Comprehensive Regulatory Framework
The U.S. dust safety regulations are not just a set of rules, but a comprehensive framework based on key directives and regulations enforced by various agencies, including OSHA, NIOSH, and the EPA. This framework is designed to ensure your safety and keep you well-informed about the potential hazards.
The Occupational Safety and Health Administration (OSHA) sets regulations for worker safety, including permissible exposure limits (PELs) for various hazardous substances. Key standards include OSHA 29 CFR 1910.1000, which addresses general industry standards for air contaminants, and OSHA 29 CFR 1926.55, which applies to construction industry standards for dust and air contaminants.
The Hazard Communication Standard (HCS, OSHA 29 CFR 1910.1200) ensures that the hazards of all chemicals produced or imported are classified. It requires chemical manufacturers and importers to evaluate the hazards of the chemicals they produce or import and to provide information about them through labels and safety data sheets (SDSs).
The National Institute for Occupational Safety and Health (NIOSH) provides recommended exposure limits (RELs) and conducts research to provide updated guidance on occupational safety. The Environmental Protection Agency (EPA) oversees environmental exposure to hazardous substances through regulations such as the Clean Air Act (CAA), which sets limits on emissions of hazardous air pollutants.
These regulations are essential in protecting public health and the environment by controlling exposure to hazardous substances.
Focus on Hazardous Substances: Titanium Dioxide and Silica
Substances such as titanium dioxide and silica are given particular attention due to their significant health risks. Titanium dioxide, used extensively in pigments and coatings, is classified as possibly carcinogenic to humans (Group 2B) by the International Agency for Research on Cancer (IARC). OSHA and NIOSH guidelines help manage its safe handling to minimize inhalation risks.
Crystalline silica, known for its severe health risks, including silicosis and lung cancer, is heavily regulated. OSHA’s Respirable Crystalline Silica Standards (29 CFR 1910.1053) for general industry and 29 CFR 1926.1153 for construction require measures to limit exposure, such as engineering controls and respiratory protection.
Detailed Substance Regulation: The Role of NIOSH and EPA
NIOSH conducts research and provides guidance on occupational hazards, including comprehensive studies on various substances’ health effects and recommending exposure limits. The EPA manages the assessment and regulation of hazardous substances through initiatives like the Integrated Risk Information System (IRIS), which provides health risk assessments for various chemicals.
Standards and Safety Measures
Key safety measures include the Combustible Dust National Emphasis Program (NEP) by OSHA, which aims to reduce the risk of combustible dust explosions and fires. It provides guidelines for identifying and controlling dust hazards in workplaces. OSHA’s General Duty Clause (Section 5(a)(1) of the OSH Act) requires employers to provide a workplace free from recognized hazards that are causing or are likely to cause death or serious physical harm.
Engineering Controls and Safety Practices
Effective engineering controls are critical for managing dust safety. Properly designed ventilation systems help control dust levels in the workplace. Enclosing processes that generate dust prevents it from becoming airborne. Dust suppression techniques, such as using water sprays or other methods, reduce dust emissions.
Appropriate personal protective equipment (PPE), including respirators and protective clothing, must be provided based on specific risk assessments. Training and awareness programs are vital in promoting a safety-conscious workplace. Regular training sessions and drills ensure that workers are aware of potential hazards and know how to respond effectively.
Requirements for Testing Laboratories and Industry
Testing laboratories must adhere to recognized quality control standards, such as those set by the American Industrial Hygiene Association (AIHA). Industries handling dust-producing substances must implement rigorous safety procedures, conduct regular audits, and meticulously document all processes. This level of detail ensures that every aspect of dust safety is thoroughly examined and recorded, providing reassurance and accountability.
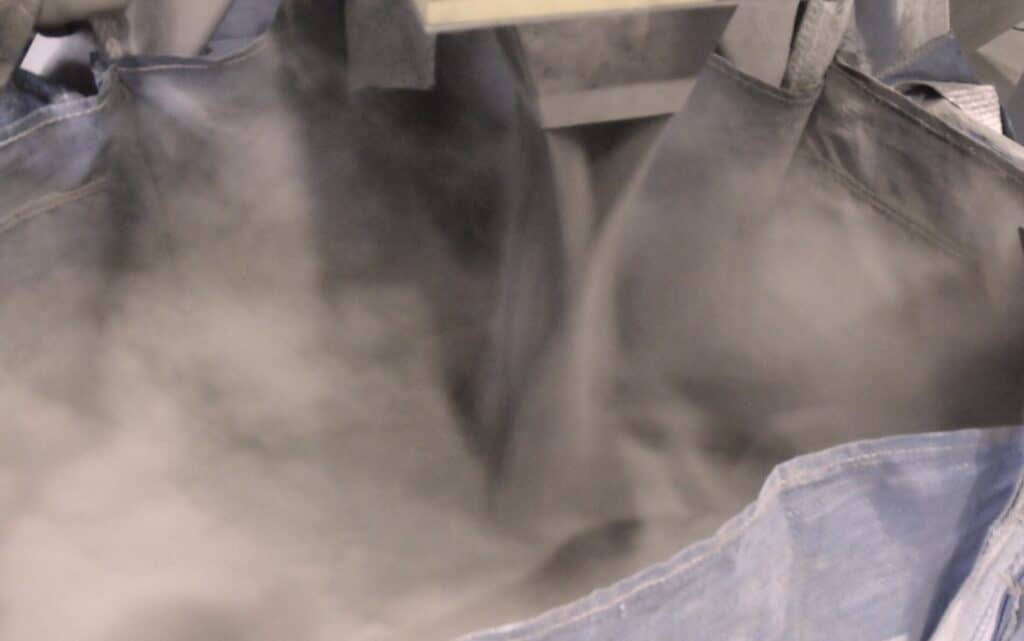
Commitment to Dust Safety
Although dust may often be perceived as a mere nuisance, it poses significant health and safety risks. By adhering to stringent standards, implementing effective safety measures, and raising awareness, the challenges of dust safety can be responsibly managed in both laboratory and industrial environments.
Historical Context and Evolution of Regulations
Understanding the historical context of how dust safety regulations have evolved in the U.S. provides valuable insight. Over the years, key milestones and changes have shaped the current regulatory frameworks, adapting to new scientific findings and technological advancements. For instance, the 2008 Imperial Sugar refinery explosion was a significant event that highlighted the catastrophic potential of combustible dust and led to increased regulatory focus and industry awareness.
Specific Industry Practices
Different industries face unique challenges and practices regarding dust safety. Examples from industries such as mining, construction, pharmaceuticals, and manufacturing illustrate how regulations are applied in various contexts. The mining industry, for example, often deals with silica dust, requiring specialized controls and monitoring practices, while the pharmaceutical industry must manage fine particulate matter from chemical compounds.
Case Studies
Real-world examples of incidents related to dust safety, such as industrial accidents or successful implementations of safety measures, provide practical insights and underscore the importance of adhering to regulations. The 2008 Imperial Sugar refinery explosion highlighted the catastrophic potential of combustible dust and led to increased regulatory focus and industry awareness.
Technological Advances
Recent advancements in technology that aid dust safety include improved dust monitoring equipment, innovative PPE, and cutting-edge engineering controls. Real-time dust monitors provide immediate feedback on dust levels, allowing for prompt corrective actions. Innovations in PPE, such as more effective respirators, enhance worker protection against inhalation hazards.
International Comparison of Dust Safety Regulations: United States vs. European Union
Dust safety regulations vary significantly between the United States and the European Union, reflecting different legislative frameworks, enforcement mechanisms, and industry practices. This article provides a concise comparison of the key aspects of dust safety regulations in these two regions, highlighting major directives and standards.
United States: OSHA and EPA
In the United States, the Occupational Safety and Health Administration (OSHA) and the Environmental Protection Agency (EPA) are the primary regulatory bodies overseeing dust safety. OSHA sets regulations for worker safety, including permissible exposure limits (PELs) for various hazardous substances. Key standards include:
- OSHA 29 CFR 1910.1000: This standard addresses general industry requirements for air contaminants.
- OSHA 29 CFR 1926.55: This standard pertains to the construction industry and covers dust and air contaminants.
OSHA also enforces the Hazard Communication Standard (HCS, 29 CFR 1910.1200), which requires chemical manufacturers and importers to evaluate and communicate the hazards of the chemicals they produce through labels and safety data sheets (SDSs).
The EPA, through the Clean Air Act (CAA), regulates environmental exposure to hazardous substances by setting limits on emissions of hazardous air pollutants.
European Union: ATEX and REACH
In the European Union, dust safety is primarily regulated under the ATEX directives and the REACH regulation, managed by the European Chemicals Agency (ECHA).
- ATEX Directives: The ATEX directives (ATEX 2014/34/EU and ATEX 1999/92/EC) regulate equipment and protective systems intended for use in potentially explosive atmospheres. These directives ensure that machinery and tools used in hazardous areas are designed to prevent dust explosions.
- REACH Regulation: The Registration, Evaluation, Authorization, and Restriction of Chemicals (REACH) requires companies to identify and manage the risks associated with the substances they manufacture and market in the EU. REACH aims to enhance the protection of human health and the environment from chemical risks.
Key Differences
One of the primary differences between U.S. and EU dust safety regulations is the approach to chemical safety. The EU’s REACH regulation is more comprehensive in chemical registration and evaluation compared to the U.S. Toxic Substances Control Act (TSCA). REACH places the burden of proof on companies to demonstrate the safety of their chemicals, whereas TSCA requires the EPA to prove that a chemical is unsafe.
The ATEX directives focus heavily on preventing explosive atmospheres, which is a unique aspect of the EU regulations. In contrast, OSHA’s regulations are broader, addressing general dust safety and worker exposure limits without the specific emphasis on explosive environments found in ATEX.
Conclusion
Both the United States and the European Union have robust frameworks for managing dust safety, yet their approaches differ in scope and specificity. While the U.S. relies heavily on OSHA and EPA standards, the EU employs ATEX and REACH to address both worker safety and environmental protection comprehensively. Understanding these differences is crucial for multinational companies operating in both regions to ensure compliance and protect worker health and safety.