In this customer experience, CEO Michiel de Boer and team leader Ronny Kaβ explain:
- How hygiene and cleanability were decisive in choosing Dinnissen
- How Nöll & Co now produces 6 times as many products per day with the new line
- How Nöll & Co is experiencing the service of Dinnissen’s engineers
- How all output targets were achieved
Hygiene and cleanability were decisive
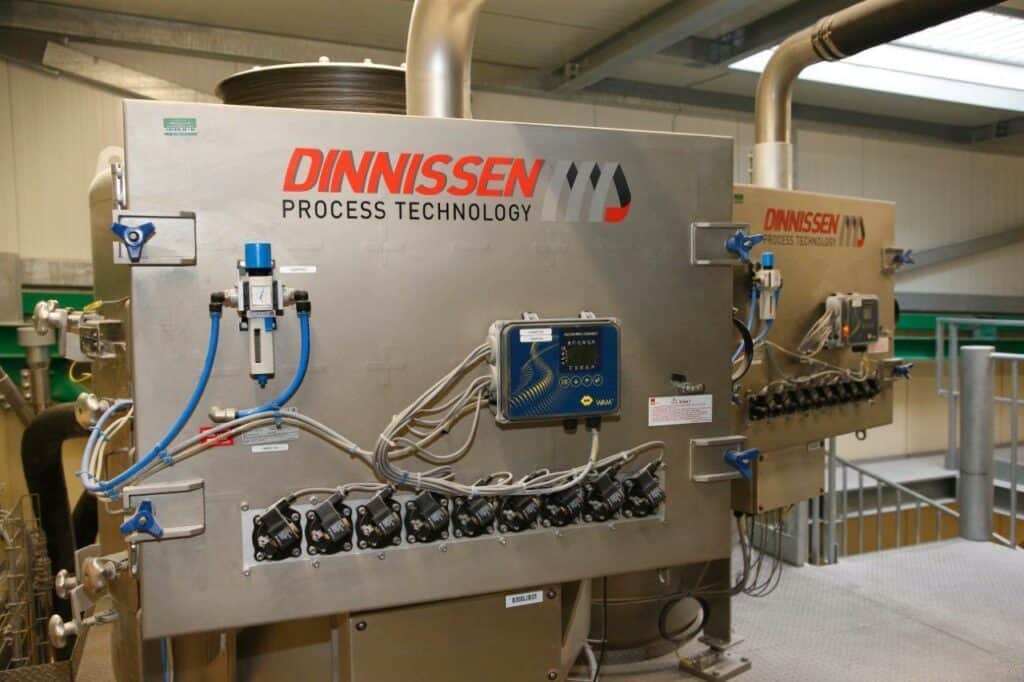
As Nöll & Co produces ingredients and semi-finished products for dairy products, baked goods, confectionery, ice cream, sports nutrition, soups and sauces, strict hygiene requirements apply. Therefore, fast and efficient cleaning between batches were important requirements. After asking around which company provided the best and easiest-to-clean machines, Nöll & Co came in contact with Dinnissen. First, options for modifications to the old line were discussed, but soon enough a plan for a completely new line was drawn up.
“Through Dinnissen’s post-installation support, we achieved the desired output of 3 tons per hour.” – Ronny Kaβ, team leader Nöll & Co
New line brings daily production from 5 to 30 tons
Stock & Production Team Leader Ronny Kaβ says: “The production that is now possible is incomparable to that of the old line. With the original machines, we could produce 3 to 5 tons per day. The new line has increased this six-fold, to around 30 tons per day.” The entire line was supplied by Dinnissen; from product intake with a bag chute and Big Bag stations, the raw material is conveyed via vacuum pumps into hoppers. This is followed by a Pegasus® mixer, a Big Bag filling system, and a filling line from Votech, which was built in cooperation with Dinnissen.
“You can buy a nice race car, but you also have to train the drivers to be successful. The same goes for Dinnissen’s line and our staff.” – Michiel de Boer, CEO Nöll & Co
The original plan drawn up by Dinnissen and Nöll & Co did not equal the line that was actually built in the end. Ronny Kaβ points out: “Because Dinnissen gave so many possibilities and options, it was difficult to filter out the best choice for ourselves. We now have a completely different line than we thought we were going to build when we first started. But on the other hand, the service to keep the line running well was top-notch. When the line was just up, we were nowhere near achieving the expected 3 tons per hour. After fine-tuning and tips and tricks from Dinnissen, we tackled the bottlenecks and got to where we want to be.”
CEO De Boer: “Our efficiency is still growing every week”
Michiel de Boer, CEO of parent company F&F Group is also positive about the aftercare: “You can buy a nice race car, but you also have to train the drivers in order to be successful. The same goes for Dinnissen’s line and our staff. A Dinnissen employee explained to our team how to work with the line optimally, and our efficiency is still growing every week. Dinnissen’s online support also works fine. You can get in touch with a technical engineer easily, who then helps us remotely. Out of 10 problems, eight can be fixed in no time.”
“Production has gone from 3-5 tons per day to 30 tons per day. That’s a six-fold increase in total production.” – Michiel de Boer, CEO Nöll & Co
All output targets reached
Together, the team at Nöll & Co in Büren and employees at Dinnissen optimized the line. Not only by aligning all components but also by training the employees. As a result, the predetermined targets in terms of output were achieved. In fact, Nöll & Co already has room for a second line to increase capacity even further. By all means, the space is there in Büren. In their modern warehouse, bags of milk powders are ready to be dispatched, to just about every branch of the food industry.
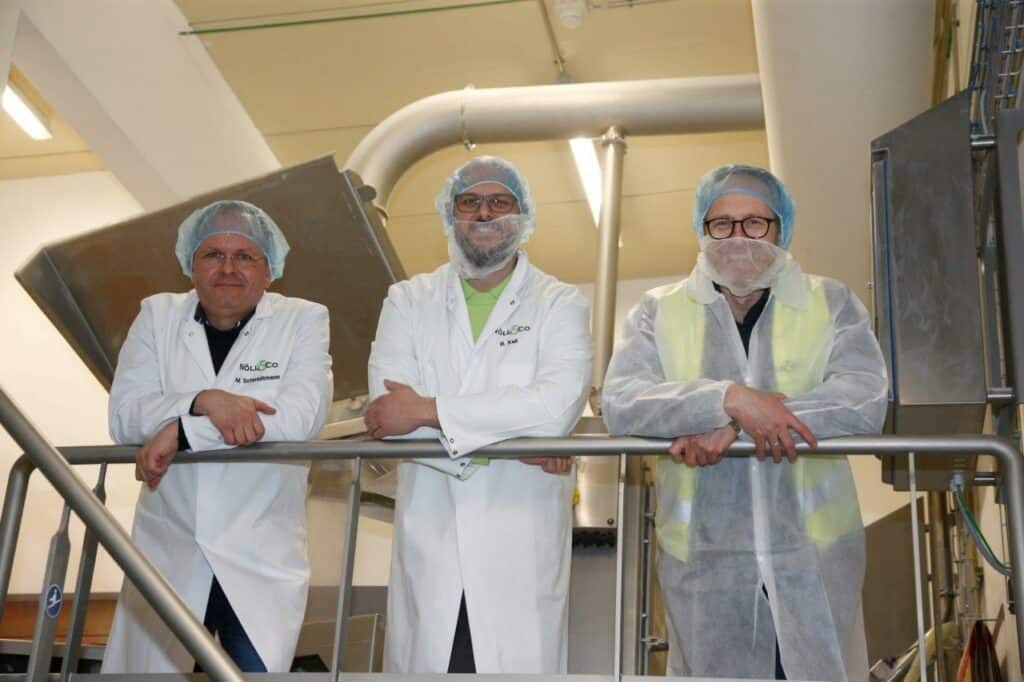
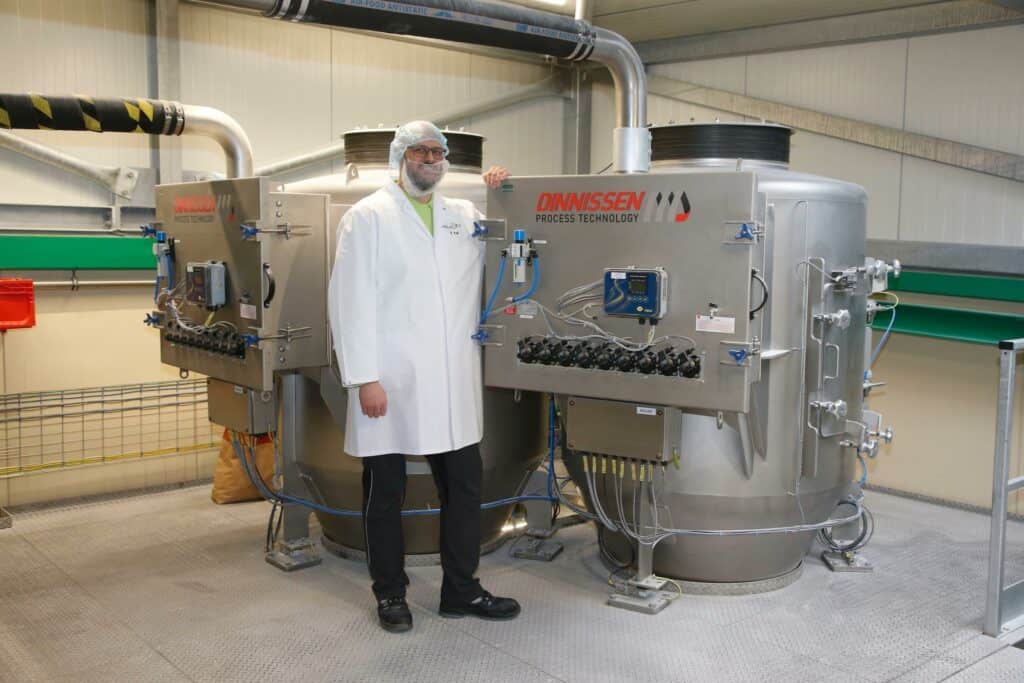