Initial Situation & Problem
Nahrin’s dosing system consists of two conical collecting and dosing units. First, the spice mixtures are conveyed into the first hopper (Application A) using a dosing feeder. The product then moves to the filling station, where a dosing hopper (Application B) dispenses precise quantities into tins.
However, both applications faced frequent discharge issues due to product compaction above the outlets. This led to bridging, which could only be resolved using mechanical vibrators and manual hammer blows (Fig. 1).
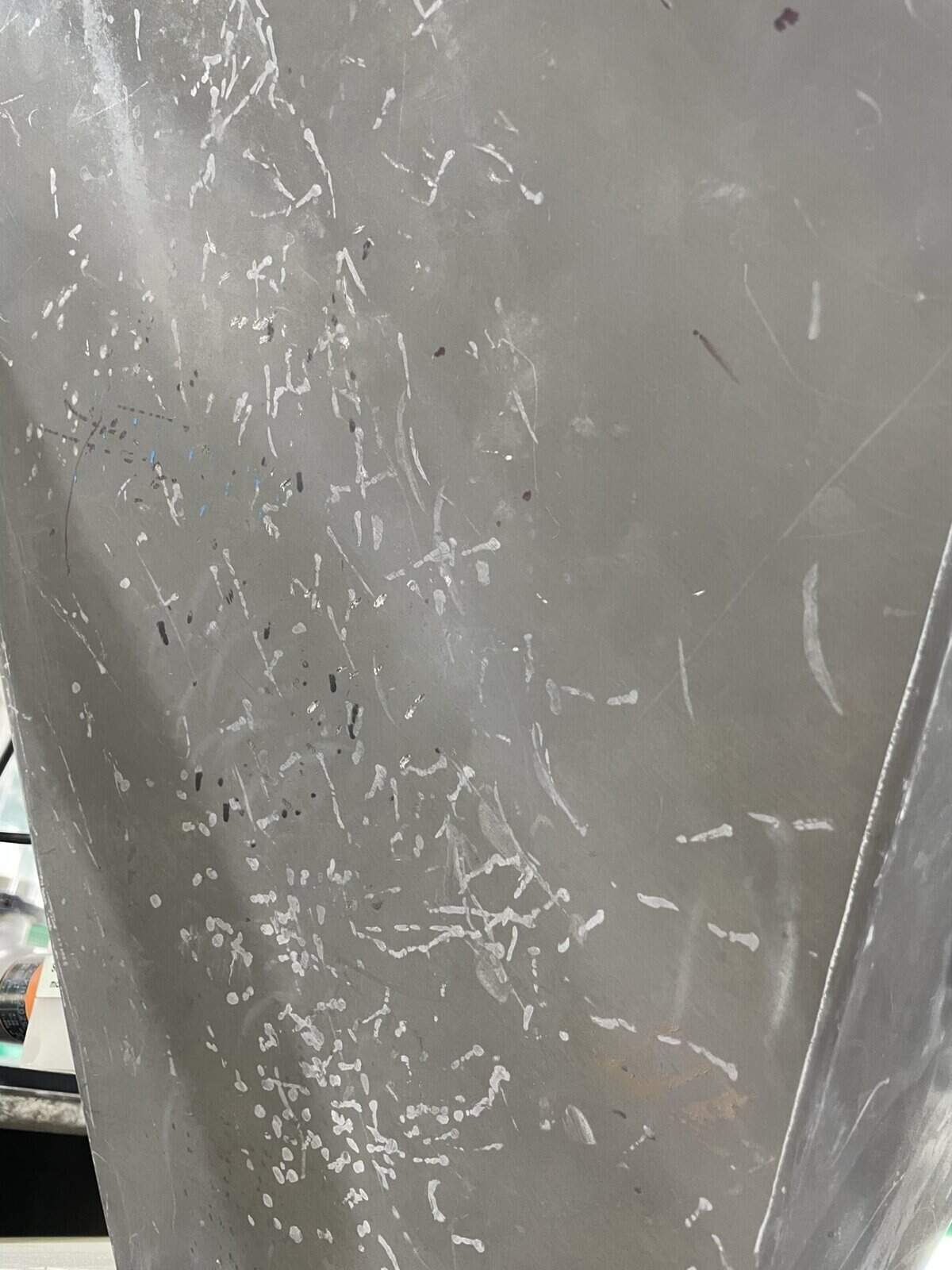
Figure 1: Effects of the hammer blows
on the funnel (application A)
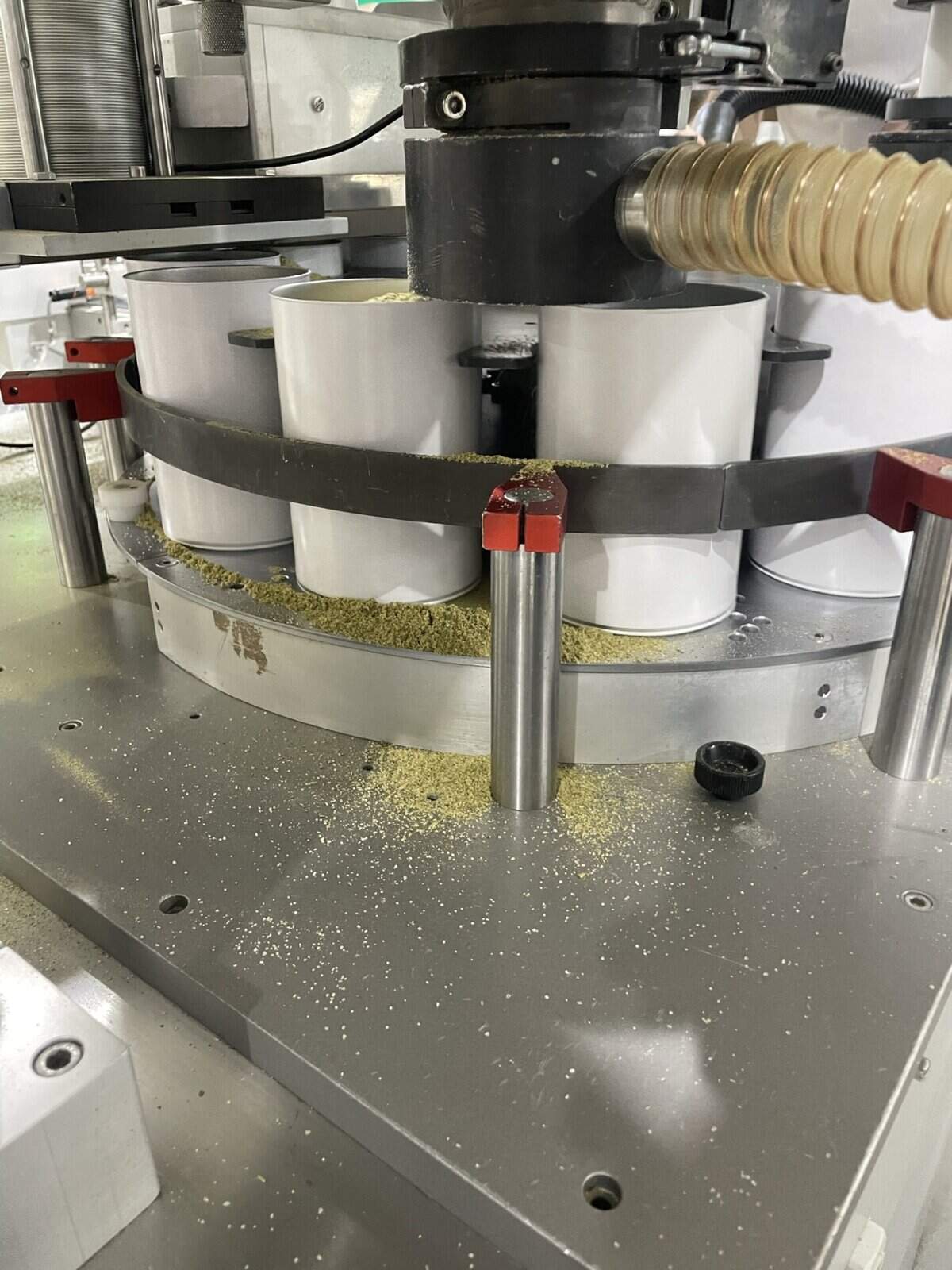
Figure 2: Improper dosing leads to
product loss (application B)
This caused problems throughout the entire dosing process. On the one hand, the employees were constantly exposed to increased noise pollution (over 90dB) caused by the knockers. On the other hand, the irregular, abrupt dosing caused by the mechanical flow aids meant that Nahrin’s strict quality specifications regarding filling quantities could not be met in some cases. As a result, some of the affected cans had to be refilled. In addition, valuable product was lost during the process (Fig. 2).
Approach
Thanks to close cooperation between the customer and Artech, mechanical waveguides made of aluminum were developed specifically for this project. These were welded to the outer walls of the two hoppers, and the ultrasonic converters were then screwed on (Fig. 3).The ultrasonic generator (Fig. 4) was used to analyze the frequencies of the applications and parameterize jobs.
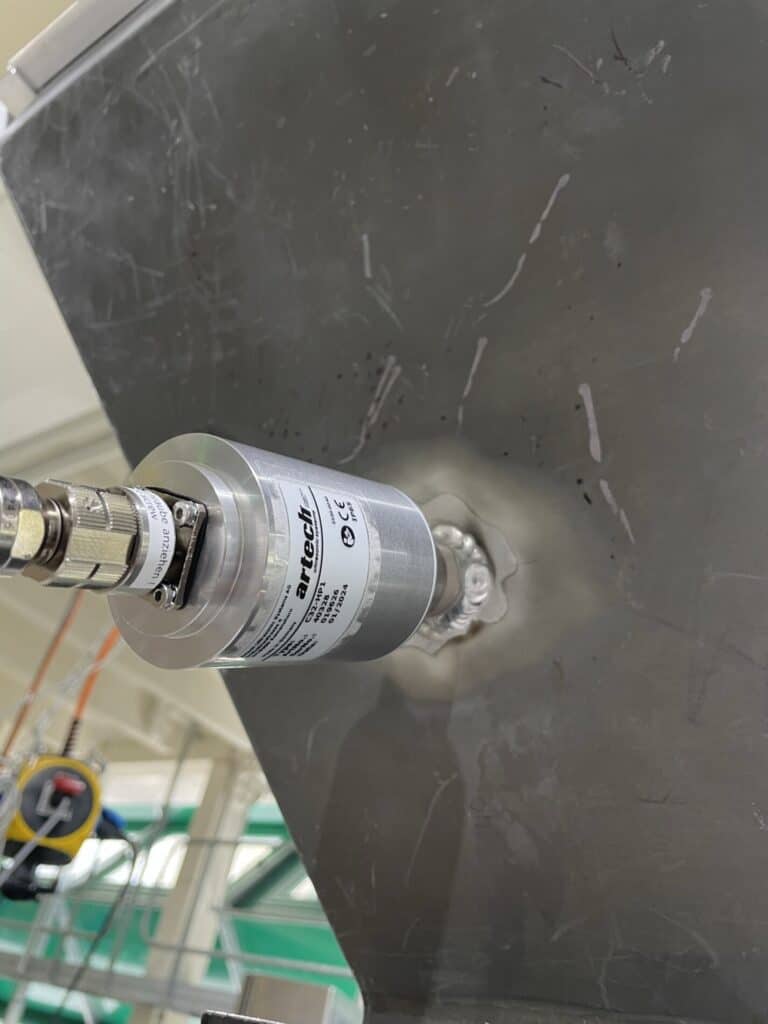
Figure 3: Ultrasonic converter
on the aluminum hopper
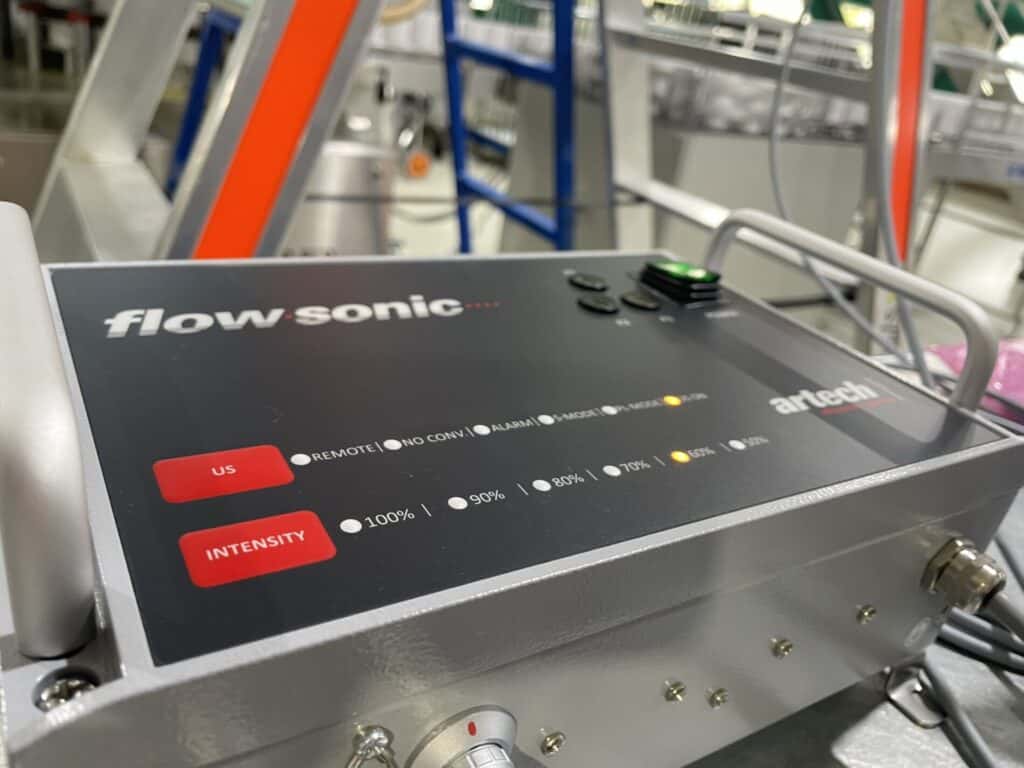
Figure 4: Ultrasonic generator
Result / Advantages
By using the Artech ultrasonic discharge and dosing aid flowsonic®, mechanical vibrators and manual hammer blows can now be completely avoided. Noise pollution has been significantly reduced from the original level of over 90dB. In addition to the noise reduction, the optimized dosing within the quantity tolerances enables employees carry out less heavy work, such as transporting and emptying cans back into the hopper. In addition to more precise dosing and correspondingly less waste (Fig. 5), the average dosing time per can has been improved by approx. 30% thanks to the smooth powder flow (Fig. 6) (example seasoning mix 730 grams = standard dosing time per unit: without ultrasound 2.2 seconds, with ultrasound 1.5 seconds).
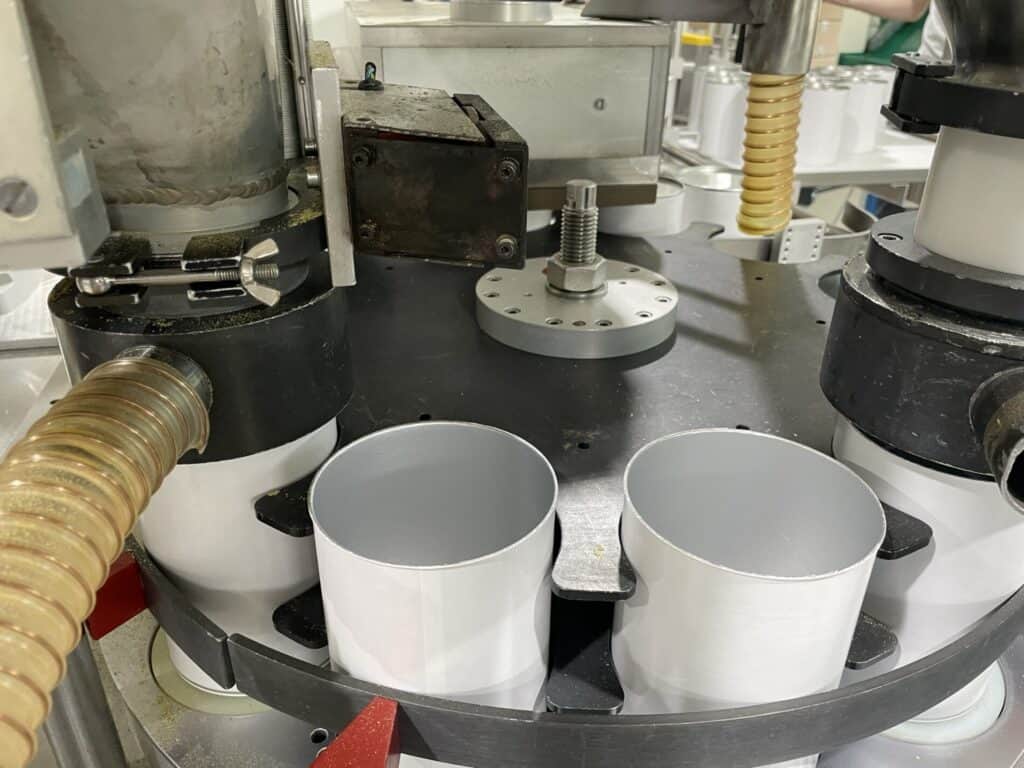
Figure 5: Minimal product loss
compared to mechanical flow aids
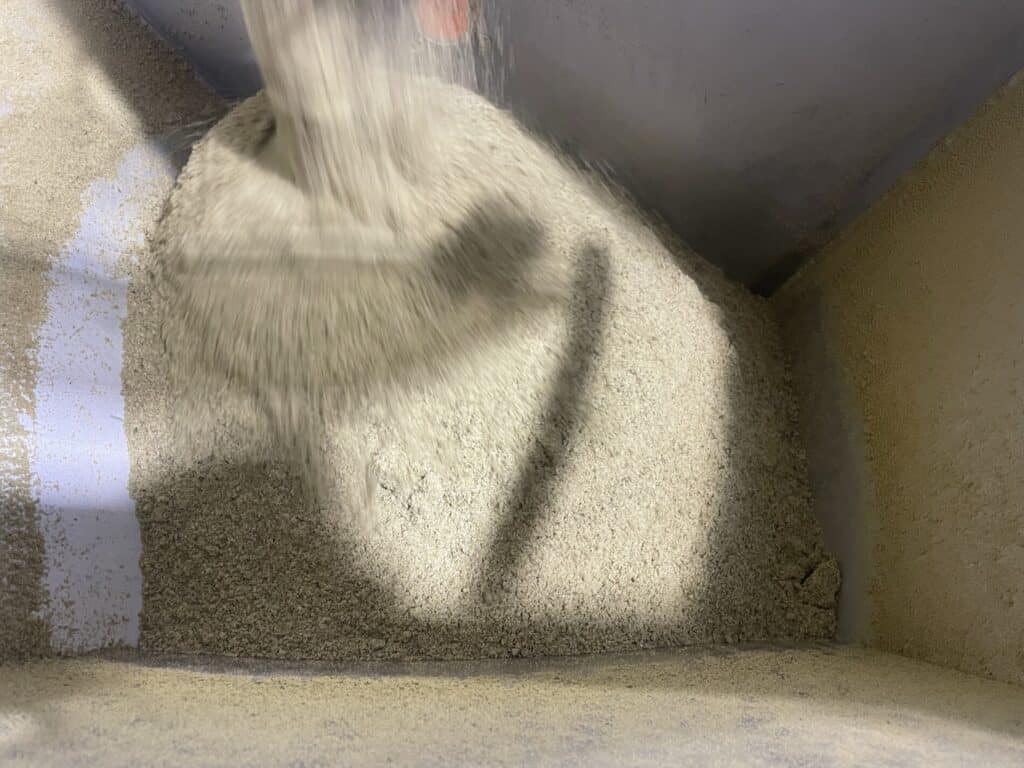
Figure 6: Smooth powder flow thanks to
ultrasound
Products used
- 1x FS-1-200-T generator
- 2x Converter C32-HP1
- 2x HF-cable 10m
- 2x Titanium bolts
- 1x Wall bracket for generator
- 2x Customized waveguides