That’s what level sensors and software can do for your plant—both easily and affordably.
Measurement starts with the sensor.
In most cases, the most important job of a level sensor in a silo or hopper is to ensure adequate material is flowing through the system to avoid process interruptions and reduce cycle times.
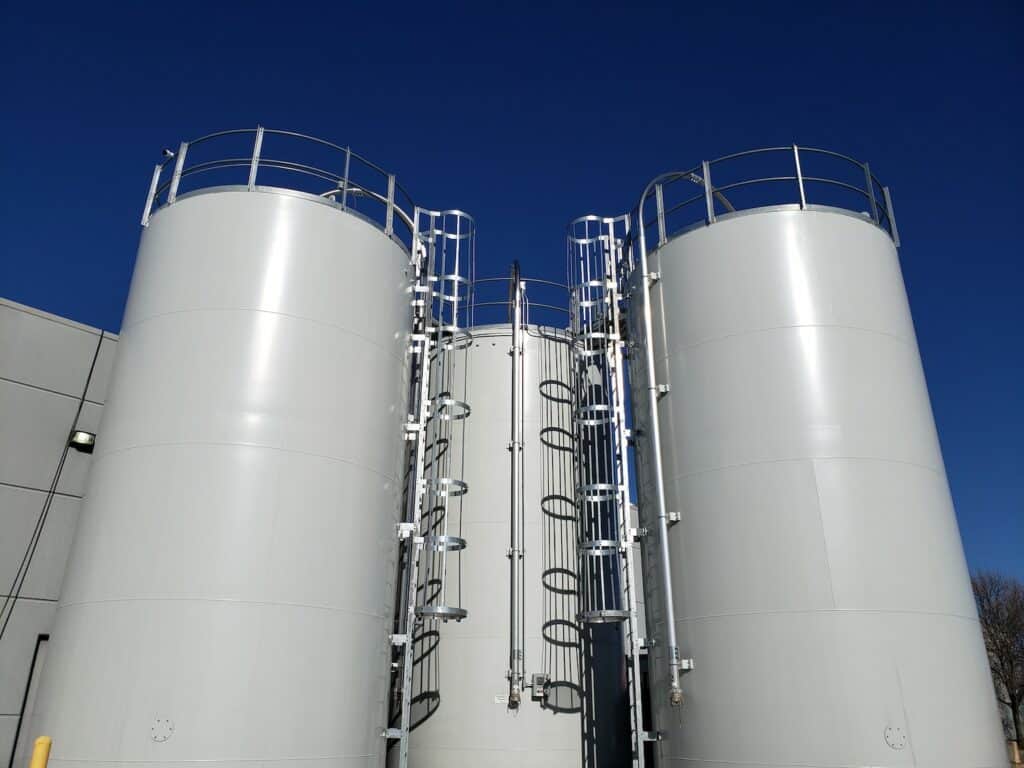
Level sensors are easily installed or retrofit on most any silo. Level sensors measure distances with very high levels of accuracy, generally within +/-0.2”. The types of sensors best suited for solids and powders are immune to the noise and dust that occurs when filling the silos. Liquid-level sensors offer technologies that can compensate for foam, condensation, turbulence, and interface measurement. Today’s sensors report inventory levels in real-time and are highly reliable with long service life and require minimal maintenance.
Sensor technologies to measure solids or powders.
A dust-penetrating non-contact radar is a go-to sensor for non-contact continuous level measurement. The advent of narrow-beam 80 GHz technology ensures reliable operation in dust and fast update rates. For large, active hopper or silos that need continuous tracking a non-contact radar can measure levels in real-time and update in just seconds. In addition to radar, there are other types of sensor technology that may be better suited to the application or your budget.
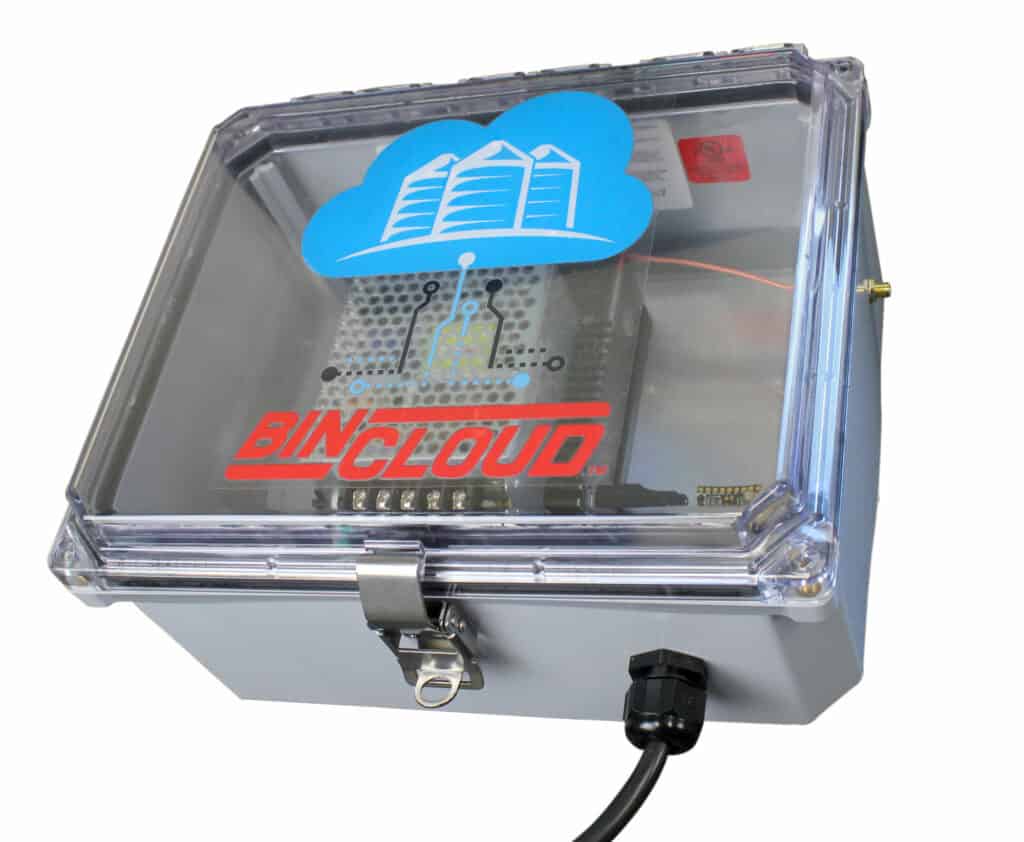
A 3DLevelScanner can account for surface variations of the material in the silo and account for conditions such as cone up or down. It is also the only sensor to measure multiple points on the material surface and account for irregularities when calculating volume.
Bob-style or weight-and-cable sensors work much like a tape measure. They take measurements at predetermined time intervals such as once an hour or several times a day, or on-demand. They have been utilized in processing industries for more than two decades. They are budget-friendly, mechanical devices with long service life.
A battery-powered laser level sensor can be used if conduit and power is not readily available. This type of sensor can save significantly on wiring costs and hiring electricians. Laser technology performs best in low-dust applications such as silos containing granules or pellets.
Simplicity lies in the system.
Thanks to sophisticated software that does the math for you, the distance to the material in a silo can be converted to an estimate of mass or volume. The accuracy of the estimate is dependent upon entering the correct silo dimensions into the software and the evenness or irregularity of the piling or topography of the material in the silo.
Processing and purchasing personnel can rely on the software for timely alerts and trend reporting. They can see their silo inventories in multiple areas in the plant as well as when they are off-site. Readings in the software program are also used by purchasing managers to monitor inventory, place orders in a timely manner, and know when to schedule deliveries.
User-friendly software platforms.
As far as software is concerned, you need to determine if you want software installed on your local area network (LAN) to access from a PC or a cloud-based software-as-a-service (SaaS) that is accessed from the internet on a phone, tablet, or PC.
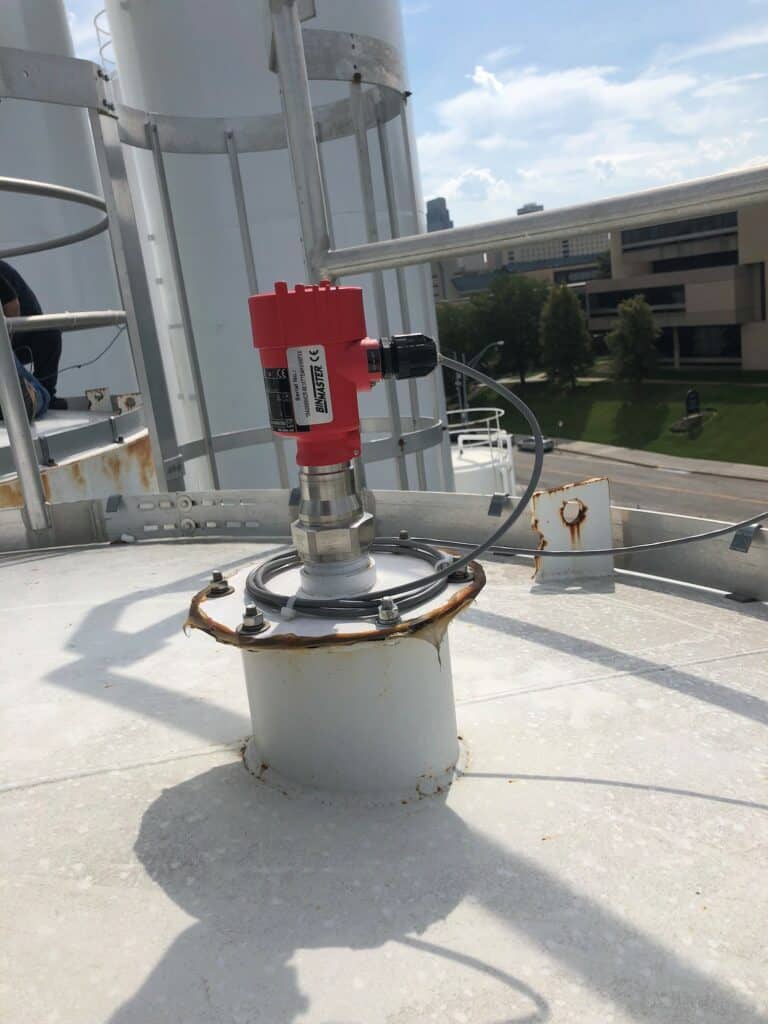
Both are easy to work with and highly affordable. A software program installed on your local network is a one-time software purchase per plant location. The software accommodates up to 120 silos. Cloud-based programs are subscriptions based upon the number of silos you are monitoring. The cost is several dollars per month per silo, plus a cellular program if one is needed.
Cloud-based programs have the benefit of not requiring an IT expert to install or manage the program. Updates to the software are provided by the host company, which will also provide the necessary training and ongoing support.
Both LAN and SaaS programs offer similar features. Both have easy-to-use, graphical interfaces. Bins can be sorted by type and status. An administrator can control who has access to the program and what information is available to them. Historical reports can be quickly downloaded for specific time periods.
Perhaps the most loved feature of inventory management software is automated alerts. Sent via text or email, these alerts help plants ensure that silos or hoppers don’t run empty and interfere with production. When used in tandem with purchasing, orders can be placed in a timely manner and deliveries scheduled so as not to interfere with production.
An automated inventory system using level sensors and software is highly affordable. It offers simplicity and speed while allowing plant personnel to be safe and more effective (and happy) in their jobs. One quick call can get your plant’s needs specified.