Processors in the market for feeding equipment have a number of options to consider when choosing the correct feeder for their application. One of the most important factors in making the best choice is understanding the range of materials you intend to feed with this equipment. Here are some basic questions to ask about materials and other parameters when evaluating feeder technologies and discussing options with your equipment suppliers:
- Is the feeder designed to handle the required feed rates?
- Is the material you are choosing able to achieve your accuracy and feeding requirements?
- Is the feeder designed to fit into the space required?
- Will it be a volumetric or gravimetric feeder?
- Can the feeder handle all of the materials planned, or do changes have to be made for the feeder to work correctly?
Investing in the correct feeder technology will help your ROI and product stability. Create a relationship with your equipment suppliers and evaluate the best solution for your process. The more information you know about your material the easier it is to choose the correct feeder.
Materials Characteristics for Feeding
Once you and your material supplier have decided on the type of materials that work best with your process bring your feeding equipment supplier in to evaluate the material that you plan to use and the process for which it is intended.
- What are the different shapes and sizes of raw materials that you will be processing? Samples of each material will be required.
- What is the bulk density of each material?
- What unique flow characteristics does each material have? These are typically designated as free- flowing, fairly free flowing, and non-free flowing
- At what temperature will you be processing each material? For example, PET is typically dried at a high temperature and may require special nozzles for warm air or other options.
- What are the throughput requirements for each material? Be prepared to specify minimum, maximum and nominal rates.
- What is the area of classification? Be sure to advise your equipment supplier if material is volatile or in a volatile area. Please review and supply the MSDS information so your equipment suppliers will understand how to handle the material when testing.
- What are your accuracy requirements? Feeding equipment suppliers are challenged in finding the best feeder technology recommendation to achieve your accuracy and throughput requirements. This may sound like a simple task; but in reality, if you do not implement the correct feeding technology you will end up spending money, time and resources chasing problems that could have been discovered in lab tests.
Let’s dive into a few examples of customer requirements and which considerations were necessary to achieve their goals. These examples of materials were considered for a single-component feeding system or as part of a multi-component feeding system.
Example 1: Feeding a proprietary pellet
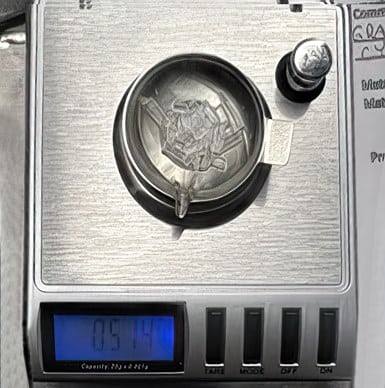
A clear pelletized material has a bulk density of 40 lb/ft3. The material size varied from 17 mm to a small crystal the size of salt. The customer required a feed rate of 0.275 lb/hr or 125 g/hr.
In reviewing the above information, the biggest issue with the material was the particle-size variation. By just a visual review, a standard auger feeder would not achieve the proper consistency needed for the low feed rate. We opted for a special disc feeder with a reduced disc size to allow the longer pellet sizes to be fed consistently.
As expected, the bulk density varied but was able to be fed within a few tenths of a gram variation over a 15-second time period. To improve accuracy, we recommended to the customer that the material be granulated or cut more evenly. Flowability was not an issue; but, as would be expected, the smaller fines fell to the bottom of the feed hopper first and caused the feed rate to change greater than required over time.
The desired throughput was easily achieved using the disc feeder designed for low rates. Figure 1 shows the amount (0.51 g) required in 15 sec.
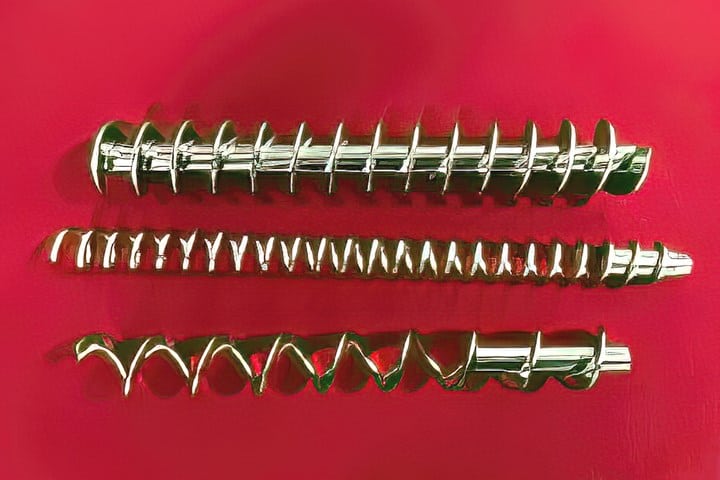
Example 2: Feeding Regrind
There is a push for processors to utilize more and more regrind in their products. Those who do not produce enough in-house regrind look for outside sources of regrinds through brokers, recyclers and compounders. The challenge is to ensure how consistently they can feed the different regrind shapes, sizes, and bulk-density variations. Here is where the equipment manufacturer can help with designing the correct feeder configuration.
Most common issues that processors will deal with is how much regrind can be introduced into their process before it starts producing a bad product. This typically requires an evaluation of the regrind and establishing a proper feeder screw design and tube diameter.
These are some basic concepts you can consider when feeding regrind-based material. It is always beneficial to work with your feeder supplier to evaluate the best feeder for you process.
- Larger chunks of regrind typically will require the ID of the tube to be greater than the screw diameter to prevent the feeder from locking up. Depending on the type of material (such as higher bulk densities), those larger chunks may require a solid-core auger for more consistent transportation through the flights.
- For lower density regrinds a spiral screw may be better suited.
- With regrinds, be prepared to use multiple screws and designs to achieve your different throughput rates (Fig. 2).
- If lighter regrinds are introduced back into your process, internal feeder and or hopper agitation may be necessary to eliminate bridging.
- Keep the inlet to your auger screw as large as possible; this will help keep material from bridging.
- With some regrind materials, using downcomer designs can create periodic material stoppages, so it will be important to understand flowability and design equipment accordingly.
Example 3: Feeding Antioxidant Additive
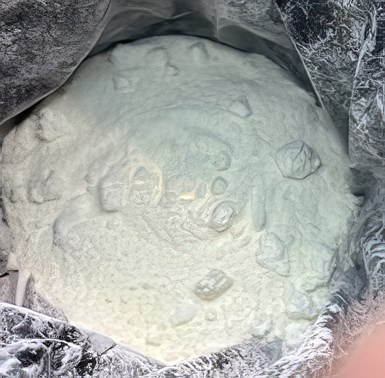
It was required to feed an additive in powder/flake form at 5 to 10 lb/hr with a 33 lb/ft3 bulk density. This particular additive (Fig. 3) behaves unusually in feeding. In the initial review, it flowed fairly well and seemed like an easy material to feed, but over time it proved to play havoc with a feeder. When testing this material over a couple days using a vibratory, single- or twin-screw feeder, the material would start to harden in the area where the material was worked constantly. The eventual outcome would be reduced flow and/or stoppage of the feeder. This reduced flow would cause the user to shut down the process regularly to clean the feeder.
The processor wanted to find a feeding technology to reduce his downtime. After further testing and evaluation, we designed a special disc design that allowed the material to flow with very little working between the material and metal surface of the feeder. To improve accuracy, we utilized a gearmotor that would run at a low rpm. Utilizing this concept, we were able to reduce the cleaning time and number of times cleaning was required.
About the author
Roger Hultquist is co-owner and president of Orbetron, LLC in Lincoln, R.I., a manufacturer since 2011 of bulk material feeders for quantities from 1 g/hr up to 20,000 lb/hr. He has been involved in the bulk material and liquid feeding industry for over 35 years, working for a number of different auxiliary equipment manufacturers that supply to industries such as food, pharmaceuticals, plastics, chemicals and more.