To eliminate common blending challenges, DEC has developed an innovative in-line mixing system that combines active substances without altering their physical properties or risking contamination to operators or the environment. Leveraging PTS powder transfer technology, this fully automated system transfers, mixes, and discharges products using vacuum and pressure under inert conditions. It is specially designed to meet the stringent demands of the pharmaceutical industry and is capable of handling hygroscopic, oxygen-sensitive, or explosive powders.
Versatile Application Range
The same unit can accommodate various batch sizes, from laboratory-scale to large-scale production. It effectively blends powders with significant differences in ratios (down to 1/10,000) and diverse properties, ensuring uniformity and high containment levels.
This technology integrates seamlessly into existing production lines. Powders can be automatically transferred from drums, sacks, or process equipment such as dryers.
Operating Principle
The system features a main tank equipped with an integrated central deflector to promote uniform powder distribution. On top of the tank, a PTS powder transfer chamber with two tangential inlets is installed.
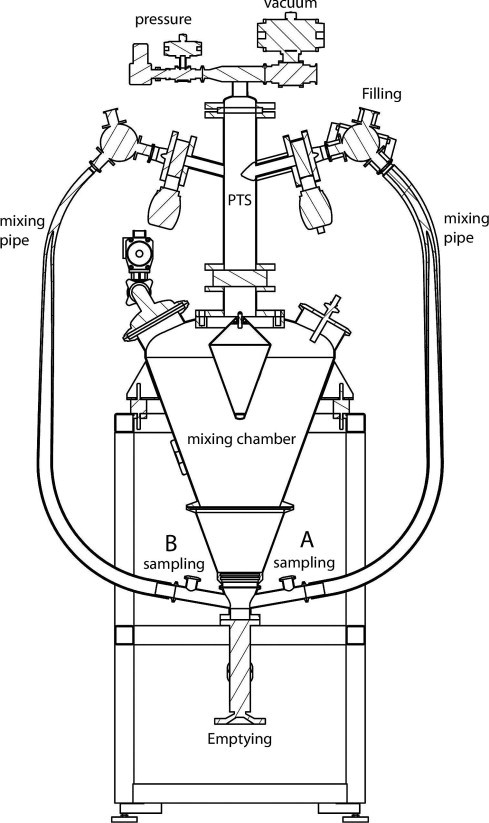
Pneumatic valves, controlled via a pneumatic or electro-pneumatic cabinet, manage the transfer cycles. The PTS chamber operates cyclically through alternating vacuum and pressure. Powder is automatically introduced into the chamber by opening the inlet valve (connected to a vacuum pump) and one of the bottom 3-way valves. To empty the chamber, the outlet and pressure valves (for compressed air or nitrogen) open, dispensing the powder over the deflector into the main tank.
Once all powders are transferred, mixing begins. The system circulates the powder upward through two mixing pipes into the PTS chamber, where two jets converge, enhancing mixing efficiency before the material is returned to the main tank.A filtration membrane located at the top of the PTS prevents fine particles from entering the vacuum system. This membrane is regularly cleaned during each cycle with compressed air or inert gas to maintain suction performance.
Materials are transferred in dense phase mode at limited velocities, preventing particle damage or attrition. After mixing, the system can automatically discharge the blended powder through the bottom, forwarding it to the next process stage via another vacuum source.
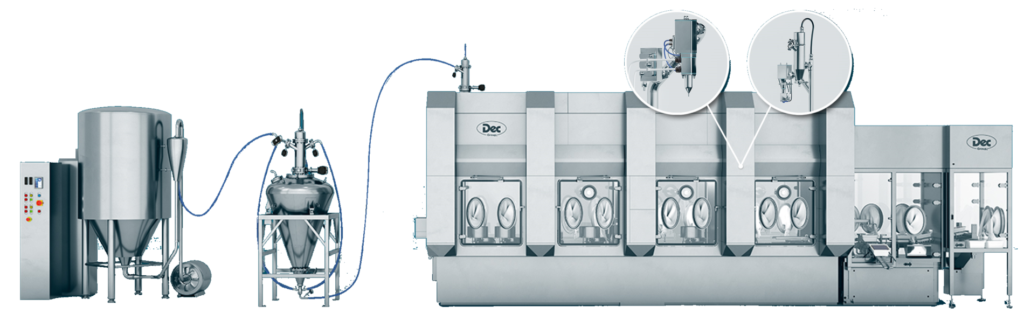
Validation of Blending Efficiency
Mixing trials conducted by Swiss universities demonstrated the system’s high performance. Using a 100 L system with capacities between 10 L and 90 L, controlled by software, tests evaluated different fill levels (25%, 50%, 90%) and tracer concentrations (0.01% to 10% w/w) without prior blending. The results showed effective homogeneity and short mixing times.
Sampling during mixing employed two inline devices: the MPTS (mini PTS) for 30 g samples and the Powderflex system for 1 g samples, both operating with vacuum and pressure in dense phase. The system achieved highly diluted blends down to 0.01% w/w within 6 minutes, with no segregation observed after about an hour. Target concentrations were consistently met, with RSD values between 1.5% and 7% for the 30 g sampler, and within +/-10% of target for the 1 g sampler, confirming excellent homogeneity.
Available in sizes from 5 to 6000 liters, PTS Batchmixer® is a closed, self-filling blending system that ensures consistent product homogeneity, high containment, and reduced mixing times compared to traditional methods. Lacking moving or rotating parts, it requires minimal maintenance and is straightforward to clean through CIP/SIP procedures.