Common point-level indicators include rotary level switches, capacitance probes, vibrating rods, probes and forks, diaphragm switches, and tilt switches.
Point-level indicators alert when stored material stops, contacts, or falls away from the instrument. The switch is wired to an alarm, light, or control panel to alert of a high or low level or start or stop a process.
High-level alerts prevent overflows and ensure you maximize capacity. While low-level alerts prevent material outages that cause a dry run or production delay.
A point-level indicator has a because it eliminates cleanup or material contamination from an overfill. Plus, there’s no wasted material from improper batching.
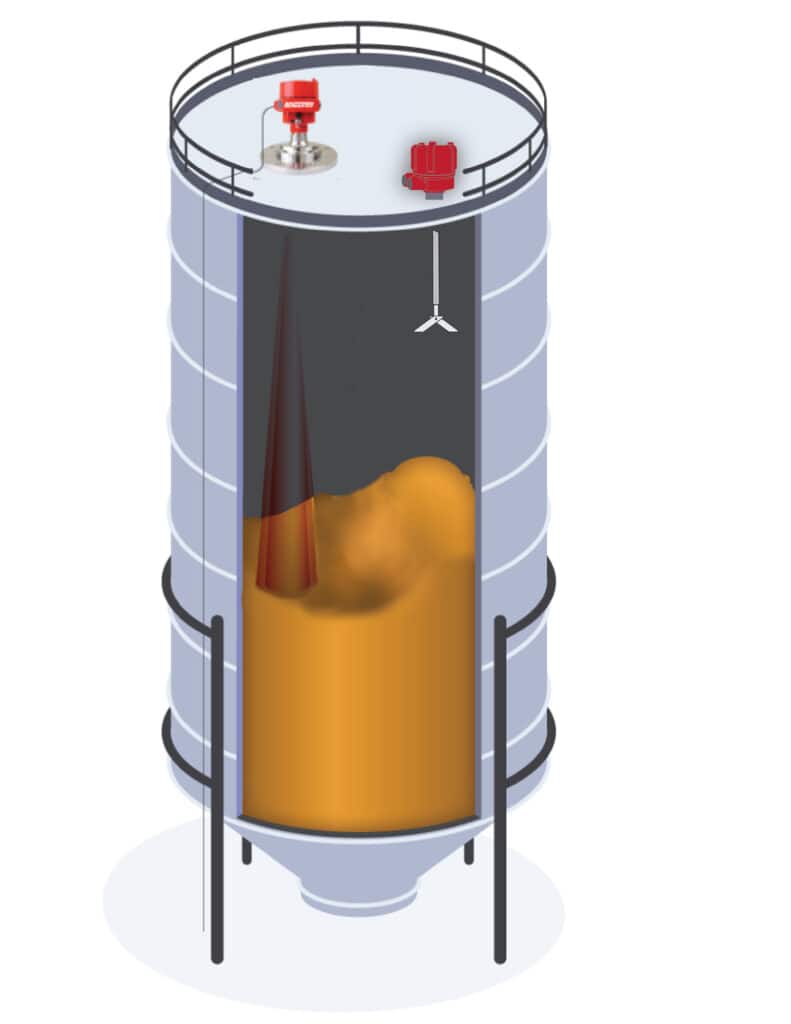
A point-level indicator also detects plugged chutes by alerting when chutes clog with material. You can also wire a point-level switch for process control By using the switching relay to turn a process off or on … like a conveyor leg.
Point-level sensors will alert to a conveyor overload And prevent jamming or damaging conveyors. They also provide redundancy in an Inventory management system. Use point-level and continuous-level sensors in tandem as a pre-alarm to prevent overfills that may damage equipment at the top of the vessel.
Point-level sensors are affordable. Compact and easy to wire, install point-level sensors a few vessels at a time, without a huge investment in time or money. And they often fall in an MRO budget and don’t require capital expense approval.
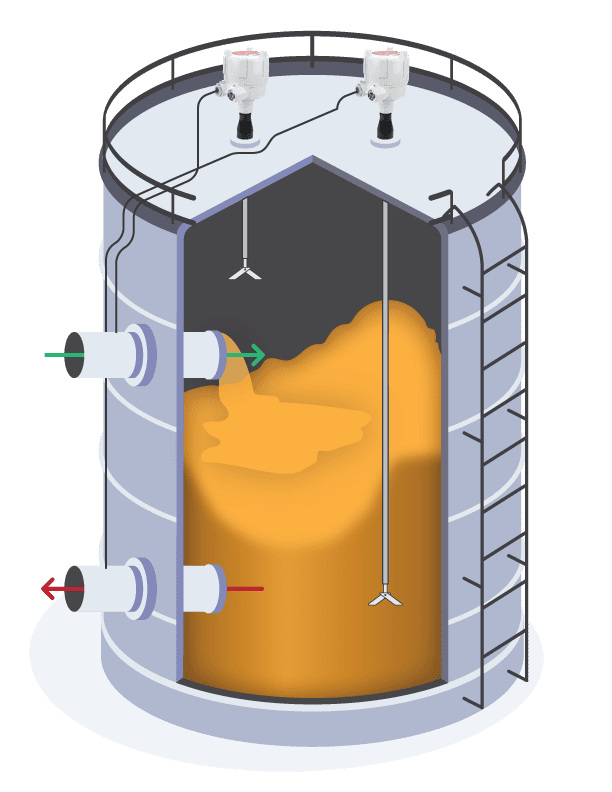