As with most drying production lines, there are a multitude of flexible connectors between different parts of the process machinery, and HOCHDORF Sulgen were using traditional cloth, plastic and rubber hoses, fixed with hose clamps.
Their production lines were experiencing problems with milk powder leakage around the clamped connections, as well as issues with the sharp-edged hose clamps leaving small cracks or holes in the flexible hoses. The dust leakage and residue build-up were also a hygiene concern.
Frequent connector changes were required due to the damage caused by the hose clamps, and this, in addition to their regular CIP (Clean-in-Place) operations, meant staff were often risking injury from both the clamps themselves and slipping screwdrivers when manipulating them during replacement.
The time required for these replacements, and constant product leakage clean-ups meant valuable production time was being lost.
The Production Manager for Babycare at the Sulgen plant was keen to look at an alternative solution as part of HOCHDORF’s continuous improvement and were excited about the possible applications for the BFM® fitting within the plant, particularly to reduce dust emissions and improve internal handling.
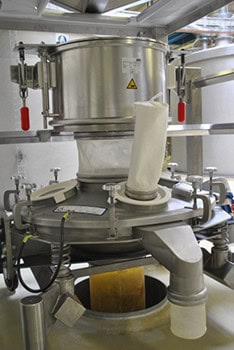
The main challenge was the huge variety of connection sizes within the plant and they needed help to work out the best connector for each location, and the right installation gap to leave between each set of BFM® spigots.

BFM® fitting’s Swiss representative, Swissfilter AG, worked with the team at HOCHDORF to carefully measure and plan out the installations throughout the plant.
After an initial trial, HOCHDORF were extremely happy with the transparent BFM® fitting system. Dust emissions at the connections were completely eliminated, improving overall hygiene throughout the plant. The BFM® connectors could easily and safely be installed and removed with little machine downtime and without tools, making CIP (clean-in-place) and changeouts much faster and more efficient.
In fact, the team at HOCHDORF were so impressed with the BFM® fitting system that they made the decision to begin replacing all of their existing connectors throughout the plant. The first step was the complete conversion of the initial spray tower line, involving over 60 connectors.
The remaining connectors are being replaced as part of their regular maintenance program, and in the first quarter of 2018, HOCHDORF commissioned an additional brand-new spray tower line, equipped with BFM® connectors right from the start.
The BFM® connector solution has enabled dust-free production at the Sulgen plant, ensuring the highest hygienic standards and therefore improved product quality. The connectors also enjoy a very high level of acceptance among employees because they are so easy to use and have significantly reduced risk of injury.
The team at HOCHDORF are also impressed with the clean, professional presentation of the BFM® connectors. When they have site visits, the plant now looks so immaculate and professional, it helps create trust with their customers and supports the marketing of their products.
HOCHDORF’S Production Manager said: ’’With the unique product features of the flexible BFM® connectors I achieve perfect hygiene in production and high employee satisfaction. I’m a true BFM® fan!”