Foreign metal objects may enter the product from a vehicle transporting the product to a processing facility. In other cases, contamination can be traced back to the inside of a processing plant, oftentimes from nails, bolts and other metal parts falling from grinding, crushing or other processing machinery.
Fortunately, metal contamination problems can be reduced or eliminated by using metal detectors and magnetic separation equipment. Incorporating metal detectors and magnetic separators through various stages of food processing helps ensure regulations are satisfied and product purity is protected, whether the food characteristics are dry, moist, or liquid.
Also, removing contamination early in the production stage prevents damage to grinders, ovens, screeners, and other processing equipment. This article discusses how metal detectors and magnetic separation equipment are applied at food processing facilities to produce a safer, high-quality product.
Detect and separate
Installing magnetic separators and metal detectors can help avoid both material contamination and equipment damage in dry bulk processing. Magnetic separators come in a variety of configurations and divert ferrous materials such as fines, shavings, abraded machine parts, screws, washers, and other pieces from the material process stream.
Metal detectors detect metal contamination entering a specific field—for instance a pipe, conveyor, or a material chute—and then activate a rejection mechanism to remove the intruding particle. The most sensitive metal detectors can detect ferrous and nonferrous metals down to submillimeter sizes.
Why install both? No magnetic separator is ever 100% effective in removing contamination. The same is true for metal detectors. Removing contamination first with a magnet also means the metal detector will reject less frequently, reducing product losses.
This dual approach is especially effective in eliminating metal from whole bulk foods such as almonds, coffee and cocoa beans, and raisins, as well as more granular bulk items like sugar, flour, crushed chili peppers, and various spices. The magnet removes the ferrous contamination, while the metal detector focuses on any ferrous metals, as well as nonferrous metals such as aluminum, copper, brass, and stainless steel, missed by the magnet.
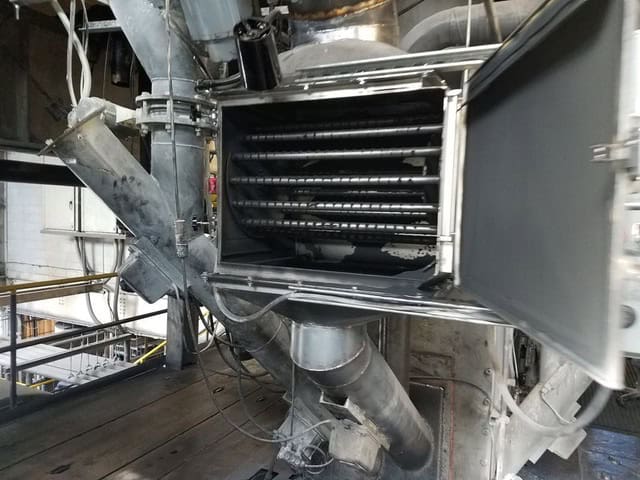
Magnetic separators used in bevy of applications
Assessing the material being processed is a key step in selecting the proper magnetic separator. Materials generally fall into three categories: dry, moist, or liquid. A wide range of product variation exists within each of these groups, depending on the particle size of solids or viscosity of liquids.
If the particles are small and free flowing, a grate magnet provides the best opportunity for ferrous contamination to contact a magnet directly. Grates do the best job with vertical product flows, while plate magnets work well if the material is cascading down a chute. These product-cleaning methods require that the product flow be stopped when removing collected ferrous contamination from the magnet.
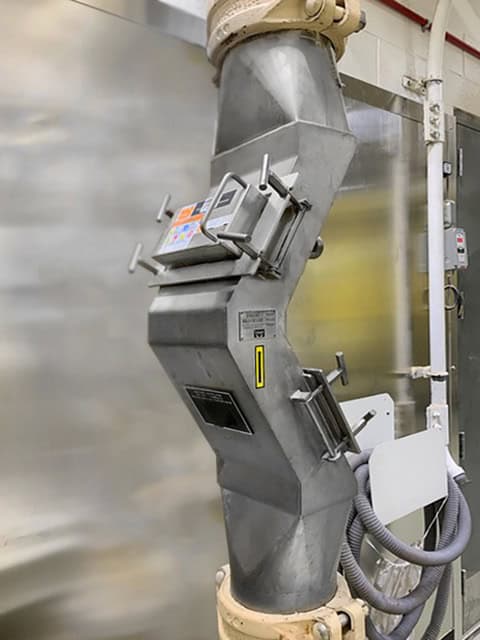
Grate magnets are designed for steep-sloped hoppers, floor openings, vertical closed chutes, and ducts and help prevent ferrous and small, weakly magnetic contaminants—such as work-hardened stainless steel—from contaminating the material mix. Grate magnets are made of one-inch diameter (25mm) magnetic tubes in a grid formation, which allows material to cascade through the grate.
Plate magnets are simple and economical to install and are very efficient at removing occasional pieces of tramp metal from dry material flow. In a typical chute installation, the magnetic material adheres to the magnet face while the product slides across the face of the magnet. The magnetic field attracts and holds ferrous material until the plate is removed for cleaning.
Magnetic separators that have moving parts can help speed up the processing and metal removal from light, fluffy materials that tend to clog and bridge when passed through small openings. In this case, a number of powerful magnetic tubes rotate through the material. The magnetic action attracts and holds the unwanted metal, and the rotary action prevents the material from packing and plugging the processing line.
Products in a liquid or slurry state require a magnetic trap, which removes small particles of magnetic scale, rust, and fine iron contamination from tiny, ½-inch (13mm) pipeline or large 30-inch (762mm) diameter line. All models of magnetic traps have clean, simple designs with no moving parts. They handle materials with temperatures up to 150 degrees F (65 degrees C) with special models available for temperatures to 850 degrees F (454 degrees C).
Drum magnets are also used by processors to remove tramp metal from a product flow. The magnet assembly is enclosed within a stainless-steel drum and fixed in position. The drum rotates around the magnet, conveying material through the magnetic field. Clean or nonferrous material cascades off the drum face while the magnetic material is drawn around the drum and discharged at the bottom.
Metal detectors enhance purity
Once dry material cascades through these magnets, the next stop should be for the material to pass through a metal detector to reject all magnetic and nonmagnetic metal contamination. Metal detectors combine a precision mechanical design with state-of-the-art electronics, multiple frequency range, vibration immunity and complex algorithms to detect the smallest metals in various products.
The most sensitive metal detectors can detect ferrous and nonferrous metals down to .5 millimeter in size, making them ideal to prevent fine metal contamination in granulators, shredders, and downstream packaging equipment. Metal detectors are also used to verify that desired metal objects are present in final package goods—such as novelties in plastic containers.
Modern metal detectors operate for long periods of time, frequently in adverse environments, with minimal maintenance. The power required to operate a metal detector and reject drive is minimal, even if a special conveyor is needed to pass through the metal detector. Metal detectors can be configured to reject the contaminated product automatically, even if the rejection point is some distance from the detector.
A tunnel-style metal detector should be strategically placed during the stage when bulk material is transported on a conveyor belt and before any final packaging (heading for wash down or after roasting, for example).
These conveyor system metal detectors are available in various belt width and aperture heights and can be calibrated for different material sensitivities. As the bulk material makes its way through the detector, any lingering metal is detected via an automated reject such as a flip gate or head pulley.
Metal detectors are available in other configurations and styles. For example, Liquid Line Metal Detectors are designed for liquids, pastries, slurries, or other viscous products where high-sensitivity metal detection is required. This type of detector can be mounted vertically or horizontally and is available in pipe sizes up to 4 inches in diameter. Also, vertical drop metal detectors are engineered for use in gravity free-fall applications.
Final checks for quality
Dry bulk material can pick up trace metal contamination as it goes through a final hopper and into a super sack or bulk bag. For extra protection, a series of tube magnets coupled with a vertical metal detector and reject is recommended before bagging and sealing This final step prevents an entire sack or bag from being rejected because of metal contamination, helping protect a processor’s brand name and recognition.
Using the right combination of magnetic separators and metal detectors can safeguard processing equipment, ensure product purity, and protect a company’s brand name. These tested technologies always keep bulk material under strict surveillance and prevent unnecessary machine downtime and costly maintenance.
Established in 1942, Eriez is a global leader in separation technologies. Our commitment to innovation has positioned us as a driving market force in several key technology areas, including magnetic separation, flotation, metal detection and material handling equipment. The company’s 900+ employees provide trusted technical solutions to the mining, food, recycling, packaging, aggregate and other processing industries. Headquartered in Erie, Pennsylvania, USA, Eriez designs, manufactures, and markets on six continents through 12 owned international subsidiaries and an extensive sales representative network.
By Craig Lorei, Eriez Global Market Manager-Light Industry