*Greenwashing – Misleading the public to believe that a company or other entity is doing more to protect the environment than it is, greenwashing promotes false solutions to the climate crisis that distract from and delay concrete and credible action.
Product life cycle
It is estimated that more than 45,000 kilometers of non-biodegradable polyester and nylon fabrics used in conveyor belt carcasses are discarded annually in Europe alone. That is more than the circumference of our planet and represents the single biggest influence on the industry’s carbon footprint.
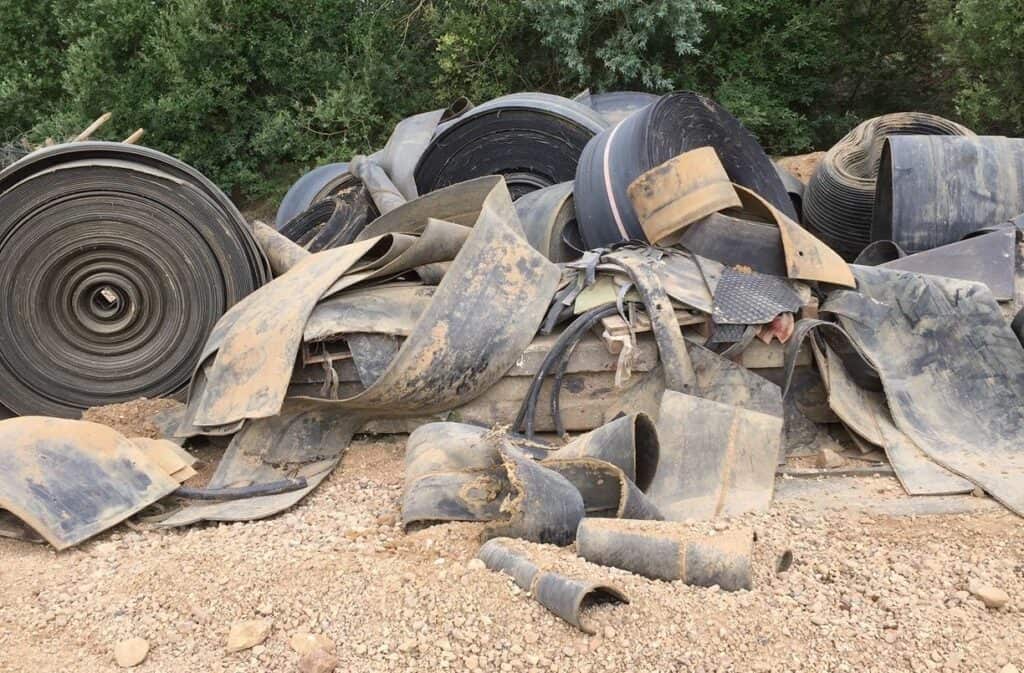
The biggest environmental benefit we can therefore have is to produce conveyor belts that last for up to four or five times longer than would normally be expected. Extending the product life cycle effectively reduces the amount of conveyor belting that needs to be manufactured in the first place while at the same time dramatically reducing the amount of worn out and damaged belt that is being consigned to the scrapheap and ultimately to landfill.
Minimizing our products’ environmental footprint
The second aspect of our environmental focus is the chemicals and ingredients used to create the rubber we use and the lasting environmental impact that they may have on the environment. To make some rubber compounds it is unavoidable that some potentially dangerous chemicals must be used. However, we are very proud to say that all the components we use to manufacture our products comply with the very strong regulations that are in place to protect humans and the environment in the form of REACH (Registration, Evaluation and Authorisation of Chemical substances) regulation EC 1907/2006 and Regulation (EU) No.2019/1021 concerning the use of persistent organic pollutants. These are regulated worldwide by the Stockholm Convention and the Aarhus Protocol, which are international treaties implemented in the European Union through the European Chemicals Agency (ECHA).
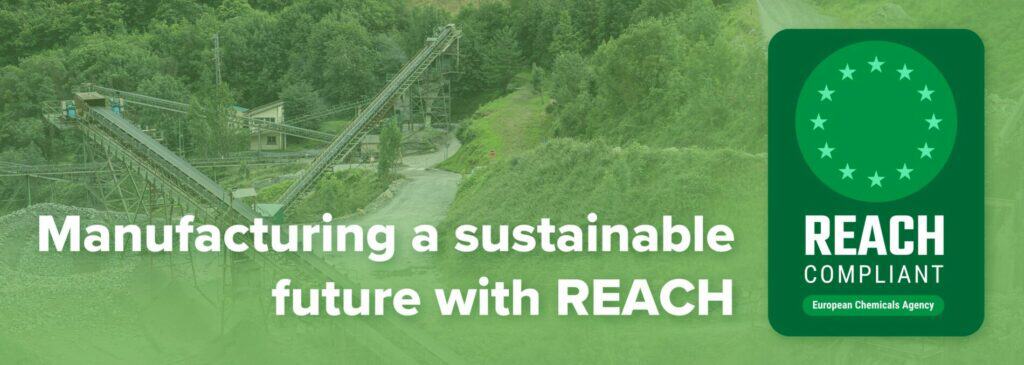
The regulations place direct responsibility on manufacturers to manage the risks from chemicals and to provide safety information. We were the first major manufacturer of conveyor belts to achieve REACH compliance and we have remained its leading advocate ever since. Unlike a great many of our competitors, we manufacture our own rubber, which enables us to comply with environmental regulation because we have full control over everything that we do rather than relying on outside sources to do it for us.
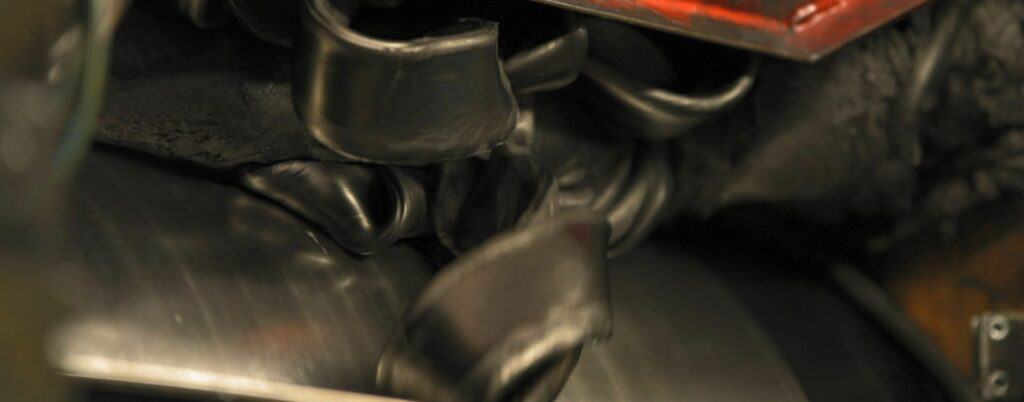
Sadly, many European conveyor belt manufacturers have chosen to ignore REACH and POP’s regulation, either completely or at least partially because of the impact it has on their production costs. Worse still, conveyor belt manufacturers located outside of EU member states and the UK such as those in Southeast Asia, are not subject to the regulations and are therefore free to use unregulated raw materials that are entirely prohibited or at least have strict usage limitations within Europe. This is why we always advise end-users to ask their belt supplier for confirmation of REACH regulation compliance.
Optimizing production processes.
Much of the machinery used to manufacture rubber industrial conveyor belts is old and not as energy efficient as it could be, so we have invested many millions of euros replacing outdated machinery with new, technically advanced, more energy efficient production equipment, which reduces the carbon footprint.
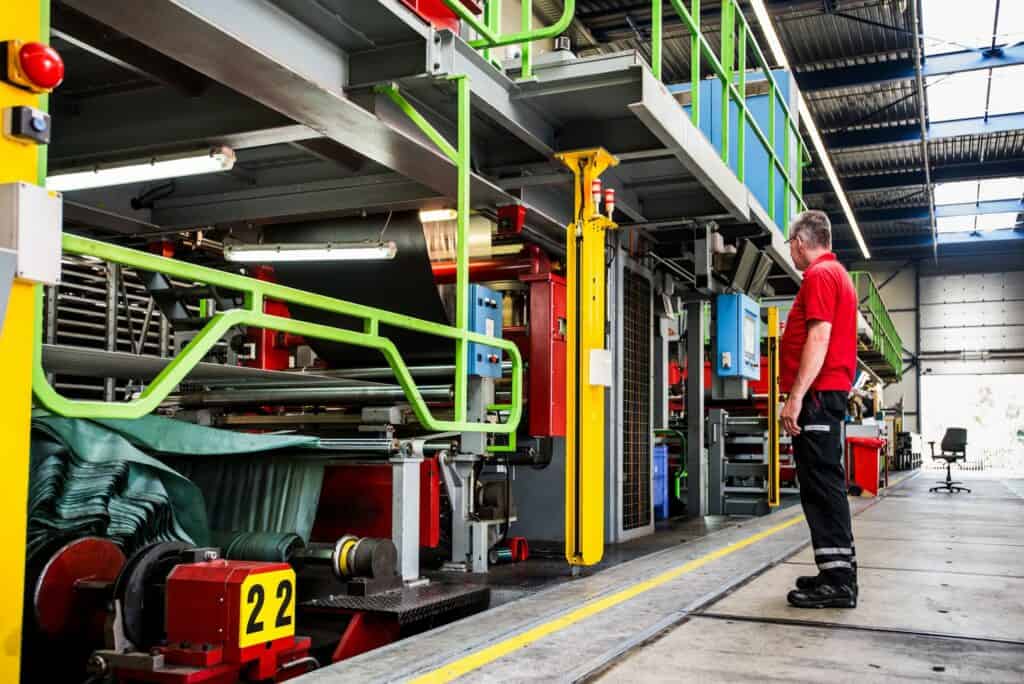
Very importantly, we have introduced new products such as our single-ply Ultra X range of belts that possess many environmental advantages including helping to maximise production efficiency and minimises the amount of power consumed. Another advantage is that having a thinner, lighter but stronger carcass compared to conventional multi-ply conveyor belt reduces the amount of rubber and polyester and nylon fabric used in the manufacturing process as well as the power needed to drive the belt, all of which helps to reduce its carbon footprint.