeting GMP regulatory requirements such as 21 CFR part11.
Driving Experimentation and Deepening Insights
The application of SmartX was pivotal in executing the study’s methodology, enabling the novel “merged-PLS model.” The core challenge was combining continuous NIR spectral data with influential FBG process parameters for superior particle size prediction.
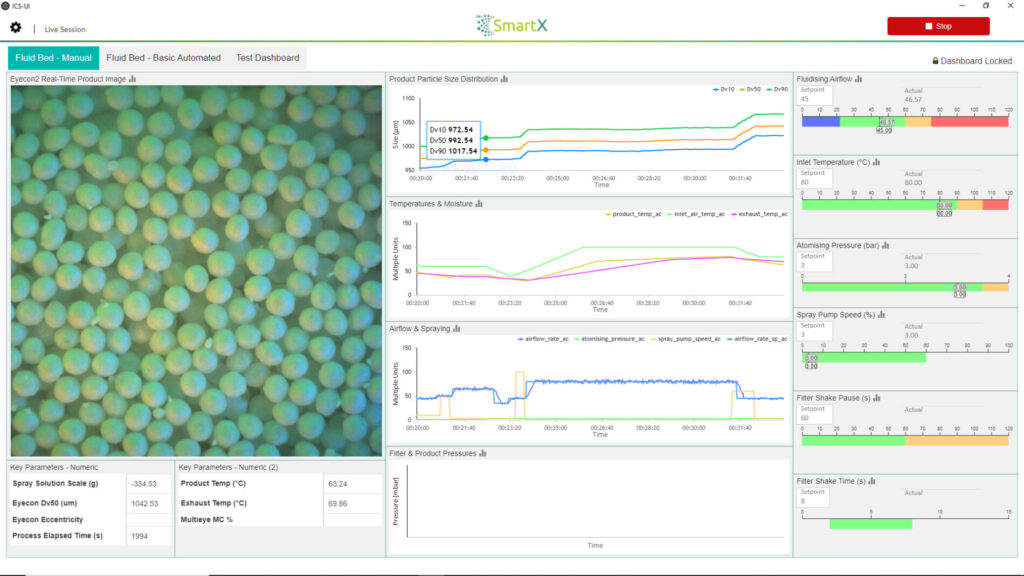
SmartX facilitated this by:
- Orchestrated Experimental Design: Protocols executed set and maintained the critical FBG parameters for process control. This automated control allowed systematic exploration of the process window.
- Synchronized Data Stream Integration: SmartX perfectly synchronized high-frequency NIR data with FBG process parameters. Crucially, this included data from the PAT Eyecon2 providing image-based particle size analysis. As the sensors collected data, SmartX simultaneously logged FBG data of temperature, airflow, spray pressure, and other variables at the exact timestamp. This data alignment, integrating intelligent sensor outputs, was fundamental, making the “merged-PLS” approach possible.
- Real-time Monitoring & Visualization : The SmartX interface provided real-time dashboards displaying both the NIR data from and Particle size data from Eyecon2. The visual feedback allowed researchers to observe dynamic granulation evolution, identify critical points, and understand how parameter changes manifested in NIR signals and developing granule properties. This significantly enhanced process understanding.
- Accelerated Data Processing for Model Development: High-quality, synchronized data was available for analysis, eliminating time-consuming manual data extraction and pre-processing. Researchers exported clean, aligned datasets, significantly accelerating the iterative process of partial least square (PLS) model development and refinement, leading to faster insights and more efficient model optimization.
- Facilitating the Merged-PLS Model: The very premise of the “merged-PLS model” – combining NIR and process parameters – relied entirely on synchronized data from analytical instruments and the process control system.
Results and Enhanced Process Understanding
The results of the study, were highly significant. For all considered particle size fractions (Dv10, Dv25, Dv50, Dv75, and Dv90), the “merged-PLS model” consistently yielded an improved root-mean-squared error of prediction (RMSEP) compared to models using NIR data alone or process parameters alone. This improvement was consistent across various validation scenarios, including challenging analyses with limited batches, demonstrating the model’s robustness and generalizability.
Implications of enhanced predictive performance:
- Superior Real-time Prediction: Accurate, reliable real-time PSD prediction during FBG.
- Deeper Process Understanding: By combining NIR with process parameters, the model and researchers gained a holistic understanding of how operational settings directly influence spectroscopic signatures and resulting particle size. This moves beyond simple correlation to a more profound insight into the underlying process dynamics.
- Enabling Predictive Control: Accurate real-time prediction allows a shift from reactive control to predictive control (adjusting before a deviation occurs). This proactive approach significantly reduces batch variability, minimizes waste, and ensures consistent product quality.
- Accelerated Process Development: Rapid data collection, analysis, and modeling within a Smart manufacturing environment drastically reduces time and resources for process development and optimisation. This means faster time-to-market for new products or improved process efficiency for existing products.
Conclusion: The Future of Smart Manufacturing
This study demonstrates how InnoGlobal’s SmartX platform served not just as a process automation platform, but drove rapid experimentation, enabling deeper insight into fluidized bed granulation complexities. By seamlessly connecting diverse intelligent sensors and instruments, ensuring high-fidelity synchronised data acquisition, and facilitating real-time process control for R&D automation. SmartX enabled researchers to develop a novel and significantly improved predictive models.
The success of the “merged-PLS model” is a testament to the power of integrated data and intelligent automation. It underscores SmartX’s role as a critical enabler for manufacturing companies embracing Industry 4.0 and 5.0 principles. By empowering enterprises to connect processes, unlock valuable data, and equip teams so they can build sustainable, resilient, human-centric production capabilities.