Abrasive and sticky product such as sugar, cocoa, lactose & chocolate can be a serious challenge for operators. Products such as sticky sugars can be very unhygienic, tough to clean and can lower separation efficiency, while magnets with exposed moving parts are prone to binding/jamming and handling issues.
There is a wide range of risks where metal fragment contamination can occur in the snacks and confectionery industry, ranging from equipment wear (such as chocolate conches) to contamination in incoming raw materials. Some ingredients such as salt, sugar, and gluten are more likely to contain foreign metal contamination, such as tiny metal fragments, than other ingredients.
Magnetic separators are often installed in jacketted chocolate lines or syrup lines above bulk ingredient discharges, upstream of powder sprinkles, post minor ingredient intakes, and at ingredient bag dump areas.
It is vital to ensure magnets are installed at ingredient intakes for traceability of suppliers that they meet minimum requirements.
There may also be several strategic processing locations through the plant prior to final products and packing. Magnets placed upstream will help control the risk before it is dispersed more extensively throughout the process.
The final magnet should be installed as far downstream as practical, yet upstream of final metal detection. This will help relieve the metal detector and help reduce nuisance trips and excess wastage that results from a quarantine event.
Magnattack® magnetic separation solutions for confectionery applications:
Gravity (Control Flow Ingredients)
Mag-Ram® Self-Cleaning Grate Magnet
- For dry products/ powder applications
- Customisable cleaning options
- Zero downtime
- Provides lean contaminant sample
- Available in 1-800 TPH capacity
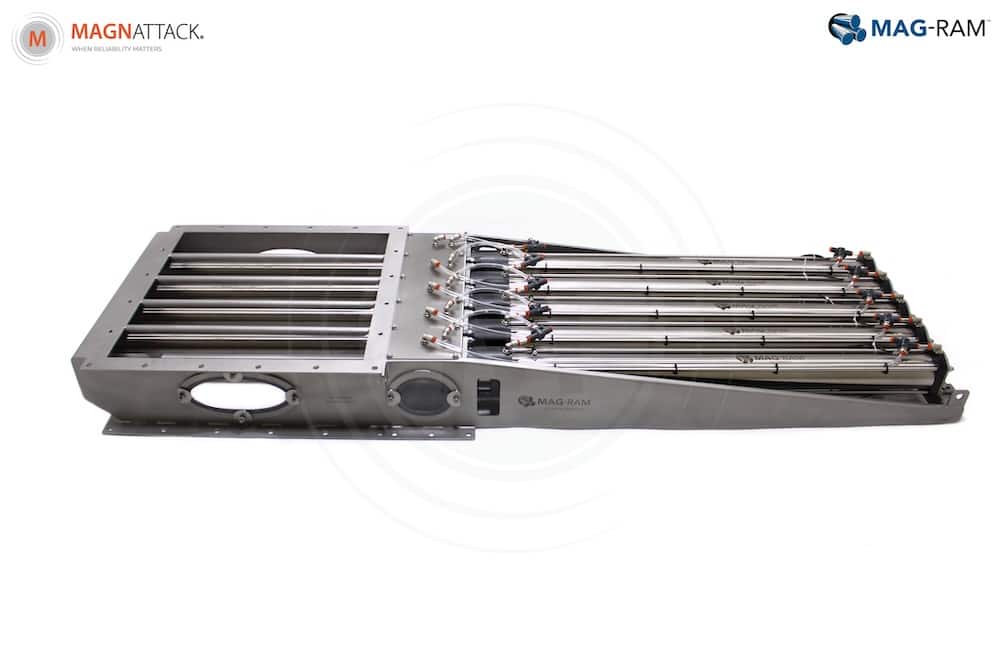
- For dry products/ powder applications
- Suits both ultra-fine powders and coarse granular products
- Cleaning tool for efficient cleaning
- Customisable designs available for tight spaces
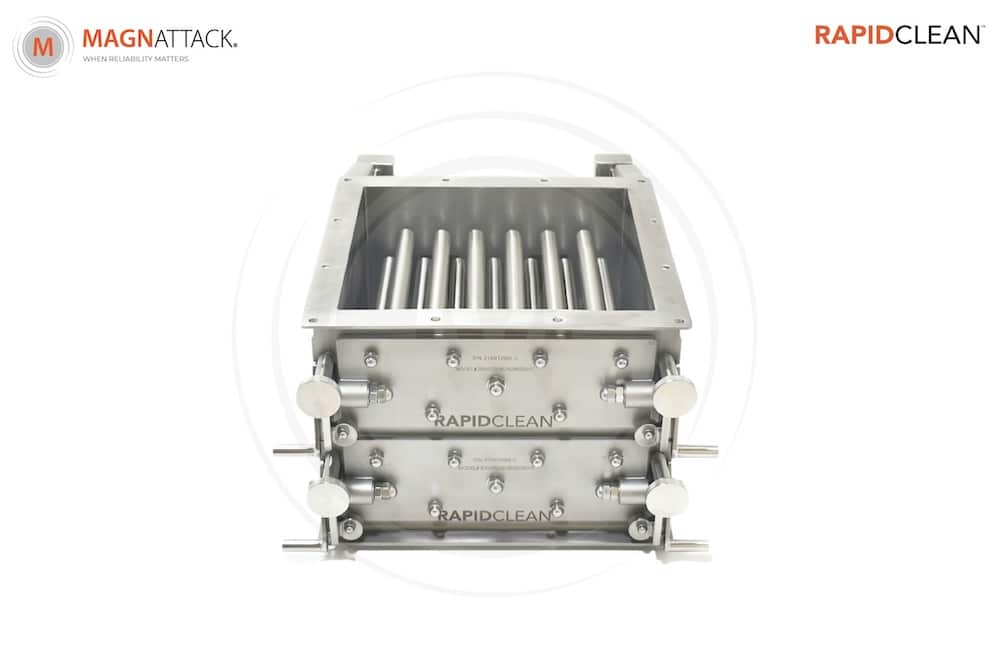
Blowlines (Powder Conveying)
Spherical Pneumatic Transfer Magnet
- For dry products in high-velocity pneumatic powder transfer applications
- Cleaning station & cleaning tool
- Large surface area for safe retention or contaminants
- Hydroformed housing to optimise product contact & reduce flow restriction
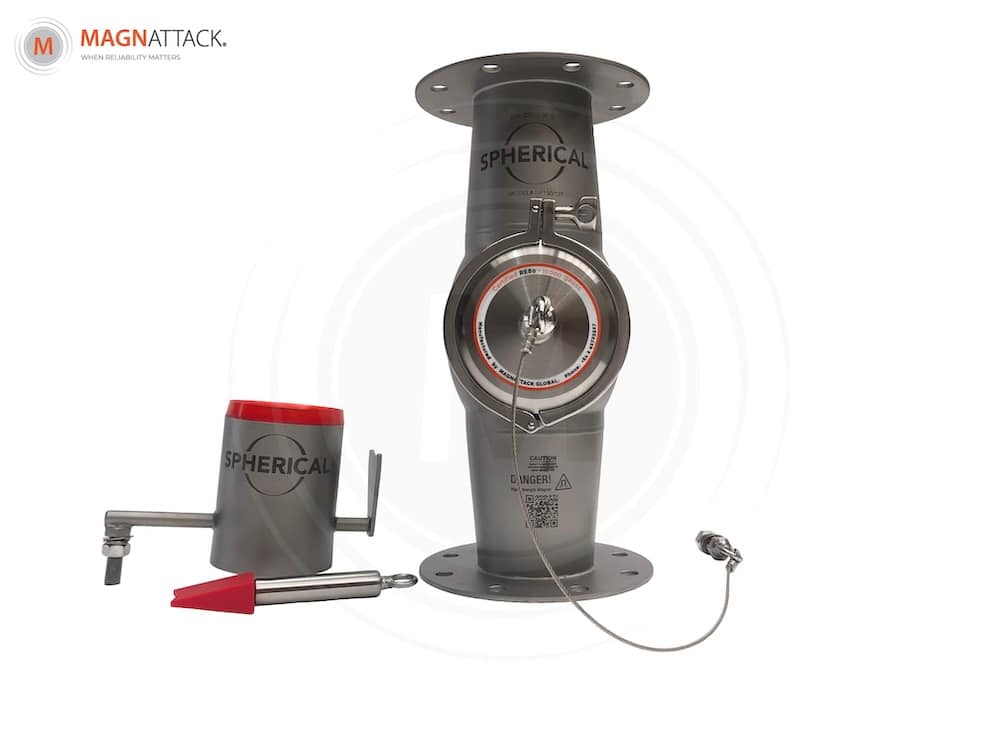
Liquid Processing
- Jacketted designs for heated product lines, such as chocolate
- Magnets perform at maximum strength in high-temperature liquid and CIP application
- Maximum product to magnet contact
- Efficient separation without leaks, blockage, or distortion
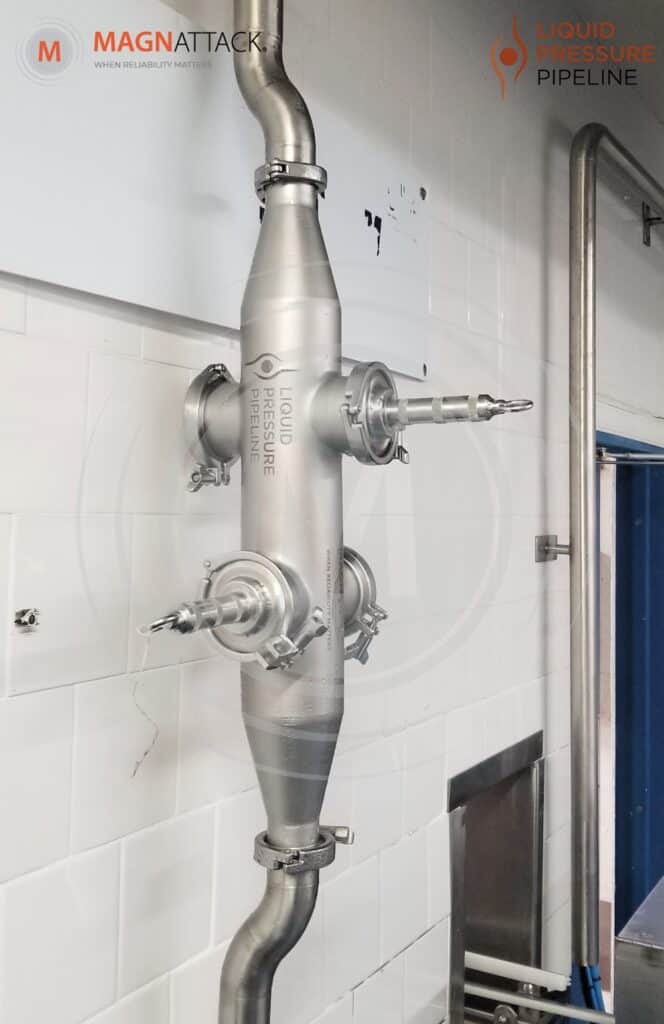
- For viscous & non-viscous liquid applications such as syrups, chocolate, oil, etc.
- Protection of expensive equipment such as pumps or homogenisers
- Saves time during filter & magnet inspections
- Fully drained design
- Available with thermal jacketting
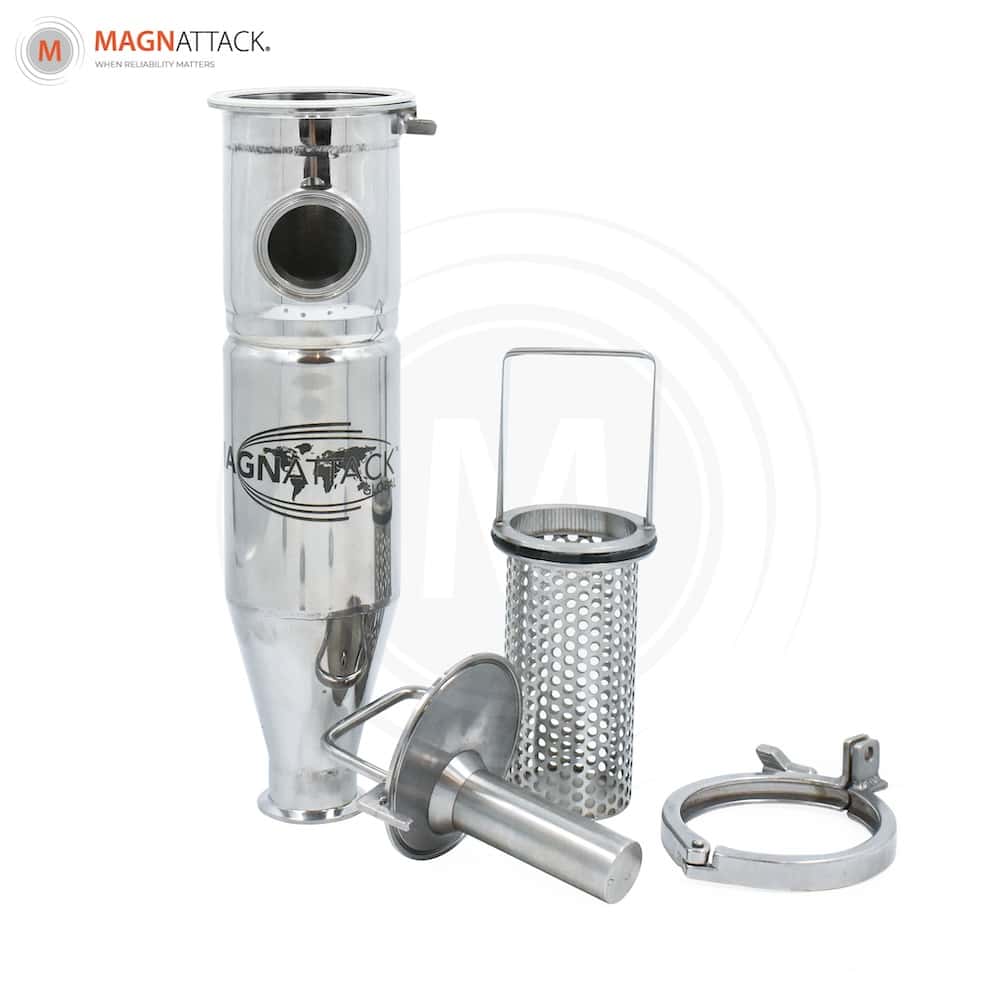
High-Risk Applications
- Common use in pipelines, chutes, ducting, and more
- Shape reduces risk of product bridging or blockage
- Minimal impact on line pressure
- Captured magnetics are safely retained in the low pressure zone, reducing the risk of re-contamination
- The leading edge of the probe separates the flow and enables maximum product to magnet coverage
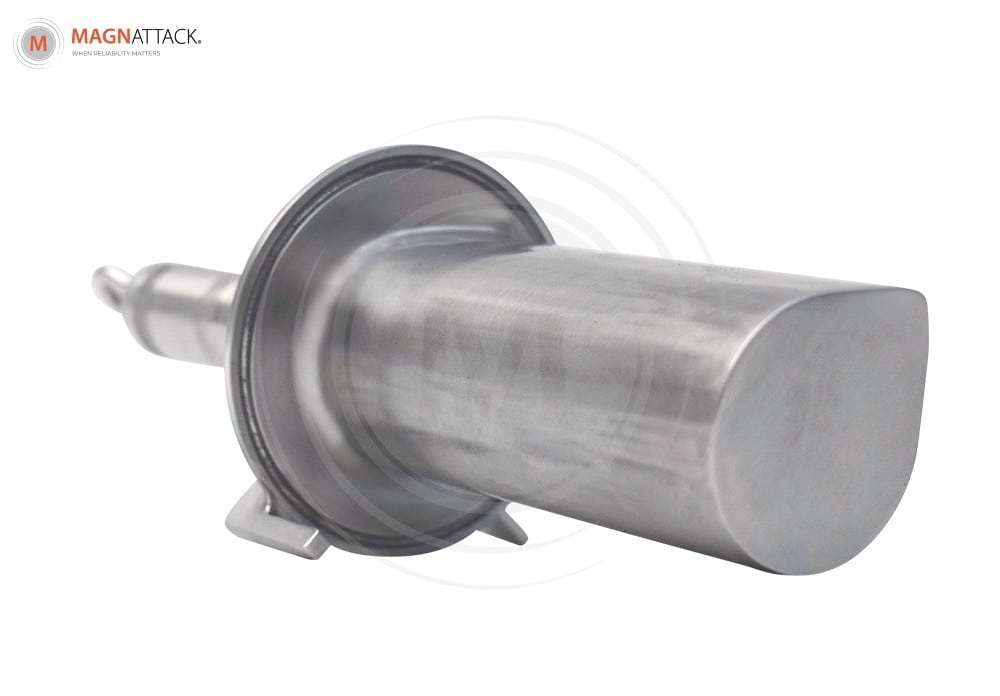
Custom Magnets for Existing Equipment
- Suited for free-flowing products
- Customised to integrate to existing plant equipment
- Can be installed at inlets & outlets of hoppers, bases of chutes/ ducting, above packers on packing outlets, sifter discharges, and before high impact & damage susceptible machinery
- No frame options – easy cleaning and less obstruction to flow
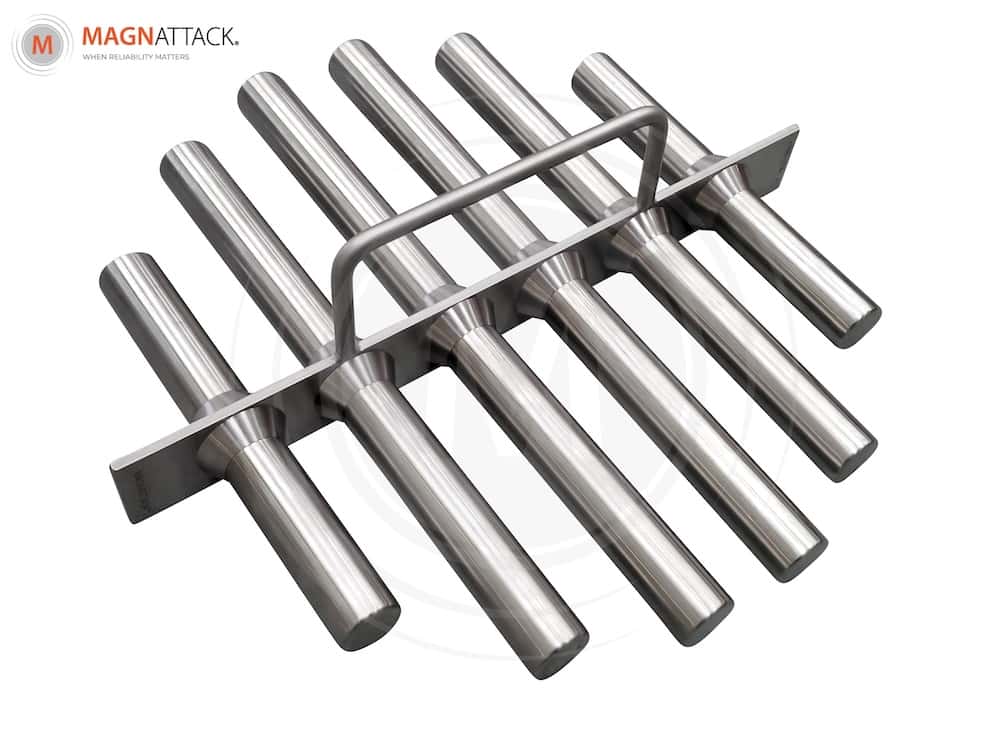
- Perfect for installing at the point of discharge at the end of conveyors
- Optional complete bracketry systems for easy handling – allows operators to lift out and away from the process flow for cleaning – reduces risk of recontamination
- Larger diameter bar size for increased separation efficiency
- Does not cause bridging/ blockage in product lines
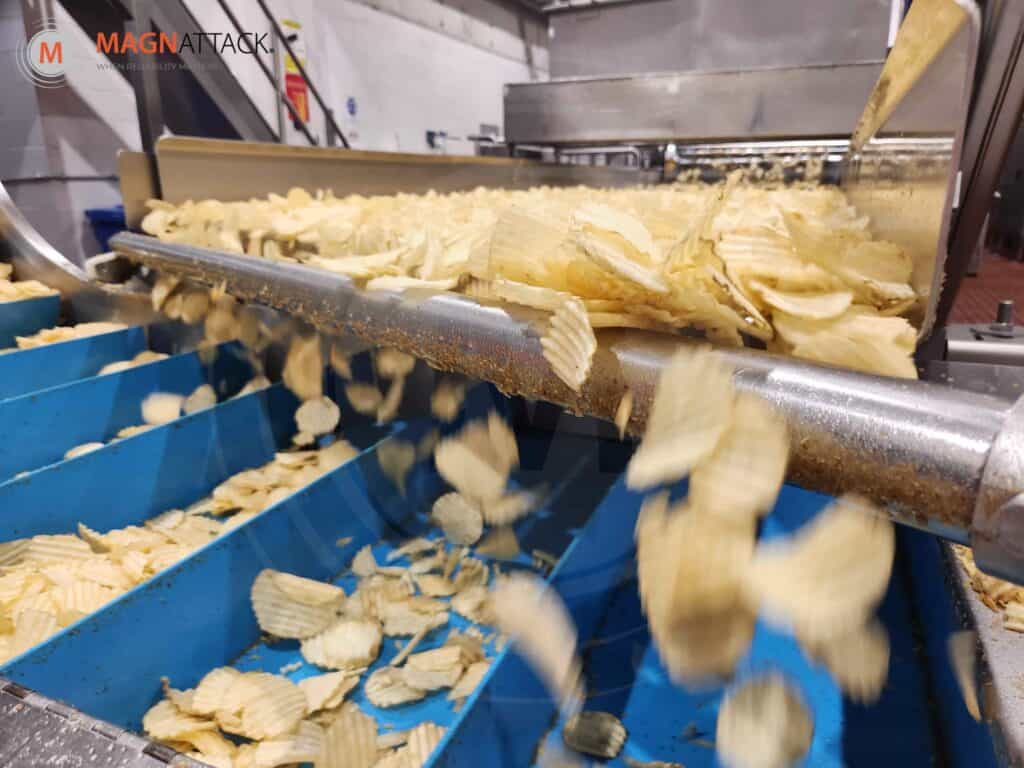
Some applications are susceptible to wear and tear due to abrasive product. This can cause the magnet surface to wear to the point where worn areas on magnets can lead to toxic contamination issues. Magnattack® developed Dura-Slik® – a Magnattack® surfacing treatment to resist abrasion and add a barrier of protection against harsh product and the effects of contaminants reacting with the magnets in some instances. This Abrasion-Reduction Technology was designed for magnet surfaces which greatly reduces surface tension, abrasion and helps in releasing any bonded powder and magnetic fragments.
Find out more about Magnattack® magnetic separators, or contact the Magnattack® Global team.