Many commonly processed dusts are highly combustible, and the combination of dust particles, confined spaces, and possible ignition sources creates an extremely hazardous environment that requires strict safety measures to prevent disaster.
One of the most common high-risk locations for problems is equipment transitions where the powder flows between two pieces of machinery through a non-metallic flexible connector.
A common belief is that just having earthing (or grounding) cables in place is sufficient to prevent the kind of spark discharges that can ignite dust explosions in these settings. However, nothing could be further from the truth!
The Basics of Dust Explosions in Powder Processing
In processing plants, dust explosions pose a high risk wherever powdered materials escape containment and settle on surfaces. One of the most high-profile examples of this kind of event was the tragic explosion at the Imperial Sugar Company plant in 2008, which killed 14 workers and injured 38 others (shown adjacent).
These explosions can occur when fine dust becomes airborne and encounters an ignition source. Even a thin layer of dust is enough to cause a significant secondary explosion if ignited after an initial blast, amplifying the damage and often resulting in devastating outcomes.
To mitigate these risks, plants must prioritize the containment of dust within processing equipment and minimize dust leakage. Effective dust management and equipment maintenance are essential in preventing dust accumulation, which can serve as fuel for potential explosions.
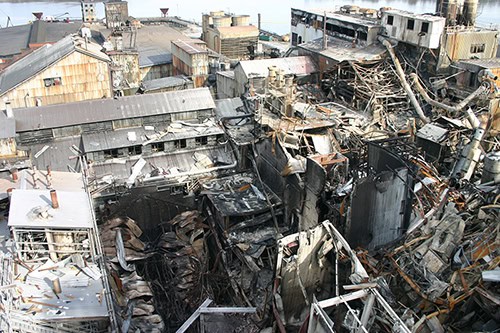
The Role of Earthing Cables in Spark Discharge Prevention
Static electricity creation is inevitable during powder processing, where dust particles move through pipes, rubbing against surfaces and generating electrostatic charges. This charge can build-up and lead to hazardous spark discharges if it isn’t managed effectively. In an industrial context, spark discharges occur when two materials with different electrical potentials come close enough to allow a charge to jump, creating a spark. These sparks, if near combustible dust or gas, can be a serious fire hazard.
Earthing cables help to control this risk by creating a path for static charges to dissipate safely into the ground. This helps equalize the electrical potential across different components, minimizing the risk of uncontrolled spark discharges.
However, while earthing cables are essential, they may not be sufficient to fully prevent sparking and ignition in all parts of a processing line.
Why Earthing Cables Alone May Not Be Enough
Although grounding cables can reduce the risk of static buildup, they don’t address all electrostatic hazards in powder processing environments. Static charges can still accumulate inside flexible connectors—where powder flows through non-conductive materials—even if the equipment is grounded. These connectors, often made from rubber or silicone, tend to be insulating rather than conductive, allowing static to build up instead of dissipating safely.
Flexible connectors are particularly vulnerable to spark discharges, especially when not designed for static dissipation. While grounding cables are typically placed at transition points to equalize potential between metal sections of the piping, they do not prevent static build-up within the connectors themselves. Without a direct path to dissipate this internal charge, static can build until it releases as a spark, easily igniting flammable dust or gases.
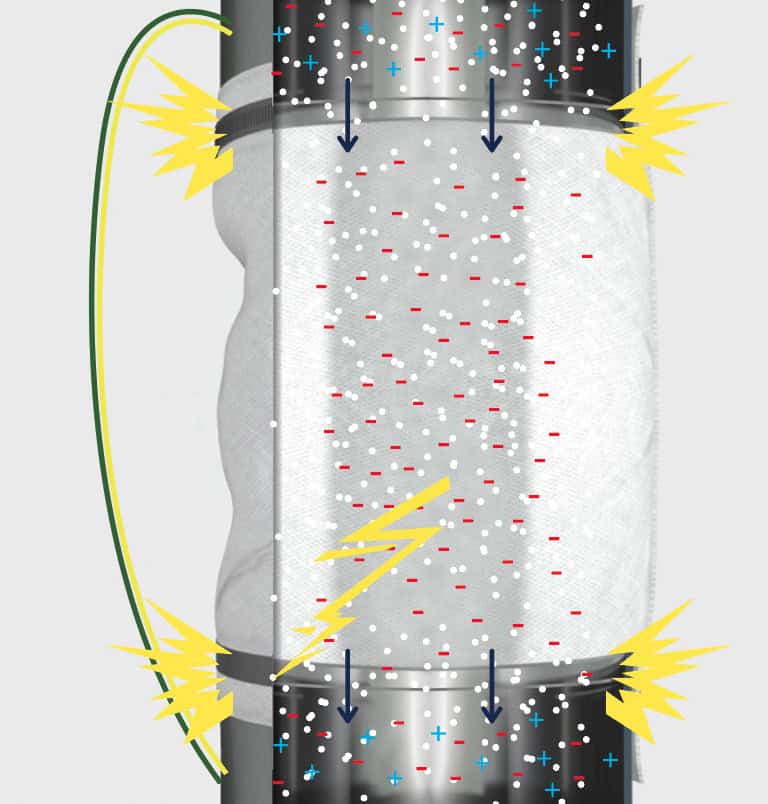
Enhancing Safety with Static-Dissipative Materials
To reduce electrostatic risks, static-dissipative materials in flexible connectors are crucial.
These materials are manufactured to allow charges to dissipate in a controlled manner, thereby reducing the potential for sparks within connectors.
Industry-leading BFM® fitting uses static-dissipative materials like their proprietary polyurethane, Seeflex, which is specifically designed to prevent electrostatic buildup. The most popular product is the Seeflex 040E, rated with a surface resistivity of 1010, and this allows for safe static dissipation in most applications, significantly lowering the risk of sparks inside flexible connections.
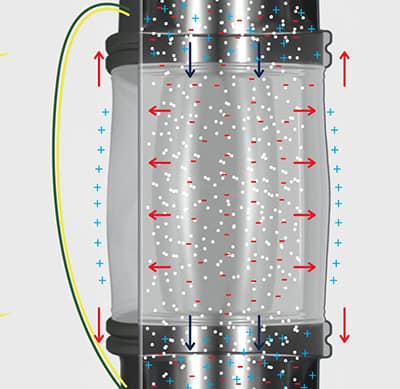
Additional options like Seeflex 040AS (with a surface resistivity of 108) and Teflex NP Black (a pure PTFE material with a surface resistivity of 106) offer even higher dissipative characteristics for particularly high-risk applications.
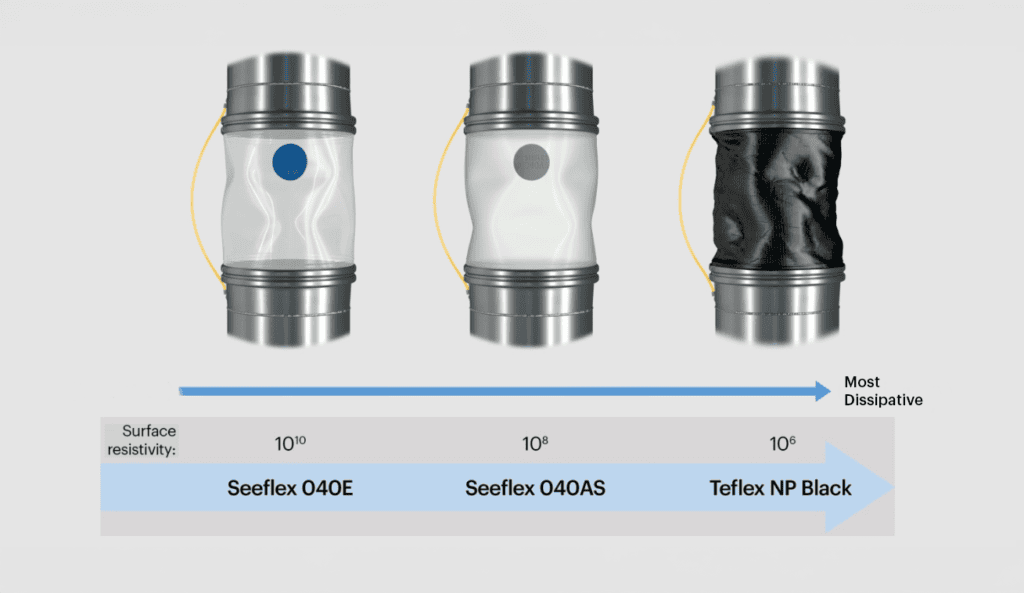
Flexible Connector Design Is also Key
In addition to the material properties, the design of the flexible connectors themselves plays a role in allowing dust to leak into the plant environment, as well as containing any potential initial explosions that can occur inside equipment. Clamped connectors are notorious for leaking dust and being the first point of weakness in the case of an internal explosion.
BFM® fittings’ connectors, however, seal tightly within their spigots, preventing leakage while offering robust resistance to internal explosions. These features help contain the explosion’s energy within the processing line, reducing the chances of a secondary, more damaging explosion.
Earthing cables and static-dissipative materials are both essential, but other important practices like regular cleaning and maintenance are imperative to minimize the risk of spark discharges and dust explosions.
It’s important to use appropriate air filters or dust collectors suitable for your dust type and operation to capture residual airborne particles. BFM® fitting’s quality FM1 breather bags, for example, are a top choice for global manufacturers who need to allow airflow through their processes without allowing dust to escape.
Regular inspection of equipment and proactive maintenance not only improves safety but also reduces downtime and extend equipment life.
A Holistic Approach to Spark Discharge Prevention
While earthing cables are essential for minimizing the risk of electrostatic discharge in powder processing environments, alone they aren’t enough. Flexible connectors, where static build-up is common, require additional safeguards, such as using static-dissipative materials to control internal charge accumulation.
Properly designed connectors, regular equipment maintenance, and dust management are also critical in reducing the risk of spark discharges.
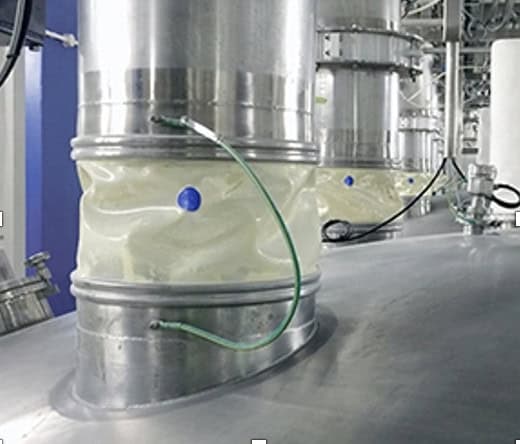
If your plant is serious about doing all it can to protect staff from the devastating effects of dust explosions, the BFM® fitting flexible connector system provides the best way to minimize your risks at these dangerous transition points.