Food processing is the conversion of raw bulk ingredients (agricultural products) into food for human consumption or transforming one form of food into another.
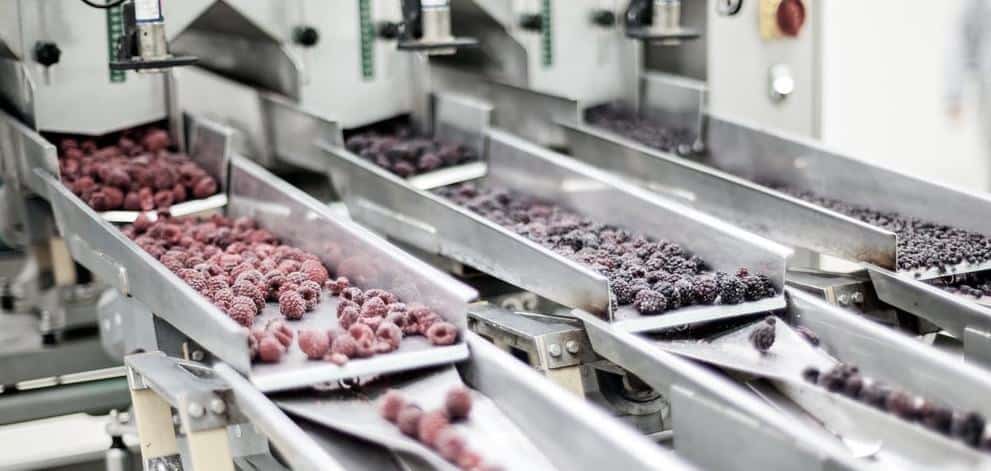
Food processing is the conversion of raw bulk ingredients (agricultural products) into food for human consumption or transforming one form of food into another.
What comes to mind when you think of processed foods? You’re right if you think of items such as snack chips, cookies, and soft drinks.
But you might be surprised to learn that most foods we eat are processed.
Processing food definition = Food processing is any deliberate change in a food that occurs before it’s available for human consumption.
It can be as simple as drying or freezing food to preserve nutrients and freshness or as complex as formulating a frozen meal with the right ingredients and nutrients.
A few examples of processed foods include:
Primary food processing
Primary processing is the conversion of raw materials to food commodities. Milling is an example of primary processing.
Secondary food processing
Secondary processing is the conversion of ingredients into edible products – this involves combining foods in a particular way to change properties. Baking bread is an example of secondary processing.
Tertiary food processing
Tertiary food processing produces prepared convenience foods like canned soups or frozen dinners.
The food processing industry is a large segment of the overall food industry and has grown fast.
The availability of a significant raw material base supports the growth of food processing industries.
These raw bulk materials like grain, sugar, flour, wheat, corn, dairy products, spices, and starch are stored in bulk quantities and then divided into smaller batches to be incorporated into the production process.
Food processing made for human consumption has a plenitude of regulations, as well as strict requirements with regard to reconciliation and accountability.
Food processing market
The food processing market is an important global market that has grown fast in recent years because of rising demand for food in emerging markets, changes in consumer habits, and a big leap forward in technological capabilities.
Food processing market size
The growing demand for processed and ready-to-eat food products, industrial automation, and strict government regulations regarding standardization and hygiene drives the global food processing market.
Issues associated with food processing
Essential issues associated with the food processing industry are food safety, cross-contamination, hygiene, and dust explosivity.
Food processing safety is crucial as it helps protect consumers from the risk of foodborne illnesses and it helps to prevent consumers from risks of health-related conditions.
The food processing industry uses a wide range of process instruments and processing equipment.
From the impact of advanced process automation and artificial intelligence to the growing demand for organics, the food processing industry is undergoing a period of fundamental change.
Food processing companies manufacture, package, or store food for human consumption.
A food-producing company sells its products to households, restaurants, or institutional food services through a grocer or wholesaler. Food processing companies are responsible for ensuring their products are safe for consumption.
Companies active in industrial food processing mainly process dairy products, preserved fruits and vegetables, grain mill products, pet foods, bakery products, confectionery products, fats and oils, and more.
The food manufacturing process can be organized in unit operations, such as:
These operations are controlled to maintain consistent product quality, safeguard staff health, and food safety standards, and avoid problems that may stop the production line from running, which would result in ‘downtime.’
The industrial food processing industry uses a wide range of machinery, equipment, and instrumentation.
Food must be processed and packaged hygienically, attractively, and efficiently in the food industry. Every project is based on the client’s technological, technical, and financial wishes.
Generally, equipment used in food processing applications serves one of the following purposes: measurement, transportation, storage, processing, or thermal treatment.
Measurement devices include scales and weighing systems, level monitoring systems, moisture measurement systems, flow meters, thermometers, particle analyzers other precision process control components.
These instruments are used to analyze machines and ingredients and allow manufacturers to perform and duplicate processing procedures without any complications.
They also monitor existing systems and machinery, whether to log data during product testing or quantify typical performance statistics.
Measurement devices are critical during food manufacture, as minor changes can lead to drastic changes in the finished product.
Used food processing equipment
Used food processing equipment can be a valuable cost and time-saving alternative.
Used equipment is offered at a fraction of the cost of new equipment and is usually shipped immediately.
Multiple pieces of equipment, even an entire process line, can be obtained from a single source.
This can reduce start-up and troubleshooting efforts, as well as shipping costs.
While many pitfalls exist for the used process equipment buyer, the advantages can be worthwhile.
Factors to consider before purchasing used food processing equipment are:
What was the equipment used for?
Prior uses of equipment can introduce risk because the residue may be left in the equipment. In general, avoid equipment that was previously used for non-food purposes, especially if it will be a direct food contact surface.
What is the equipment made of?
Processing equipment that may contact food should be corrosion-resistant, non-toxic, odorless, nonabsorbent, and easy-to-clean materials and comply with the national mandatory standards.
Can you take the equipment apart relatively easily?
All food processing equipment should be fully broken down for cleaning purposes.
Without taking the equipment apart, all equipment in use should be accessible for cleaning, sanitation, maintenance, and routine inspection without deconstructing it.
In an economy with rising production costs, new regulations, and changing safety standards, food processors have an even more challenging time remaining profitable.
By focusing on controlling and monitoring costs related to food processing and storage, food manufacturing and processing companies can make measurable improvements in their business.
Food processing software provides the functionality and value needed to improve operational efficiency.
Food processing software offers the following benefits:
The response drives the food manufacturing industry to both customer and consumer trends and needs.
The food processing industry is a large segment of the overall food industry, from farming and food production, packaging and distribution to retail and catering.
Finding a source covering all aspects of processing bulk dry foods and food manufacturing is challenging.
Product supervisors and plant and project engineers must keep up-to-date with the latest food processing news.
Access to news on breakthrough technologies in food processing, food processing innovations, and general food industry news and events is crucial for any food industry professional.
Get the extensive coverage for dry material handling professionals who buy, maintain, manage or operate equipment, delivered to your inbox (it’s free!).
By signing up for our list, you agree to our Terms & Conditions.
Get the extensive coverage for dry material handling professionals who buy, maintain, manage or operate equipment, delivered to your inbox (it’s free!).
By signing up for our list, you agree to our Terms & Conditions. We deliver two E-Newsletters every week, the Weekly E-Update (delivered every Tuesday) with general updates from the industry, and one Market Focus / E-Product Newsletter (delivered every Thursday) that is focused on a particular market or technology.
Since 2010, we have been providing industrial professionals with the latest innovations, case studies, and the most comprehensive equipment guide in solids handling, in a variety of markets.
A
website
© BulkInside 2025
By signing up for our list, you agree to our Terms & Conditions. We deliver two E-Newsletters every week, the Weekly E-Update (delivered every Tuesday) with general updates from the industry, and one Market Focus / E-Product Newsletter (delivered every Thursday) that is focused on a particular market or technology..