- Highly accurate: suitable feeding systems for every raw material used in the food industry
- Food-grade: Hygienic Design-compliant feeding for absolutely safe food production
- Time-efficient: less downtime thanks to easy, fast cleaning
Anuga FoodTec will revert to an in-person trade fair and is set to open its doors from April 26 to 29. Brabender Technologie, one of the world’s leading manufacturers of gravimetric feeders, featuring digital weighing technology and discharging equipment for bulk solids and liquids from all sectors of industry, will be there – a component supplier to all.
High-precision feeding for any raw material used in the food industry
Be it the FlexWall® Plus universal feeder, single- or twin-screw feeders, vibratory feeders, weight-belt feeders, liquid feeders or discharging aids: Brabender Technologie is helping to make food production both safe and easy on resources by providing a broadly based portfolio of Hygienic Design-compliant gravimetric and volumetric feeders as well as discharging aids. Take the production of granola mixes as an example: dried fruits are often sticky and nuts are prone to breakage. That is why Brabender Technologie has developed the “fruit feeder”. This special food feeder features specific screw and tube combinations and ensures that nuts passing through the screw tube are not ruined and the skins of raisins are not damaged, and therefore that they do not stick. However, Brabender Technologie is also at the top of its game as far as evolving trends are concerned, like feeding plant-based proteins for dry or wet extrusion purposes during the manufacture of meat substitute products.
Rely on the substantial expertise of the feeding experts
“We are the right people to talk to with regard to any issues concerning the wide range of feeding tasks involved in the food industry – and that includes process engineering issues. Continuous or batch? We are adept at both and have been finding the right solutions for a wide variety of feeding requirements together with our food industry customers for many years,” Klaus Plien, Head of Food Sales at Brabender Technologie, explains.
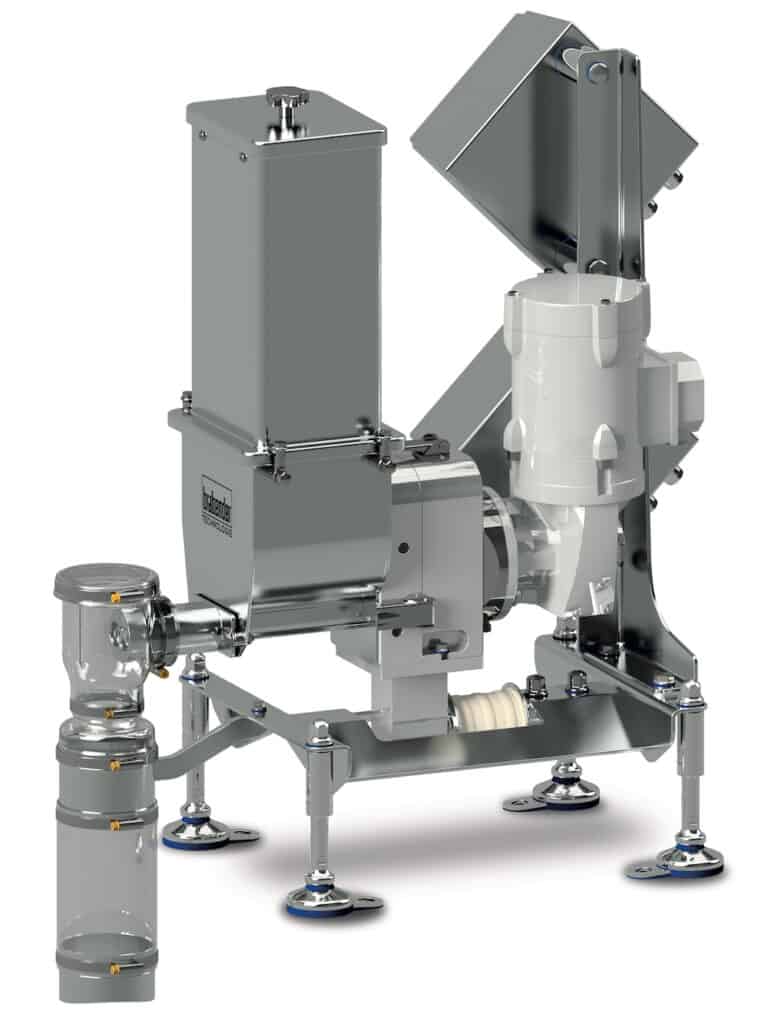
Feeding systems that adapt superbly to the product
The systems that were specially developed for food industry applications ensure highly accurate feeding at absolute adherence to formulations – the perfect basis for permanent quality control. That is important, because every raw material behaves differently. Klaus Plien knows what the differences are. “Natural ingredients often differ very widely in terms of size and shape. Every individual ingredient has special properties, and mixes of multiple ingredients can in turn has quite different properties. That makes the raw materials used in food processing particularly sensitive. Our Hygienic Design-compliant feeding systems can easily be adapted to match the properties and consistency of each raw material.”
Hygienic Design: food-grade and time-efficient thanks to ease of cleaning
Particularly high hygiene standards apply in the food industry and they need to be ensured as early as the feeding stage of any production process. As a leading expert on the subject of feeding and member of the European Hygienic Engineering & Design Group (EHEDG), the global player based in Duisburg, Germany is able to provide an absolutely safe and suitable feeding system for virtually any raw material – irrespective of whether they are dry, moist or liquid products.Brabender Technologie has factored food-grade components into the product development of its feeders specifically for processing foods, and is therefore in a position to meet these stringent hygiene requirements in full.
Klaus Plien: “Horizontal surfaces and exposed threads no longer feature in designs. Instead, users benefit from rounded edges, cavity-free weld seams and quick-release fasteners for screws and screw tubes. The terminal boxes we use also comply with Hygienic Design requirements and drive is provided by a fanless smooth motor. All the plastics we use are FDA- and 1935/2004-compliant materials.” As a result, Hygienic Design not only increases food safety, but also reduces downtimes of all the equipment to a minimum, because the feeders are easy to clean.