The bottleneck and the seven types of waste
In all plants, there is always a bottleneck – a bottleneck that limits production capacity. Most companies are aware of this bottleneck, but are you aware of the other seven types of waste? These are:
- Overproduction
- Waiting times
- Transports
- Reworking
- Stocks
- Movements
- Errors and rework
These wastes need to be identified and eliminated in order to maximize productivity. A retrofit offers the perfect opportunity to identify and eliminate these inefficiencies.
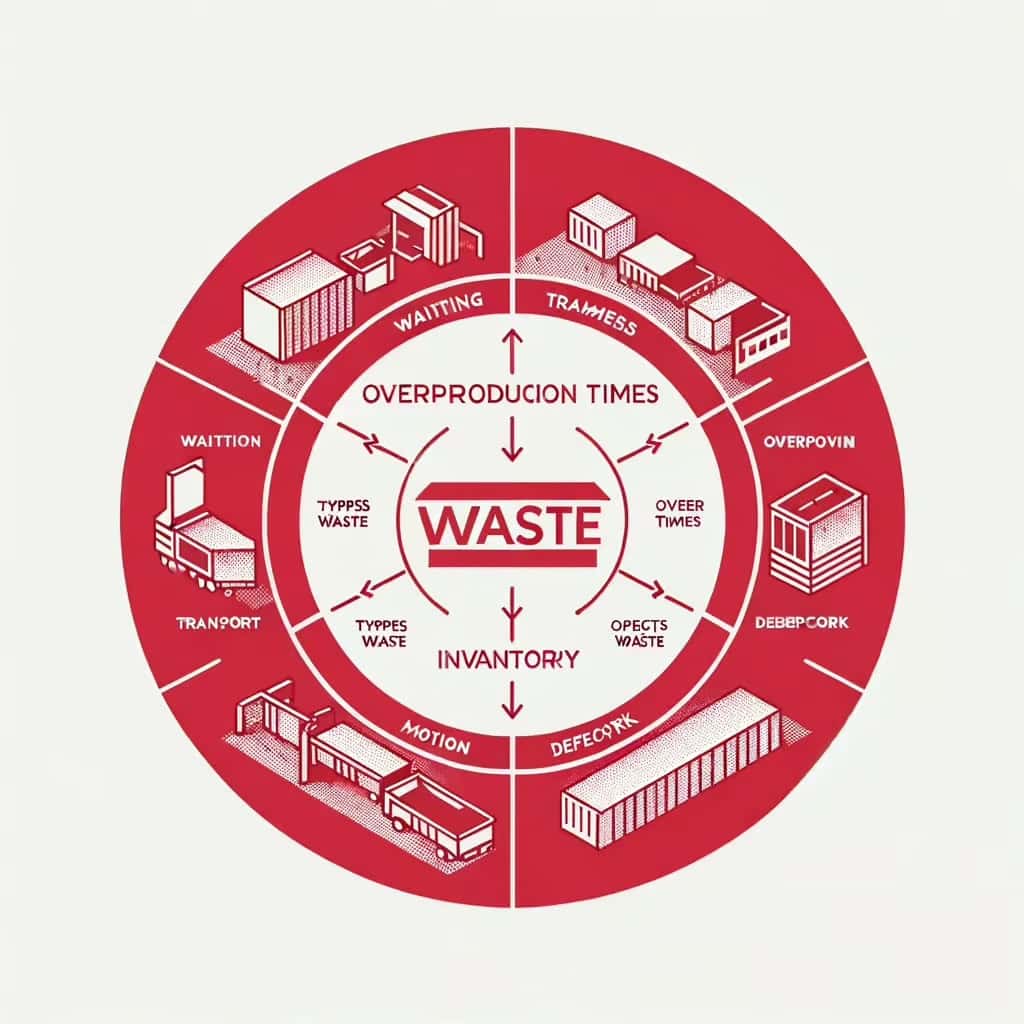
Use of the digital twin
By using the digital twin, order data and recipe data can be optimally matched to the prevailing conditions. This ensures maximum productivity and transparency at all times. By dividing the systems in the value stream into assets and creating a digital twin for each asset, we create the necessary transparency at all times to sustainably improve productivity.
Interdisciplinary collaboration and mindfulness
We achieve this on an interdisciplinary basis by ensuring that everyone involved has access to all relevant data in the value stream. This promotes cooperation between all departments and creates the basis for streamlining organizations without introducing more bureaucracy, but finding solutions as a team. An example from the plastics industry shows how raw material handling can be optimized in a heating/cooling mixer combination so that up to five orders can be processed fully automatically at the same time. This not only significantly reduces the workload for employees, but also creates transparency right through to the end product.
An often overlooked but significant benefit of the Digital Twin is the promotion of mindfulness in the industry. Through real-time monitoring and detailed data collection, companies can:
Advantages of retrofitting in raw materials handling
- Increase in productivity: By modernizing their control systems and using the digital twin, companies can significantly increase their production capacities.
- Reduction of waste: Identifying and eliminating the seven types of waste leads to more efficient processes and lower operating costs.
- Transparency and control: The digital twin enables seamless monitoring and optimization of production processes in real time.
- Relief for employees: Automated processes reduce manual effort and allow employees to concentrate on value-adding activities.
- Sustainability: Optimized processes and reduced waste contribute to more sustainable production.
- Promotion of cooperation: The digital twin promotes collaboration between all departments and creates the basis for streamlining organizations without introducing more bureaucracy, but finding solutions as a team.
- Introduction of AI: The foundation and the collected data enable the integration of AI for further optimizations and online controls, leading to continuous improvements day by day.
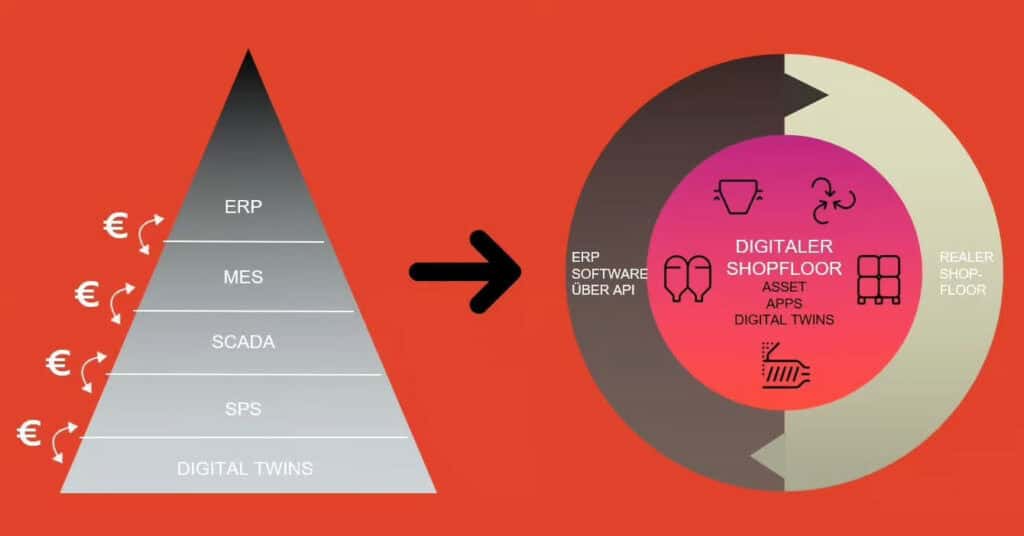
Integration into the value stream and raw material handling
The digital twin and the digital product passport offer enormous advantages in the value stream and raw material handling. They make it possible to monitor and optimize all steps from the receipt of raw materials through production to delivery. By integrating them into the value stream, companies can:
- Identify and eliminate bottlenecks: Real-time data enables precise monitoring of production processes, allowing bottlenecks to be quickly identified and rectified.
- Continuously improve processes: By analyzing the collected data, companies can continuously optimize and adapt their processes to increase efficiency and productivity.
- Making sustainable decisions: Transparent and consistent data along the value stream and in raw material handling support sustainable decisions and help to minimize the ecological footprint.
Mindfulness and collaborative working
An often overlooked but significant benefit of the Digital Twin is the promotion of mindfulness in the industry. Through real-time monitoring and detailed data collection, companies can:
- Mindfulness of people: The health and safety of employees can be improved through precise monitoring and early warnings of potential hazards.
- Mindfulness on machines: Machines can be operated more efficiently and their service life extended through continuous monitoring and preventive maintenance.
- Mindfulness of products: Products can be manufactured to the highest quality and their production processes made transparent, which leads to greater customer confidence.
- Mindfulness of systems: Overall systems can be optimized and harmonized to ensure a smooth production process.
In addition, the digital twin supports collaborative working by providing a platform for exchange and cooperation. This enables different departments and partners to work together more efficiently and develop innovative solutions together.
Conclusion
A retrofit offers an excellent opportunity to significantly increase productivity and efficiency in raw materials handling. By replacing the control systems and using the digital twin, companies can optimize their processes, eliminate waste and achieve sustainable competitive advantages. Interdisciplinary collaboration and comprehensive transparency in the value stream create the basis for continuous improvement and maximum productivity. The digital twin also promotes awareness of people, machines, products and systems and improves collaborative working.
Stay tuned for more exciting insights and success stories from the world of Industry 4.0 and automation. Let’s shape the future of production together!