From brewing to baby food, and solids to slurries, level sensor solutions are available for inventory monitoring and flow detection to optimize uptime and supply chain management. BinMaster NCR-86 radars provide non-contact measurement of both liquid and solids. Mini capacitance probes are ideal for tight spaces and smaller vessels. Flow detect alerts operators of blockages or absence for dry solid flow.
The key to bulk material measurement in the food production industry is getting the right sensor for the application. Selecting the sensor entails considering the size of vessel, the hygienic requirements, and bulk density of the material measured. Even in the same plant, silos, tanks, and bins may require differing technologies.
Challenges for food level measurement:
- Powders, solids, liquids, and slurries all behave differently
- Material caking or buildup prevents flow from a vessel
- Vessels may not empty or discharge completely
- Process downtime causes shortages of key ingredients
- Flow interruptions occur in sticky or powdered materials
- Excessive rework and waste caused by improper batching
- Limited system capacity creates processing delays
- Loss of inventory control can lead to spoilage
Bulk density of food ingredients in silos directly influences storage capacity, transportation efficiency, and production consistency. Understanding compaction and material behavior under storage conditions ensures the optimal utilization of resources and maintenance of quality standards. The bulk density of material varies tremendously. Ingredients vary widely in material mass within a given volume. Knowing your bulk density can help you improve processing and control inventory carrying costs.
Material | lb./ftᶾ |
Rice, puffed | 6 |
Oat hulls | 8 |
Almonds | 29 |
Dry Buttermilk | 31 |
Raisins, moist | 38 |
Gelatin | 45 |
Ascorbic Acid, fine | 1,998 |
How do sensors and software make my supply chain efficient?
Cloud-based solutions provide better inventory data with more automation and less labor. Inventory is available anywhere, anytime, to plant workers, managers, purchasing, and finance departments with one login for every material, vessel, and plant.
Real-time Monitoring: Level sensors provide continuous, real-time data on stock levels, enabling timely replenishment and reducing the risk of stockouts or overstocking.
Accurate Data: Cloud inventory software integrates with current level sensor data, for real-time reporting, streamlined order processing, and enhanced supply chain efficiency.
Cost Reduction: By optimizing inventory levels through precise monitoring, processors can reduce holding costs, minimize waste, and improve cash flow management.
Demand Forecasting: Advanced analytics from inventory software, supported by sensor data, enable more accurate demand forecasting, leading to better production planning and resource allocation.
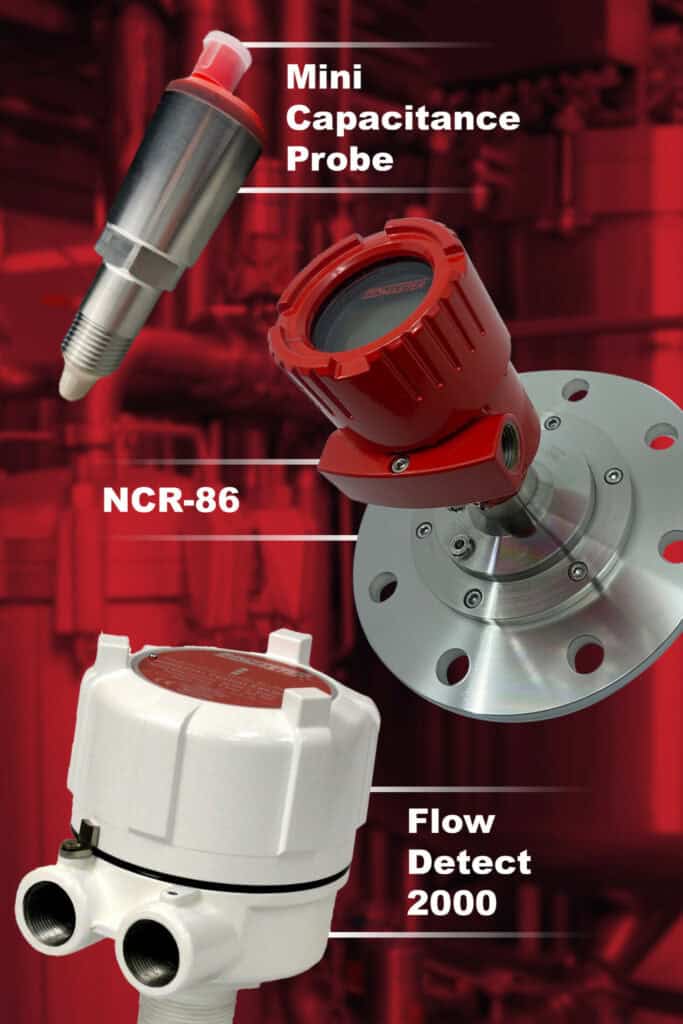
Three Ways Cloud Inventory Saves
Hedging Volatile Markets: Efficient inventory management helps food processors hedge prices by allowing bulk purchasing during low prices, reducing costs, and mitigating price volatility.
Preventing Product Shortages: Shutting down production lines is costly. Demand forecasting helps prevent ingredient shortages by projecting days until empty so you can maintain optimal stock levels.
Faster Financial Reporting: Raw ingredient inventory reports aid the finance department by providing accurate data for cost analysis, budget forecasting, and financial statements.
What types of vessels are suited for cloud inventory?
BinMaster’s food processing solutions help you manage inventory from raw material storage in bins outside the plant to small processing vessels inside the plant. Measure any powder, solid, liquid, or slurry, whether of any bulk density, specific gravity, or dielectric constant with confidence.
Storage Silos: Sensors measure the level of solids or liquids in a silo, bin, or tank. The amount of material on hand is calculated using the size of the storage vessel, the distance to the material, and the bulk density.
Batching Tanks: Liquid and dry ingredients are added, blended, or heated in make-up or batch tanks. Precision batching is critical to product quality, consistency, and customer satisfaction.
Mixers: The mixing process combines two or more ingredients to produce a consistent mixture that can be replicated time after time. Mixing involves liquid and powder, liquid and solid, or watery liquid and oils.
Conveyors: Sensors can detect the presence, absence, or level of material on a conveyor. They are used in food production’s sorting, cooking, seasoning, cooling, and packaging steps.
Pipelines: Sanitary piping is an essential transporting component for liquids and solids in the food industry. Flow sensors detect the flow or absence of raw to finished product in a pipeline.
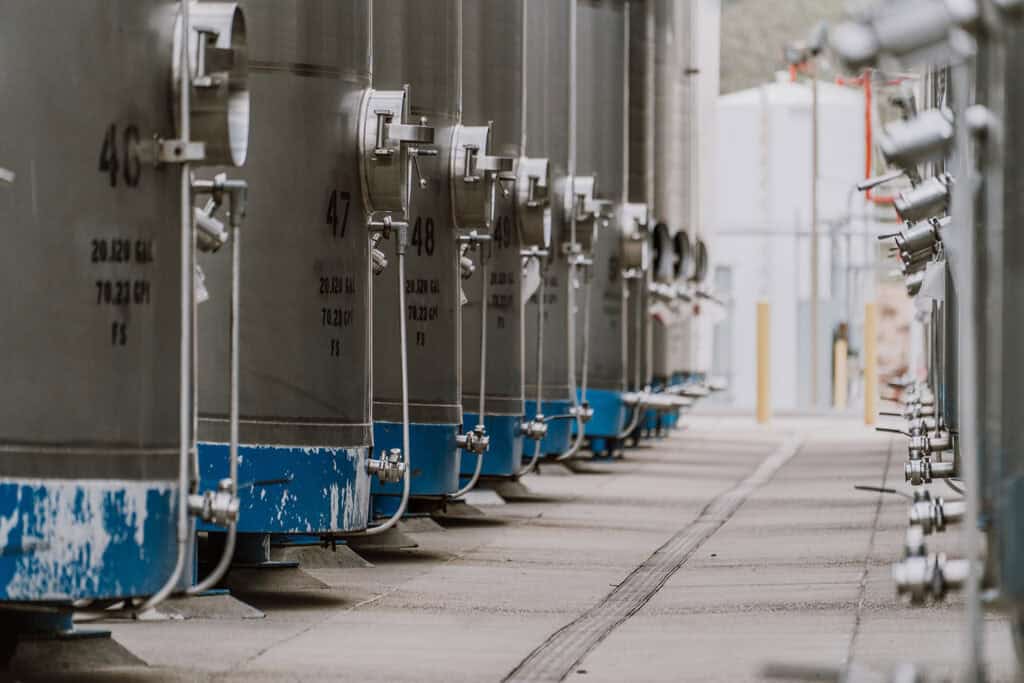