Properly weighing and accurately delivering the ingredients without manual intervention can result in a number of process advantages, including overall product safety, fewer mistakes, better accuracy, lower bulk material costs, improved product quality and savings in manufacturing costs.
Several key factors can be considered when implementing an automated ingredient dispensary system which can influence the type of batching system recommended and optimize ingredient cost savings and overall ROI.
Gain-In-Weight (GIW) vs. Loss-In-Weight (LIW) – Which is right for my process?
Typically, ingredient-batching systems can be categorized into two major different technology options: gain-in-weight batching using scale weighing or volumetric feeders, and loss-in-weight batching using gravimetric loss-in-weight feeders.
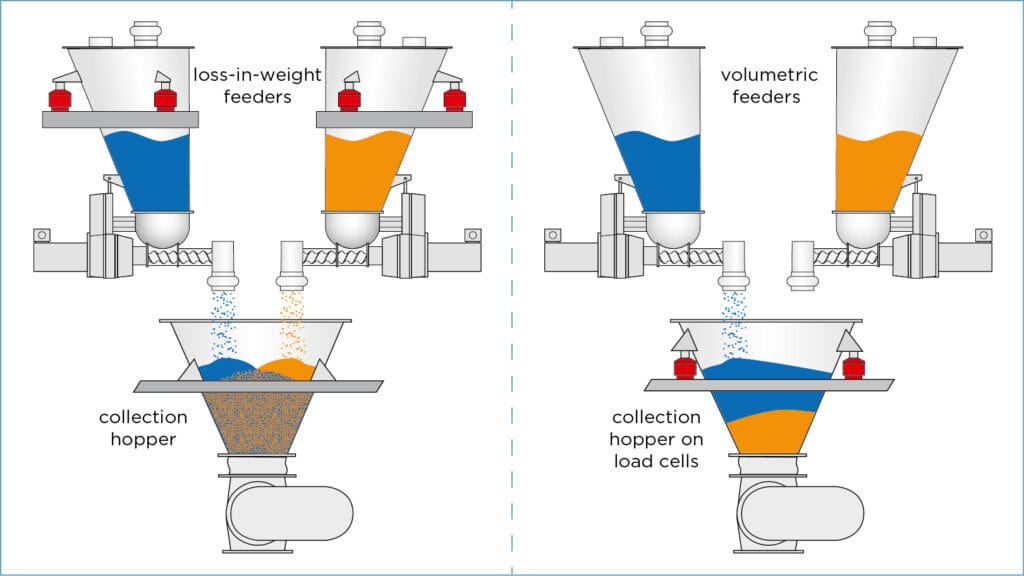
Loss-in-Weight Batch = Loss-in-weight feeders feed simultaneously into a collection hopper.
Gain-in-Weight Batch = Volumetric feeders feed sequentially into a weighed collection hopper.
Gain-in-Weight Batching Using Volumetric Feeders
In GIW batching volumetric metering devices sequentially feed multiple ingredients into a collection hopper mounted on load cells. Each feed device delivers approximately 90% of the ingredient weight at high speed, slowing down towards the end of the cycle to deliver the last 10% at a reduced rate to ensure higher accuracy. Once all the ingredients have been delivered, the batch is complete and the mixture is discharged into the process below. Because this type of batching method is sequential for each ingredient, it results in a longer overall batching time than with LIW batching (outlined below), especially if the number of ingredients is high.
When major ingredient batching requires a single ingredient to be delivered to multiple stations or multiple ingredients delivered to a single destination, scale hoppers can be used. Scale hoppers are receiving hoppers suspended on load cells for ingredient batch weighing. The material resides in the scale hopper until the precise weight and/or combination of materials is achieved. With the scale weighing system, weigh accuracies of ± 0.5% of the full scale capacity can be expected. Once the desired weight has been achieved, the process below then calls for material, a butterfly valve opens and the material in the scale hopper is discharged.
Loss-in-Weight Batching using Gravimetric Feeders
LIW batching, utilizing gravimetric screw feeders for each ingredient, provides a significant accuracy and process time advantage over GIW batch techniques. LIW batching is used when the accuracy of individual ingredient weights in the completed batch is critical or when the batch cycle times need to be very short. In addition, LIW feeding affords broad material handling capability and thus excels in feeding a wide range of materials from low to high rates. Gravimetric feeders operating in batch mode simultaneously feed multiple ingredients into a collection hopper. Once all the ingredients have been delivered, the batch is complete and the mixture is delivered to the process below. Since all ingredients are being delivered at the same time, the overall batch time as well as further processing times downstream are greatly reduced. This method of batching is often used for high value ingredients due to their ingredient cost and to ensure accurate proportioning in the mixture.
As with GIW batching, the first 90% of the batch weight (as determined by the pre-programmed recipe) is fed at a fast rate by the feed screws. The last 10% is fed in a slower “dribble” mode to ensure an accurate batch weight, reaching accuracies of ± 0.1% of the desired setpoint.
In pharmaceutical dispensaries, for example, Coperion K-Tron’s pharmaceutical feeders are also used in cluster type arrangements, as shown in picture 1, in order to dispense several ingredients at once, all using high accuracy Smart Force Transducer load cells.
How Do You Choose?
Each of these technologies have inherent advantages and limitations. In order to choose the most efficient system, it is important to review the critical criteria required for the system as a function of batch time, accuracy required, amount of time allowed for quick changeover/cleaning and of course, overall costs.Optimization of batch accuracy will also be a function of the load cell resolution available.
For example, in GIW batching, when discharging into a hopper or receiver on load cells, the accuracy is a function of the full scale capacity of the receiving vessel. In other words, a system designed to add both macro and micro ingredients in the same vessel may not be able to detect accurately the smaller amounts. This difference in accuracy between GIW and LIW systems (± 0.5% of full scale versus ±0.1% of actual ingredient weight) can have a significant impact, especially with higher cost ingredients such as high value additives, vitamins, probiotics, etc.. Therefore, many times, in order to make the overall batching operation more cost effective, a combination of the GIW and LIW batching is used. GIW batching techniques are used for the macro ingredients, and separate LIW feeders are used for the micros whose batch weights may be too small to be detected by the GIW scale hoppers.
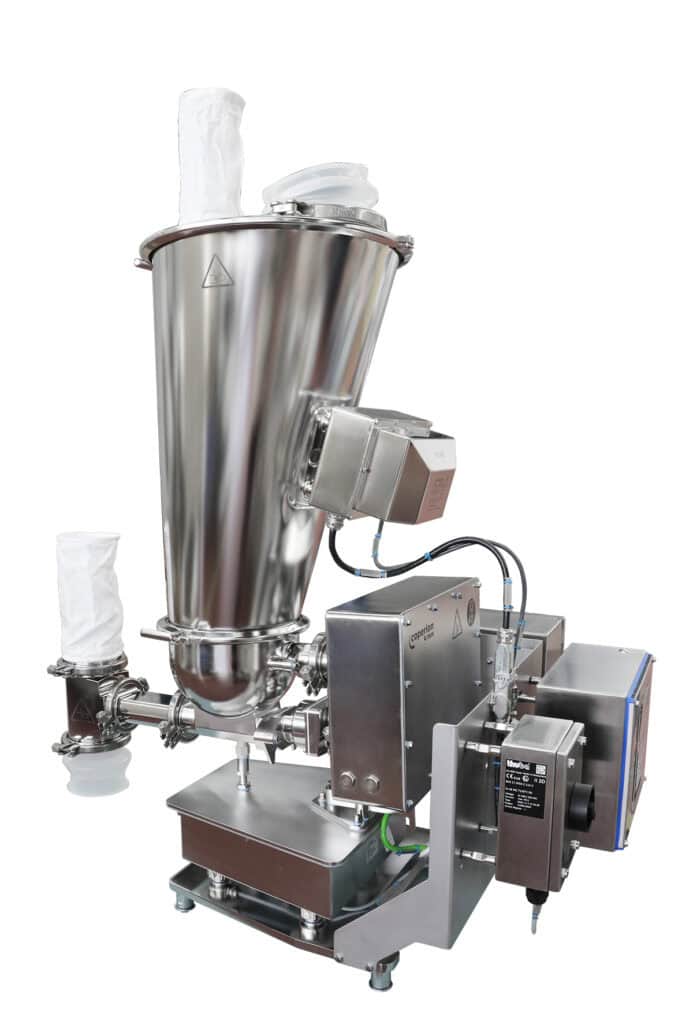