A customer had major issues with a belt conveyor that should transport the instant chocolate drink powder from production to a sieve placed right above the filling lines. The installed belt conveyor contaminated the powder with wear which was not acceptable. Because all upstream equipment was already installed, less than 1 m below a discharge rotary valve was available.
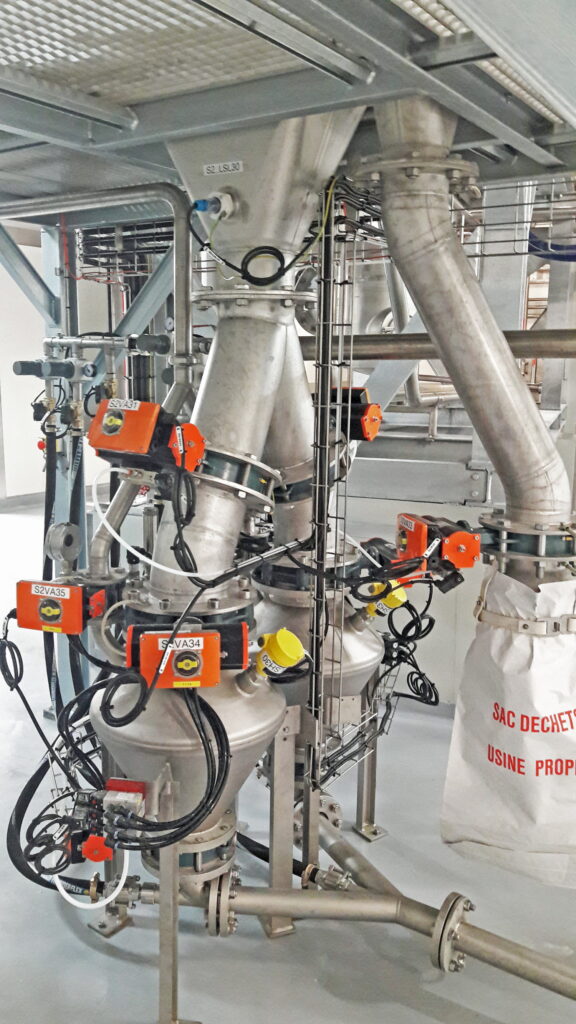
A lean phase pneumatic conveying system with negative or positive pressure would have been possible. However, because the powder must be treated very gently minimizing the creation of fines during the transport, a low-velocity dense phase conveying system Gericke PulseFlow PTA with two vessels was selected. The two 20 l pressure vessels were placed side by side and successfully fitted below the continuously discharging rotary valve. The chocolate powder is fed at a rate of 1.5 t/h into one pressure vessel while the other vessel is conveying and alternating. This mode generates continuous product transport.
In another project, the client had an IBC and a metal detector system for unloading milk powder. The task was to convey the milk powder at a rate of 3 t/h to receiving hoppers above the filling line and at the same time not to create fines. Therefore, again the gentle Gericke PulseFlow PTA dense phase conveying system operating at low velocities was chosen. Due to the height restriction of 1.5 m this time, two 50 l pressure vessels were selected.
Utilizing twin vessels reduces the height requirement compared to using single vessels in combination with intermediate buffer hoppers when there is a continuous process upstream. Twin vessels allow continuous operation. At the same time, the air consumption is reduced because smaller pipe diameters can be utilized compared to a single vessel system. For single vessel conveying also filling times have to be considered during which conveying is pausing and in order to achieve the same absolute capacity, the instantaneous capacity during conveying time has to be increased which requires larger pipe diameters and higher air consumptions.