The main ingredients are stored in eight large silos — one each for salt, sugar, dextrose and calcium sulfate (an anti-caking agent), and four for flour. Typically, a 70,000 lb (31,818 kg) silo empties twice a day, says maintenance supervisor Mike Dolan, adding “We move 6000 or 7000 lb (2727 or 3182 kg) through the plant in 20 minutes.”
Sifting the ingredients is a necessary part of producing a quality mixture. Dolan says more than a dozen centrifugal sifters have been doing that job for many years. However, the increased incidence of screen failure, causing downtime and potential product contamination, prompted the company to look for replacement screens that would operate more reliably over long periods of time.
Sourcing better screens
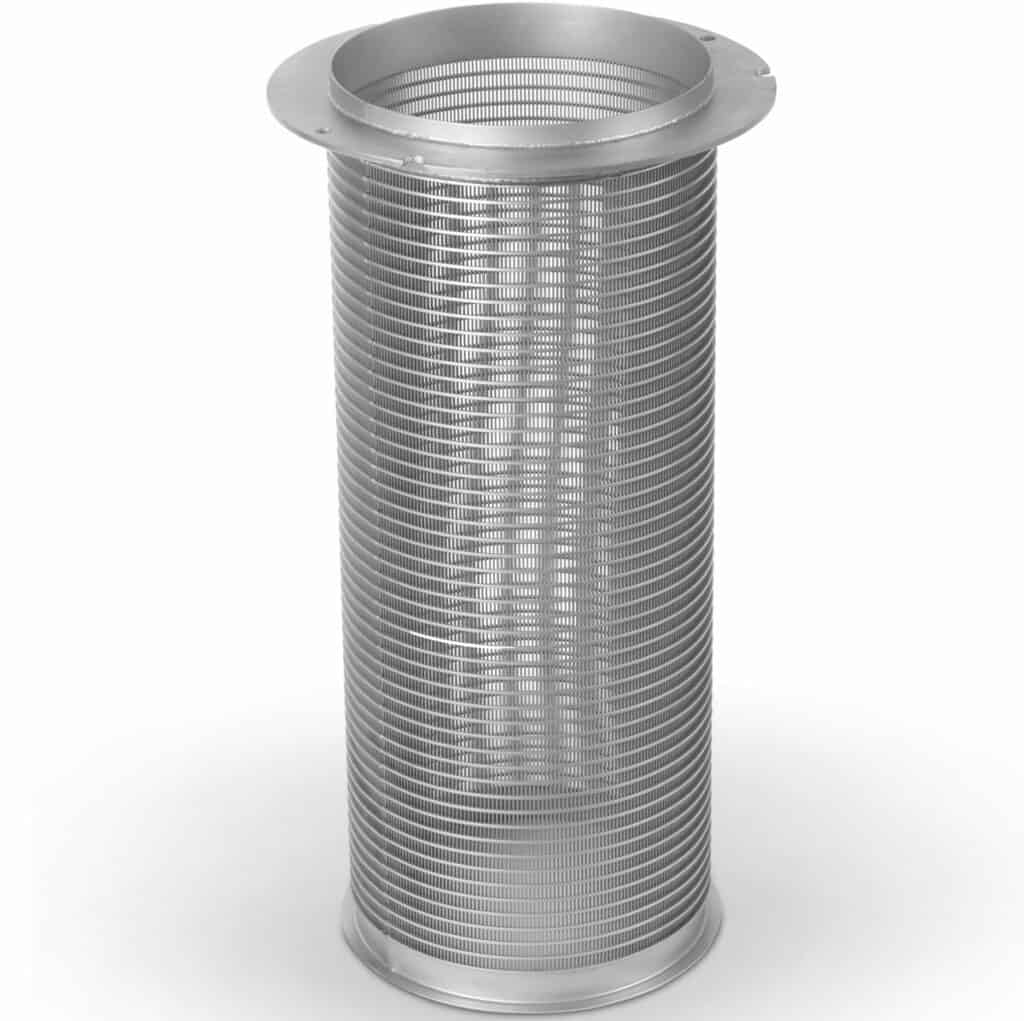
Finding compatible replacement cylindrical screens of sufficient strength became a challenge, Dolan says. The company contacted Kason Corporation, a manufacturer of centrifugal sifters that also offers customized screens, and requested a sample screen of heavy-duty design with screen mesh of rigid, stainless steel wedge wire.
The company installed and evaluated this one screen on the centrifugal sifter that serves the whole-wheat flour silo. It ran successfully for a three-month trial with “no errors, no issues,” says Dolan. After that, Corbion ordered the heavy duty replacement screens for 13 more centrifugal sifters of various sizes.
“Even though it was a competitor’s equipment, Kason built their own wedge wire screens to fit,” Dolan notes.
Specifying replacement screens
The screen-replacement project took place in two stages over six months. In specifying the screens, Dolan says, “Stainless steel, food-grade was absolutely the number one priority.” Maintaining the previous throughput was another important consideration.
The fact that the replacement screens are one-piece assemblies appealed to the maintenance team at Corbion. “Nothing is worse than receiving equipment and having to assemble it,” Dolan says. “We just install the screen, close the access door, and run.”
Dolan notes that a critical part of the replacement screen project was Kason’s willingness to work with the Corbion team to develop the replacement screens and adapt them as necessary. On the first try, some dimensions were just a little off, Dolan says, but the manufacturer took care of it right away. “The second try was perfect.”
In addition, Dolan observes, the replacement screens break up lumps better than the previous screens did.
Incorporating centrifugal sifters for manual additions
On five of the processing lines, small amounts of ingredients are added manually at “hand-add stations.” These additions may be any of 900 different ingredients packaged in 50-lb boxes, Dolan says.
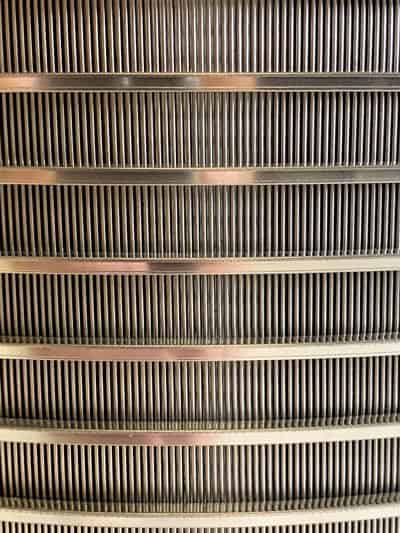
Corbion ordered two new Kason CENTRI-SIFTER centrifugal sifters with integral bag dump stations to facilitate manual additions. The units were customized to accommodate the 7-foot (2.1 m) high space on the processing line. The manufacturer “worked with us to build a non-standard configuration of the sifter/bag dump station to fit the limited vertical clearance,” Dolan says. This was the only way to add sifting capabilities without redesigning the production lines, he continues.
The throughput of the hand-add sifters is designed for 1000 lb/hour (454 kg/hour). Kason made a small adjustment to adapt the sifters to the application, increasing the pitch on the paddles inside the sifters to improve flow.
After operating the two centrifugal sifters/bag dump stations on the two lines for a few months, Dolan said, “We loved them and ordered a second set.”
Previously, the manual additions were not sifted; sifting took place at the end of the process instead. “So if we found something in the product, we had to throw out the whole batch – you’re talking a couple of thousand pounds,” Dolan said.
“The biggest thing is that good sifting is a selling point for us. If you tell the customer you sift 100 percent of your raw materials going in, down to a 6- or 8-mesh screen, it gives peace of mind,” he says.