Hazard monitoring describes the equipment and process of monitoring material handling equipment and facilities for proper operation and the conditions that can lead to the creation of a heat source that can initiate an explosion. There are a myriad of choices of hazard monitoring equipment designed specifically for material handling and processing equipment such as bucket elevators, belt conveyors, drag conveyors, rotary airlocks, roller mills, hammer mills, grinders, etc.
However, before deciding on the specific type of sensor and control, you must first decide on what parameters you are going to monitor and which safety standard applies to your facility. For some industries and equipment, laws and regulations are mandatory. Internationally, there are standards bodies that provide guidance for hazard monitoring such as CSA (USA, Canada), ATEX (Europe), IEC (global), INMETRO (Brazil), EAC (Russia), etc.
These standards are only the starting point for the minimum requirements. The plant manager should determine which areas are dust hazard environments and then consider each piece of machinery and determine which parameters need monitoring.
Monitoring Points on Select Machinery
The following illustrates the most common monitoring points on select grain handling machinery. The end user should always evaluate each individual piece of machinery for potential sources of ignition and monitoring needs as machinery performance can vary significantly and each machine may have its own unique behavior.
- Bearing Temperature Sensor: Worn or failing bearings can generate excessive heat and, in the event of a catastrophic failure, the bearing can break apart and cause metal-on-metal sparking.
- Surface Temperature Sensor: Surface temperature sensors can monitor small flange bearings and auxiliary equipment such as motors, gearboxes and tail pulley alignment on enclosed belt conveyors. They can also measure ambient temperature as a reference for other temperature monitoring.
- Belt Misalignment Sensor: A belt misalignment sensor will indicate when the conveyor belt is about to rub on the conveyor enclosure. A misaligned belt can cause excessive heat.
- Speed Switch Sensor: A shaft-mounted speed switch or speed sensor monitors conveyor speed for slowdown. Slowdown can indicate low belt tension or slippage on the head or drive pulley, which can result in friction, a source of heat. Tail slowdown can also be indicative of excessive load or binding equipment.
- Rotary Shaft Encoder: Another form of speed sensor with options for higher resolution and the option to detect rotational direction of the monitored shaft. When calibrated properly, it can also monitor gate and valve position.
- Plug / Choke Sensor: Plug / choke sensors monitor the condition where grain is no longer free-flowing and has built up to potentially unsafe levels which may cause overloading of equipment, back-legging, filling the boot pit, grain spillage, belt slip, belt misalignment or damage to the equipment.
- Slack/Broken Chain Detection: Commonly referred to simply as a slack chain sensor, this sensor monitors a chain- driven conveyor for a slack or broken chain.
- Door Position Inductive Proximity Sensor: This proximity sensor monitors when an overabundance of grain, possibly due to a plug condition, forces open an inspection door, driving a sensing tab on the door out of range of the proximity sensor. It can also detect the position of a slide gate or other equipment.
- Rotary Level Indicator: The rotary level indicator will detect the presence of grain when the grain rises to a level that inhibits the normal rotation of a motor driven paddle.
- RF Capacitance Level Indicator: The RF capacitance level indicator will detect the presence of grain when the grain rises to a level that effects the normal capacitance sensed by the internal electronics.
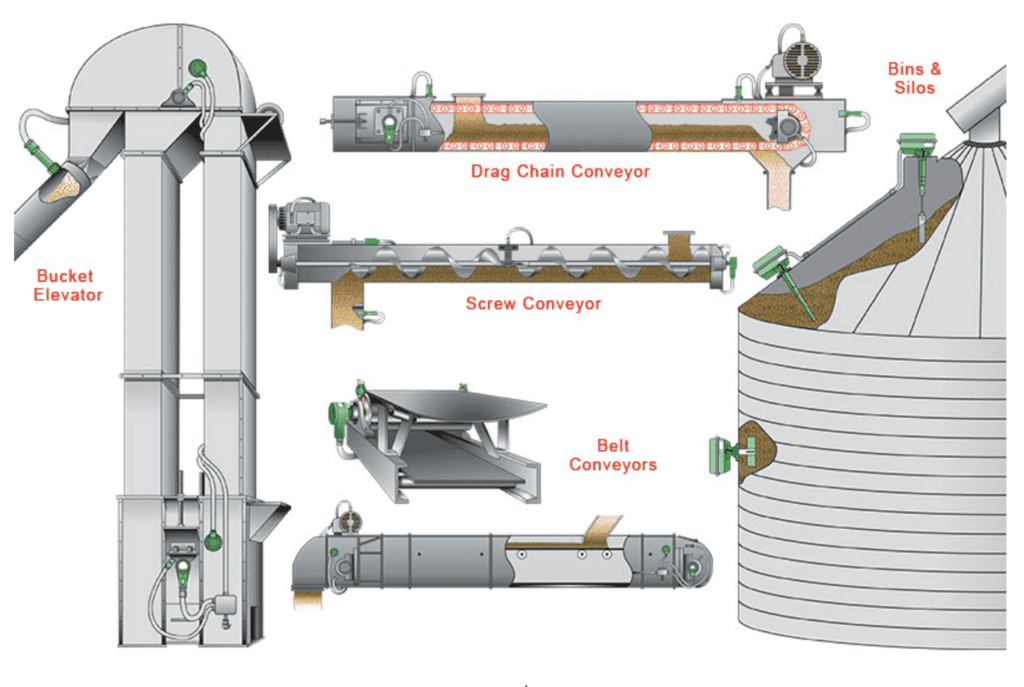