This manufacturers dedication to innovation shines through in how they customize starch properties to meet specific client requirements, be it for thickening, texturizing, or stabilizing products. This tailored strategy not only showcases the company’s technical prowess but also its pivotal role in the food and beverage sector, continuously adapting to changing market demands.
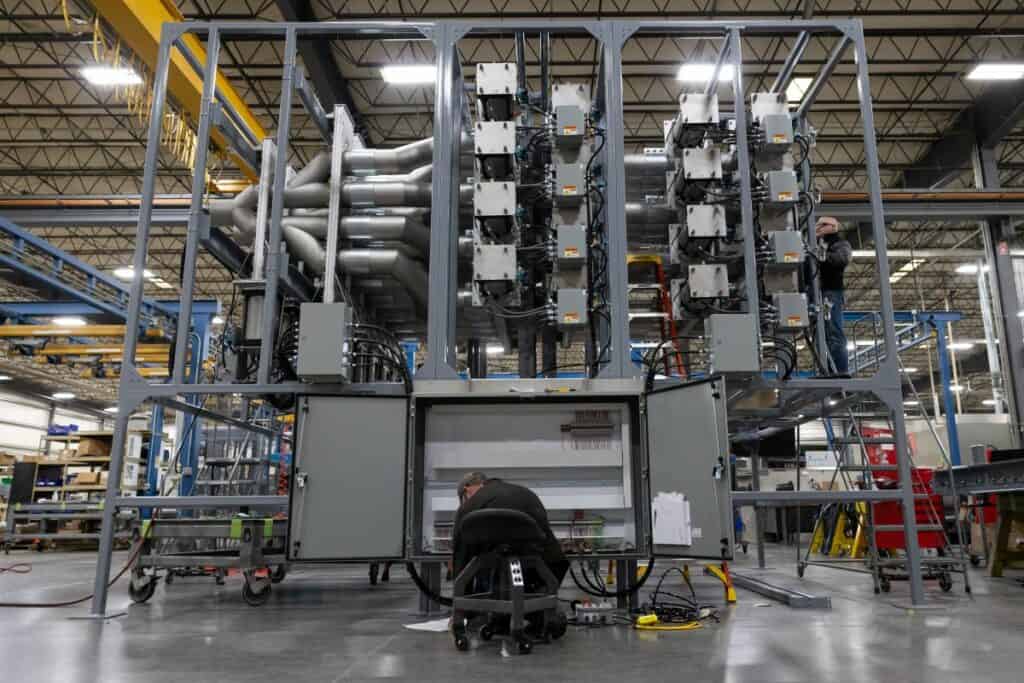

The manual hose change process in material handling, particularly in extensive operations like those at this customer facility, poses several challenges affecting efficiency and safety. A primary concern is the time-intensive nature of manual changes, significantly slowing down production rates. Each change involves halting machinery, manually disconnecting and reconnecting hoses, and restarting operations—an error-prone process with potential delays. Moreover, the physical toll on workers conducting these manual exchanges is substantial, raising concerns about workplace ergonomics and employee well-being. There’s also an increased risk of cross-contamination during material handling, as remnants from prior uses may mix if hoses aren’t thoroughly cleaned between changes. This risk presents a serious hurdle in maintaining the high-quality standards vital in food and beverage manufacturing. Consequently, the need for automated, advanced systems to streamline material handling, reduce downtime, and uphold strict hygiene standards is evident.
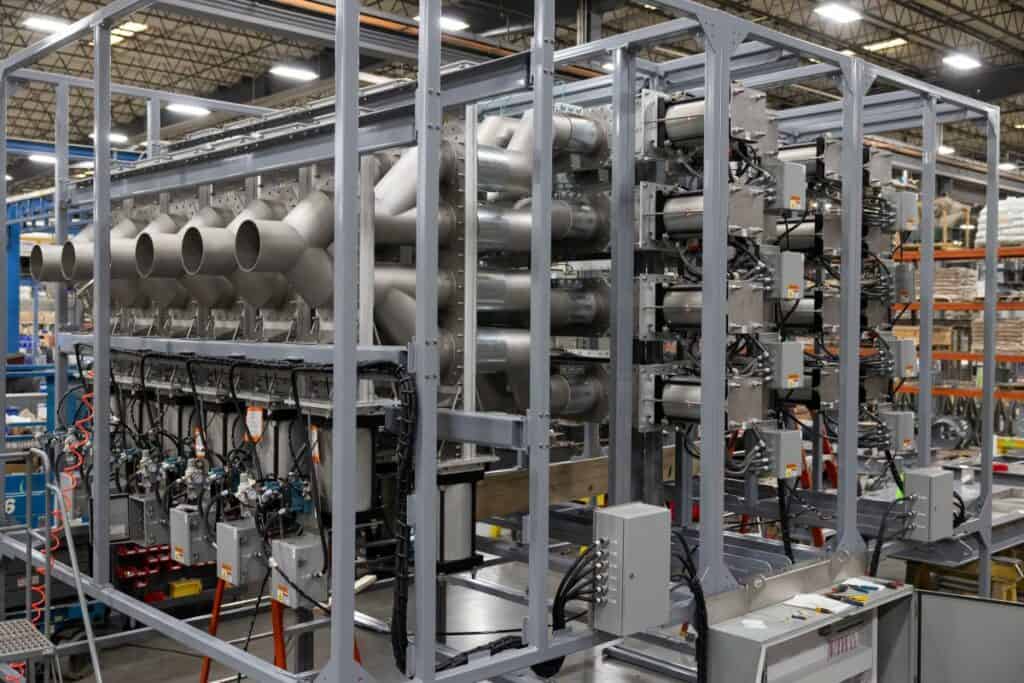
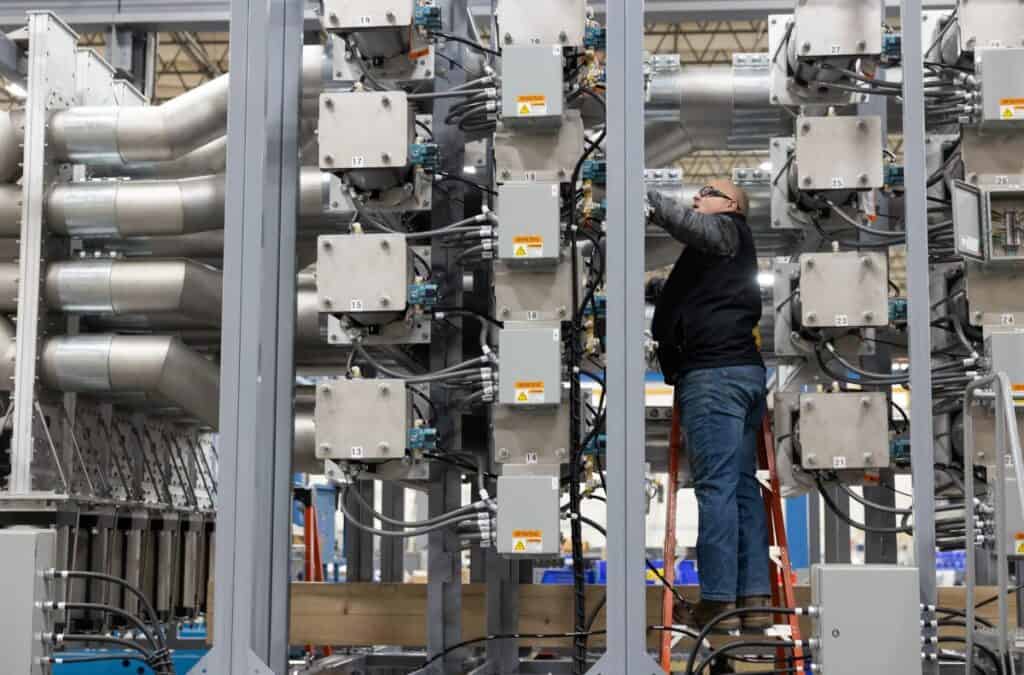
Given the challenges outlined, the Vortex Multi-port Diverter emerged as the ideal solution, directly addressing issues linked to the manual hose change process. Its design facilitates smooth transitions between materials or production lines sans the need to halt machinery or engage in labor-intensive hose changes. This not only drastically minimizes downtime but also streamlines operations, boosting productivity and efficiency. The Vortex Multi-port Diverter enhances workplace safety and employee welfare by automating material switching, lessening physical strain, and reducing injury risks tied to manual tasks. Its automated system not only guarantees a safer work environment but also enhances employee contentment and operational efficiency. Discover more about the Vortex Multi-port Diverter or reach out to us today!
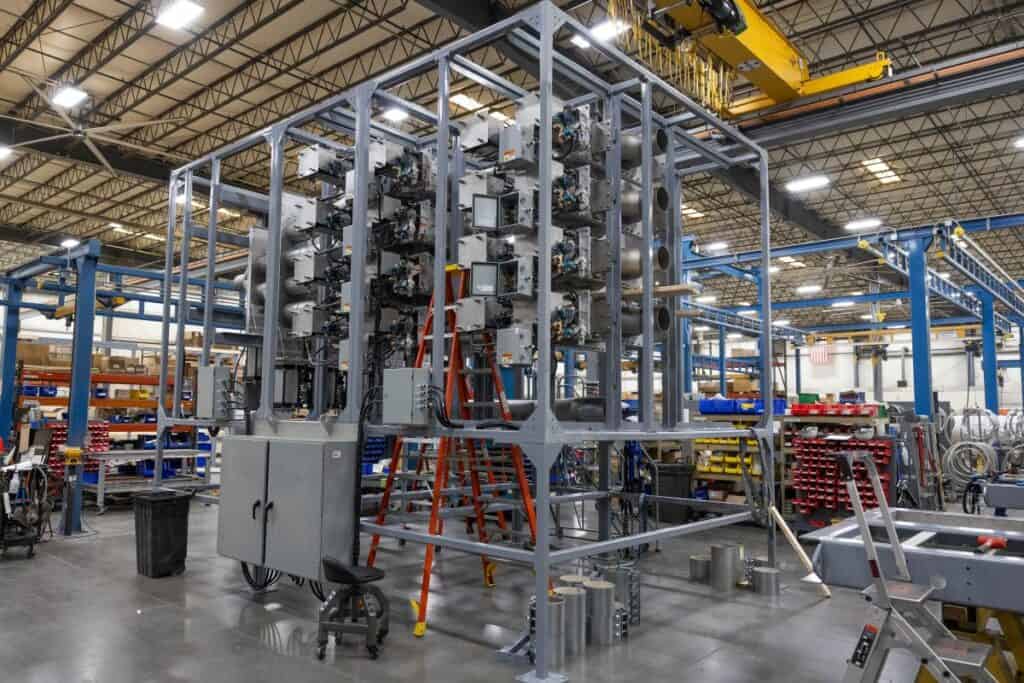
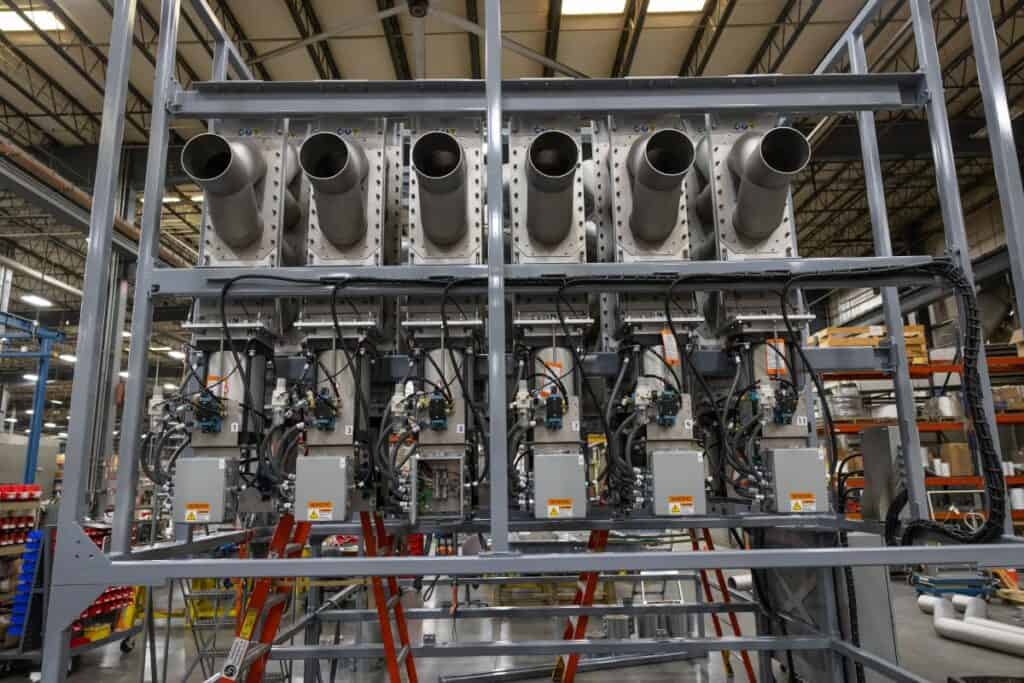