Variation in the moisture content of the raw materials has historically presented a challenge to feed processors. The raw ingredients’ moisture content varies depending on the prevailing environmental conditions during harvest, transportation, and storage.
The perfect solution is to constantly measure the flowing materials’ moisture content and correct moisture variations in real time. In the past, such systems have been complicated to use and have required ongoing complex and expensive maintenance. Modern, sophisticated, reliable and affordable moisture sensors are now available that can simply and economically control the moisture content throughout the entire process.
The use of online moisture measurement sensors enables the control system to automatically react to changes and adjust the process to achieve a continuous and precise moisture level in the material, whether for storage, further processing, or final packaging.
Why should you measure moisture?
Raw materials vary in moisture content, and this variation leads to weighing discrepancies. The weight of usable material will vary dependent on the moisture content. An increase in moisture content means that there is less usable material. A reduction in moisture content gives more usable material for the given weight. Without compensation, this leads to different proportions of usable material being added to a formulation. This affects both the final yield and causes variation in the nutritional value.
Accurate control of the moisture during the drying process prevents under-drying and over-drying. Over-drying material uses excessive energy, reduces the yield, and can damage the material being dried (for example, becoming brittle if dried too quickly). Under-drying leads to potential mycotoxin growth and reduces the storage life of the material.
The accuracy of the moisture measurement system will affect the final moisture target of the dryer as the material being dried will need to be below a maximum allowed value. If you use a moisture sensor that can get as close as possible to the maximum value, you reduce the amount of extra drying needed, which reduces the energy being wasted.
Although this is often regarded as a small reduction, reducing the distance from the target will lead to more significant savings in energy.
Choosing to rely on a moisture sensor that can measure to a precision of +/-0.5% instead of 1.0% seems a slight improvement. Still suppose you consider a process that is drying material from 20.0% to a maximum of 14.0%. In that case you can see from Figure 2 that the 0.5% improvement in the sensor precision yields a much more considerable 7.15% energy saving if the energy input is proportional to the moisture loss.
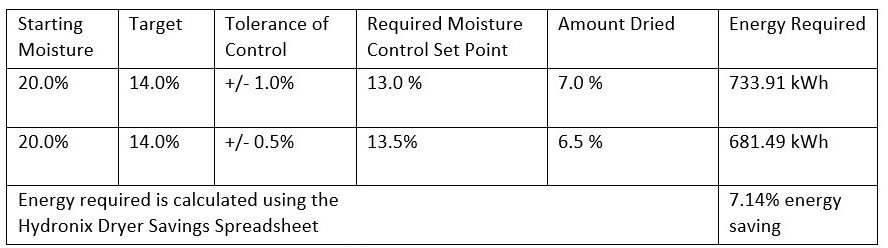
Where should you measure moisture?
Moisture control throughout the process allows the production of higher quality, balanced and more valuable feed:
- Drying for Storage at the outlet of a dryer – During this phase, it is essential to keep the process on the target moisture, as wet material can lead to severe problems, such as hotspots and mycotoxins or allow insects to thrive.
- Milling / Tempering at the inlet of the tempering system – This process regulates the moisture of the grains and cereal before milling to ensure the correct separation of the husk. The water content also affects the final size and shape of the milled powder.
- Pelleting / Conditioning during the conditioning process – Water and heat are added to the material flow using steam during this process. Achieving the correct moisture allows the production of perfect pellets and removes the risk of damage to the die.
- Drying for packaging at the outlet of a dryer – In the same way that the raw ingredients benefit from moisture control, the feed also needs to be dried to a specific target to ensure long shelf life without yield loss.
Benefits
By controlling the moisture during the weighing up of the raw materials, it is possible to correctly control the protein content of the final pellet and guarantee superior product quality. There are also cost benefits of water control ranging from an increase in the yield from a raw material, a reduction in spoiled material and optimisation of the energy input into the processes.
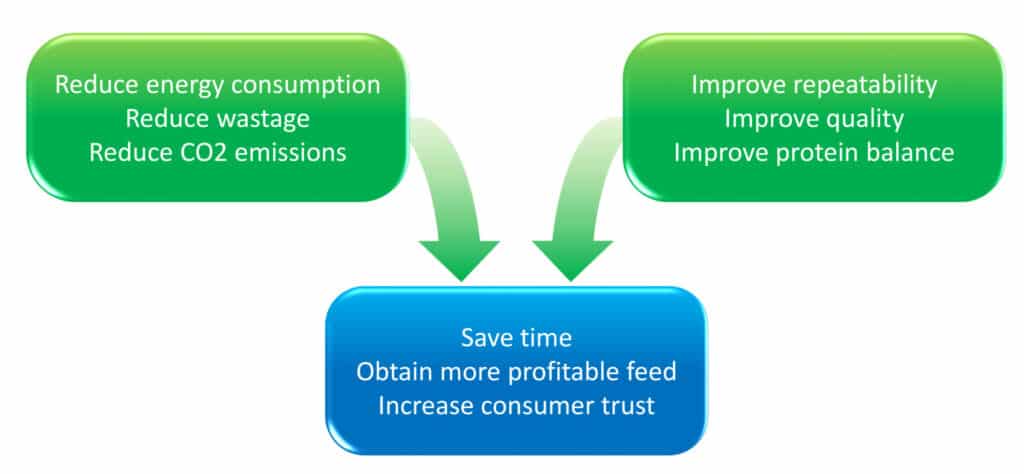
For dryer control, one often overlooked advantage is the ongoing impact of not using the optimal drying rate. By drying with too high a temperature for the moisture in the material, you can increase the damage being done to the husk, which then becomes apparent during either milling or de-husking.
One producer using a moisture control system in their parboiled rice production reported a reduction in broken rice of 2.5%, equivalent to an increase in their yield of premium quality product of 4,000 kg per week. By looking solely at this extra yield at current market rates, this would be an additional USD 1,668.00 per week giving a return on investment of only a few months.
By calculating the energy input needed to dry the material and how much extra energy is input when missing the final target value, it is possible to show extra savings.
Conclusion
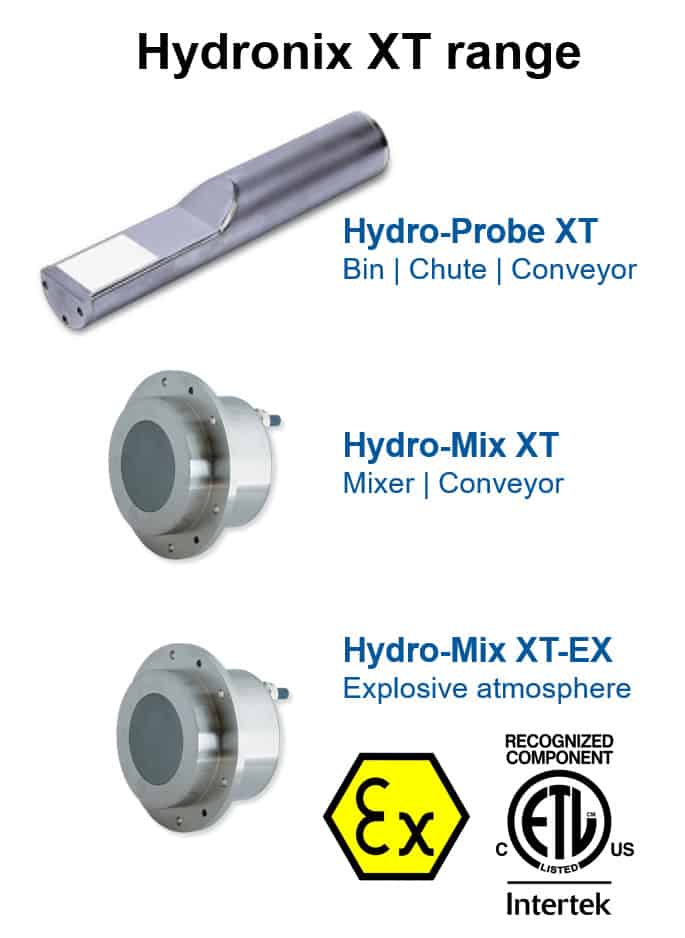
Using a consistent blend of usable materials and maintaining a constant final moisture target saves energy and extends the time between dryer maintenance. Benefits also include producing a consistent feed with a repeatable and homogenous nutritional value and a reliable shelf life.
The Hydronix XT range of sensors uses an industry-leading Digital Microwave Measurement Technique and has a proven track record in these types of applications throughout the world. In addition, the sensors are simple to install and require very little maintenance.