As a fifth generation family business, we have learned that long-term success in fertilizer production comes down to consistency, process control, and flexibility. Our focus at EMT is not to offer standard solutions, but to translate our blending expertise into systems that work for the reality of our clients—where raw materials vary, space is limited, and time is always critical.
The process starts with dosing
Everything in blending starts with correct dosing. Whether you’re working with granular materials, powders, or liquids, accurate dosing is the foundation for any consistent end product.
In our systems—whether continuous or batch—we use load cell-based weighing and stainless steel dosing equipment to ensure that dosing remains stable under various conditions. Especially with varying bulk densities, humidity, or raw material behaviour, the dosing mechanism needs to adapt. That’s why we rely on frequency-controlled drives and live feedback loops between hopper weight and dosing speed.
We design our systems so that the dosing is not only accurate, but also repeatable. It’s not about being precise once—it’s about being precise every single day.
Choosing between batch and continuous
Over the years, we’ve installed many batch and continuous blenders around the world. Neither system is better by default—it depends entirely on the operation.
- Continuous systems, like our Weighcont blender, are excellent for high-volume plants with consistent recipes. The dosing and blending happen in one flow, with minimal intervention, and the entire system is easily automated.
- Batch systems give more flexibility in formulations, better suited for operations with frequent recipe changes or specific blending requirements with smaller batches, lower central capacity and higher amount of raw materials.
A good example of the continuous system is one of our recent projects in South America, where we implemented a full processing line including a Weighcont blender, micro dosing unit, inline urea coating machine, and a high-capacity bagging system. The line was designed not just for output, but for blending precision, ease of material flow, and the ability to apply additives mid-process.
This project shows how a continuous blending concept—when combined with liquid dosing and inline coating—can meet both capacity and formulation complexity in a tropical production environment. That line now runs at high output with minimal intervention, thanks to process integration and system stability.
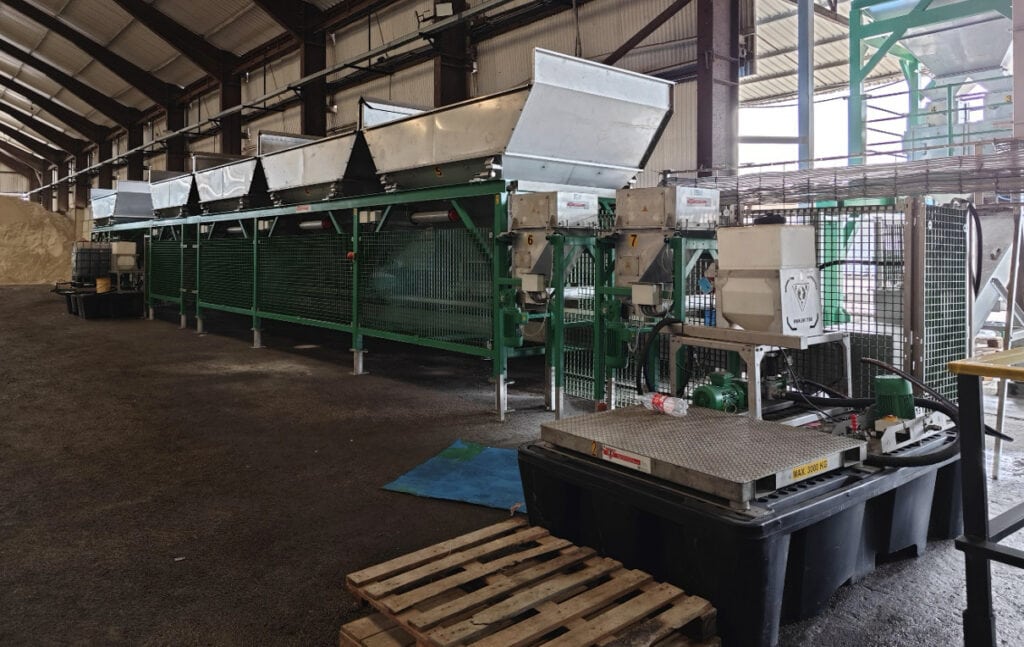
Blending is more than just mixing
Our vertical screw blenders are designed to create a lifting wave motion that mixes gently but thoroughly. In horizontal drum blenders, we use internal flighting to fold materials without breaking granules. In paddle blenders, the twin-shaft system ensures quick mixing, especially for water-soluble fertilizers or powders. Inclined screw blending is a thorough blending with a short mixing time.
In all designs, we pay special attention to cleanout. Having a fast clean discharge with no product left behind means less downtime and less contamination between runs—something that really adds up over time.
Adding micronutrients or liquids
These days, many producers are working with additives—whether it’s inhibitors, anti-dust/caking, or trace elements. The challenge is how to integrate them efficiently and accurately into the process.
At EMT, we use inline dosing techniques for liquids and separate micro-hoppers for dry micronutrients. In a recent project, for example, a Micro Dosing Hopper was added to ensure precise application of key nutrients. This is especially important when the additive is only 1–2% of the total mix—but plays a critical role in product performance.
The ability to dose both powders and liquids during blending, without interrupting the process, gives producers the flexibility to meet customer specifications without needing double handling or steps.
From blending to bagging – Keeping the flow aligned
I always remind clients: a blender is only as effective as the process that follows. We often integrate bagging systems directly after blending, so there is no break in the material flow.
Whether filling 25/50 kg bags or FIBCs of 500/1500 kg, we ensure that the packaging line can handle the blender’s output. In the previous mentioned project in South America, a Quattro Small Bag bagging unit was implemented to process high volumes of product with automated precision. The system is designed to match the speed of the blender, minimizing bottlenecks and operator dependency.
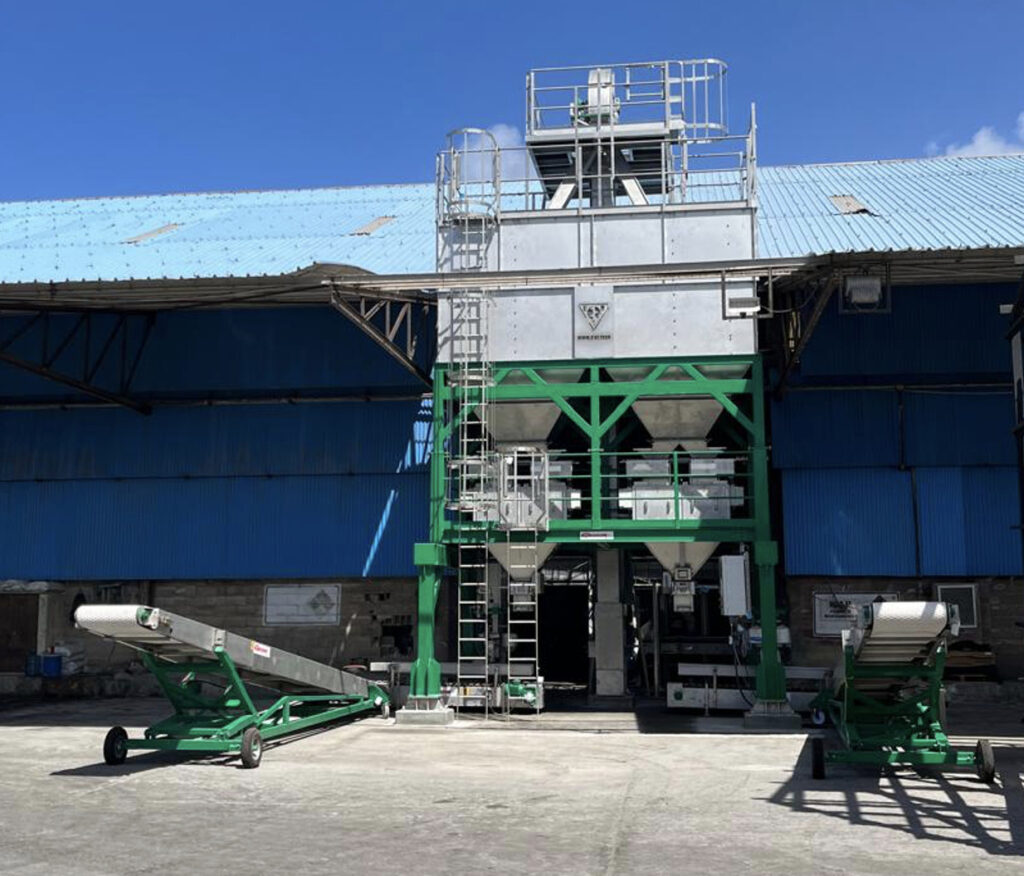
Process control and operator support
A well-designed blender is only as strong as the control system behind it. That’s why EMT also invests in process management software, including Optiblend. This software allows producers to calculate blends based on nutrient value, cost, and crop requirement—then sends that data directly to the machine controls.
In a case like the one in South America, where complex formulations and high throughput go hand in hand, having this kind of digital support reduces operator error and increases formulation confidence.
Final thought
At EMT, blending is where everything starts. It’s the point where raw materials become a product with value. Our role is to support that process—not with overcomplicated solutions, but with practical systems that make blending more accurate, more efficient, and more reliable.
Whether it’s in South-America, Europe, or anywhere else, our aim is always the same: help producers control their process and deliver consistent quality every day.