In the pursuit of greater economy, sometimes more really can be less.
Conveyor belt technology has advanced enormously in recent years. Conveyor operators should therefore rightly expect considerably longer operational lifetimes compared to what was acceptable as recently as five or ten years ago. However, the fact is that most operators continue to repair and replace belts much more frequently than they should need to. The good news is that it can be surprisingly easy to achieve significant reductions, both in the frequency of belt replacement as well as belt repairs and maintenance simply by being aware of commonplace deceptions and misconceptions.
What is the TRUE cost of a conveyor belt?
Although sales people will always maintain that making a choice based on price rather than the quality of the product is not the best way to make a decision, the fact remains that price is important because conveyor belts are costly items. The reality is that price will almost invariably be the number one factor in the selection criteria.
Conveyors play a vital role and have to cope with demanding environments and materials and it is the conveyor belts themselves that are invariably the most vulnerable component. Their durability and reliability are therefore critical factors, both in terms of productivity and in budgetary management. Despite this, the preoccupation still seems to be the price of the belt rather than its ‘whole life cost’. This almost invariably means buying low-priced belts, the vast majority of which originate from Asia.
Price is very rarely an accurate measure of ultimate cost.
When visiting ports and terminals I have often found myself shaking my head in disbelief when I come across buyers of conveyor belts who are absolutely convinced that they are getting a good deal because the price they are paying can be as much as 30% (or more) lower than the more well established ‘premium quality’ brands. The fact that they will almost certainly have to buy at least two and quite possibly three ‘economy’ belts instead of one, good quality harder-wearing belt ‘expensive’ belt over the same period seems to be ignored.
The true economic value of a conveyor belt can only be properly established by calculating the ‘whole life’ cost. This is simply achieved by adding the price paid to other known associated costs such as fitting, repairs and maintenance. Lost production time is another important cost to factor in. The total is then divided by either the actual (or anticipated) operational lifetime (measured in either weeks, months, years or running hours) or alternatively by the tonnage carried. In my experience it is surprisingly rare to find a conveyor operator who makes such calculations. It may be hard to believe but some do not even keep records of when old belts are replaced with new ones.
Why the difference?
Perhaps the question I am most often asked is how there can be such huge differences in price between one belt supplier/manufacturer and another for belts of apparently the exact same specification. There are two equally valid answers to that question. The first lies in the cost make-up of producing a conveyor belt. The second is the actual quality of the belt including the kind of trickery and deception that many manufacturers and suppliers use nowadays to create the illusion of quality.
The cost of producing a conveyor belt
There can never be a fixed formula due to the wide variety of individual belt specifications but the influence of raw material costs on the selling price is hugely significant. As a general ‘rule of thumb’, raw materials constitute some 70% of the total cost of producing a conveyor belt. The general overheads element is generally around 10%. Thanks to the high level of automation, the actual labour cost element is very low. You are unlikely to see more than three or four people operating a typical production line. This last fact certainly shoots down the usual assumption that belts imported from Asia are lower priced because their labour costs are much lower than those in Europe.
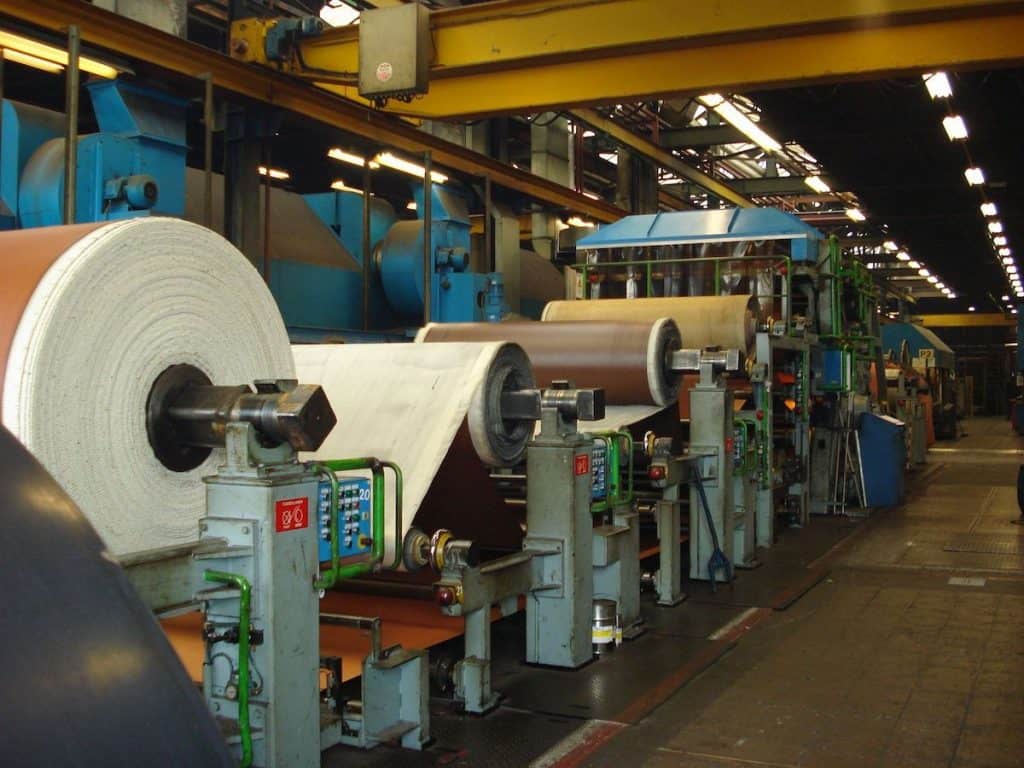
When faced with a huge difference in price and the fact that raw materials make up the vast bulk of the total manufacturing cost, it is perfectly reasonable to conclude that materials of a lower quality have been used to achieve that difference. For example, the pressure to keep costs to an absolute minimum means that recycled rubber of highly questionable origin may well have been used in the mix. Another cost-saving method is to use cheap ‘bulking’ fillers to replace part of the rubber polymers in the rubber compound.
The tell-tale signs to look for when evaluating quality can be broken down to the two main constituent parts of a conveyor belt, which is the carcass and the rubber covers used to protect that carcass.
The carcass
The type of belt most commonly used for transhipment is rubber ‘multi-ply’ with a polyester/nylon (EP) fabric reinforced carcass protected by an outer cover of rubber. It is the carcass that provides the inherent characteristics of a conveyor belt such as its tensile strength and elongation (elasticity or ‘stretch’ under tension).
Although the belts being offered may state the same specification, there can be huge differences in the actual quality of the fabric plies. In low quality (low cost) fabrics, although the amount of material used in the longitudinal strands (warp) of the fabric may be adequate, the amount of transversal (weft) material is kept to an absolute minimum in order to reduce cost. Although the required tensile strength is achieved, albeit with a low safety factor, rip and tear resistance is reduced and elongation (stretch) is low.
Low elongation may not sound overly important but if the elongation is too low then this can cause a number of problems including a general inability to accommodate the contours of the conveyor and its drums and pulleys. This can quite easily lead to the premature failure of the belt.
What to watch out for
A method of cost (price) cutting that is now becoming an increasingly common practice is the use of totally polyester (EE) fabric plies in a carcass that is declared as having an EP carcass (polyester/nylon mix) construction. The reason for this deception is that the cost of EE fabric is some 30% lower than the cost of EP fabric. This helps the seller to achieve the perception of a lower ‘like for like’ price. This may sound relatively harmless but the seriousness of the physical effects are huge. The biggest danger is that a polyester weft can cause low transverse elasticity, which reduces both the troughability and impact resistance of the belt and consequently also causes tracking issues. In addition, less weft in the belt can also reduce rip resistance, fastener strength and ability to handle small pulley sizes.
The covers
As the rubber used for the outer covers is the single biggest element of cost when manufacturing a conveyor belt it is consequently the single biggest opportunity for manufacturers to economise. There are many different types of rubber compound used for rubber multi-ply belts because modern-day belts have to deal with a multitude of different (and often combined) demands. Most of the rubber used in conveyor belting is therefore synthetic.
There are literally hundreds of different chemical components and substances that are needed to create the synthetic rubber compounds that, once vulcanized, are able to meet the specific physical performance and safety requirements. For dry cargo handling, the four basic aspects that most determine the quality of performance are wear (abrasion) resistance; tear strength, oil resistance and ozone & UV resistance. The greatest influence on the operational lifetime of a conveyor belt comes from the level of abrasion resistance of the rubber.
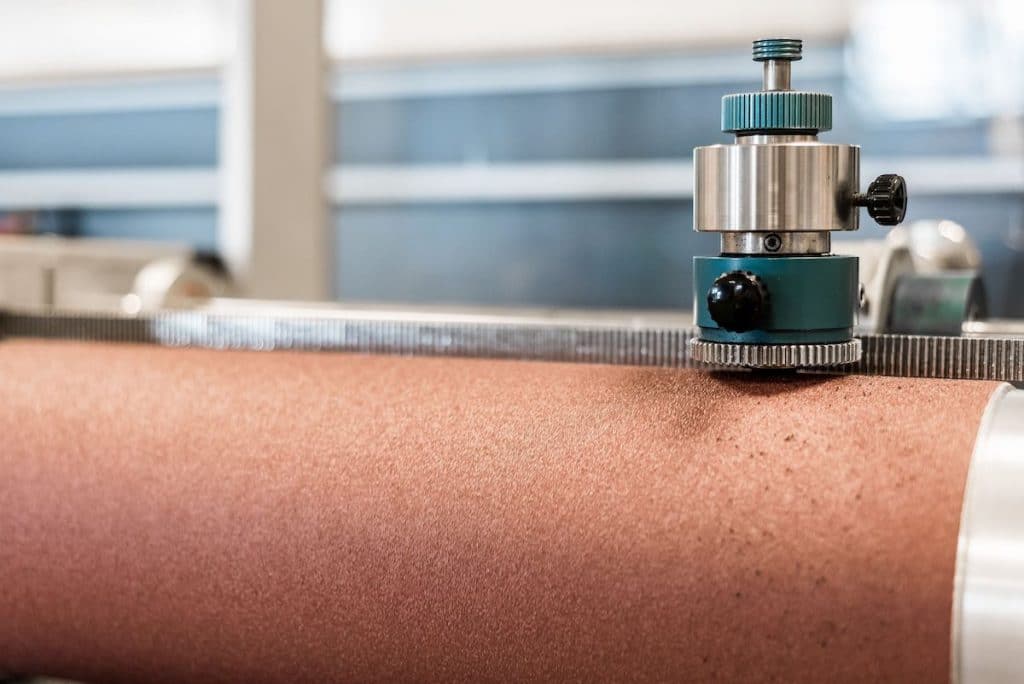
Abrasive wear testing
Abrasion resistance (ISO 4649 / DIN 53516) is measured by moving a test piece of rubber across the surface of an abrasive sheet mounted on a revolving drum. It is expressed as volume loss in cubic millimeters, for instance 150 mm³. The most important thing to remember when comparing abrasion test results (or promises!) is that higher figures represent a greater loss of surface rubber, which means that there is a lower resistance to abrasion. The lower the figure then the better the wear resistance. Comparing (evaluating) one offer from another is made very difficult by virtue of the fact that (with only one exception that I know of) the technical datasheets provided by manufacturers and traders almost invariably only show the minimum requirement of a particular test method or quality standard rather than the actual performance that the belt being offered would be expected to achieve.
In addition to checking the level of resistance to abrasion it is advisable to check the thickness of the rubber covers when the belt arrives on site. Apart from using the lowest grade rubber possible, another trick made the suppliers of ‘economy belting’ is to supply covers that can be up to 15% (or more) thinner than the promised specification. 1mm here or there may not sound much but it represents a huge cost saving to the manufacturer that they can reflect in the price. At the same time, it means 15% shorter wear life for the unfortunate end-user.
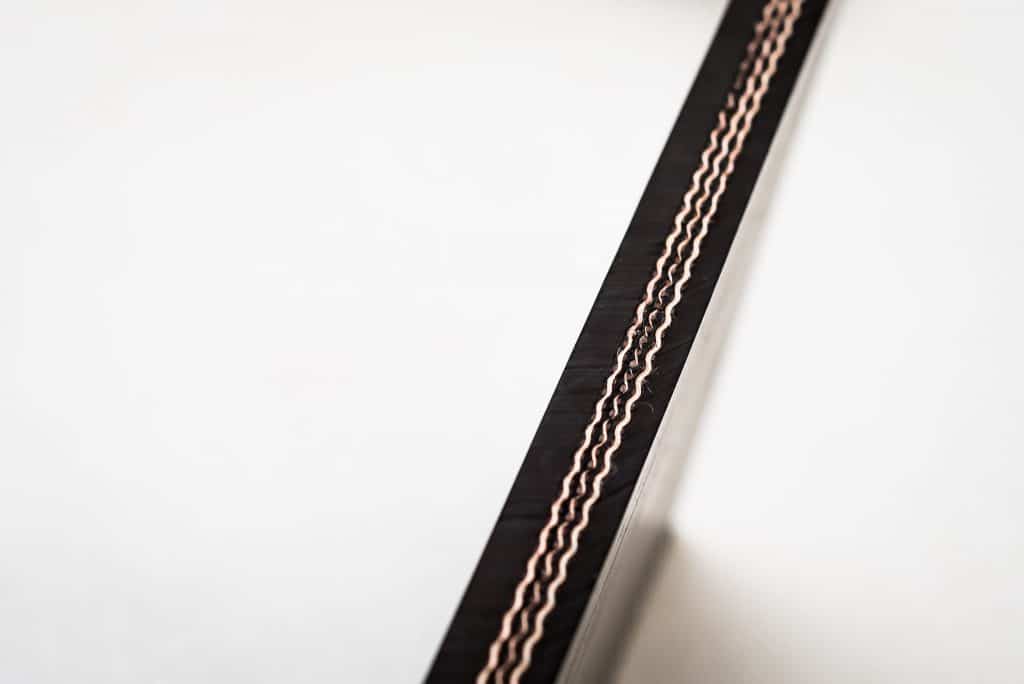
Oil resistance
Many bulk materials, especially grain and biomass, contain oils and resins; either mineral or vegetable/animal. When oil of any kind penetrates rubber it causes it to swell and distort. This results in serious tracking and steering problems, accelerated wear and ultimately premature replacement. There are two recognised test methods for oil resistance, both of which involve almost identical test procedures. These are ISO 1817 and the comparable, slightly less elaborate but equally tough American ASTM ‘D’ 1460.
When evaluating offers for oil resistant belting and looking at the respective quality standards, it is very important to bear in mind that many of the biggest manufacturers of belting in the world use the DIN reference number 22102 G when referring to oil resistant belting. This is very misleading because the letter ‘G’ is simply used to denote oil (or grease) resistant belting. DIN 22101 G does not actually contain any requirements, test methods or limits specific to oil resistant belting. This is a classic example of how the use of a test method reference number is designed to provide reassurance to the buyer but in reality is meaningless in terms of actual performance.
Ozone & UV qualities
There is absolutely no question that ALL rubber conveyor belts should be fully resistant to the damaging effects of ozone and ultra violet light. This is because at ground level ozone becomes a pollutant. Exposure increases the acidity of carbon black surfaces and causes reactions to take place within the molecular structure of the rubber. This has several consequences such as a surface cracking and a marked decrease in the tensile strength of the rubber. Likewise, ultraviolet light from sunlight and fluorescent lighting also accelerates deterioration because it produces photochemical reactions that that promote the oxidation of the surface of the rubber resulting in a loss in mechanical strength.
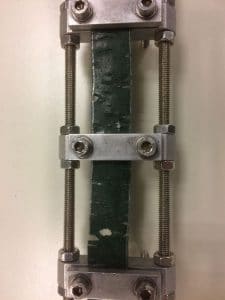
Rubber belts that are not fully resistant to ozone and UV can start to show signs of degradation before they have even been fitted to a conveyor. Despite its crucial importance, not least its huge influence on the working lifetime of a belt, ozone and UV resistance is very rarely, if ever, mentioned by traders or manufacturers. This is almost certainly because the anti-ozonants that need to be added during the mixing process to make the rubber compound resistant to ozone & ultra violet cost money and that, of course, makes the belt less competitive on price. My advice is to always make ozone & UV resistance a required part of the specification when selecting any rubber conveyor belt.
Safe to handle?
The pressure to compete on price has increasingly led to the use of potentially dangerous chemical substances to artificially accelerate the vulcanization process. When the European Union’s REACH (Registration, Evaluation and Authorisation of Chemical substances) regulation EC 1907/2006 came into force in June 2007 such concerns should have largely been dispelled. The regulations were introduced to improve the protection of human health and the environment from the risks that can be posed by chemicals. All European manufacturers are legally obliged to register the use of “substances of very high concern” (including those believed to cause various forms of cancer) that are listed within the regulations with ECHA (European Chemical Agency).
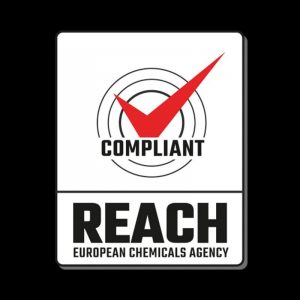
However, it is important to be aware that manufacturers located outside of EU member states are not subject to the regulations and are therefore free to use unregulated raw materials. However, those who import belts from outside the EU ARE responsible for the application of REACH regulation. Personally, I would always recommend asking for written confirmation from the belt manufacturer or supplier that the product they are offering will be produced in compliance with REACH EC 1907/2006 regulations.
CE Marking
Compliance with CE quality standards is increasingly being stipulated by purchasers of industrial conveyor belts. However, CE accreditation does not apply to conveyor belts because they are not a product category that is subject to specific directives that are required to be CE marked.
The letters “CE” used in the CE Marking are the abbreviation of French phrase “Conformité Européene” which literally means “European Conformity”. The term initially used was “EC Mark” but it was officially replaced by “CE Marking” in the Directive 93/68/EEC in 1993.
It is important to be aware of the fact that a very similar mark exists which many potential users may mistakenly believe is a genuine CE mark of European conformity. In reality it actually stands for “China Export”, meaning that the product was manufactured in China.
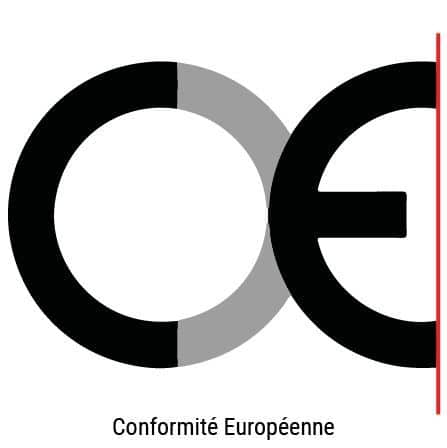
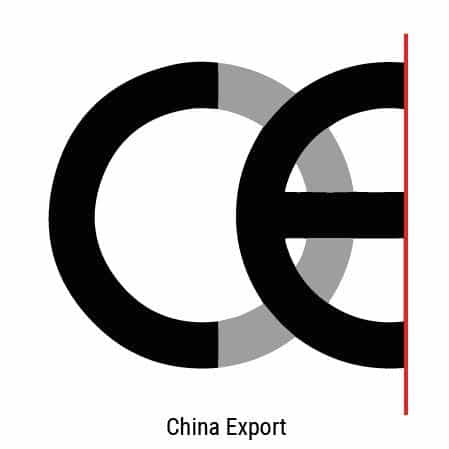
Be sure of what you are buying
A fast-growing and very significant proportion of belting sold in Europe is imported from South East Asia by traders. This is not to say that all belting imported from Asia is substandard because that is not the case. However, random laboratory test of imported belt continues to consistently reveal serious and quite worrying shortcomings.
One such test on a basic abrasion resistant belt revealed that the tensile strength of the carcass was more than 20% below the specified minimum. It was also discovered that the abrasion resistance of the covers was 47% over the DIN Y maximum standard of 150 Mm3. To make matters even worse, ISO 1431 testing showed that the rubber had virtually no resistance to ozone and began to crack within 6 hours of exposure. Another set of tests on a fire resistant belt revealed that the 6mm specification of the top cover thickness actually measured only 4mm.
Even more seriously, the belt had a totally inadequate level of fire resistance. In the ISO 340 test the duration of continued burning (visible flame) should be less than 15 seconds for each sample with a maximum cumulative duration of 45 seconds for each group of six test samples. The total time that the six Chinese belt sample test pieces took to self-extinguish was 102 seconds.
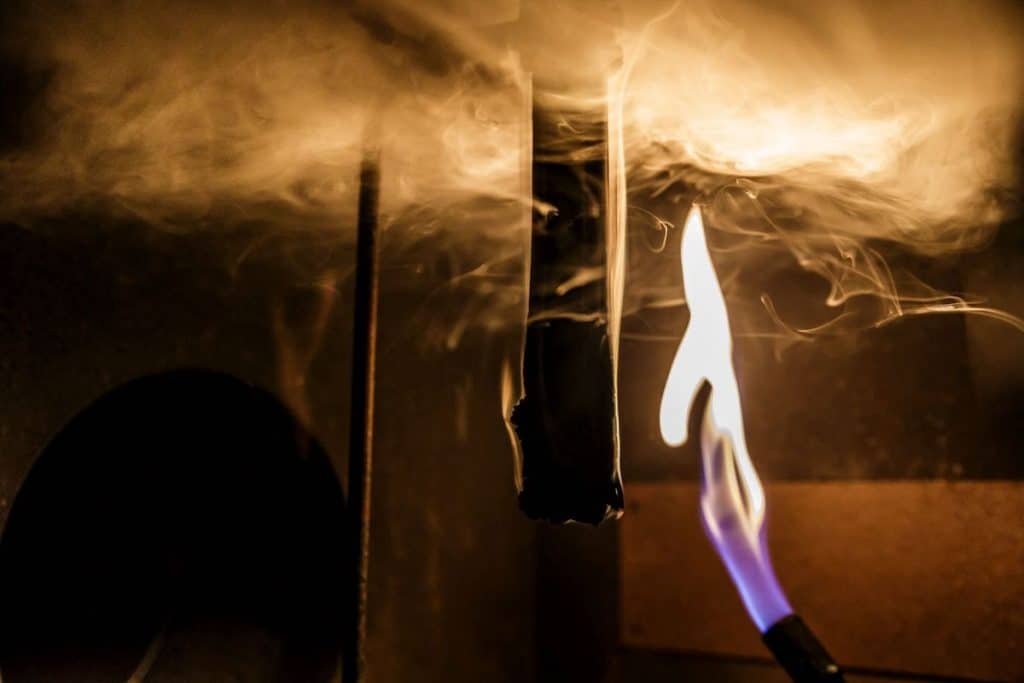
End-users are effectively required to rely on the honesty and integrity of the trader who in turn is reliant on the honesty and integrity of a manufacturer who may well have their own interpretation of test methods and quality standards. European conveyor belt manufacturers could also justifiably argue that they are at a disadvantage. Interestingly but somewhat worryingly, with only one notable exception as far as I can tell, all European-based belt manufacturers import and re-sell belting under their own brand name to supplement their overall output. This allows them to be more competitive on price. Again, the vast bulk of these imports come from China and to a lesser extent India.
Seek advice
A significant difference in price is best treated with suspicion. As the quality of a belt is usually reflected by its price it is always worth the effort to check and compare the original manufacturer’s specifications very carefully and ask for documented evidence of compliance and performance. As I mentioned earlier, the only way to assess value for money is to know the true cost. Paying a bit more for the superior performance and lower lifetime cost provided by one, good quality belt rather than two or three ‘economically priced’ belts will almost certainly prove that sometimes, more really can be less.
Leslie David
About the author
After spending 23 years in logistics management, Leslie David has specialised in conveyor belting for over 13 years. During that time, he has written numerous technical guidance bulletins and is one of the most published authors on conveyor belt technology in Europe.