This helps protect the integrity of the product itself for end-user safety, as well as safeguards the health and safety of production workers.
Hygiene is Imperative For Pharma Manufacturing
Whether it’s the production of the primary active pharmaceutical ingredients (APIs) or the binders used in the final end product, to comply with international regulations and standards, the entire pharmaceutical manufacturing process must adhere to the highest protocols in terms of hygiene.
Hygienic design of production equipment – including the flexible connectors that link all of the process machinery together – is essential for pharmaceutical manufacturers.
Staff Safety In Pharmaceutical Processing
Working with the chemicals involved in pharmaceutical manufacturing can be relatively high risk for staff on the factory floor. APIs, for example, are the components in drugs and medicines that are designed to produce biological change in the human body. Prolonged exposure, therefore, can have serious consequences.
The protection of workers from the potential harmful effects of APIs poses a significant challenge for the pharmaceutical industry and it’s imperative that everything is done to reduce possible exposure to these chemicals.
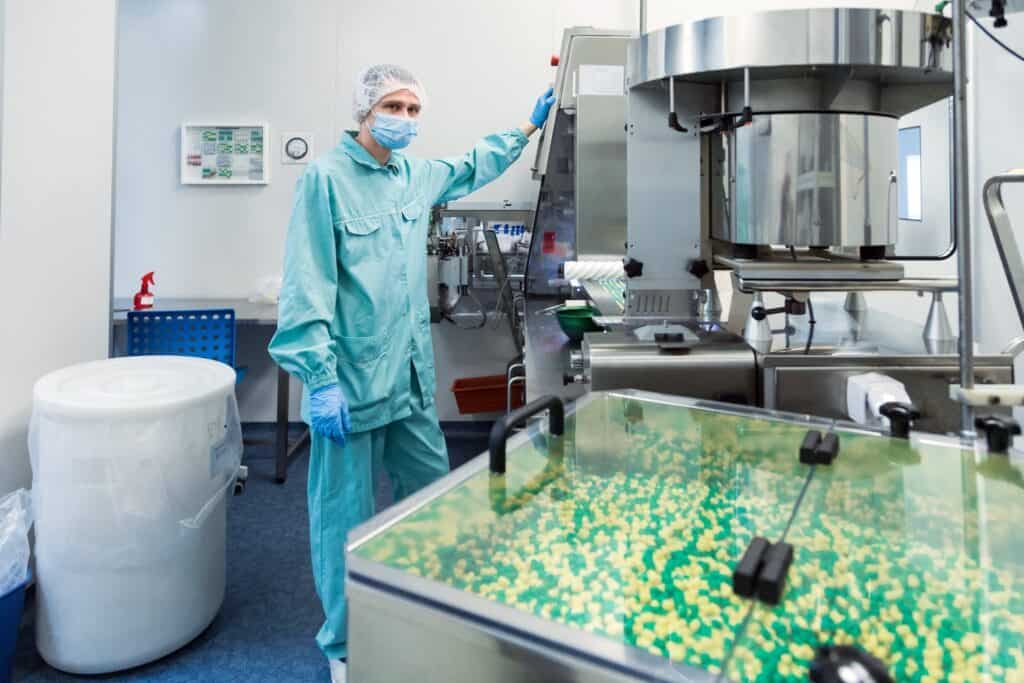
Personal protection equipment (PPE) is of course essential, but pharmaceutical manufacturers must design their entire process systems with the best possible quality equipment that can be relied upon to provide 100% leak-free product transfer process.
The less product that can escape into the plant environment in the first place the less the possible potential exposure for staff.
Keeping Valuable Products Inside The Process
Pharmaceutical ingredients are usually relatively high-value products, so ensuring there is no product wastage or potential contamination is important for maximum efficiency.
Many pharma processes are undertaken in ‘cleanrooms’ which require a fully controlled environment to reduce the chance of any airborne microbes, dust or aerosol particles.
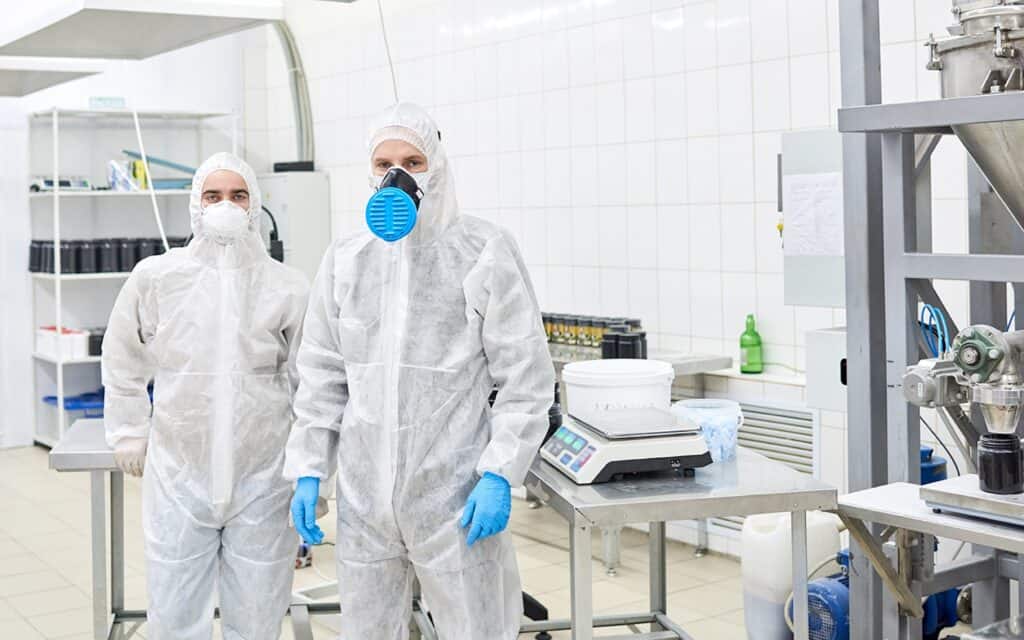
The transition points between equipment, particularly if one is moving such as a sieve or sifter, are the most common locations for problems with powder leakage that can compromise cleanroom environments.
Fine powders like those often used in pharmaceutical manufacturing can be hard to contain, so a quality, 100% sealed flexible connection system is imperative.
Choosing a Quality Connector System for Safety, Hygiene and Efficiency
Maintaining the integrity of the product while ensuring efficiency and regulatory health and safety compliance is crucial. Flexible connector systems, serve as essential components for transferring materials between processing equipment.
Here are five crucial factors pharmaceutical manufacturers should consider when selecting a flexible connector system.
- Hygienic Design & Cleanability: Contamination risks are a top concern in pharmaceutical manufacturing. Hygienic design features, such as smooth internal surfaces, minimize the risk of bacterial growth and make the connectors easier to clean. The ability for use in conjunction with CIP/SIP should be considered, as well as how easy they are to disassemble and reassemble for manual removal of any residual cleaning chemicals.
- Dust Tightness: Clamped connectors, often used in the production of binding agents, are notorious for leaking and causing significant contamination issues and health and safety concerns for operators. A flexible connector system needs to be able to provide a 100% sealed system that guarantees zero leaks, essential for operating under both positive and negative pressure.
- Durability & Pressure Resistance: In pharmaceutical plants, flexible connectors need to be removed and replaced frequently for cleaning. They also need to be able to perform under pressure and movement without cracking or tearing. Durability against wear and tear from continuous operations under pressure and frequent removal should be a top priority.
- Ease of Installation & Maintenance: The cost of ongoing maintenance and production downtime due to failure or time for replacement after cleaning is a significant consideration. Systems that are durable, fast to fit and require minimal maintenance provide long-term savings and enhance operational efficiency. Choose connectors that are easy to install and maintain, reducing labour costs.
- Regulatory Compliance: Pharmaceutical manufacturers must adhere to strict regulatory guidelines set by agencies like the FDA. Flexible connectors used in drug manufacturing must also meet material traceability, testing, and documentation requirements to ensure product safety and efficacy. Seek reputable suppliers who can provide documentation for regulatory inspections.
Selecting the right flexible connector system is a critical decision for pharmaceutical manufacturers.
The Connector System Used by 90% of the World’s Biggest Pharma Companies
The BFM® fitting system is recognized worldwide as the connector solution for reliable, safe, hygienic pharmaceutical processes. So why are our products chosen by over 90% of the world’s biggest pharmaceutical manufacturing companies.? Here’s just a few of the key reasons:
Hygienic Crevice-Free Design: The BFM® snap-in connector and spigot adaptor provide a smooth internal, crevice-free system with no gaps, reducing the risk of contamination. This design also aids flushing during cleaning. It makes BFM® highly suitable for hygienic applications like pharmaceutical manufacturing where cleanliness and avoiding material buildup are critical.
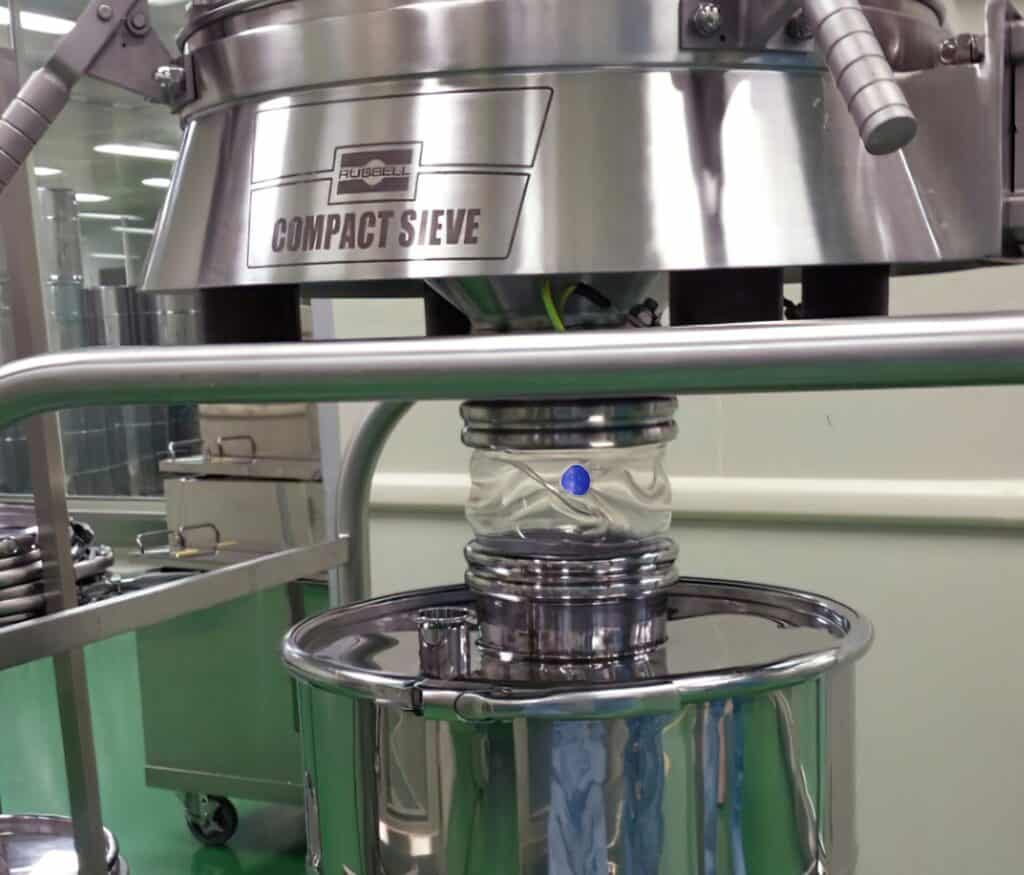
100% Leak Free Seal: The specially shaped ‘cuff’ on the ends of a BFM® fitting connector snap-fit exactly inside the corresponding shaped ridges on the BFM® spigot adaptor, and the outward pressure of the snap-band inside the cuff creates the perfect 100% seal. Because it seals from the inside, product leakage and blow-outs are eliminated.
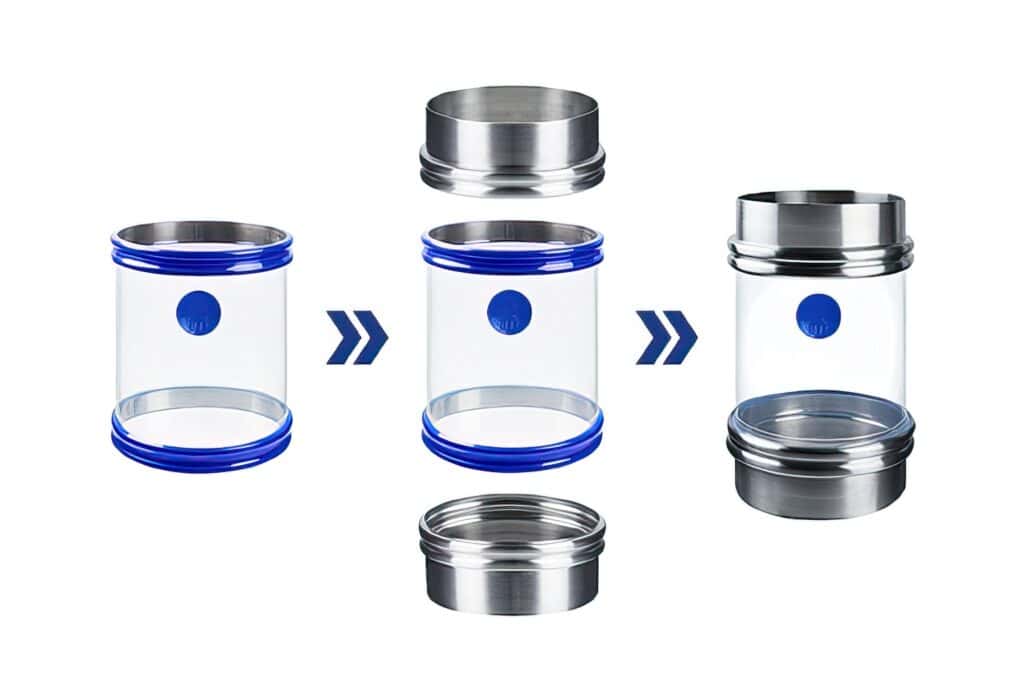
Durable Materials: The flexible connector materials used in BFM® fittings, such as our proprietary Seeflex materials, offer superior durability and strength while providing visibility of the material being transferred. The BFM® range of connector material also includes pure PTFE connectors (our Teflex products) which can be used across the entire pH scale to very high temperatures, making them ideal for use with harsh cleaning chemicals often required in the pharmaceutical industry.
Quick Installation and Removal: The fast and easy snap-fit design allows for rapid changeovers, minimizing downtime. A BFM® fitting connector can be removed and replaced in well under 30 seconds without the need for tools or specialised skills, reducing the risk of operator error in refitting the connector incorrectly. This is particularly beneficial in industries where batch processing and frequent cleaning are required, such as pharmaceutical production.
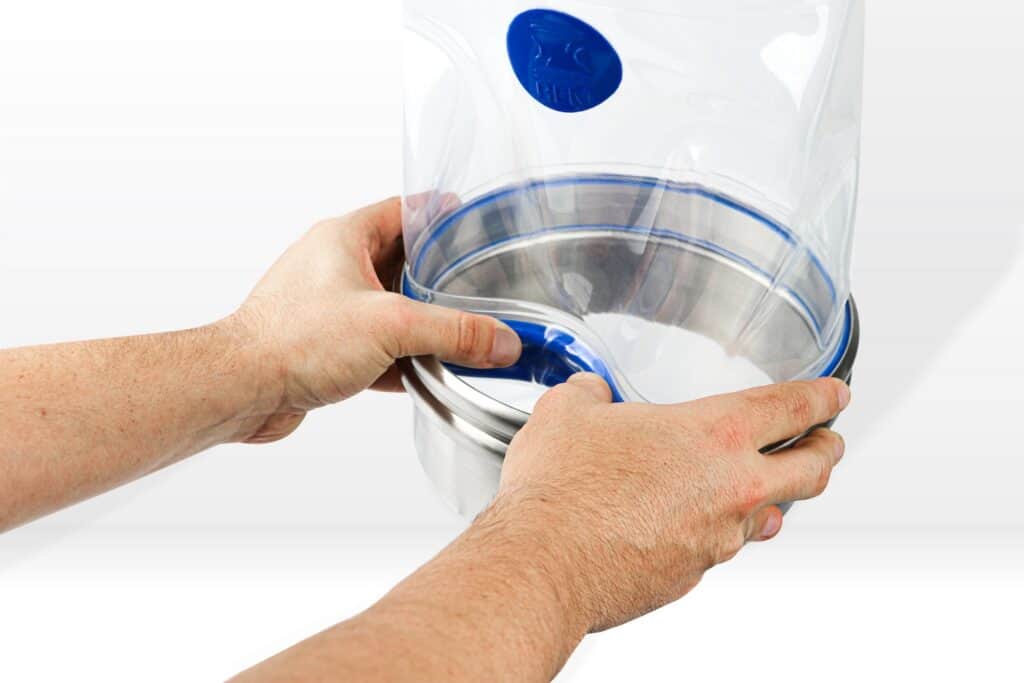
Regulatory Compliance: BFM® fittings are made from FDA-compliant materials and are rigorously tested to meet international standards like ATEX for use in pharmaceutical manufacturing. Our products have also assisted major pharmaceutical manufacturers achieve their OEL compliance requirements.
BFM® fittings combine hygienic design, ease of use, and robust performance to help pharmaceutical manufacturers operate a safe, efficient production process that meets stringent regulatory requirements.
If you manage a pharmaceutical processing operation that has challenges issues with hygiene, safety or efficiency because of your flexible connections, take a look at the BFM® fitting difference today.