In various industrial sectors, especially in bulk material handling, it is becoming increasingly necessary to combine continuous level measurement and data monitoring with automated visualization. The measurement results from UWT silo sensors are quickly and easily displayed using licence-free software and can be conveniently called up on screen at any time. This effective silo logistics system significantly increases transparency and planning reliability for the plant operator. If desired, customers or suppliers working with in the processing plant can also be integrated into this system. With the right combination of level and point level measurement, extremely efficient solutions for bulk solids management can be realized.
This was such the case in this application: an international plastics processor was faced with the primary difficulty of mapping the exact real time fill levels of silo batteries at three production sites and making this information centrally accessible. In addition, the sensors had to work reliably and precisely, regardless of the different properties of the stored plastic granules, such as the DK value, dust development or fluctuating temperatures.
All Under Control! Centralized fill level monitoring with convenient Modbus network
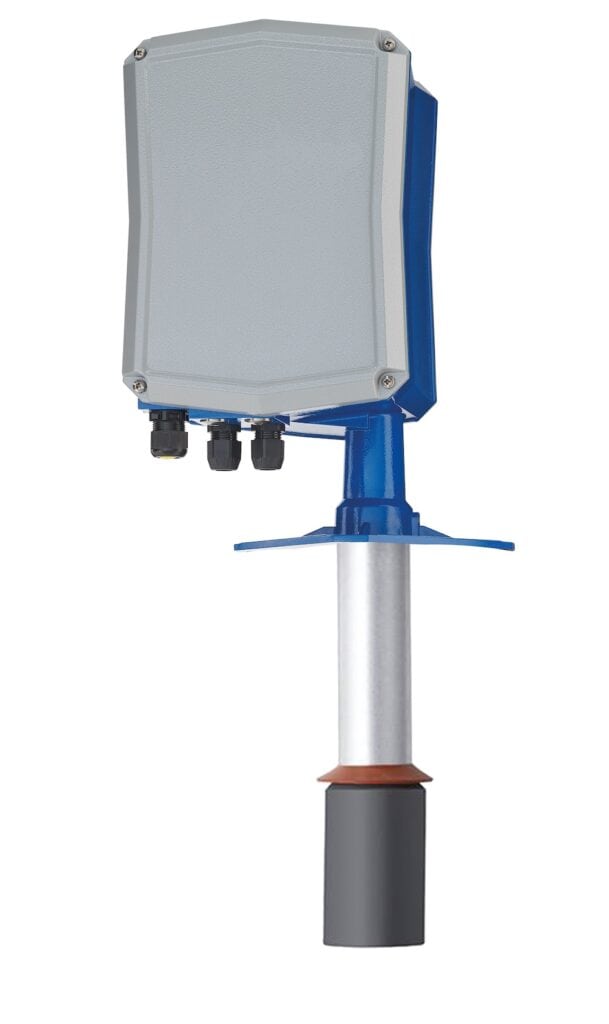
The project was implemented by UWT with a customized solution using a combined installation of the NivoTec® 3500 for level monitoring, the NivoBob® 3100 electromechanical lot system for level measurement and the RN 3002 full detector from the Rotonivo® series.
The NB 3500 with Modbus RTU interface continuously measures the level of various plastics in the silos, regardless of the bulk density and DK value. The Rotonivo® – RN 3002 full silo alarm reliably supports the system and thus protects against overfilling. The arm of the Rotonivo® rotary paddle level switch can be flexibly adjusted to the required length and the appropriate switching point. Both sensors are versatile all-rounders in the plastics industry and are suitable for use in all solids, granulates and powders. They are cost-effective and easy to install.
Optimal monitoring and control of fill levels
The NivoTec® NT 3500 is a level visualization system for displaying and monitoring fill levels and limit levels, ideal for complex applications. This stand-alone system works with visualization software on a web server module and can monitor up to 50 silos – or more on request.
At the core of the NT 3500 is a web server module with powerful visualization software. All fill level monitoring and display functions can be conveniently operated via a PC or an illuminated membrane touch panel. The Ethernet interface allows simultaneous operation from all connected PCs, with password-protected access. The control cabinet can be equipped with various operating and display elements, including a touch panel (10.4″ or 15″) or a digital fill level indicator with LED lights for full and empty notifications.
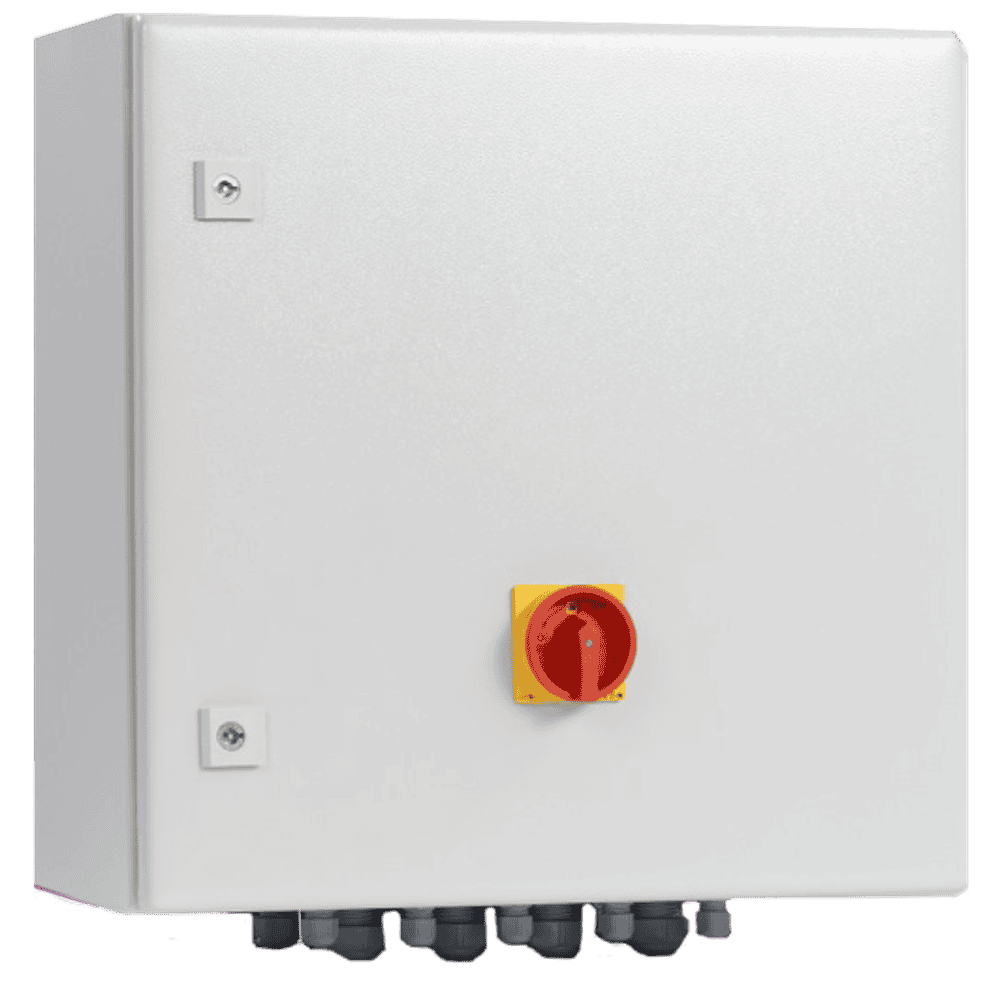
Electromechanical lot systems can be started via the visualization software or manually using a button. A horn can be installed on the silos to sound an alarm in the event of a full signal. A pinch valve control to stop filling in the event of a full alarm is also available. The NT 3500 offers a complete solution, including the power supply for the sensors, and is supplied with project-specific electrical planning.
Core components of the system solution:
NivoTec® NT 3500: This system offers comprehensive visualization of fill levels and enables central monitoring. It displays the fill levels in real time and ensures that the data from all production sites can be retrieved and analyzed centrally. The three silo systems were connected to the NT 3500 controller via gateways and VPN tunnels, which ensures secure and reliable data transmission.
NivoBob® 3100: The level measurement is carried out by the robust NivoBob® 3100 lot sensor, which delivers precise measurement results regardless of the material properties of the plastic pellets. This independence from variables such as DK value, dust development or temperature changes is crucial for the reliability of the measurements.
Modbus network: Communication between the level sensors and the central visualization system takes place via a Modbus network. This protocol enables fast and reliable data transmission, which means that the central systems always receive up-to-date and accurate fill level information.
Rotonivo® -RN 3002: To prevent silo overfills, the full detector of the RN 3002 series is used. This sensor continuously monitors the maximum fill level and alerts in a timely manner to prevent overflows.
Key challenge and its solution
The centralised recording of the fill level monitoring of several silo batteries across different locations places specific demands on the communication and measurement systems:
- Real time data availability: For efficient production planning, it is essential that the fill levels are available in real time. The Modbus network from UWT ensures that the measurement data is transmitted immediately and without delay.
- Precision and reliability: The NivoBob® 3100 systems provide accurate measurement data that is independent of varying material properties. This reliability is crucial in order to obtain consistent and usable information.
- Central administration: With the NivoTec® NT 3500, the fill levels of all locations can be centrally managed and monitored. This enables management to react quickly to changes and make informed decisions.
Benefits and results
The UWT solution offers numerous advantages:
- Increased efficiency: The centralized recording and real-time display of fill levels means that production processes can be better planned and resources optimally utilized.
- Cost savings: Precise fill level measurement and the avoidance of overfilling reduce material losses and production downtime.
- Increased operational safety: The use of reliable sensors and a robust communication network minimizes the risk of incorrect measurements and technical failures.
Thanks to the implementation of gateways and VPN tunnels to connect the three silo systems with the NT 3500 controller, the plastics processor was able to significantly improve its operating processes, increase efficiency and ensure operational reliability. The flexibility and reliability of the technologies used have proven their worth in the demanding environment of plastics processing.