The initial article How to Safely Store Combustible Dusts & Powders discussed how a hazardous area classification should be undertaken. This resulted in the assignment of a hazardous zone within or around items of processing equipment. Typical zones for powder silos and bulk bags handling combustible dusts were:
Silos
- Zone 20 within a silo.
- Zone 21 for pneumatic transfers, rotary valves and screws.
- Zone 22 within clean side of silo filter, fan and exhaust.
Bulk Bags
- Zone 21 within a bulk bag and beneath the grill of a tipping station.
- Zone 22 for 3m around the bulk bag.
- Zone 22 for 1m around tipping station if LEV, if not then Zone 21.
- All dust zones down to impervious floor level because dust clouds will fall to the ground.
Any electrical or mechanical equipment installed or used (if portable) within these zones needs to be constructed to the essential safety requirements of the ATEX Directives and certified as appropriate for the zone. This essentially means that the probability of the equipment acting as a potential ignition source for a flammable dust cloud present is low. The aim is to eliminate the potential of an item of equipment acting as an ignition source.
The applicable BS EN 60079 standard considers thirteen different types of potential ignition sources:
- Hot surfaces
- Flames, smoking and hot work
- Mechanical friction and impact sparks
- Electrical installations and equipment/apparatus
- Electrostatic
- Exothermic reactions and spontaneous combustion
- Stray electrical currents in electrical installations
- Adiabatic compression and shockwaves
- Radio frequency electromagnetic radiation
- Lightning
- Visible and high frequency electromagnetic radiation
- Ultrasonic sound waves
- Ionising radiation
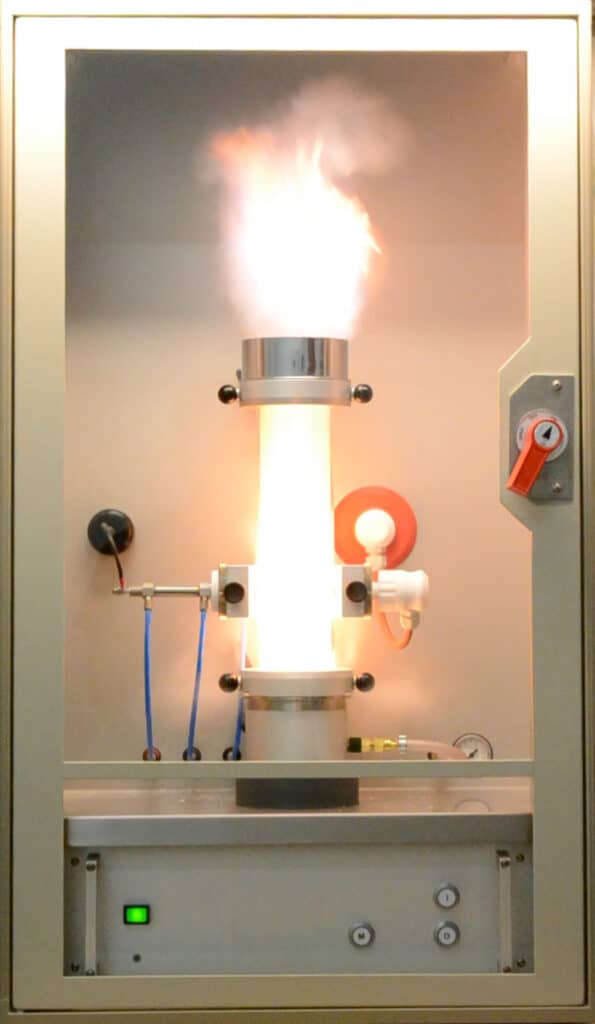
So, essentially any form of energy could have the potential to ignite combustible dust clouds, if the source has sufficient energy to ignite a substance-specific combustible dust cloud. The most common ignition sources for combustible dust clouds are hot surfaces, electrostatics, unsuitable electrical equipment, and mechanical sparks.
The first step is to determine whether or not your dust is in fact combustible. This is determined by subjecting your powder/dust to a specific test, known as the Group A/B test (Dust Combustibility Test BS EN ISO IEC 80079-20-2). Essentially, in specific apparatus, a dust cloud is generated and subjected to a high-energy ignition source. If the cloud ignites, then it is classified as a Group A or Combustible dust. If it doesn’t ignite, it is a Group B or non-combustible dust. You may indeed be able to determine if your powder is combustible or not by simply searching literature. Either way, you need this knowledge to be able to undertake the hazardous area classification in the first place.
Although you may know that your combustible dust is in fact combustible, what you don’t know is how much energy is required to ignite the dust cloud. Every substance is different in this regard, and it is not possible (or very difficult) to calculate what level of energy is necessary to achieve ignition. But there are specific tests that can and should be undertaken to determine these energy levels for different sources of energy.
For ignition of a combustible dust cloud, there are two tests required:
- Minimum Ignition Energy (MIE) – determines the minimum energy from electrostatic or mechanical means which can ignite the dust cloud
- Minimum Ignition Temperature – determines the minimum temperature which can ignite the dust cloud
Clearly, if this temperature or energy level cannot be reached in your specific processing equipment, then ignition of a combustible dust cloud will not occur.
The MIE test equipment generates a dust cloud, and a spark between two electrodes of a specific energy level is generated. In the test apparatus, the spark between the electrodes can be achieved by two means – via capacitance or induction. The capacitance generated spark mimics electrostatic ignition sources, and the inductance generated spark mimics mechanically generated sparks.
The MIT test equipment generates a dust cloud under specific temperature conditions.
The MIE’s of combustible dust can range from 1mJ to >1000mJ
A purely capacitive MIE value is used for all processing situations, as the majority of operations involving powders will generate electrostatic charge, and therefore there is a high possibility of the material being exposed to an electrostatic spark discharge.
The table below shows some typical electrostatic spark (capable of igniting dust clouds) energy values along with some known mechanisms and examples:
Discharge Type | Mechanism | Example | Approximate Maximum Potential Energy (mJ) |
Cone | From charged bulk powders | Insulating granular material being discharged into silo | 10 – 100 (dependent on various factors) |
Spark | From an isolated conductor | Metal flange on plastic or glass pipeOperator wearing insulating footwearUnearthed Type C FIBC | Up to 200(dependent on the capacitance of the conductor) |
Propagating Brush | From thin insulating materials being highly charged with opposing charge on each surface | Dielectric break down of an insulating pneumatic conveying pipes surface to the earthed metal embedded spiral.Highly charged powder coating on an earthed metal substrate being approached by an earthed item | 2000 |
The inductive MIE is used to evaluate whether friction, grinding and impact sparks from stainless steel on stainless steel contact will produce enough energy and temperature to ignite the material in the form of a dust cloud. This is determined from the tip speed of a rotating component. When tip speeds are less than 1 m.s-1 then there is no risk from ignition by mechanical sparks however when greater than 10 m.s-1 it must be assumed that there is a risk of ignition from mechanical sparks unless you have relevant test data to prove otherwise.
In the next article of this series, we will discuss what measures can be taken on your processing plant to prevent ignition of combustible dusts.
Sigma-HSE is an internationally recognized process safety company with ISO/IEC 17025 accredited testing laboratories. We provide fire and explosion data: 20L, MEC, MIE, LIT, LOC, electrostatics, and thermal screening. Our safety engineers are experienced in DSEAR, ATEX, and DHA across many process industries.