The discharger frame is mounted on castors for in-plant mobility, while a hinged sub-frame supporting a surge hopper, flexible screw conveyor and support mast can pivot down for manoeuvring through doorways and low-headroom areas.
The IBC frame is forklifted onto receiving cups, which position the IBC outlet onto the surge hopper inlet. Material flowing from the IBC into the charging adapter of a flexible screw conveyor is propelled at an incline, and discharged into elevated process equipment and storage vessels.
The conveyor handles a broad range of free- and non-free-flowing bulk solids ranging from pellets to sub-micron powders with no separation of blended products. The flexible screw is the only moving part contacting material, and is driven by an electric motor positioned beyond the discharge point, preventing material contact with seals.
Ready to plug in and run, the mobile unit can serve multiple functions throughout the plant. It can be rolled to a cleaning station where a lower clean-out cap on the conveyor tube can be removed to flush the smooth interior surfaces with steam, water or cleaning solutions, or to fully remove the flexible screw for cleaning and inspection.
The system is available in carbon steel with durable industrial coating, with stainless steel material contact surfaces, or in all-stainless steel (shown) finished to industrial, food, dairy or pharmaceutical standards.
Flexicon also manufacture other configurations of IBC and bulk bag dischargers as well as tubular cable conveyors, flexible screw conveyors, pneumatic conveying systems, bulk bag conditioners, bulk bag fillers, bag dump stations, drum/box/container tippers, drum fillers, weigh batching and blending systems, and engineered plant-wide bulk handling systems with automated controls.
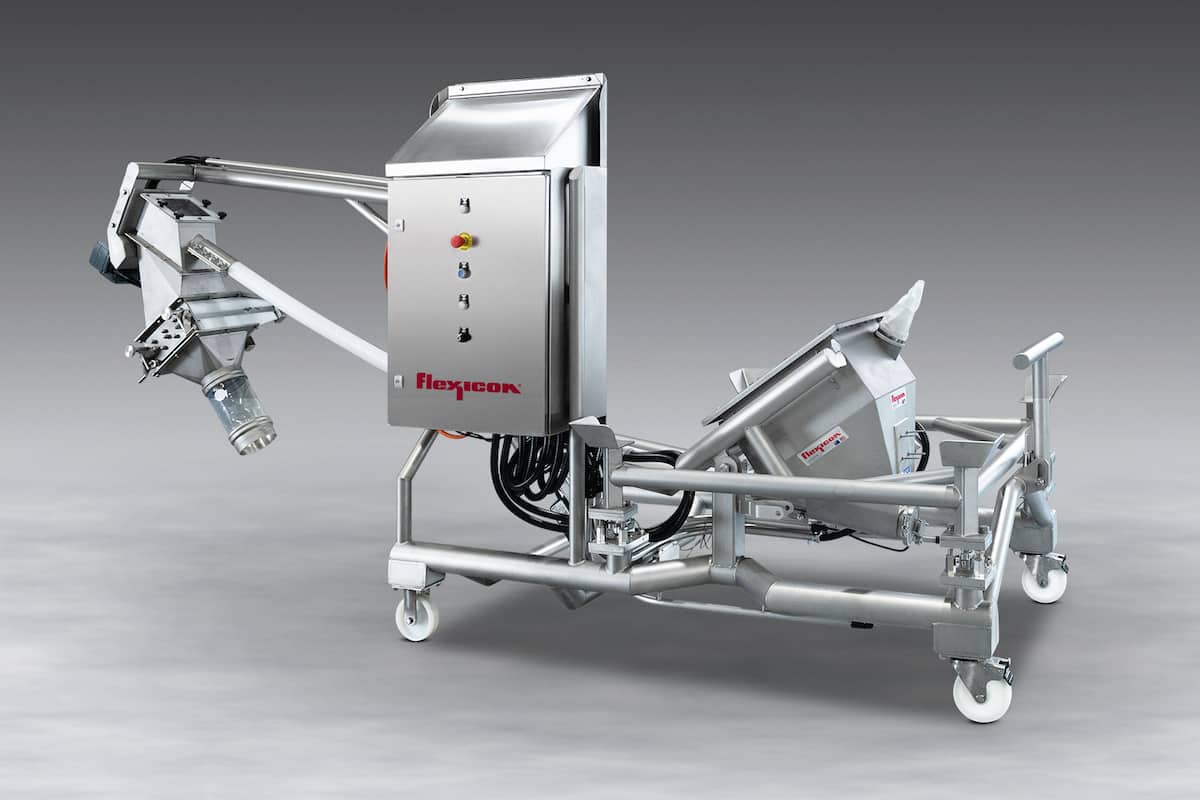
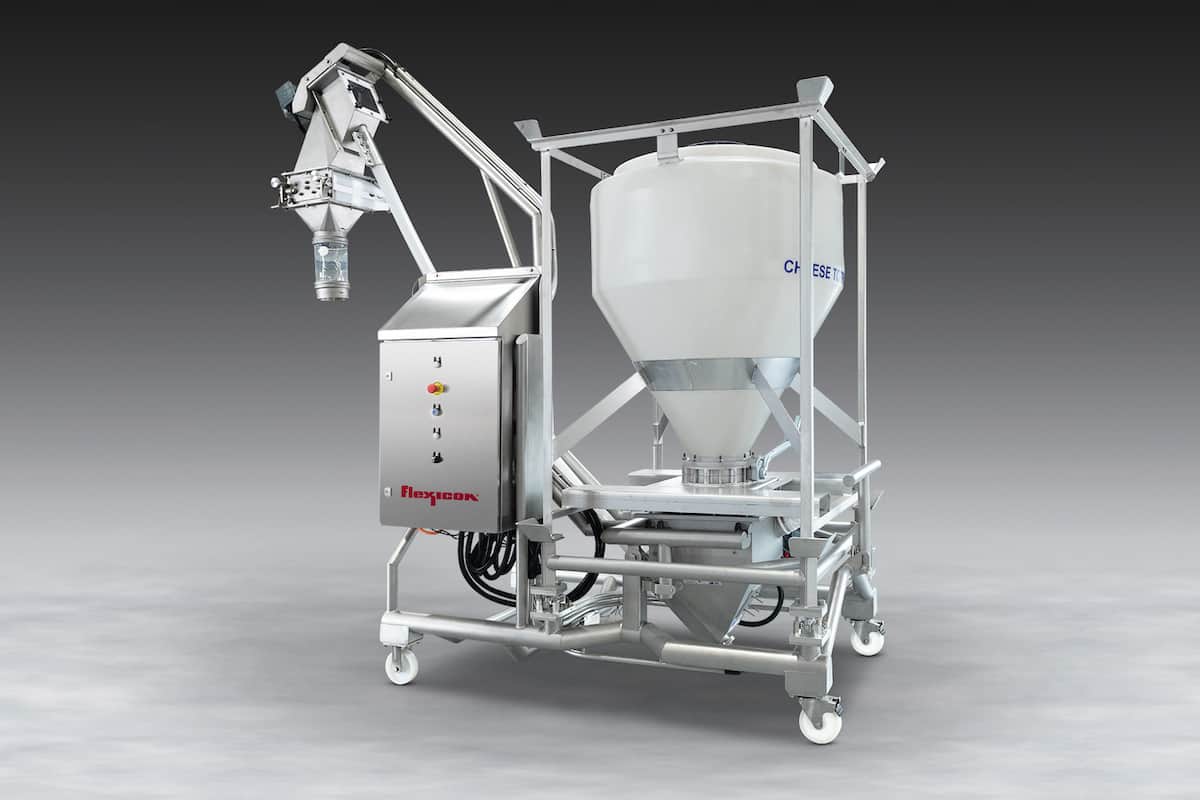