Powder leakage most commonly occurs where the product transitions between equipment via a flexible connector. This is often due to clamp failure, poor quality connector material, design, fitment – or all of the above!
In addition to the serious explosion risk this poses, downtime for repairs and clean-ups, as well as loss of product, can be costly in the long run.
But what about flexible connectors used in non-powder processing applications – are high quality, well-sealed connectors really that important? The answer is yes and for a variety of reasons!
Movement of Any Dry Bulk Product Creates Dust Danger
When rocessing any dry bulk product, dust and electrostatic charge will still be produced, even if the product itself isn’t in powder form. Whether it’s grains, plastic granules or coffee beans, the simple act of the bulk movement of a ‘dry’ material through equipment – particularly at non-metallic transitions – can generate enough charge to be a potential spark discharge risk.
Movement of dry material in large volumes will also naturally create a certain volume of dust, which can in turn leak out of the process line and settle on surfaces outside of the equipment, creating a secondary explosion risk.
So, no matter what the product form, every dry bulk processing line needs a flexible connector system that will provide a 100% dust-tight seal, as well as help effectively dissipate electrostatic build-up.
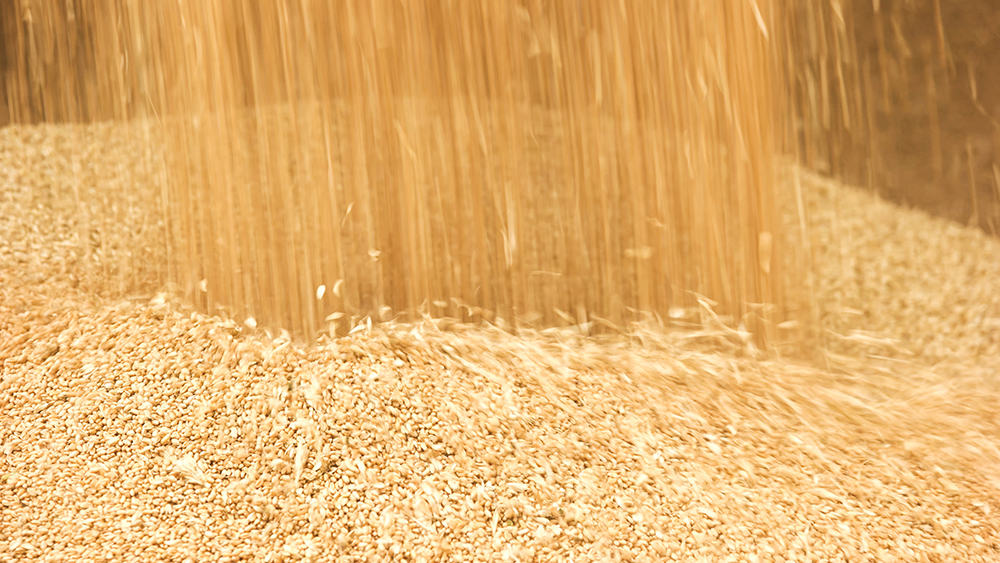
Wet Applications – Leaks and Pressure a Challenge
Whether it’s in a liquid, slurry or paste form, transporting bulk product in a ‘wet’ form presents its own challenges, but preventing leaks is still naturally at the top of the list.
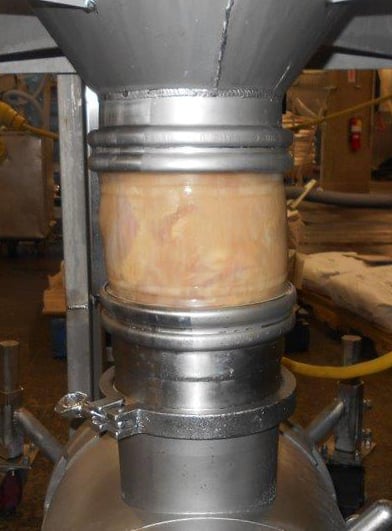
The product’s viscosity is the key here – if the material being transported is of lower viscosity, for example, the likelihood of it seeping out through any flexible connector is higher, so the better the seal design of your flexibles, the cleaner and more efficient your whole process will be.
To help prevent leakage, many ‘wet’ products are transported via negative/vacuum pressure and therefore a fully sealed system is needed to maintain optimal product flow. If air is sucked into the system at any point via the flexible connectors, it will naturally reduce the vacuum pressure and therefore the product flow volume drops, reducing efficiency.
Clean-in-place (CIP) applications are commonplace for many food processors, where water and cleaning chemicals are flushed through a process line periodically at high volume for short periods. While this is slightly different from constantly processing liquids, quality flexible connector seals and the ability to withstand high head pressure in these instances are extremely important.
Abrasive Products Need Durable Flexible Connector Materials
The physical characteristics of non-powdered dry products processed in bulk can vary greatly – from grains of rice and wood chips to microbeads and cereal flakes – and so too does the amount of wear that these products can impart on flexible connectors. Whilst steel equipment and piping can handle significant abrasion inflicted by the high-volume flow of these products, any non-metallic transition points – like flexible connections – need to be particularly durable.
Design considerations to minimise the amount of product contact with the wall of flexible connectors should also be applied wherever possible to help reduce wear. This can be done by ‘flow correction’ methods where a slight adjustment to the inlet pipe design can direct the flow of product inwards rather than outwards or at an angle. This is particularly important for high velocity flow or high temperature/high abrasion products, like roasted coffee beans, sand, or plastic chips.
What is the Best Flexible Connector System for Non-Powder Applications?
The BFM® fitting system is best known for containing powders, but its adaptability to handling non-powdered products like granules, cereals, slurries, and pastes is also well-proven.
Engineered with precision and crafted from high-quality materials, BFM® fittings are designed to withstand the rigours of industrial environments. The unique design of the snap-fit connectors and specially shaped spigots ensures a superior seal for both dry and wet applications. The materials utilized in BFM® fittings are carefully selected for their resilience, offering exceptional resistance to abrasion and UV degradation.
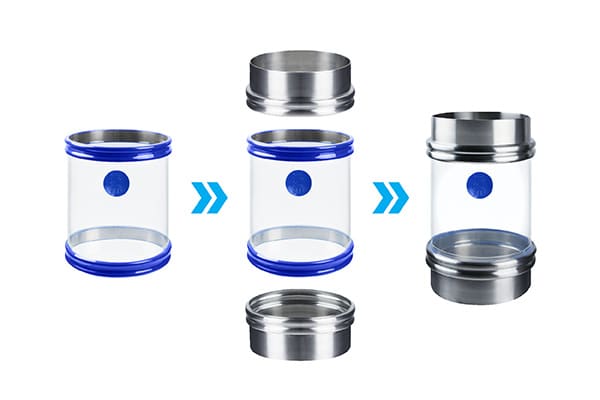
Seeflex 040E, a specially formulated ether-based polyurethane, is the most widely used connector material in the BFM® fitting range and is renowned for its strength, flexibility, and resistance to environmental stressors. This proprietary material is highly abrasion resistant, maintaining its integrity over prolonged use and ensuring long-term reliability in demanding applications.
Real-World Success Stories Testament to BFM® fitting’s Versatility
The efficacy and durability of the BFM® fitting system in non-powder applications have been demonstrated in real-world applications across diverse industries for many years.
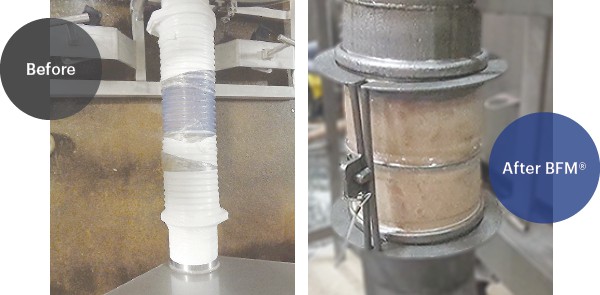
USA chicken processing giant Tyson Foods Inc., for example, adopted BFM® fittings in their Berryville plant and revolutionized the efficiency of their production line. The plant used a high-pressure vacuum conveying system to transport chicken slurry throughout the process line and had problems with leakage using their existing connectors. The lack of a 100% seal was not only a hygiene issue but the vacuum pressure required for efficient product flow couldn’t be maintained.
Staff had resorted to taping the connections to stop the leaks – but a legal hygiene requirement of full system dismantling and cleaning every 12 hours created a considerable labour cost burden due to the time involved in removing and refitting the taped connectors.
By changing the flexible connectors to BFM® fitting Seeflex 040E snap-fit connectors, they now have a 100% sealed system which maintains the vacuum pressure to allow a higher volume of product to be processed. The removal and replacement of connectors during each cleaning cycle now happens in a matter of minutes and has reduced their cleaning costs by 90%.
BFM® fitting blue band connectors are being used all around the world on a daily basis in non-powder applications, processing products like liquid chocolate, cereals, biowaste slurry, wood chips, blood plasma and freeze-dried coffee to name just a few. For more information on the better-performing, versatile and durable BFM® fitting system, visit