What is a Mixer?
Mixers are a sophisticated and precise piece of equipment designed to blend, emulsify, homogenise, and combine various ingredients — a critical step in the production of commercial and industrial goods, including chemicals, ceramics, pharmaceuticals, cosmetics, and food products.
Mixers rearrange component materials into a state of (ideally) uniform distribution and complete dispersion. While the general public may associate the term “mixer” with cement mixers or kitchen blenders, the reality in industry is far more complex. Even within fluid mixing, there are countless variations requiring careful consideration of mixing head type, speed, size, and shaft configuration.
What Needs to Be Mixed?
Choosing the right mixer begins with a clear understanding of the application and the function the mixer must serve. While end users may focus on the final product, it’s essential to consult a mixing specialist early on, as they will consider a broader range of factors to determine the best equipment.
Materials to be mixed vary greatly in physical form — from molecular compounds to larger particles. Effective mixing increases interfacial area between components, enhancing mass and heat transfer as well as chemical reactions. This makes mixing a key unit operation in nearly every process industry, affecting both the consistency and quality of the final product — whether it’s a simple blend or a complex reaction.
Perfect mixing is rarely necessary — or even possible. The goal is to achieve the level of uniformity required by the process. Evaluating this degree of mixing is essential for controlling process performance and product quality.
How do you assess the degree of uniformity of a mix?
Sampling is the most direct method of assessment, though it’s not always feasible, especially with solid materials. Sample size is typically related to particle size, but in industries like food, other factors — texture, colour, and flavour — may require full production testing to properly evaluate the mix.
Sampling also helps determine the most effective mixing time, which in turn informs mixing rate and overall plant efficiency.
A mixer’s true quality lies in its ability to deliver repeatable, consistent results. This requires a deep understanding of the materials involved, as variations in properties can greatly affect the process. Customisation is often necessary to meet specific manufacturing conditions.
Mechanisms of Mixing
There are three basic mechanisms which can be present in a mixing operation: molecular diffusion, eddy diffusion and bulk or convective flow.
- Molecular diffusion – Driven by concentration and temperature gradients; typical for low-viscosity liquids and gases.
- Eddy diffusion – Occurs under turbulent conditions and requires higher energy, especially with viscous materials. The Winkworth PV Process Vessel is an example for such applications.
- Bulk or convective flow – Common in solids mixing, this involves material rearrangement (e.g., kneading or shear impact). Various Winkworth products support this mechanism.
Mixing Solids
Solids often consist of particles with diverse shapes and sizes. The geometrical, physical, and aerodynamic properties of particulate solid materials all affect the selection of the mixer and its operating parameters. These characteristics directly influence how materials behave during the mixing process and determine the efficiency and effectiveness of the chosen equipment.
The key properties include:
- Bulk density – mass per unit volume
- Particle shape and size distribution
- Flowability – not all materials are free-flowing; some may be fibrous, rubbery, or resinous
- Particle fragility – how easily particles break under stress
- Static charge – which can affect how particles interact and mix
Each of these affects how materials behave during mixing and what kind of mixer is most appropriate.
Mixing is also essential to heat and mass transfer processes. As requirements vary, so too do the types of available mixers.
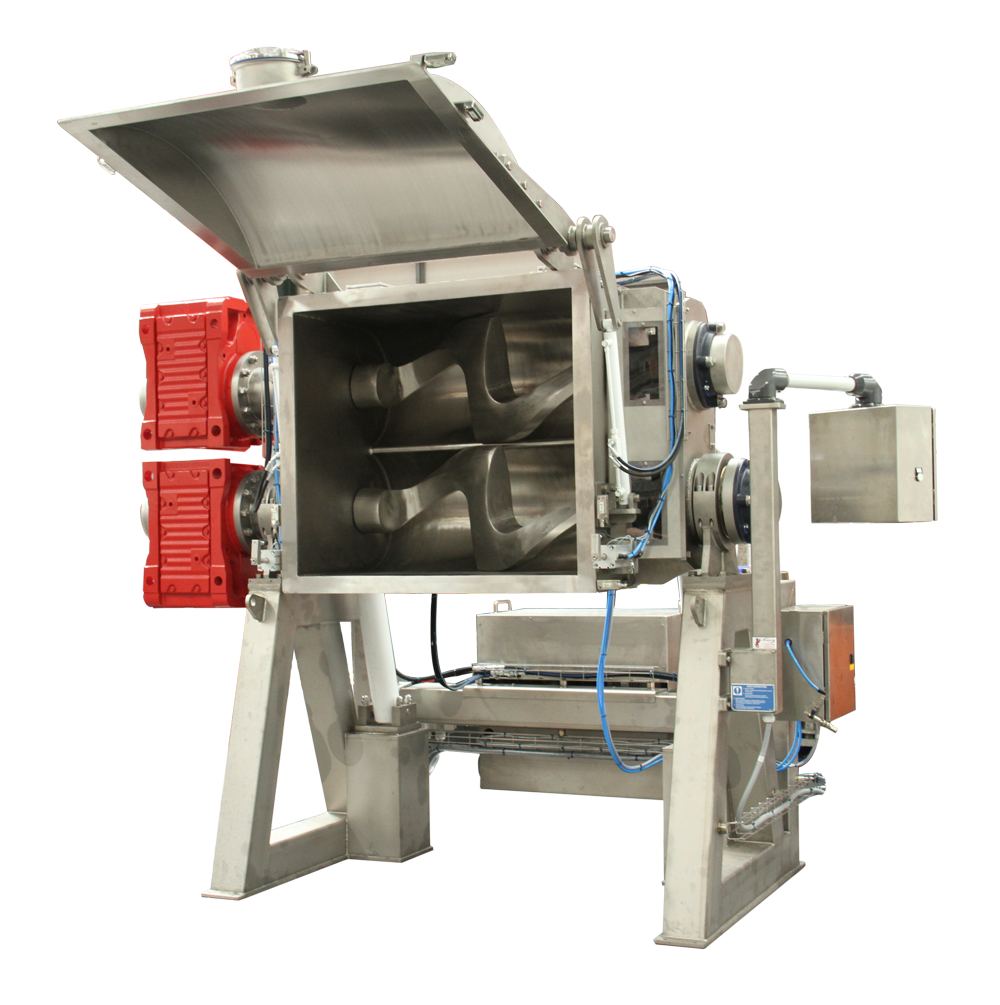
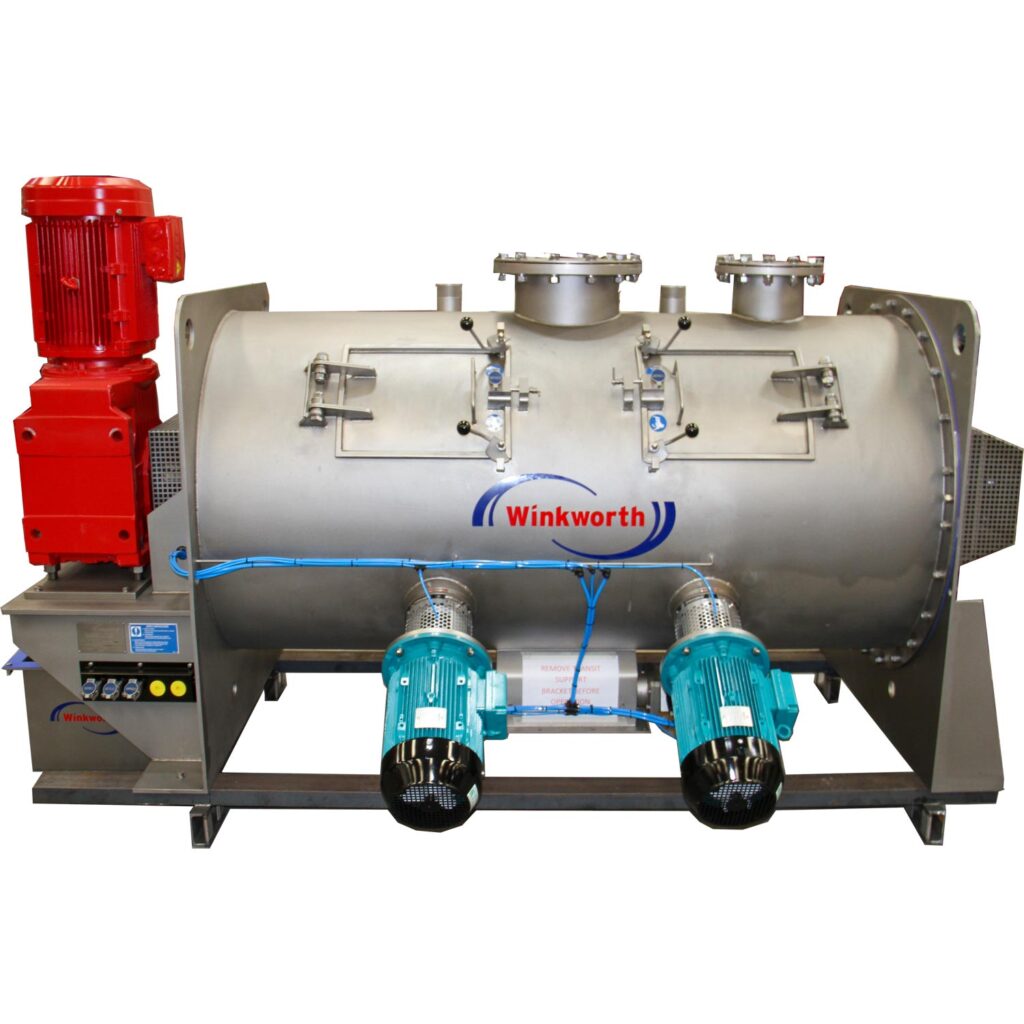
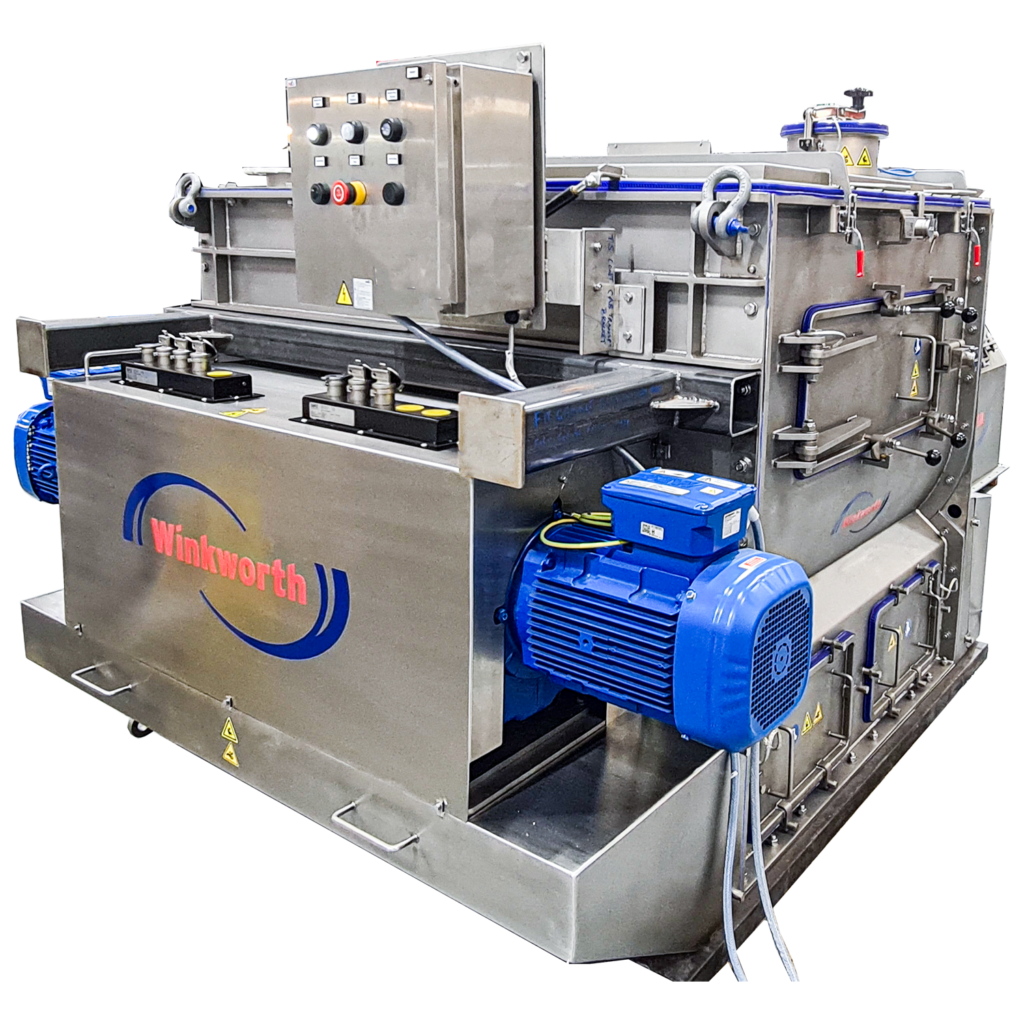
Blending vs. Mixing: What’s the Difference?
Though often used interchangeably, blending and mixing have distinct meanings in industrial contexts. Blending is a gentler process aiming to create a uniform distribution, often forming a new, cohesive substance. Mixing, on the other hand, may involve combining components that can later separate.
Understanding this distinction is key when selecting equipment — many applications require blending to achieve a truly homogeneous result.
Understanding the Materials
The process of selecting a mixer begins with a thorough study of the media to be mixed, which can vary greatly by industry. Common materials include liquids, emulsions, slurries, pastes, solids with liquids, and powders or granular substances. Understanding the consistency, properties, and specific characteristics of these materials is essential in narrowing down the mixer choice to one that best suits the application’s technical and production requirements.
Each material type presents unique challenges in terms of flow behaviour, particle interaction, viscosity, and compatibility. The more detailed the understanding of the media, the more accurate and effective the mixer selection will be — ensuring consistent, high-quality results throughout the production process.
Understand the Different Types of Mixers?
Mixers typically fall into three broad categories: diffusion, shearing, and convective.
Tumble Mixers (Diffusion).
Tumble mixers rely on gentle rotation to mix materials. These diffusion mixers can incorporate air as part of the blending process. Gravity continuously pulls the material down, while drum rotation causes it to roll and blend, promoting uniform distribution without the need for high energy input.
The Winkworth DC ‘Double Cone’ Blender falls into this category.
High Shear Mixers (convective)
High shear mixers are designed for demanding mixing applications involving both solids and liquids. Operating at high speeds with powered blades, they generate intense shear forces, making them ideal for tasks such as: Emulsification, Homogenisation, Dispersion, Particle size reduction and Disintegration of cohesive materials.
These mixers are essential for combining ingredients that resist blending under low shear conditions.
The Winkworth RT ‘Paddle or Plough share’ mixers fall into this category.
Heavy Duty, high shear Mixers (shearing)
Designed specifically for handling highly viscous, dense, and pasty materials — such as thick doughs, chewing gum, rubber compounds, and adhesives — these mixers use twin-shaft configurations or specialized blades like Z or Sigma types to maintain effective mixing under extreme conditions. Single-shaft mixers often fail under these stresses, making heavy-duty alternatives critical for processing materials with viscosities exceeding 750,000 cps.
The Winkworth Z or ZX ‘double Z/ Sigma blade’ mixers fall into this category.
One final comment
Mixing should never be considered in isolation. It is an integral part of the entire materials handling process. From the outset, careful attention must be paid to how raw materials are introduced to the mixer and how the mixed product is transferred to the next stage of the process.
This ensures:
- De-mixing does not occur
- Operations remain safe, efficient, and hygienic
- Labour is minimised
- Production and maintenance costs are optimised
Failure to consider these aspects can impact both product quality and operational performance.
Winkworth Machinery Limited specialises in all types of solids mixing, with over 100 years of experience serving a global customer base across virtually every industry — from traditional manufacturing to emerging technologies.
We invite you to explore our full range of solutions:
- View photos, videos, and case studies
- Arrange a trial at our Customer Test Centre
- Take advantage of short-, medium-, or long-term hire
- Get expert advice — no matter where you are in your project
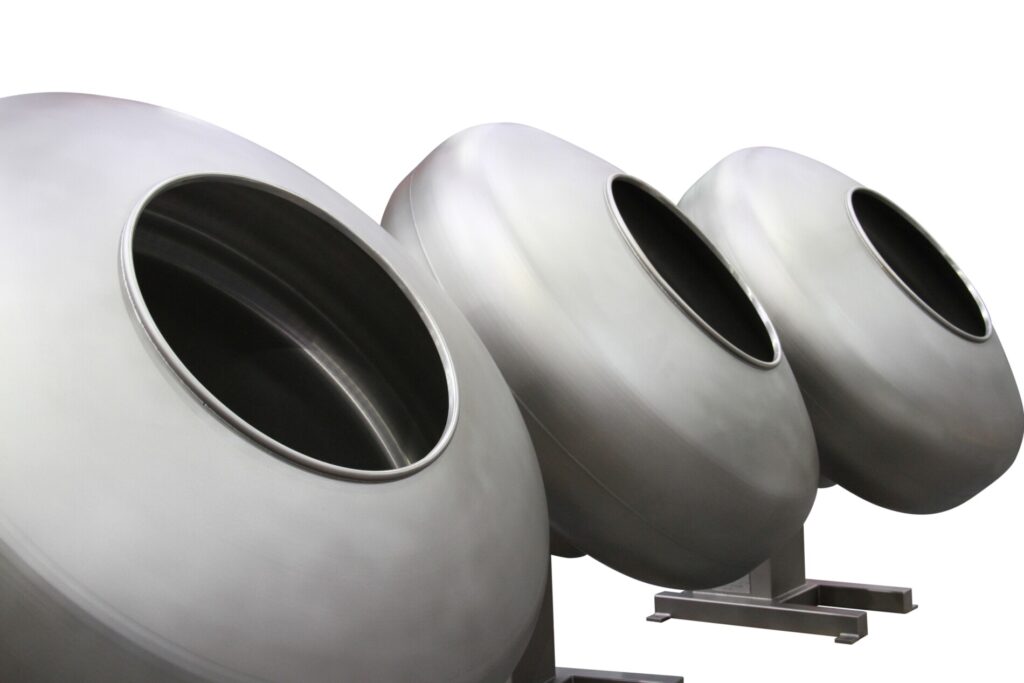