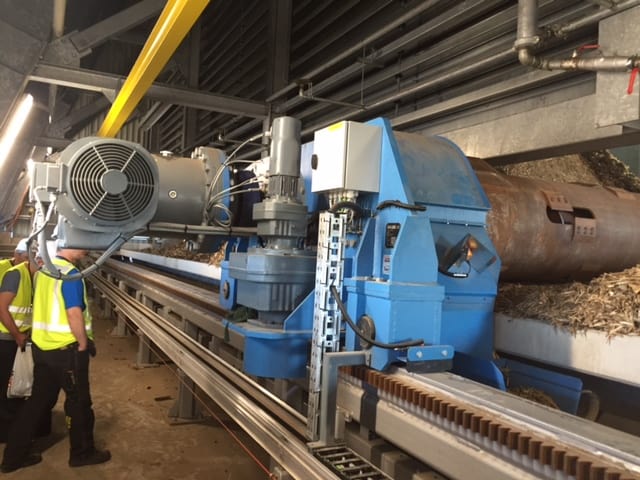
The slots are furnished with activators which reclaim material when the tube rotates. Typical reclaiming rate is 50-400 m3/h but 10 – 1000 m3/h is viable. Material that is fed into the tube is conveyed to the end by the internal screw, thus the material being conveyed is protected from the static pressure exerted by the remaining material in the pile/silo.
The whole unit traverses across the base of square silos on rails and in round silos on a swivel about the centre. Tube rotation depends on travelling direction thereby ensuring consistent operation. The intelligent design employed in the tube and screw configuration constitutes a “closed forces system” and hence no thrust forces into the structure are generated.
Conveying is by gravity flow through the slots and the required power is reduced by at least 70% compared to an open traditional screw reclaimer. Each slot is identical and reclaim is uniformly distributed along the whole length of the tube.
In round silos more slots towards the outer end of the tube compensate for larger swept area. By definition, the design produces a mass flow which allows for first in first out conditions. Feed rate is uniform and is a linear function of adjustable tube rotation.
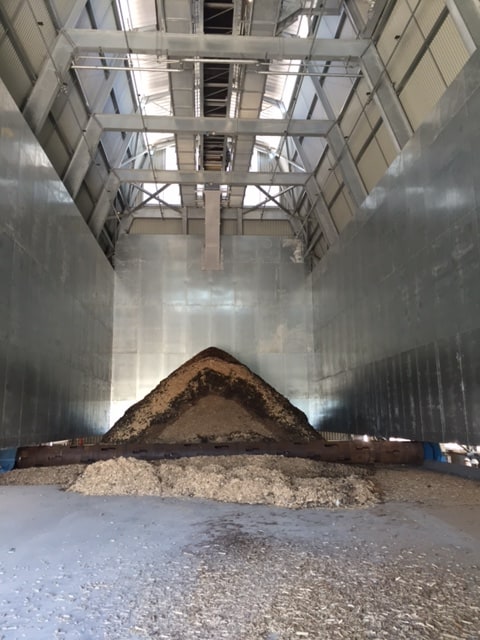
Major advantages using “TubeFeeder” are:
- low energy consumption,
- homogenisation of cross-segregated material,
- preserves quality of bulk particles,
- gives precise blending of qualities.
In economical terms “TubeFeeder” features compared to traditional solutions:
- Reduces operational costs in energy and wear.
- Improves process control by uniform feed rate, homogenisation and insignificant particle degradation.
- Reduces overall investment costs in structure and electrical installations.