In part I of this series of articles “How to Safely Store Combustible Dusts & Powders” discussed how a hazardous area classification should be undertaken. This resulted in the assignment of a hazardous zone within or around items of processing equipment. The Part II article considered the ignitability characteristics of powders.
Combustion is simply an exothermic chemical reaction between a fuel and air or oxygen. For example, combustion of natural gas (methane) in air results in the combustion products of carbon dioxide and water vapour, and the release of a significant amount of energy. Hence any powder which is not fully oxidised, will be capable of reacting with air and undergoing the combustion process.
As with most chemical reactions generally some form of energy must be inputted to the fuel/air mixture to start the reaction – this is generally achieved by heating the reactants, but all the other potential energy sources (electrostatic sparks, mechanical sparks etc) discussed in Part II can achieve the same result. It is also common knowledge that chemical reactions generally occur more easily when the solid powder is of small particle size – hence why dust explosions occur. This is due to the surface area to volume relationship – the smaller the particle size, the larger the surface area. Also, any heat generated from the particle cannot be dissipated throughout the bulk of the powder, so the localised energy vapourises the solid particle.
But the potential energy source must have sufficient energy to start the combustion reaction. This is why understanding the specific ignitability characteristics of the powder is important – the minimum ignition energy and safe allowable temperature are key parameters. If the energy generated in the processing operation does not exceed the energy required to start the combustion reaction, then ignition will not occur, and a fire or explosion cannot result. If a generated dust cloud does not come into contact with a source at a temperature above the safe allowable temperature; or an electrostatic spark energy is less than the minimum ignition energy of the powder, then combustion will not occur.
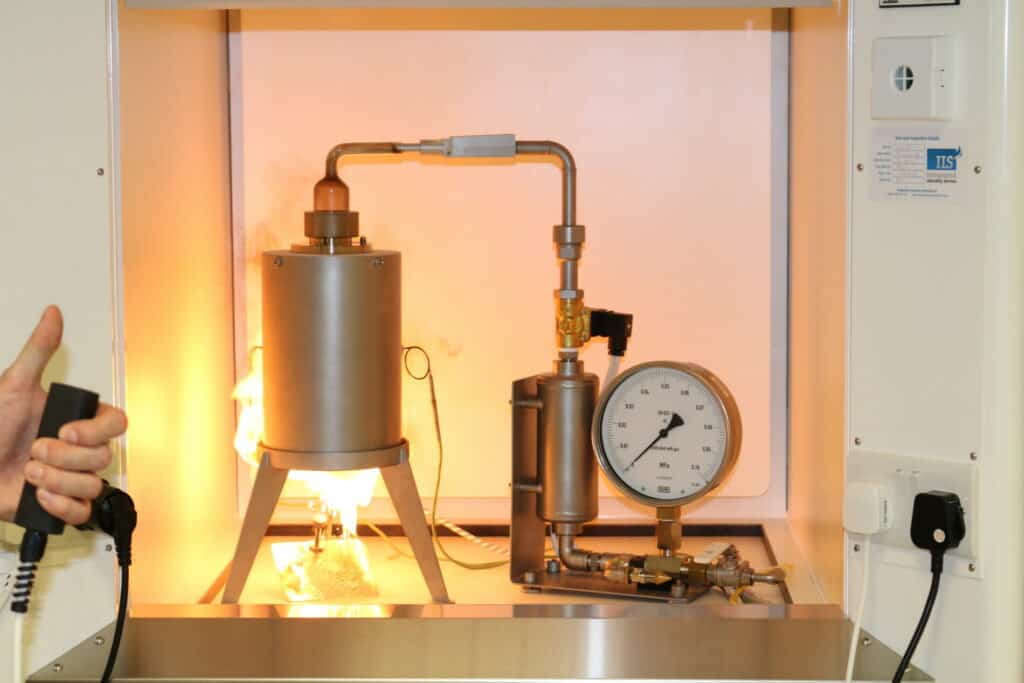
The Hazardous Area Classification has indicated where potential flammable dust clouds may occur, and how likely they are of being present. The first aim is to ensure that flammable dust clouds do not exist. This can be achieved by ensuring the combustible powders are of large particle size; or are used in a wetted or paste form; or by the use of inerting to remove the oxygen, etc.
Reducing the probability of electrical or mechanical sources of ignition being present, or reducing the potential energy generated from such sources (so the energy is below the powder specific minimum ignition energy etc) can be achieved in various ways. For example, ensuring all metal components and personnel are earthed will prevent spark discharges; reducing the presence or limiting the size of insulating components, or the addition of anti-static agents to high resistivity powders, can prevent electrostatic charge accumulation; reducing the tip speed of rotating equipment can prevent sufficient mechanical energy being developed.
Any electrical or mechanical equipment installed or used (if portable) within the hazardous zones is required to be of ‘special’ construction. The ‘special’ construction of the item of equipment is laid down in the essential safety requirements of the ATEX Directives and are certified as appropriate for the zone. Essentially the construction ensures that sparking components either do not generate sufficient energy, or prevent the sparking components from coming into contact with a flammable dust cloud. There are different protection mechanisms used in the construction (for example, intrinsic safety, pressurisation, encapsulation etc).
This essentially means that the probability of the equipment acting as a potential ignition source for a flammable dust cloud present is low. The aim is to eliminate the potential of an item of equipment acting as an ignition source.
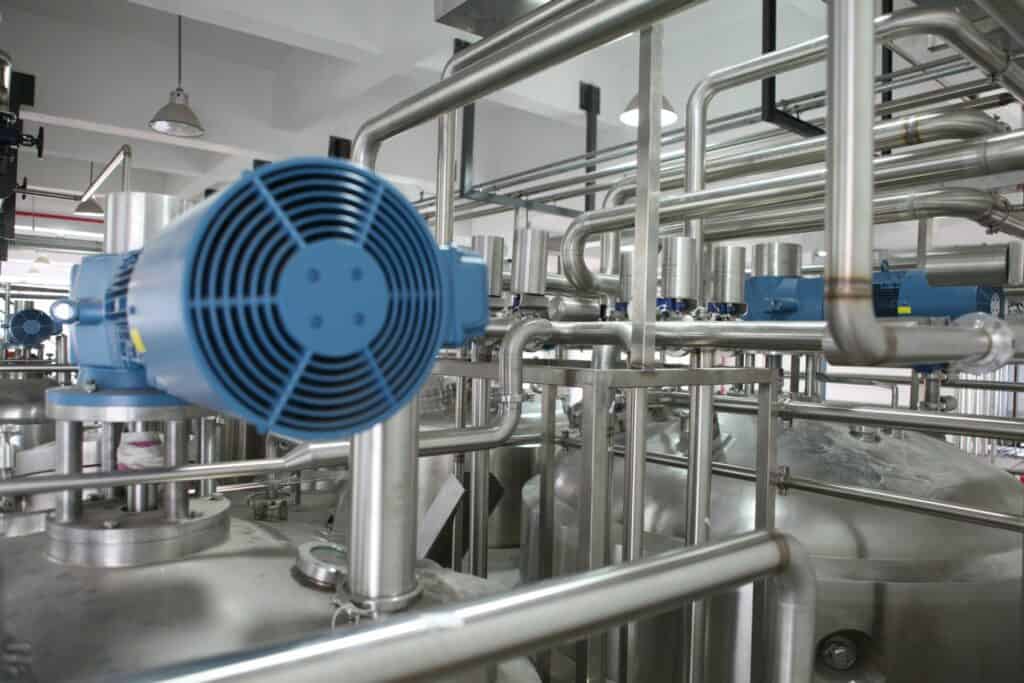
The result of a fire or explosion is a combination of the likelihood of a flammable dust cloud being present, and the likelihood of an effective ignition source being present simultaneously. If a flammable dust cloud is present continuously (Zone 20), then the risk reduction is achieved by the probability of an ignition source being present. In this case, so-called Category 1 equipment is constructed which essentially means that the equipment will not act as an effective ignition source in normal operation; in an expected malfunction state; or in a rare malfunction. If a flammable dust cloud is present infrequently (Zone 22), then the risk reduction is primarily achieved by the probability of a flammable dust cloud being present. In this case, so-called Category 3 equipment is constructed which essentially means that the equipment will not act as an effective ignition source in normal operation only.
The equipment can also be constructed in such a way that the equipment cannot generate heat. Provided the maximum temperature that the equipment item is below the safe allowable temperature then safety is ensured.
Although, prevention or reduction of the generation of flammable dust clouds and the reduction of potential effective ignition sources should ensure safety, an actual ignition may still occur – the risk has been reduced but not eliminated. Therefore in the next article of this series, we will discuss what measures can be taken on your processing plant to deal with potential ignited events.
Sigma-HSE is an internationally recognised process safety company with ISO/IEC 17025 accredited testing laboratories. We provide fire and explosion data: 20L, MEC, MIE, LIT, LOC, electrostatics and thermal screening. Our safety engineers are experienced in DSEAR, ATEX and DHA across many process industries.
Read: “How to Safely Store Combustible Dusts & Powders: Part I“
Read: “How to Safely Store Combustible Dusts & Powders: Part II“