Its Pizza Time!
In industrial pizza production, the Vortex® Fill Pass Diverter™ enhances ingredient management, especially flour, in pneumatic conveying systems. It supports seamless transport of flour to processing points with a design that reduces seal wear and preserves flour integrity, crucial for maintaining dough quality.
The Diverter accurately scales flour into hoppers, essential for adhering to recipe proportions for different pizzas. It accommodates diverse pizza styles efficiently without compromising quality. Constructed from FDA-compliant materials, it ensures hygiene and safety, critical in pizza production.
The device’s integration into systems for different materials supports the blending of various flours and ingredients, enabling customized dough recipes. The Vortex Fill Pass Diverter combines tradition and technology in pizza production, ensuring efficiency and quality, and meeting diverse recipe specifications. Its precise control over flour handling not only streamlines production but also enhances pizza quality, maintaining its global popularity.
Vortex Equipment Technical Details
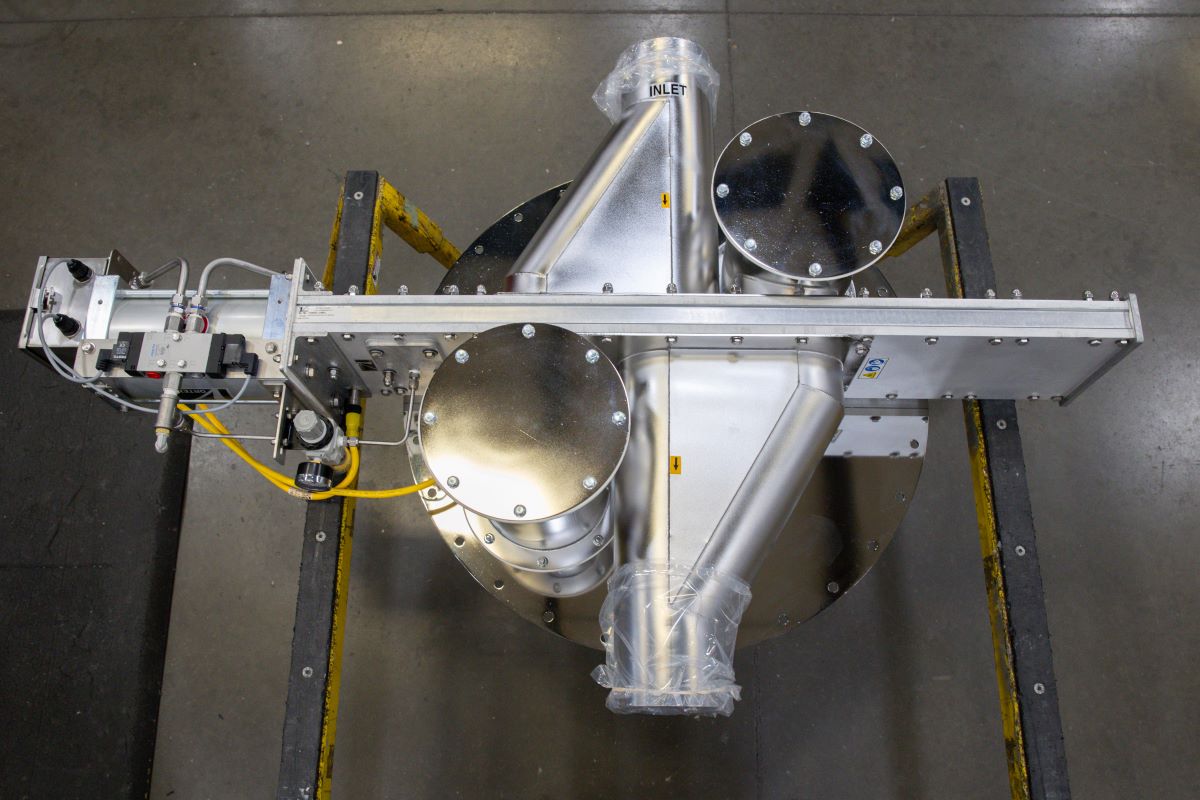
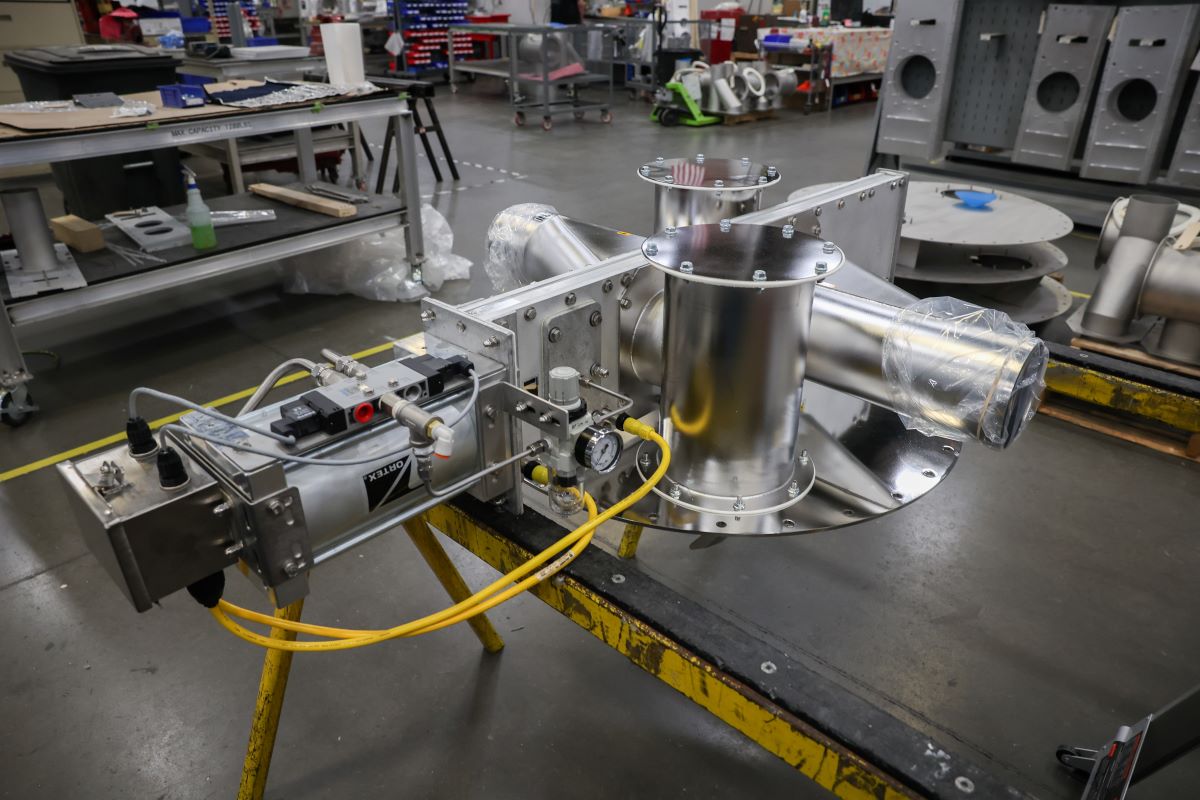
Vortex Model No. D63-8SSHS-MG-SM1-PX-E83230
- 6″ Â Fill-Pass Diverter Valve. Â
- Aluminum frame, main flanges, and safety covers. Â
- Live loaded, wear compensating seals with a 304 stainless steel blade. Â
- Inlet and outlet weldments are constructed from 304 stainless steel. Â
- Sealed body cavity allows for addition of air purge assembly (sold separately). Â
- Material contact is 304 stainless steel and polymer.
- Double acting air cylinder actuator
- (HS) – Hopper Stackable mounting flange. Â Can be used in conjunction with Stackable Flange models for multiple conveying lines. Â Hopper Stackable models use large stack sizes and spread inlet / outlet stacks for superior air / material separation with minimal carryover.
- (MG) – Air cylinder is equipped with a magno-piston for use with magnetic reed position indication switches.
- (SM1) – Valve is rated for 180ËšF(82ËšC) maximum continuous service. Â PET pressure plates are backed with a foam void filler and live loaded natural rubber load seals. Â Valve blade is electropolished to handle sticky materials, outdoor service, and washdown conditions.
- (PX) – Valve has boss welded into main body to accept proximity switches (required when purchasing inductive proximity switches)
- Engineering Specification (E83230) – RA36 FINSH FOR PRODUCT CONTACT SURFACES. Â NON-PRODUCT CONTACT STAINLESS STEEL SURFACES TO BE ELECTRO-POLISHED.