Demand for lithium-ion batteries continues to grow in the electromobility sector. This increases the demand for raw materials, such as copper. One of the world’s largest and best-known deposits with estimated reserves of 1.1 billion metric tons of copper ore is located near the port city of Ilo – just under 37 kilometers northeast of Moquegua in southern Peru. Anglo American, one of the world’s largest mining companies, operates the Quellaveco copper mine there.
Anglo American is headquartered in London. Through subsidiaries and shareholdings, the Group mines platinum, diamonds, copper, nickel, iron ore and coal. It also operates plants for the extraction of manganese and niobium as well as steel mills.
Ready for the increasing demand for copper
The Quellaveco project was developed jointly by Anglo American and the Mitsubishi Corporation. The ambitious goal: The plant is expected to mine 1.1 million metric tons of copper annually. To ship this enormous amount of raw material to the target countries, Peru is investing heavily in the country’s infrastructure – for example, in a new port terminal located just under 20 kilometers south of the city of Ilo. The terminal is operated by the energy company Engie. In search of a suitable partner to supply the ship loading system, the project managers selected FAM Minerals & Mining GmbH.
The globally active company headquartered in Magdeburg, Germany, is a traditional manufacturer of conveyor systems. Its history dates back to the 19th century. As a leading supplier, the company provides equipment for the entire bulk material handling chain – from extraction, conveying, loading and storage to the processing of various raw materials for different industries. Since the summer of 2022, FAM has been wholly owned by the BEUMER Group, headquartered in Beckum, Germany.
Dust-free to the destination
The Quellaveco open pit mine relies on a high level of automation to protect workers and minimize dust pollution. The copper ore is transported via a conveyor belt to the truck loading station. Sensors signal when a truck arrives for transport. The gate opens automatically and closes again behind the truck. An extraction system is activated to prevent dust from escaping during loading. Once the raw material has been loaded and hermetically sealed on the truck, the gate opens again. Now the truck continues to a tire wash facility. “The facility is automatically activated via sensors – until the tires are 100% clean,” explains Martín Cabrera, port project manager at Anglo American.
No dust formation is to be expected when the copper ore is received, stored and shipped. To be on the safe side, however, the plant operator has installed systems that can capture the particles. “These efficient systems work similarly to large vacuum cleaners,” explains Karen Huaraca, Anglo American’s environmental officer. “They filter the dust and then release the clean air into the environment.”
All the information collected by the sensors is sent to the operations center in real time, enabling the plant to be controlled automatically. The operations center is located about 90 kilometers from Quellaveco.
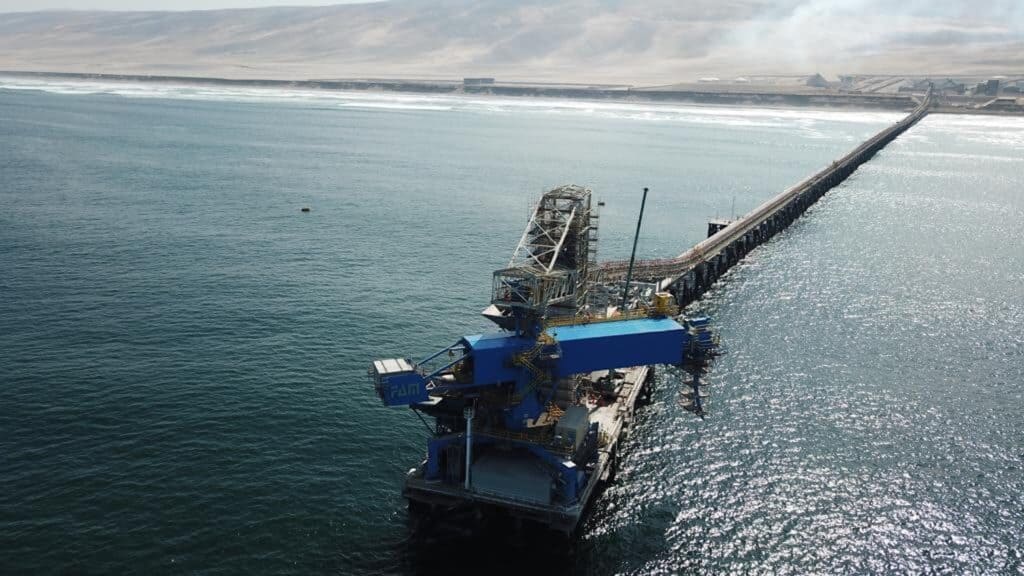
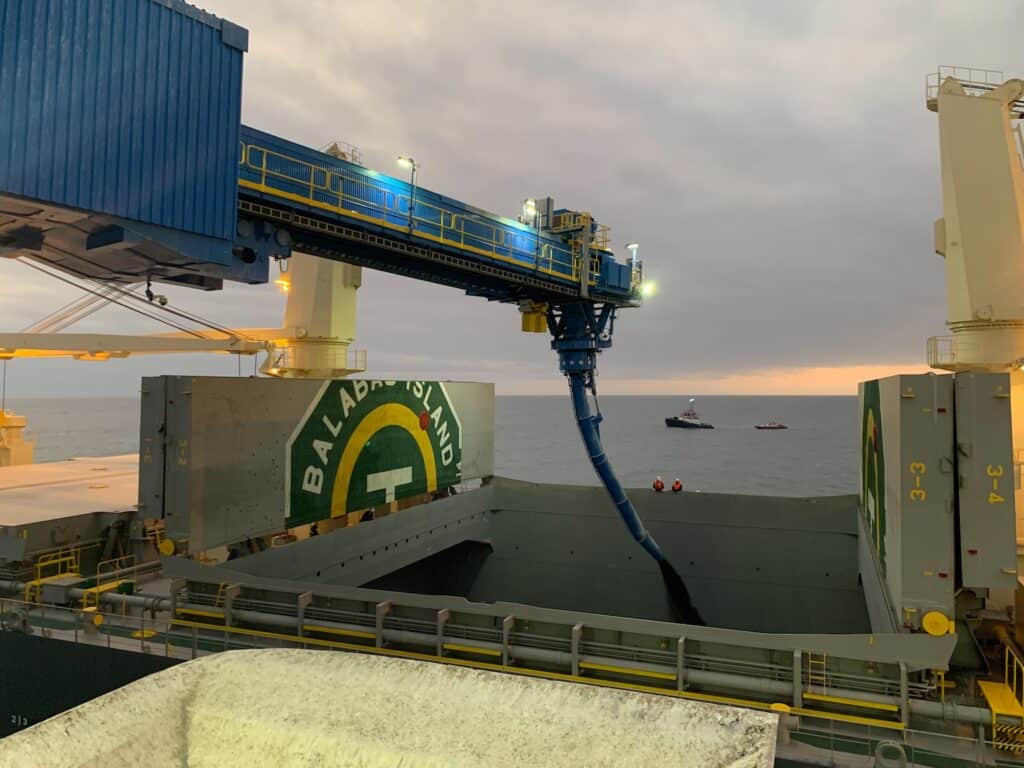
From the mainland on to the ship
The trucks transport the raw materials to the port. There, the copper ore is stored in a warehouse, which has a capacity of more than 80,000 tons. A conveyor system conveys the material from the mainland and transfers it to the new SL1320.51/30 ship loader. The loader has a swiveling superstructure. At the end of the boom is the loading device with a belt conveyor. The material slides down a telescopic tube into the cargo hold. This means that there are no major environmental emissions during loading. The telescopic tube can be swiveled hydraulically to reach every corner of the cargo hold. The ship loader has a conveying capacity of around 1,320 tons per hour.
FAM successfully commissioned the system at the end of 2022. The supplier also handled the installation of all the mechanical components, as well as the electrical and control engineering, project planning, production, transportation and consulting.
FAM Project leader Alexander Kammerer: “This project was challenging in many ways. We had to deal with both high seismic loads and COVID 19 pandemic delays. But thanks to the support of our colleagues from FAM América Latina Maquinarias Limitada in Chile, we succeeded in implementing the project within the given parameters.”